Mitsubishi BT PCB Manufacturer
Mitsubishi BT PCB Manufacturer,The Mitsubishi BT PCB is a specialized printed circuit board designed to support Mitsubishi Electric’s Binary Tree system. This PCB features precision design and high-quality manufacturing aimed at ensuring system stability and reliability. Its design considers the complexity and performance requirements of the system, including support for signal transmission, power management, and data processing. The Mitsubishi BT PCB employs advanced materials and manufacturing processes to ensure excellent electrical characteristics and durability. It may utilize High-Density Interconnect (HDI) technology or special interlayer connection designs to achieve a more compact layout and higher performance. Additionally, the Mitsubishi BT PCB may include features such as multilayer design, metal core, or special protective coatings to meet specific application needs and environmental requirements. In summary, the Mitsubishi BT PCB represents a commitment to quality and innovation in supporting Mitsubishi Electric’s Binary Tree system.
What is a Mitsubishi BT PCB?
A Mitsubishi BT PCB, also known as a Mitsubishi Board to Board Power Circuit Breaker, is a component used in electrical systems to protect against overcurrent situations. It’s specifically designed for board-to-board applications, typically found in industrial and automotive settings where space is limited and high reliability is required.
The primary function of the Mitsubishi BT PCB is to interrupt the flow of current when it exceeds a certain threshold, preventing damage to sensitive components or the system itself. This can occur due to short circuits, overloads, or other faults. By breaking the circuit when necessary, the PCB helps ensure the safety and proper functioning of the electrical system.
These breakers are often compact in size and designed to be mounted directly onto circuit boards, facilitating easy integration into electronic devices or larger systems. They may feature various protective mechanisms such as thermal or magnetic trip elements to respond to different types of overcurrent conditions.
Mitsubishi Electric, a global leader in electronics and electrical equipment, manufactures a range of PCBs tailored to specific applications and industry requirements. These PCBs undergo rigorous testing and quality control measures to meet international standards for safety and performance. Overall, the Mitsubishi BT PCB plays a crucial role in safeguarding electrical equipment and maintaining operational efficiency in diverse settings.
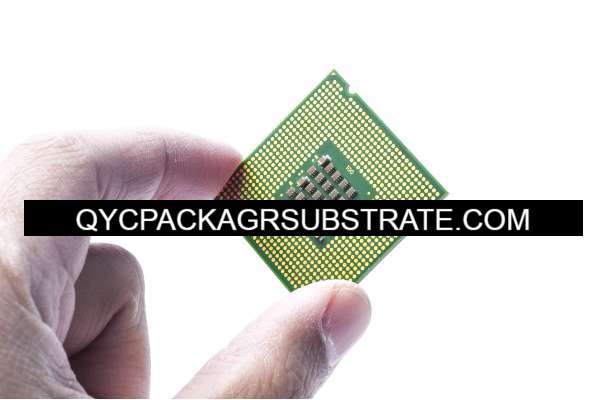
Mitsubishi BT PCB Manufacturer
What are the Mitsubishi BT PCB Design Guidelines?
While specific design guidelines for Mitsubishi BT PCBs may vary depending on the application and model, there are some general principles that designers typically follow to ensure optimal performance and reliability:
- Electrical Specifications: Ensure that the PCB meets the electrical specifications provided by Mitsubishi Electric for the particular model of BT PCB being used. This includes parameters such as voltage rating, current rating, trip characteristics, and maximum fault current handling capacity.
- Layout Considerations: Pay attention to the layout of the PCB to minimize signal interference, voltage drops, and thermal issues. Proper placement of components, traces, and ground planes is crucial for optimal performance and reliability.
- Heat Dissipation: Provide adequate thermal management to dissipate heat generated during normal operation and fault conditions. This may involve using heat sinks, thermal vias, and proper airflow to maintain the temperature within acceptable limits.
- Component Selection: Choose components that meet the required specifications and are compatible with the operating conditions of the PCB. Pay special attention to the selection of semiconductor devices, such as MOSFETs or IGBTs, as they play a critical role in the operation of the BT PCB.
- Protection Features: Incorporate additional protection features such as transient voltage suppression, reverse polarity protection, and short-circuit protection to enhance the reliability and safety of the PCB.
- EMI/EMC Compliance: Ensure that the PCB design complies with electromagnetic interference (EMI) and electromagnetic compatibility (EMC) standards to minimize the risk of interference with other electronic devices and systems.
- Testing and Validation: Perform thorough testing and validation of the PCB design to verify its performance under various operating conditions and to ensure compliance with relevant industry standards and regulations.
- Documentation: Maintain comprehensive documentation of the PCB design, including schematics, layout files, bill of materials (BOM), and design calculations, to facilitate troubleshooting, future revisions, and compliance with regulatory requirements.
By following these guidelines, designers can create Mitsubishi BT PCBs that meet the necessary performance, reliability, and safety requirements for their intended applications.
What is the Mitsubishi BT PCB Fabrication Process?
The fabrication process for Mitsubishi BT PCBs involves several steps, each crucial for ensuring the quality, reliability, and performance of the final product. While the exact process may vary depending on the specific requirements of the PCB design and the manufacturing facility, here is a general overview of the typical steps involved:
- Design Verification: Before fabrication begins, the PCB design is thoroughly reviewed and verified for accuracy and compliance with specifications. This may involve design validation checks, such as Design for Manufacturability (DFM) and Design for Testability (DFT), to identify and address any potential issues early in the process.
- Material Selection: High-quality materials are selected for the PCB substrate, copper layers, and other components based on the design requirements and performance criteria. Mitsubishi Electric may have specific material specifications for their BT PCBs to ensure optimal performance and reliability.
- Preparation of Substrate: The substrate material, typically a fiberglass-reinforced epoxy laminate (FR-4), is prepared by cutting it to the required size and shape. Holes are drilled for through-hole components and vias, and surface preparation techniques are applied to ensure proper adhesion of the copper layers.
- Copper Cladding: Copper foil is laminated onto the substrate using heat and pressure to create the conductive layers of the PCB. The copper layers may be applied to one or both sides of the substrate, depending on the design requirements.
- Image Transfer: A photoresist material is applied to the copper layers, and the PCB design pattern is transferred onto the photoresist using a photomask and UV light exposure. This step defines the conductive traces, pads, and other features of the PCB layout.
- Etching: The exposed copper areas not protected by the photoresist are etched away using chemical processes, leaving behind the desired copper traces and features on the PCB. Careful control of the etching process is essential to ensure precise trace widths and spacing.
- Drilling and Plating: Holes are drilled through the PCB for through-hole components and vias. The drilled holes are then plated with copper to establish electrical connections between different layers of the PCB.
- Component Placement: Surface-mount and through-hole components are placed onto the PCB according to the design layout. Automated pick-and-place machines may be used for surface-mount components, while through-hole components may be inserted manually or using automated insertion equipment.
- Soldering: The components are soldered onto the PCB using solder paste and reflow soldering ovens for surface-mount components or wave soldering machines for through-hole components. This step creates reliable electrical connections between the components and the PCB.
- Testing and Inspection: The assembled PCBs undergo rigorous testing and inspection to verify functionality, electrical continuity, and quality. Various testing methods, such as automated optical inspection (AOI), in-circuit testing (ICT), and functional testing, may be employed to ensure that the PCBs meet the specified requirements.
- Final Finishing: The PCBs are cleaned, and any excess solder or flux residues are removed to ensure cleanliness and reliability. Surface finishes such as HASL (Hot Air Solder Leveling), ENIG (Electroless Nickel Immersion Gold), or OSP (Organic Solderability Preservatives) may be applied to protect the exposed copper surfaces and enhance solderability.
- Packaging and Shipping: The finished PCBs are packaged according to customer requirements and prepared for shipping to their final destination.
Throughout the fabrication process, stringent quality control measures are implemented to detect and correct any defects or discrepancies, ensuring that the Mitsubishi BT PCBs meet the highest standards of quality, reliability, and performance.
How do you manufacture a Mitsubishi BT PCB?
Manufacturing a Printed Circuit Board (PCB) for a Mitsubishi BT (Binary Tree) system involves several steps. Here’s a simplified overview:
- Design Phase: Initially, you need a detailed schematic and layout design for the PCB. This involves using specialized PCB design software like Altium Designer, Eagle, or KiCad. The design should incorporate all the necessary components, connections, and layout considerations specific to the Mitsubishi BT system.
- Component Procurement: Once the design is finalized, you need to procure all the components required for the PCB assembly. This involves sourcing electronic components such as resistors, capacitors, integrated circuits, connectors, etc., from suppliers. For a Mitsubishi BT system, components might be specialized and need to meet certain quality standards.
- PCB Fabrication: The next step is to manufacture the actual PCB. This involves printing the circuit layout onto a copper-clad laminate board using a photosensitive process. The board is then etched to remove excess copper, leaving behind the desired circuit traces.
- Component Placement: Once the PCBs are fabricated, the components are placed on the board according to the design layout. This can be done manually for small-scale production or using automated pick-and-place machines for larger volumes.
- Soldering: After component placement, the PCB undergoes soldering to permanently attach the components to the board. This can be done using wave soldering, reflow soldering, or hand soldering techniques depending on the scale of production and component types.
- Testing:Once soldered, the PCBs undergo testing to ensure that all components are functioning correctly and that there are no manufacturing defects. This may involve automated testing equipment, functional testing, and visual inspection.
- Quality Control and Inspection: Quality control checks are performed to ensure that the PCBs meet the required specifications and standards. This may involve electrical testing, inspection of solder joints, and overall board integrity checks.
- Assembly: Once the PCBs pass quality control, they can be assembled into the final Mitsubishi BT system along with other components such as enclosures, wiring harnesses, and user interfaces.
- Final Testing: The assembled Mitsubishi BT system undergoes final testing to ensure that it operates as expected and meets the performance criteria specified by Mitsubishi Electric.
- Packaging and Shipping: Finally, the manufactured Mitsubishi BT systems are packaged securely and shipped to customers or distribution centers for deployment.
Throughout this process, attention to detail, quality control measures, and adherence to design specifications are crucial to ensure the reliability and performance of the Mitsubishi BT system.
How much should a Mitsubishi BT PCB cost?
The cost of a Mitsubishi BT Printed Circuit Board (PCB) can vary significantly depending on various factors such as:
- Complexity: The complexity of the PCB design, including the number of layers, the density of components, and the intricacy of the circuitry, will influence the cost. More complex designs typically require more materials and labor, leading to higher costs.
- Component Cost: The cost of the components used on the PCB, including integrated circuits, resistors, capacitors, connectors, etc., can vary based on their specifications, quantities, and suppliers. Specialized or custom components may be more expensive than standard off-the-shelf parts.
- Manufacturing Volume: The volume of PCBs being produced can affect the cost per unit. Larger production runs typically benefit from economies of scale, leading to lower per-unit costs. Conversely, small production runs or prototype quantities may incur higher costs due to setup expenses and lower production efficiency.
- Manufacturing Technology: The manufacturing processes and technology used to fabricate the PCB can impact the cost. Advanced techniques such as HDI (High-Density Interconnect) or flexible PCB fabrication may incur higher costs compared to standard PCB manufacturing methods.
- Quality and Certification Requirements: If the Mitsubishi BT PCB requires adherence to specific quality standards or certifications, such as IPC standards or UL certification, additional costs may be involved for compliance testing and documentation.
- Supplier and Location: The choice of PCB manufacturer and their location can also influence the cost. Different manufacturers have varying pricing structures, capabilities, and overhead costs, which can affect the final price of the PCB.
Without specific details about the Mitsubishi BT PCB design, quantity, and manufacturing requirements, it’s challenging to provide an exact cost. However, a rough estimate for a moderately complex Mitsubishi BT PCB in small to medium quantities could range from a few dollars to several tens of dollars per unit. For precise pricing, it’s recommended to consult with PCB manufacturers or suppliers for a customized quote based on your specific requirements.
What is Mitsubishi BT PCB Base Material?
The base material used for Mitsubishi BT (Binary Tree) Printed Circuit Boards (PCBs) can vary depending on the specific requirements of the application, design considerations, and manufacturing processes. However, typical base materials commonly used for manufacturing PCBs include:
- FR-4: FR-4 (Flame Retardant 4) is the most widely used base material for PCBs. It is a composite material composed of woven fiberglass cloth impregnated with epoxy resin. FR-4 offers good electrical insulation properties, mechanical strength, and dimensional stability. It is suitable for a wide range of applications and is cost-effective.
- FR-4 High Tg: FR-4 High Tg (Glass Transition Temperature) is a variant of standard FR-4 with a higher glass transition temperature, typically above 170°C. This material is chosen for applications requiring enhanced thermal resistance to withstand elevated temperatures during assembly processes such as soldering and reflow.
- Polyimide (PI): Polyimide is a high-performance polymer known for its excellent thermal stability, chemical resistance, and mechanical properties at high temperatures. Polyimide-based PCBs, often referred to as “flexible PCBs” or “flex circuits,” are used in applications where flexibility or resistance to harsh environments is required.
- Rogers Material: Rogers Corporation manufactures a range of specialty high-frequency laminate materials suitable for applications requiring superior electrical performance at microwave frequencies. These materials offer low dielectric constant (Dk) and low loss tangent (Df), making them ideal for RF/microwave circuits and high-speed digital applications.
- Metal Core: Metal core PCBs feature a metal substrate layer, typically aluminum or copper, for improved thermal conductivity and heat dissipation. These PCBs are commonly used in applications requiring efficient heat management, such as LED lighting, power electronics, and automotive systems.
The choice of base material for a Mitsubishi BT PCB depends on factors such as operating environment, electrical performance requirements, thermal management needs, and cost considerations. Designers typically select the most suitable material based on these factors to ensure the optimal performance and reliability of the PCB in the intended application.
What are the 7 qualities of good customer service?
Good customer service is characterized by several key qualities that contribute to positive interactions and relationships between businesses and their customers. Here are seven qualities of good customer service:
- Responsiveness:Good customer service involves promptly addressing customer inquiries, concerns, and requests. Responding in a timely manner demonstrates attentiveness to customer needs and fosters a sense of trust and reliability.
- Empathy: Empathy is the ability to understand and relate to the emotions and perspectives of customers. Customer service representatives who demonstrate empathy acknowledge customers’ feelings, validate their experiences, and strive to find solutions that meet their needs.
- Clear Communication:Effective communication is essential for conveying information clearly and accurately. Customer service representatives should use clear and concise language, actively listen to customers, and provide thorough explanations to ensure understanding and avoid misunderstandings.
- Problem-Solving Skills: Good customer service involves being proactive in resolving issues and addressing customer concerns. Customer service representatives should possess strong problem-solving skills, be resourceful in finding solutions, and be empowered to take appropriate actions to resolve issues promptly.
- Professionalism: Professionalism encompasses maintaining a courteous and respectful demeanor, regardless of the situation or customer interaction. Customer service representatives should conduct themselves professionally, adhere to company policies and standards, and strive to create positive experiences for customers.
- Consistency: Consistency is key to building trust and credibility with customers. Good customer service involves delivering consistent levels of service quality across all customer interactions, channels, and touchpoints. Consistency helps establish reliability and reinforces the brand’s reputation.
- Customer Focus: Good customer service prioritizes the needs and satisfaction of customers above all else. Customer service representatives should be customer-centric, demonstrating a genuine interest in helping customers and going above and beyond to exceed their expectations.
By embodying these qualities, businesses can create positive customer experiences, build strong relationships, and foster loyalty and satisfaction among their customer base.
FAQs
What is a Mitsubishi BT PCB?
A Mitsubishi BT PCB is a printed circuit board that uses Bismaleimide Triazine resin material from Mitsubishi, known for its high performance in demanding applications.
What industries use Mitsubishi BT PCBs?
Industries such as automotive, aerospace, telecommunications, and high-performance computing often use Mitsubishi BT PCBs due to their superior thermal and electrical properties.
Can your company manufacture custom Mitsubishi BT PCBs?
Yes, our company specializes in manufacturing custom Mitsubishi BT PCBs tailored to meet specific customer requirements.
What is the typical lead time for a Mitsubishi BT PCB?
The lead time can vary depending on the complexity and volume of the order but typically ranges from a few weeks to a couple of months.
How do I ensure my Mitsubishi BT PCB design is manufacturable?
Following our Mitsubishi BT PCB design guidelines and consulting with our engineering team during the design phase can help ensure manufacturability.
What testing do Mitsubishi BT PCBs undergo?
Mitsubishi BT PCBs undergo electrical testing, thermal cycling tests, and reliability assessments to ensure they meet performance standards.
What is the minimum order quantity for Mitsubishi BT PCBs?
The minimum order quantity can vary, but we can accommodate both small prototype runs and large production orders.