Minimum Trace PCB Manufacturer
Minimum Trace PCB Manufacturer,Minimum Trace PCB refers to printed circuit boards designed with extremely fine conductor traces. These boards are crucial for applications requiring high-density integration and precise signal routing. By minimizing the width and spacing of conductive traces, Minimum Trace PCBs enable compact and efficient electronic designs, reducing signal interference and enhancing electrical performance. They are commonly used in advanced electronics such as mobile devices, wearables, and aerospace equipment where space constraints and signal integrity are critical. The fabrication of Minimum Trace PCBs demands precise manufacturing techniques to achieve reliable operation and maintain high-speed signal transmission capabilities.
What is a Minimum Trace PCB?
A Minimum Trace PCB refers to a printed circuit board (PCB) where the width of the conductive traces is minimized to achieve specific design goals. This type of PCB design is crucial in high-frequency applications where signal integrity, impedance control, and reduced electromagnetic interference (EMI) are critical.
Designing a Minimum Trace PCB involves careful consideration of various factors such as the material properties, trace width, spacing, and the dielectric constant of the substrate material. Typically, thinner traces offer lower impedance and reduced signal loss, making them suitable for applications requiring high-speed data transmission.
Manufacturing a Minimum Trace PCB requires advanced fabrication techniques to ensure precise trace dimensions and consistent quality. This approach is often used in RF/microwave circuits, signal processing systems, and other high-frequency applications where maintaining signal integrity is paramount.
By optimizing trace widths and layouts, engineers can minimize signal distortion, improve performance, and meet stringent design requirements for modern electronic devices.
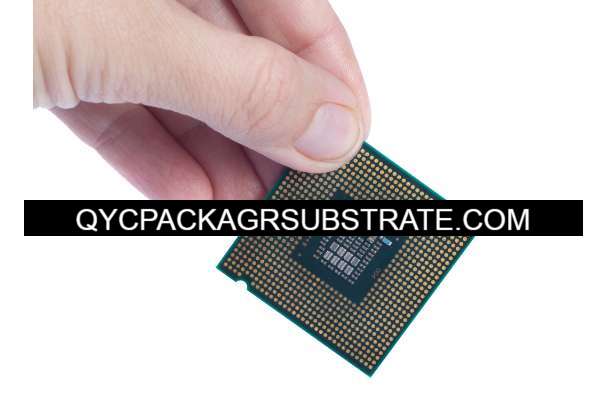
Minimum Trace PCB Manufacturer
What are the Minimum Trace PCB Design Guidelines?
Designing Minimum Trace PCBs requires adherence to specific guidelines to ensure signal integrity and reliability. Here are key guidelines to consider:
- Trace Width and Spacing:Determine the minimum trace width and spacing based on the required impedance and current-carrying capacity. This is crucial for maintaining signal integrity and preventing crosstalk or noise interference.
- Dielectric Material Selection: Choose PCB materials with a low dielectric constant (εr) to minimize signal loss and impedance variations. High-frequency PCB materials like Rogers RO4003C or FR4 with a high-Tg rating are common choices.
- Impedance Control: Maintain consistent impedance throughout the PCB by controlling trace widths, spacing, and layer stack-up. Use impedance calculators and simulation tools to verify impedance values.
- Signal Integrity Considerations: Minimize signal reflections and loss by using controlled impedance routing techniques. Avoid sharp bends and corners in traces, as these can cause signal degradation and impedance mismatches.
- EMI and Crosstalk Mitigation: Implement ground planes and proper shielding techniques to reduce electromagnetic interference (EMI) and crosstalk between adjacent traces or signal paths.
- Via Placement and Design: Optimize via placement to minimize signal distortion and maintain signal integrity. Use via stitching for connecting ground planes and reducing noise coupling.
- Power Distribution:Ensure adequate power distribution and thermal management by optimizing power trace widths and keeping them short and direct.
- Manufacturability: Consider PCB manufacturing capabilities and limitations when designing minimum trace PCBs. Ensure that the chosen trace widths and spacing can be reliably produced without compromising quality.
- Testing and Validation: Perform signal integrity simulations and testing to verify design performance under real-world operating conditions. Use TDR (Time Domain Reflectometry) and VNA (Vector Network Analyzer) measurements to validate impedance and signal integrity.
Following these guidelines ensures that Minimum Trace PCB designs meet performance requirements for high-frequency applications while maintaining reliability and manufacturability.
What is the Minimum Trace PCB Fabrication Process?
The fabrication process for Minimum Trace PCBs involves several key steps to ensure precision and reliability in high-frequency applications. Here’s an overview of the typical fabrication process:
- Design Preparation:Start with a detailed PCB design that includes specific trace widths, spacing, layer stack-up, and material specifications suitable for high-frequency performance. Use CAD (Computer-Aided Design) software to create the layout and routing.
- Material Selection: Choose PCB materials with low dielectric constant (εr) and low dissipation factor (tan δ) to minimize signal loss and maintain signal integrity. Common materials include high-frequency laminates like Rogers RO4003C or FR4 with a high-Tg rating.
- Preparation of Substrate: Begin by cleaning and preparing the substrate material for lamination. This involves ensuring the surface is free from contaminants that could affect adhesion during lamination.
- Lamination: Layer the substrate material and prepregs (pre-impregnated resin) according to the specified layer stack-up. Apply heat and pressure in a laminating press to bond the layers together. This step ensures proper alignment and bonding of the inner layers.
- Drilling: Precision drill the PCB to create holes for vias and component mounting pads. Use CNC (Computer Numerical Control) drilling machines with high accuracy to achieve the desired hole sizes and positions.
- Electroless Copper Deposition: Coat the inner layers with a thin layer of electroless copper to facilitate subsequent plating processes. This step prepares the surface for creating conductive traces.
- Plating: Electroplate the drilled holes and exposed copper surfaces with additional copper to build up the thickness of the conductive traces and vias. This process ensures electrical conductivity and durability.
- Etching: Apply a photoresist mask to define the trace patterns on the outer layers. Use chemical etching to remove unwanted copper, leaving behind the desired trace patterns. The etching process must be precise to maintain trace widths and spacing.
- Surface Finish:Apply a surface finish to protect exposed copper traces from oxidation and ensure solderability. Common surface finishes include ENIG (Electroless Nickel Immersion Gold), HASL (Hot Air Solder Leveling), and OSP (Organic Solderability Preservatives).
- Silkscreen and Legend Printing: Optionally, apply silkscreen printing for component labels and legends on the PCB surface. This step helps in identifying components and their placements during assembly.
- Testing and Inspection: Perform electrical testing (such as continuity testing and impedance testing) and visual inspection to verify the integrity of traces, vias, and overall PCB quality. Testing ensures that the fabricated PCB meets design specifications.
- Final Fabrication Steps: Rout the PCB to its final shape and size. Cut individual PCBs from larger panels using CNC routing or V-cut methods. Clean the PCB thoroughly to remove any residues from the fabrication process.
- Packaging and Shipping: Package the finished PCBs according to customer requirements and prepare them for shipping or further assembly processes.
By following these steps with precision and attention to detail, manufacturers can produce Minimum Trace PCBs that meet the stringent requirements of high-frequency applications, ensuring optimal signal integrity and reliability.
How do you manufacture a Minimum Trace PCB?
Manufacturing a Minimum Trace PCB involves a meticulous process to ensure high-frequency performance and reliability. Here’s a detailed step-by-step guide:
- Design Preparation: Begin with a comprehensive PCB design using CAD software. Specify trace widths, spacing, layer stack-up, and material selections suitable for high-frequency applications. Ensure the design meets impedance control requirements.
- Material Selection: Choose PCB materials with low dielectric constant (εr) and low dissipation factor (tan δ) to minimize signal loss. Common high-frequency materials include Rogers RO4003C or similar laminates with high-Tg FR4.
- Substrate Preparation: Clean and prepare the substrate material for lamination. Ensure the surface is free from contaminants to facilitate proper adhesion during lamination.
- Layer Lamination: Layer the substrate material and prepregs according to the specified stack-up design. Use a laminating press with controlled heat and pressure to bond the layers together securely. This step ensures proper alignment and bonding of inner layers.
- Drilling: Precision drill the PCB to create holes for vias and component mounting pads. Use CNC drilling machines for accuracy in hole size and position control.
- Copper Plating: Initiate with electroless copper deposition on inner layers to prepare for subsequent plating processes. This step enhances the adhesion and conductivity of copper traces and vias.
- Inner Layer Imaging: Apply a photoresist mask and use UV light to expose the desired trace patterns on inner layers. Develop and etch away unwanted copper using chemical processes, leaving behind well-defined copper traces.
- Surface Preparation: Clean and prepare outer layer surfaces for applying photoresist and subsequent trace patterning. Ensure the surface is free from contaminants that could affect the adhesion or quality of the trace patterns.
- Outer Layer Imaging and Etching: Apply a photoresist mask to define trace patterns on outer layers. Use chemical etching to remove excess copper and define the trace widths and spacing according to design specifications.
- Surface Finish Application:Apply a suitable surface finish to exposed copper traces to protect against oxidation and ensure solderability. Common finishes include ENIG, HASL, or OSP, chosen based on design requirements.
- Silkscreen Printing: Optionally, apply silkscreen printing for component labels and legends on the PCB surface. This helps in identifying components during assembly and testing.
- Testing and Inspection: Conduct electrical testing (such as continuity testing and impedance testing) to verify trace integrity and adherence to design specifications. Perform visual inspection to ensure no defects in trace patterns or surface finishes.
- Final Fabrication Steps: Rout the PCB to its final shape and size using CNC routing or V-cut methods. Clean the PCB thoroughly to remove any residues from the manufacturing process.
- Packaging and Shipping: Package the finished Minimum Trace PCBs according to customer specifications. Ensure proper protection during shipping to maintain PCB quality.
By following these steps meticulously, manufacturers can produce Minimum Trace PCBs that meet the stringent requirements of high-frequency applications, ensuring optimal signal integrity and reliability in electronic devices.
How much should a Minimum Trace PCB cost?
The cost of a Minimum Trace PCB can vary significantly depending on several factors:
- Design Complexity: PCBs with minimum trace requirements often require more precise manufacturing processes, which can increase costs.
- Material Choice:High-frequency PCB materials like Rogers RO4003C or similar laminates with low dielectric constants tend to be more expensive than standard FR4 materials.
- Trace Width and Spacing:Tighter trace widths and spacing requirements may necessitate more advanced manufacturing techniques, impacting cost.
- Layer Count:The number of layers in the PCB affects fabrication complexity and cost. Minimum trace designs may often require multiple layers for impedance control and signal integrity.
- Surface Finish: Choice of surface finish (e.g., ENIG, HASL, OSP) can influence cost, with higher-end finishes adding to the overall price.
- Production Volume:Economies of scale apply; larger production volumes generally reduce per-unit costs due to bulk manufacturing efficiencies.
- Additional Requirements: Factors such as impedance testing, special testing requirements, and specific certifications can add to the overall cost.
To provide a rough estimate, a basic Minimum Trace PCB might cost anywhere from a few dollars to tens of dollars per square inch for small quantities. Larger volumes typically reduce the unit cost due to amortization of setup and tooling costs. It’s advisable to consult with PCB manufacturers for detailed quotes based on your specific design requirements and production volume.
What is a Minimum Trace PCB base material?
The base material for a Minimum Trace PCB typically consists of specialized high-frequency laminates designed to meet stringent performance requirements. Some common base materials used for Minimum Trace PCBs include:
- Rogers RO4003C:This is a high-frequency laminate with a dielectric constant (εr) of 3.38 and is suitable for applications requiring excellent electrical performance and dimensional stability.
- Rogers RO4350B: Another high-frequency laminate with a dielectric constant (εr) of 3.48, known for its low loss characteristics and stable electrical properties over a wide frequency range.
- Isola FR408HR: A high-performance FR4 material with improved thermal reliability (high Tg) and low dielectric loss, suitable for high-speed digital and RF applications.
- Isola IS680: A low-loss, high-thermal-performance material designed for high-frequency applications where low dielectric loss and stable electrical properties are crucial.
- Taconic TLY-5A: A PTFE-based laminate with a dielectric constant (εr) of 2.2, offering excellent electrical performance at microwave frequencies and low signal loss.
These materials are chosen for their low dielectric constants, low dissipation factors (tan δ), and stability under varying environmental conditions. They provide the necessary electrical properties to maintain signal integrity in high-frequency applications, making them ideal choices for Minimum Trace PCBs where precise trace widths and impedance control are critical.
Which company makes Minimum Trace PCB?
Minimum Trace PCBs are typically manufactured by specialized PCB manufacturing companies with advanced manufacturing equipment and extensive experience to meet the demands of high-frequency and high-performance applications. Some well-known PCB manufacturers such as Rogers Corporation and Isola Group in the United States, as well as Mitsubishi Electric in Japan, have deep technical expertise and market influence in high-frequency PCB materials and manufacturing technologies.
Our company is also a professional PCB manufacturer capable of producing Minimum Trace PCBs that meet these stringent requirements. We employ advanced manufacturing equipment and technologies tailored for high-frequency applications in PCB design and production. Here are some key advantages and capabilities of our company in manufacturing Minimum Trace PCBs:
- Advanced Manufacturing Equipment: We utilize advanced CNC drilling machines, automated production lines, and precision machining equipment to achieve precise trace and hole requirements.
- High-Quality Material Selection: We use advanced materials specifically designed for high-frequency PCBs, such as Rogers RO4003C, Isola FR408HR, which offer low dielectric constants and excellent electrical performance suitable for high-frequency and high-speed transmission applications.
- Strict Quality Control: We implement a rigorous quality management system with strict controls and testing throughout the material procurement and production processes to ensure every PCB meets design specifications and high standards.
- Customized Solutions: We provide customized Minimum Trace PCB solutions tailored to meet specific customer requirements, including design optimization, process selection, and volume production, supported by comprehensive technical consultation and support.
- Experienced Team: Our experienced engineering team and technical staff offer professional expertise and support to ensure optimal performance and reliability in Minimum Trace PCB design and manufacturing.
With our technological capabilities and commitment to quality, we are equipped to meet various customer needs in the field of high-frequency and high-performance PCBs, providing stable and reliable circuit board solutions for our customers’ products.
What are the 7 qualities of good customer service?
Good customer service is characterized by several key qualities that contribute to a positive customer experience and build customer loyalty. Here are seven essential qualities:
- Responsiveness: A good customer service team responds promptly to customer inquiries, issues, or complaints. They acknowledge customer concerns in a timely manner and provide updates or resolutions promptly.
- Empathy: Customer service representatives demonstrate empathy by understanding and acknowledging the customer’s feelings and perspective. They listen actively, show compassion, and strive to address customer concerns effectively.
- Clear Communication:Effective communication is crucial in customer service. Representatives should convey information clearly and concisely, using language that is easy for customers to understand. They should also ensure that they understand the customer’s questions or issues before providing responses.
- Knowledgeability: Good customer service requires a thorough understanding of the products or services offered. Representatives should be knowledgeable about company policies, procedures, and product details to provide accurate information and assistance to customers.
- Professionalism: Customer service representatives should maintain a professional demeanor at all times. This includes being courteous, respectful, and patient, even in challenging situations. Professionalism also involves maintaining confidentiality and upholding company values.
- Problem-Solving Skills: Effective customer service involves the ability to identify and resolve customer issues efficiently. Representatives should be proactive in finding solutions, taking ownership of problems, and following through until the issue is resolved to the customer’s satisfaction.
- Adaptability:Customer service often involves dealing with diverse customer needs and situations. Representatives should be adaptable and flexible, able to adjust their approach based on the customer’s personality, preferences, and the specific circumstances of each interaction.
By embodying these qualities, organizations can deliver exceptional customer service experiences that foster customer satisfaction, loyalty, and positive word-of-mouth. These qualities are foundational in building strong relationships with customers and enhancing the overall reputation of the business.
FAQs
What are Minimum Trace PCBs?
Minimum Trace PCBs refer to printed circuit boards designed with very narrow trace widths and tight spacing between traces. They are used in high-frequency and high-speed applications where signal integrity and impedance control are critical.
Why are Minimum Trace PCBs important?
These PCBs are important because they minimize signal loss and interference, enhance electrical performance, and support high-frequency operations. They are essential in applications like telecommunications, RF/microwave devices, and high-speed digital circuits.
What materials are used for Minimum Trace PCBs?
Common materials include high-frequency laminates like Rogers RO4003C, Isola FR408HR, and other specialized substrates with low dielectric constants and low loss tangents. These materials ensure minimal signal attenuation and stable electrical properties.
What are the challenges in manufacturing Minimum Trace PCBs?
Challenges include achieving precise trace widths and spacing, maintaining signal integrity, and managing impedance control. Specialized equipment and processes are required to ensure accuracy and reliability in fabrication.
What applications are suitable for Minimum Trace PCBs?
They are suitable for applications requiring high-speed data transmission, RF signal processing, radar systems, wireless communications, and other advanced electronic devices where maintaining signal integrity is crucial.
How can I optimize the design of Minimum Trace PCBs?
Design optimization involves careful planning of trace routing, layer stack-up, and selection of materials to meet impedance requirements. Use of simulation tools and adherence to best practices in high-frequency PCB design are recommended.
What are the benefits of using Minimum Trace PCBs?
Benefits include improved signal integrity, reduced electromagnetic interference (EMI), enhanced performance in high-frequency applications, and overall reliability in critical electronic systems.