Multilayer Flip Chip Substrate Manufacturer
Multilayer Flip Chip Substrate Manufacturer,Multilayer Flip Chip Substrates revolutionize semiconductor packaging with their compact design and enhanced performance. By flipping semiconductor dies and mounting them directly onto the substrate, they minimize signal delay and interference, optimize thermal management, and reduce package size. These substrates employ advanced materials like organic laminates, ceramics, or silicon, carefully engineered for superior electrical and thermal properties. With their intricate layer stackups, precise routing, and efficient interconnections, Multilayer Flip Chip Substrates offer high reliability and density, making them ideal for demanding applications in microprocessors, graphics processors, and high-speed communication devices.
What is a Multilayer Flip Chip Substrate?
A Multilayer Flip Chip Substrate is a type of packaging technology used in semiconductor devices, particularly in integrated circuits (ICs). It’s designed to provide a compact and efficient means of connecting the semiconductor die (the actual chip) to the package substrate.
Here’s how it works:
- Flip Chip Technology: In flip chip technology, the semiconductor die is flipped upside down and mounted directly onto the substrate, rather than being mounted upright and wire-bonded. This allows for a shorter interconnection path between the die and the substrate, which can lead to improved electrical performance.
- Multilayer Substrate: The substrate, typically made of materials like silicon, organic laminate, or ceramic, consists of multiple layers of conductive traces and insulating layers. These layers are used to route signals between the die and the package’s external pins.
- Interconnections: The flip chip die is typically connected to the substrate using solder bumps or balls. These connections provide both electrical connections and mechanical support for the die.
- Signal Routing: The multilayer substrate provides a complex network of interconnections, allowing signals to be routed between different parts of the die and between the die and the package’s external pins. This routing is carefully designed to minimize signal delay and interference.
Overall, multilayer flip chip substrates offer advantages in terms of electrical performance, size, and reliability compared to traditional wire-bonding techniques. They are commonly used in high-performance ICs such as microprocessors, graphics processors, and high-speed communication chips.
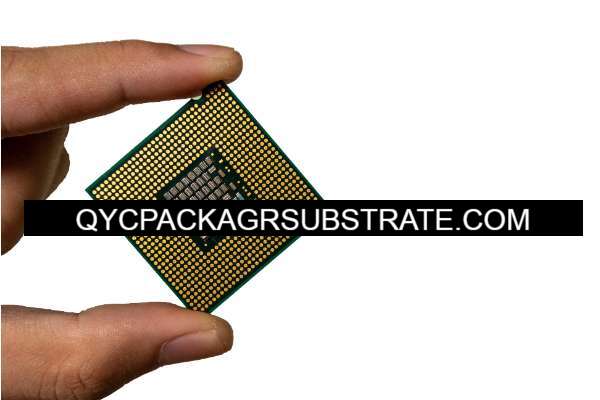
Multilayer Flip Chip Substrate Manufacturer
What are the Multilayer Flip Chip Substrate Design Guidelines?
Designing multilayer flip chip substrates requires careful consideration of various factors to ensure optimal performance, reliability, and manufacturability. Here are some general design guidelines:
- Signal Integrity: Maintain controlled impedance for critical signal paths to minimize signal reflections, crosstalk, and signal degradation. This involves carefully designing trace widths, thicknesses, and dielectric materials to achieve the desired impedance values.
- Power Delivery:Ensure efficient power distribution by minimizing voltage drops and impedance on power and ground planes. Use wide and low-impedance power and ground traces to reduce noise and voltage fluctuations.
- Thermal Management: Implement effective thermal management strategies to dissipate heat generated by the flip chip die. This may involve incorporating thermal vias, heat spreaders, and thermal pads to improve heat conduction and dissipation.
- Package Size and Form Factor: Design the substrate to fit within the desired package size and form factor while accommodating the flip chip die and external connections. Considerations include the number and arrangement of signal and power pins, as well as any space constraints imposed by the application.
- Materials Selection: Choose appropriate substrate materials based on factors such as electrical performance, thermal conductivity, cost, and manufacturability. Common substrate materials include organic laminates (e.g., FR-4), silicon, and ceramics (e.g., alumina, aluminum nitride).
- Routing and Layer Stackup:Optimize the layer stackup and routing topology to minimize signal path lengths, reduce layer-to-layer coupling, and avoid signal integrity issues. Use symmetric layer stackups and balanced routing to maintain signal symmetry and minimize skew.
- Reliability and Manufacturing Considerations:Design for manufacturability by adhering to industry standards and manufacturing capabilities. Consider factors such as solder joint reliability, solder mask design, and assembly process compatibility.
- EMI/EMC Compliance:Mitigate electromagnetic interference (EMI) and ensure electromagnetic compatibility (EMC) by incorporating EMI shielding techniques, such as ground planes and signal isolation, and adhering to EMI/EMC regulations and guidelines.
- Signal and Power Integrity Simulation: Perform thorough signal and power integrity simulations using specialized software tools to validate the design and identify potential issues before fabrication. This helps ensure that the substrate meets performance requirements under various operating conditions.
- Testability and Debugging: Design the substrate with testability in mind, including provisions for in-circuit testing, boundary scan testing, and debugging. Incorporate test points and access points for probing signals and debugging hardware issues during development and manufacturing.
By following these design guidelines, engineers can create multilayer flip chip substrates that meet the stringent requirements of modern semiconductor applications in terms of performance, reliability, and manufacturability.
What is the Multilayer Flip Chip Substrate Fabrication Process?
The fabrication process of a multilayer flip chip substrate involves several steps, each crucial for creating a high-quality substrate capable of reliably connecting the flip chip die to the package’s external pins. Here’s an overview of the typical fabrication process:
- Substrate Material Selection: Choose the appropriate substrate material based on factors such as electrical performance, thermal conductivity, cost, and manufacturability. Common substrate materials include organic laminates (e.g., FR-4), silicon, and ceramics (e.g., alumina, aluminum nitride).
- Layer Stackup Design:Design the layer stackup, specifying the number of layers, layer thicknesses, and materials. Considerations include signal integrity, power distribution, thermal management, and manufacturability.
- Lamination: Prepare the substrate by laminating multiple layers of conductive and insulating materials together. This typically involves bonding layers of copper-clad laminate and prepreg (insulating material) under heat and pressure to form a solid composite structure.
- Drilling: Drill holes (vias) through the substrate to connect different layers electrically. These vias serve as interconnections between the conductive traces on different layers and provide pathways for signals and power to pass through the substrate.
- Via Plating:Plate the drilled vias with a conductive material (typically copper) to create electrical connections between the layers. This process, known as via plating or through-hole plating, ensures continuity of electrical paths throughout the substrate.
- Circuit Patterning: Create the circuit patterns on each layer of the substrate using photolithography and etching techniques. Photolithography involves applying a photoresist layer, exposing it to UV light through a mask, and developing it to transfer the desired pattern onto the substrate surface. Etching removes unwanted copper from the substrate, leaving behind the desired circuit traces.
- Die Attach and Wire Bonding (Flip Chip): Prepare the flip chip die by attaching solder bumps or balls to its bonding pads. Place the die onto the substrate with the solder bumps aligned with corresponding pads on the substrate. Bond the die to the substrate by reflowing the solder, creating electrical and mechanical connections.
- Encapsulation:Encapsulate the flip chip die and wire bonds with a protective material (e.g., epoxy resin) to provide mechanical support and environmental protection. This encapsulation process helps prevent damage to the die and interconnections from mechanical stress, moisture, and contaminants.
- Surface Finish:Apply a surface finish to the substrate to protect exposed copper surfaces and facilitate soldering during assembly. Common surface finishes include solder mask, which covers the substrate except for solder pads, and surface coatings like immersion gold or tin-lead plating.
- Testing and Inspection: Perform electrical testing and visual inspection to ensure the substrate meets specifications and quality standards. Test for continuity, impedance, and insulation resistance, and inspect for defects such as shorts, opens, and solder voids.
- Final Assembly: Complete the substrate assembly by attaching external components, such as connectors and heat sinks, and integrating it into the overall package assembly.
By following these fabrication steps with precision and attention to detail, manufacturers can produce multilayer flip chip substrates that meet the performance, reliability, and quality requirements of demanding semiconductor applications.
How do you manufacture a Multilayer Flip Chip Substrate?
Manufacturing a multilayer flip chip substrate involves a detailed and precise process that integrates various steps to create a robust and reliable substrate capable of connecting flip chip dies to external components. Here’s a detailed overview of the manufacturing process:
- Substrate Material Selection: The manufacturing process begins with selecting the appropriate substrate material based on specific application requirements. Factors such as electrical performance, thermal conductivity, cost, and manufacturability influence this decision. Common substrate materials include organic laminates (e.g., FR-4), silicon, and ceramics (e.g., alumina, aluminum nitride).
- Layer Stackup Design: Design the layer stackup configuration, which determines the number of layers, layer thicknesses, and materials used in the substrate. Engineers carefully consider signal integrity, power distribution, thermal management, and manufacturability during this phase to optimize substrate performance.
- Lamination: The substrate fabrication process starts with laminating multiple layers of conductive and insulating materials together. This involves bonding layers of copper-clad laminate and prepreg (insulating material) under controlled temperature and pressure conditions to create a solid composite structure.
- Drilling: Drill holes, known as vias, through the substrate to establish electrical connections between different layers. These vias serve as pathways for signals and power to pass through the substrate, connecting conductive traces on different layers.
- Via Plating:Plate the drilled vias with a conductive material, typically copper, to ensure continuity of electrical paths throughout the substrate. Via plating involves depositing a thin layer of copper inside the vias through an electroplating process, forming reliable interconnections between layers.
- Circuit Patterning: Create circuit patterns on each layer of the substrate using photolithography and etching techniques. Photolithography involves applying a photoresist layer, exposing it to UV light through a mask, and developing it to transfer the desired pattern onto the substrate surface. Etching then removes unwanted copper from the substrate, leaving behind the desired circuit traces.
- Die Attach and Flip Chip Bonding: Prepare the flip chip die by attaching solder bumps or balls to its bonding pads. Place the die onto the substrate with the solder bumps aligned with corresponding pads on the substrate. Bond the die to the substrate by reflowing the solder, creating both electrical and mechanical connections.
- Encapsulation:Encapsulate the flip chip die and wire bonds with a protective material, such as epoxy resin, to provide mechanical support and environmental protection. This encapsulation process helps prevent damage to the die and interconnections from mechanical stress, moisture, and contaminants.
- Surface Finish:Apply a surface finish to the substrate to protect exposed copper surfaces and facilitate soldering during assembly. Common surface finishes include solder mask, which covers the substrate except for solder pads, and surface coatings like immersion gold or tin-lead plating.
- Testing and Inspection:Perform rigorous electrical testing and visual inspection to ensure the substrate meets specifications and quality standards. Test for continuity, impedance, insulation resistance, and inspect for defects such as shorts, opens, and solder voids.
- Final Assembly: Complete the substrate assembly by attaching external components, such as connectors and heat sinks, and integrating it into the overall package assembly.
By meticulously following each step of the manufacturing process with precision and attention to detail, manufacturers can produce multilayer flip chip substrates that meet the performance, reliability, and quality requirements of demanding semiconductor applications.
How much should a Multilayer Flip Chip Substrate cost?
The cost of a multilayer flip chip substrate can vary widely depending on several factors, including the complexity of the design, the materials used, the manufacturing process, and the volume of production. Here are some key considerations that influence the cost:
- Design Complexity: The complexity of the substrate design, including the number of layers, the density of interconnections, and the size of the substrate, directly impacts the cost. More complex designs typically require more materials and labor, contributing to higher manufacturing costs.
- Materials: The choice of substrate materials can significantly affect the cost. High-performance materials such as ceramic substrates tend to be more expensive than organic laminates. Additionally, specialized materials with enhanced electrical or thermal properties may command a premium price.
- Manufacturing Process: The manufacturing process complexity and sophistication influence the cost. Processes involving advanced technologies, precision equipment, and skilled labor tend to be more expensive. Additionally, any specialized processes required for features like fine-line routing, high-density interconnects, or embedded components can add to the cost.
- Volume of Production: Economies of scale play a significant role in determining the cost of multilayer flip chip substrates. Larger production volumes generally lead to lower per-unit costs due to efficiencies in material procurement, manufacturing setup, and overhead expenses.
- Testing and Quality Control: Rigorous testing and quality control measures contribute to the overall cost of the substrate. Comprehensive testing procedures, such as electrical testing, visual inspection, and reliability testing, ensure that the substrates meet performance and quality standards but may add to production costs.
- Supplier Relationships: The relationship between the buyer and the substrate manufacturer can also impact pricing. Long-term partnerships or bulk purchasing agreements may result in discounted pricing or preferential treatment, lowering the overall cost per unit.
- Market Conditions: Market dynamics, including supply and demand fluctuations, material prices, and competitive pressures, can influence substrate pricing. Additionally, factors such as currency exchange rates and geopolitical events may affect the cost of materials and manufacturing.
Given these considerations, it’s challenging to provide a precise cost estimate for a multilayer flip chip substrate without specific details about the design requirements and production volume. However, as a ballpark figure, multilayer flip chip substrates for high-performance applications can range from a few dollars to several hundred dollars per unit, with costs decreasing with higher production volumes and simpler designs.
What is Multilayer Flip Chip Substrate base material?
The base material used for multilayer flip chip substrates can vary depending on the specific application requirements and performance characteristics desired. Some common materials used as the base substrate for multilayer flip chip substrates include:
- Organic Laminates (e.g., FR-4): Organic laminates are widely used in electronic packaging due to their cost-effectiveness, ease of fabrication, and good mechanical properties. FR-4, a type of glass-reinforced epoxy laminate, is one of the most common substrate materials for multilayer PCBs and flip chip substrates.
- Ceramics (e.g., Alumina, Aluminum Nitride): Ceramics offer excellent thermal conductivity, mechanical strength, and electrical insulation properties, making them suitable for high-power and high-frequency applications. Alumina (aluminum oxide) and aluminum nitride are commonly used ceramic materials for multilayer flip chip substrates.
- Silicon: Silicon substrates offer high thermal conductivity and compatibility with semiconductor processes, making them suitable for applications requiring close integration with semiconductor devices. Silicon substrates are often used in advanced flip chip packaging solutions, especially for microelectromechanical systems (MEMS) and sensors.
- Flexible Substrates (e.g., Polyimide): Flexible substrates offer the advantage of flexibility and conformability, making them suitable for applications requiring bendability or integration into flexible electronics. Polyimide is a common flexible substrate material used in multilayer flip chip substrates for flexible PCBs and wearable devices.
- Metal Core Substrates (e.g., Aluminum): Metal core substrates consist of a metal core (typically aluminum) sandwiched between dielectric layers, providing excellent thermal conductivity for heat dissipation. These substrates are commonly used in high-power LED lighting applications and other thermal management-sensitive applications.
The choice of base material depends on factors such as electrical performance requirements, thermal management considerations, cost constraints, and manufacturability. Each material has its own set of advantages and limitations, and the selection process involves balancing these factors to meet the specific needs of the application. Additionally, hybrid substrates combining different materials or incorporating advanced features like embedded passive components may be used to achieve optimized performance and functionality.
Which company manufactures Multilayer Flip Chip Substrates?
Several companies manufacture multilayer flip chip substrates, including internationally renowned semiconductor packaging and electronics manufacturing companies such as Intel, TSMC, NXP Semiconductors, Micron Technology, and others. Additionally, there are companies specialized in providing packaging and interconnect solutions, such as Renesas Electronics, ON Semiconductor, and Amkor Technology.
Our company also manufactures multilayer flip chip substrates. We have advanced manufacturing equipment and a skilled technical team capable of meeting diverse customer needs. Our manufacturing process strictly adheres to international standards and industry best practices, ensuring reliable and stable product quality.
Firstly, we closely collaborate with customers to understand their product specifications, performance requirements, and production plans. Then, our design team designs the layer stackup and circuit layout of multilayer flip chip substrates according to customer requirements, taking into account factors such as signal integrity, power transmission, and thermal management.
Next, we utilize advanced manufacturing equipment and processes to carry out procedures such as lamination, drilling, copper plating, circuit pattern fabrication, and more. We rigorously control each manufacturing step to ensure product accuracy and consistency.
During the flip chip mounting stage, we employ advanced soldering techniques to ensure reliable connections between the chip and the substrate. Simultaneously, we conduct thorough quality inspection and testing to ensure that the products meet specification requirements and operate reliably.
Lastly, we offer flexible production volume solutions to meet customers’ varying order requirements. We are committed to providing high-quality products and excellent services to our customers, aiming for mutual benefit and win-win cooperation.
Overall, our company possesses the capability to manufacture multilayer flip chip substrates and is dedicated to providing customers with high-quality products and services.
What are the qualities of good customer service?
Good customer service involves several qualities that contribute to positive interactions and relationships between a company and its customers. Here are some essential qualities:
- Communication Skills:Effective communication is crucial for understanding customer needs, providing clear information, and resolving issues. Customer service representatives should listen actively, speak clearly, and convey empathy and understanding.
- Empathy and Understanding: Demonstrating empathy allows customer service representatives to connect with customers on a personal level, understand their feelings and perspectives, and provide appropriate support and solutions.
- Patience and Calmness: Dealing with customers can sometimes be challenging, especially when they are upset or frustrated. Patience and calmness help customer service representatives remain composed, handle difficult situations professionally, and find solutions without escalating tensions.
- Product Knowledge: Customer service representatives should have in-depth knowledge about the company’s products or services to answer questions accurately, provide helpful recommendations, and assist customers effectively.
- Problem-Solving Skills: Being able to identify issues, analyze problems, and find solutions efficiently is essential for resolving customer concerns and ensuring customer satisfaction. Customer service representatives should be proactive in addressing issues and taking ownership of resolutions.
- Adaptability: Every customer interaction is unique, and situations can change rapidly. Customer service representatives should be adaptable and flexible, able to adjust their approach based on the customer’s needs and the specific circumstances of each interaction.
- Professionalism: Maintaining professionalism is crucial in all customer interactions. This includes being respectful, courteous, and maintaining a positive attitude, regardless of the customer’s behavior or the complexity of the situation.
- Timeliness: Responding to customer inquiries and resolving issues promptly demonstrates respect for the customer’s time and urgency. Customer service representatives should strive to provide timely assistance and follow up as necessary to ensure customer needs are met promptly.
- Attention to Detail: Paying attention to detail ensures that customer requests are accurately documented, solutions are implemented correctly, and follow-up actions are completed as promised. Small details can make a significant difference in the overall customer experience.
- Continuous Improvement: Good customer service involves a commitment to continuous improvement. Companies should regularly gather feedback from customers, analyze trends and patterns, and make adjustments to processes, policies, and training to enhance the quality of service provided.
By embodying these qualities, companies can build strong customer relationships, foster loyalty, and differentiate themselves in the marketplace through excellent customer service.
FAQs
What is a multilayer flip chip substrate?
A multilayer flip chip substrate is a type of packaging technology used in semiconductor devices, particularly in integrated circuits (ICs). It provides a compact and efficient means of connecting the semiconductor die (chip) to the package substrate.
How does a multilayer flip chip substrate work?
In flip chip technology, the semiconductor die is flipped upside down and mounted directly onto the substrate, rather than being mounted upright and wire-bonded. This allows for shorter interconnection paths between the die and the substrate, improving electrical performance.
What are the advantages of multilayer flip chip substrates?
Some advantages include improved electrical performance, reduced signal delay and interference, enhanced thermal management, smaller package size, and higher packaging density compared to traditional wire-bonding techniques.
What materials are used in multilayer flip chip substrates?
Common substrate materials include organic laminates (e.g., FR-4), ceramics (e.g., alumina, aluminum nitride), silicon, and flexible substrates (e.g., polyimide). The choice of material depends on factors such as electrical performance, thermal conductivity, and cost.
What are the design considerations for multilayer flip chip substrates?
Design considerations include signal integrity, power delivery, thermal management, package size and form factor, materials selection, routing and layer stackup, reliability, electromagnetic interference (EMI) compliance, and testability.
What is the fabrication process for multilayer flip chip substrates?
The fabrication process involves steps such as substrate material selection, layer stackup design, lamination, drilling, via plating, circuit patterning, die attach and flip chip bonding, encapsulation, surface finish, testing, and final assembly.
What companies manufacture multilayer flip chip substrates?
Several companies manufacture multilayer flip chip substrates, including semiconductor packaging and electronics manufacturing companies such as Intel, TSMC, NXP Semiconductors, Micron Technology, and others.
What are the cost considerations for multilayer flip chip substrates?
The cost of multilayer flip chip substrates varies depending on factors such as design complexity, materials used, manufacturing process, volume of production, testing and quality control, supplier relationships, and market conditions. Costs can range from a few dollars to several hundred dollars per unit.