Mitsubishi BT Substrate Manufacturer
Mitsubishi BT Substrate Manufacturer,Mitsubishi BT Substrate is a high-performance packaging substrate manufactured using High Temperature Co-Fired Ceramic (HTCC) technology. It boasts excellent thermal stability and electrical properties, making it ideal for demanding high-power electronic devices and microwave applications. Through its multi-layered structure and precise manufacturing processes, this substrate offers superior packaging sealing and reliability, accommodating complex circuit layouts and integration needs. Widely utilized in communications, medical, and industrial control sectors, Mitsubishi BT Substrate provides a stable and dependable solution for high-frequency, high-power, and harsh environment applications.
What is a Mitsubishi BT Substrate?
A Mitsubishi BT Substrate refers to a type of substrate used in electronic packaging and semiconductor applications. Specifically, it belongs to the category of high-performance printed circuit boards (PCBs) designed for demanding applications where thermal management, reliability, and electrical performance are critical.
These substrates are manufactured by Mitsubishi Materials Corporation and are known for their high thermal conductivity, which helps in efficiently dissipating heat generated by integrated circuits (ICs) and other components. This characteristic is crucial in applications where heat dissipation is a concern, such as power electronics, RF (radio frequency) devices, and LED modules.
Mitsubishi BT Substrates typically consist of a ceramic base material, often aluminum nitride (AlN) or aluminum oxide (Al2O3), which offers excellent thermal conductivity properties compared to traditional organic PCB materials. They are designed to withstand high temperatures and harsh environmental conditions, making them suitable for use in automotive, aerospace, telecommunications, and industrial electronics.
These substrates are engineered using advanced manufacturing processes such as co-firing technology, where multiple layers of ceramic and metal conductors are fired simultaneously to create a dense, integrated structure. This process ensures robust electrical connectivity and thermal performance throughout the substrate.
In summary, Mitsubishi BT Substrates represent a specialized solution in the realm of advanced PCB technologies, offering superior thermal management capabilities and reliability for applications requiring high performance and durability in challenging operating conditions.
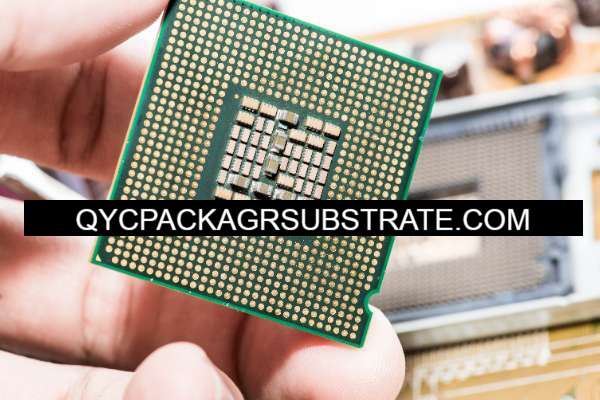
Mitsubishi BT Substrate Manufacturer
What are the Mitsubishi BT Substrate Design Guidelines?
Mitsubishi BT Substrate design guidelines typically focus on optimizing the performance and reliability of electronic assemblies using their substrates. While specific guidelines may vary based on application and product series, here are some general design considerations:
- Thermal Management: Ensure adequate thermal management by designing for efficient heat dissipation. This includes proper placement of heat-generating components, thermal vias, and consideration of thermal conductivity paths within the substrate.
- Material Selection: Choose appropriate materials that match the thermal and electrical requirements of your application. Mitsubishi BT Substrates often use ceramic materials like aluminum nitride (AlN) or aluminum oxide (Al2O3), known for their high thermal conductivity and reliability.
- Layer Configuration: Optimize the layer configuration to achieve desired electrical performance and signal integrity. This may involve careful placement of signal traces, power planes, and ground planes to minimize noise and interference.
- Via Design: Design vias (both thermal and electrical) to facilitate efficient heat dissipation and ensure robust electrical connectivity. Consider via placement and density to balance thermal management with signal integrity.
- Component Placement: Strategically place components to minimize thermal hotspots and ensure even distribution of heat across the substrate. This can help enhance reliability and longevity of the electronic assembly.
- Mechanical Considerations: Factor in mechanical stresses and thermal expansion coefficients when designing for reliability in diverse environmental conditions. Ensure the substrate can withstand mechanical loads and thermal cycling without compromising performance.
- Manufacturability: Design with manufacturability in mind, considering the capabilities and limitations of the co-firing process used in Mitsubishi BT Substrate manufacturing. This includes adhering to minimum feature sizes, layer thicknesses, and aspect ratios to ensure successful production.
- Electrical Performance: Validate electrical performance through simulations and prototyping to verify signal integrity, impedance control, and power distribution characteristics.
- Environmental Compatibility: Ensure compatibility with environmental standards and regulations applicable to your industry, such as automotive (AEC-Q200) or aerospace (MIL-STD-883).
By following these guidelines, designers can maximize the benefits of Mitsubishi BT Substrates, leveraging their high thermal conductivity and reliability to meet the stringent requirements of modern electronic applications. Specific design recommendations may vary based on the exact product series and intended use case, so consulting with Mitsubishi Materials or their technical documentation is recommended for detailed guidelines.
What is the Mitsubishi BT Substrate Fabrication Process?
The fabrication process of Mitsubishi BT Substrates involves advanced techniques tailored to produce high-performance ceramic-based printed circuit boards (PCBs). Here are the typical steps involved in their fabrication:
- Material Selection: The process begins with selecting suitable ceramic materials such as aluminum nitride (AlN) or aluminum oxide (Al2O3). These materials are chosen for their high thermal conductivity and electrical insulation properties, crucial for efficient heat dissipation and reliable electrical performance.
- Green Sheet Preparation: Ceramic powders are mixed with binders and other additives to form a slurry, which is then cast or extruded into thin sheets known as green sheets. These green sheets are flexible and contain the ceramic material in a binder matrix.
- Layer Stacking: Multiple green sheets are stacked together, with each layer containing circuit patterns and vias designed using screen printing or photolithography techniques. Conductive materials such as metal pastes (e.g., silver, copper) are used to create the circuit traces and pads.
- Lamination:The stacked green sheets are laminated under pressure to bond them together into a monolithic structure. This process removes air and ensures good adhesion between layers.
- Via Formation: Vias are formed by drilling or punching through the laminated stack to connect conductive layers vertically. These vias serve both as electrical connections between layers and as pathways for thermal dissipation.
- Firing (Co-Firing): The crucial step in Mitsubishi BT Substrate fabrication is co-firing. The entire laminated structure undergoes a high-temperature firing process in a controlled atmosphere kiln. During firing, the green sheets are sintered to form a dense ceramic substrate, and the conductive materials are sintered to form continuous conductive paths.
- Surface Finishing: After firing, the substrate surfaces may undergo processes such as polishing or metallization to prepare them for component attachment and soldering.
- Quality Control and Testing: Throughout the fabrication process, stringent quality control measures are employed to ensure dimensional accuracy, material purity, and adherence to electrical and thermal specifications. Testing may include checks for electrical continuity, thermal conductivity, mechanical strength, and reliability under various environmental conditions.
- Post-Fabrication Processing: Depending on the specific application, additional processes such as laser machining, coating, or inspection for defects may be conducted to finalize the substrate for use in electronic assemblies.
The Mitsubishi BT Substrate fabrication process is highly specialized, leveraging co-firing technology to integrate ceramic and metal components into a single, high-performance substrate. This process ensures robust thermal management capabilities and reliability, making them suitable for demanding applications in industries such as automotive, aerospace, telecommunications, and power electronics.
How do you manufacture a Mitsubishi BT Substrate?
Manufacturing a Mitsubishi BT Substrate involves a series of specialized steps and processes designed to create high-performance ceramic-based printed circuit boards (PCBs) capable of efficient heat dissipation and reliable electrical performance. Here’s a detailed outline of the manufacturing process:
- Material Selection: Start by selecting ceramic materials known for their high thermal conductivity and electrical insulation properties, such as aluminum nitride (AlN) or aluminum oxide (Al2O3). These materials are crucial for thermal management and electrical reliability.
- Green Sheet Preparation: Prepare ceramic powders by mixing them with binders and additives to form a slurry. This slurry is then cast or extruded into thin, flexible sheets called green sheets. These sheets contain the ceramic material suspended in a binder matrix.
- Circuit Patterning: Apply circuit patterns and vias onto the green sheets using screen printing or photolithography techniques. Conductive materials like silver or copper pastes are used to create circuit traces, pads, and via structures that will facilitate electrical connectivity throughout the substrate.
- Layer Stacking: Stack multiple green sheets together, aligning them precisely to form the desired layer configuration. Each layer contains the circuit patterns and via structures needed for electrical connections between layers.
- Lamination: Press and laminate the stacked green sheets under controlled pressure and temperature conditions. This process removes air and ensures strong adhesion between the layers, forming a cohesive structure ready for further processing.
- Via Formation: Create vias by drilling or punching through the laminated stack at specified locations. These vias serve as vertical interconnections between different conductive layers and also aid in thermal management by facilitating heat dissipation.
- Firing (Co-Firing): The critical step in Mitsubishi BT Substrate fabrication is co-firing. The entire laminated structure undergoes a high-temperature firing process in a controlled atmosphere kiln. During firing, the green sheets undergo sintering, where the ceramic particles fuse together to form a dense ceramic substrate. Simultaneously, the conductive materials within the vias and circuit patterns are sintered to form continuous conductive pathways throughout the substrate.
- Surface Finishing: After firing, the substrate surfaces may undergo additional processes such as polishing or metallization to prepare them for component attachment and soldering. Surface finishing ensures smooth, clean surfaces that facilitate reliable electrical connections and component mounting.
- Quality Control and Testing: Throughout the manufacturing process, rigorous quality control measures are employed to verify dimensional accuracy, material purity, and adherence to electrical and thermal specifications. Testing may include electrical continuity tests, thermal conductivity measurements, mechanical strength evaluations, and reliability testing under various environmental conditions.
- Post-Fabrication Processing: Depending on application requirements, additional post-fabrication processes such as laser machining, coating applications, or detailed inspection for defects may be performed to finalize the substrate for use in electronic assemblies.
By following these detailed manufacturing steps, Mitsubishi BT Substrates are produced to meet the demanding performance requirements of industries such as automotive, aerospace, telecommunications, and power electronics, where thermal management and reliability are critical considerations.
How much should a Mitsubishi BT Substrate cost?
The cost of Mitsubishi BT Substrates can vary widely depending on several factors, including:
- Size and Complexity: Larger substrates or those with intricate designs requiring more layers, finer features, or special configurations may cost more due to increased material and manufacturing complexity.
- Material Composition: The choice of ceramic material (e.g., aluminum nitride, aluminum oxide) and the quality of conductive materials (e.g., silver, copper) used in the substrate significantly influence costs. Higher thermal conductivity ceramics and high-purity conductive materials may increase the substrate’s cost.
- Manufacturing Process: Substrates manufactured using advanced processes like co-firing and requiring precise control over firing conditions and layer alignment may incur higher production costs due to specialized equipment and expertise.
- Volume and Order Size: Larger volume orders typically benefit from economies of scale, resulting in lower unit costs per substrate. Smaller orders or prototypes may have higher unit costs due to setup and handling charges.
- Additional Features and Customization: Substrates with specific additional features such as specialized coatings, laser machining, or customized electrical characteristics may cost more due to additional processing steps and materials.
- Supplier and Market Dynamics: Pricing can also be influenced by market conditions, supplier policies, and geographic location. Different suppliers may offer varying pricing structures based on their manufacturing capabilities and market positioning.
To get an accurate cost estimate for Mitsubishi BT Substrates, it’s advisable to contact Mitsubishi Materials Corporation or authorized distributors directly. They can provide tailored quotes based on your specific requirements, including substrate size, design complexity, material specifications, and order volume. This approach ensures you receive pricing that reflects the exact features and quantities needed for your application.
What is Mitsubishi BT Substrate base material?
The base material used in Mitsubishi BT Substrates typically consists of advanced ceramics, specifically aluminum nitride (AlN) or aluminum oxide (Al2O3). These ceramics are chosen for their excellent thermal conductivity and electrical insulation properties, which are critical for applications requiring efficient heat dissipation and reliable electrical performance.
Aluminum nitride (AlN) is particularly favored for its high thermal conductivity (approximately 170 W/mK), which is significantly higher than traditional organic substrates used in PCBs. This property allows AlN-based substrates to efficiently dissipate heat generated by electronic components, making them suitable for high-power applications where thermal management is crucial.
Aluminum oxide (Al2O3), also known as alumina, is another ceramic material used in some Mitsubishi BT Substrates. It offers good thermal conductivity (around 20-30 W/mK) and excellent mechanical strength and electrical insulation properties. Alumina substrates are often chosen for applications requiring robustness and reliability in harsh operating environments.
Both aluminum nitride and aluminum oxide ceramics undergo specialized manufacturing processes such as co-firing, where layers of ceramic and conductive materials are fired together to form a dense, integrated substrate structure. This manufacturing method ensures strong bonding between layers and optimal thermal and electrical performance throughout the substrate.
In summary, the base material of Mitsubishi BT Substrates is primarily aluminum nitride (AlN) or aluminum oxide (Al2O3) ceramics, chosen for their superior thermal conductivity and electrical insulation characteristics essential for demanding electronic applications.
Which company makes Mitsubishi BT Substrate?
Mitsubishi BT Substrate is manufactured by Mitsubishi Materials Corporation. Mitsubishi Materials Corporation is a well-known Japanese materials manufacturing company specializing in the development and production of various high-performance materials, including ceramic substrates for electronic packaging. Their Mitsubishi BT Substrate series is renowned for its excellent thermal management capabilities and reliable electrical performance, widely used in automotive electronics, aerospace, telecommunications equipment, and industrial electronics.
As a partner of Mitsubishi Materials, our company is also capable of producing similar high-performance ceramic substrates to meet customers’ stringent requirements in thermal management, electrical performance, and reliability. We have advanced manufacturing equipment and an experienced technical team capable of custom designing and producing high-performance ceramic substrates according to specific customer requirements. We employ advanced co-firing technology to ensure uniform fusion of ceramics and conductive materials at high temperatures, creating dense structures that provide excellent thermal conductivity and electrical connectivity.
In addition to producing basic ceramic substrates, we offer additional processing and services such as laser machining, special coatings, and customized electrical property adjustments to meet specific requirements in different application fields. We are committed to providing high-quality, reliable products through technological innovation and rigorous quality control, working closely with customers to ensure we meet their technical and business objectives.
If you are interested in learning more about our production of Mitsubishi BT Substrate-like products, please feel free to contact us anytime. We are dedicated to providing support and services to meet your needs.
What are the 7 qualities of good customer service?
Good customer service is characterized by several key qualities that contribute to positive customer experiences and satisfaction. Here are seven essential qualities:
- Responsiveness: Customers appreciate prompt responses to their inquiries, concerns, or issues. A timely and proactive approach shows that their needs are valued and taken seriously.
- Empathy: Effective customer service involves understanding and empathizing with the customer’s situation or emotions. Empathetic responses help build trust and rapport, showing genuine care for their experience.
- Clear Communication: Clear and concise communication is crucial in ensuring customers understand information, instructions, or resolutions provided. Avoiding jargon and using language that is easy to understand enhances clarity.
- Knowledgeability: Knowledgeable customer service representatives inspire confidence by possessing in-depth knowledge about products, services, policies, and procedures. This enables them to provide accurate information and solutions.
- Problem-Solving Skills: The ability to identify and resolve issues efficiently is fundamental to good customer service. Problem-solving skills involve listening actively, analyzing situations, and offering effective solutions or alternatives.
- Professionalism: Professionalism encompasses courtesy, respectfulness, and maintaining a positive attitude, even in challenging situations. It contributes to a pleasant interaction and reflects well on the company’s image.
- Personalization: Tailoring interactions to the specific needs and preferences of each customer enhances their experience. Personalization can involve remembering past interactions, preferences, or suggesting relevant products or services based on their history.
These qualities collectively contribute to creating a positive customer service experience that fosters loyalty, satisfaction, and positive word-of-mouth recommendations for the business.
FAQs about Mitsubishi BT Substrate
What is Mitsubishi BT Substrate?
Mitsubishi BT Substrate refers to a high-performance ceramic-based substrate manufactured by Mitsubishi Materials Corporation. It is known for its excellent thermal management properties and is used in electronic packaging applications.
What are the key features of Mitsubishi BT Substrate?
Key features include high thermal conductivity, excellent electrical insulation, reliability in harsh environments, and compatibility with high-power applications. It is often used in industries such as automotive, aerospace, telecommunications, and power electronics.
How does Mitsubishi BT Substrate compare to traditional PCB materials?
Mitsubishi BT Substrate, being ceramic-based (typically aluminum nitride or aluminum oxide), offers much higher thermal conductivity compared to traditional organic PCB materials. This makes it more suitable for applications requiring efficient heat dissipation.
What are the applications of Mitsubishi BT Substrate?
It is used in various applications where thermal management is critical, such as power modules, LED packages, RF devices, and automotive electronics. Its reliability and thermal performance make it ideal for high-power and high-frequency applications.
What is the manufacturing process of Mitsubishi BT Substrate?
The manufacturing process involves preparing ceramic green sheets, applying circuit patterns and vias, stacking and laminating the layers, co-firing at high temperatures to fuse the ceramic and conductive materials, and finishing with surface treatments and testing.
Where can I purchase Mitsubishi BT Substrate?
Mitsubishi BT Substrate is typically available through authorized distributors of Mitsubishi Materials Corporation. Companies specializing in electronic components and substrates may also offer Mitsubishi BT Substrate or similar products.
What are the benefits of using Mitsubishi BT Substrate in electronic applications?
Benefits include enhanced thermal management, improved reliability, higher power handling capabilities, and better electrical performance compared to traditional PCB materials. It helps in reducing thermal resistance and maintaining stable operation of electronic components.