MW2000 Materials PCB Manufacturer
MW2000 Materials PCB Manufacturer.High speed and high frequency material packaging substrate Manufacturer. Advanced packaging substrate production process and technology
MW2000 Materials PCBs represent a pinnacle of innovation in high-frequency electronics. Constructed using specialized MW2000 materials, these PCBs offer unparalleled performance in applications where signal integrity is paramount. With their low dielectric constant, minimal dissipation factor, and exceptional dimensional stability, MW2000 Materials PCBs ensure reliable signal transmission even at the highest frequencies. Whether it’s in the telecommunications sector, aerospace industry, radar systems, or high-speed data transmission, MW2000 Materials PCBs excel, providing engineers with a robust foundation for their designs. Their ability to withstand harsh environmental conditions while maintaining precise electrical properties makes them indispensable in critical electronic systems. Backed by advanced fabrication techniques and stringent quality control measures, MW2000 Materials PCBs represent the forefront of PCB technology, empowering industries to push the boundaries of high-frequency electronics and achieve new levels of performance and reliability.
What is a MW2000 Materials PCB?
The term “MW2000 Materials PCB” refers to a type of printed circuit board (PCB) that utilizes MW2000 materials in its construction. These materials are often chosen for their specific electrical and mechanical properties, making them suitable for various applications, particularly in industries where high-frequency performance is crucial.
MW2000 materials are a type of high-frequency laminate commonly used in PCB fabrication. They typically exhibit low dielectric constant and low loss tangent characteristics, which are essential for maintaining signal integrity at high frequencies. These properties make MW2000 materials ideal for applications such as telecommunications, aerospace, radar systems, and high-speed data transmission.
When designing a PCB using MW2000 materials, engineers must consider factors such as impedance control, signal propagation, and thermal management to ensure optimal performance. The choice of substrate material significantly impacts the overall performance and reliability of the PCB, especially in high-frequency applications where signal integrity is critical.
MW2000 Materials PCBs are often manufactured using advanced fabrication techniques such as multilayer construction, controlled impedance routing, and precision etching processes. These techniques help to minimize signal losses, reduce electromagnetic interference (EMI), and improve overall reliability.
In addition to their electrical properties, MW2000 materials also offer excellent mechanical strength and dimensional stability, which are essential for withstanding harsh environmental conditions and mechanical stress. This makes MW2000 Materials PCBs suitable for use in demanding applications where reliability and durability are paramount.
Overall, MW2000 Materials PCBs play a crucial role in enabling high-performance electronic systems, particularly in industries where high-frequency signal transmission is required. Their unique combination of electrical and mechanical properties makes them a preferred choice for engineers and designers seeking to achieve optimal performance and reliability in their PCB designs.
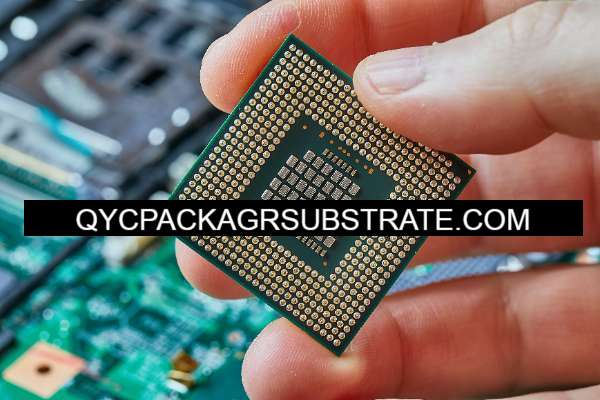
MW2000 Materials PCB Manufacturer
What are MW2000 Materials PCB Design Guidelines?
Designing a PCB with MW2000 materials requires careful consideration of various factors to ensure optimal performance. Here are some general design guidelines for MW2000 Materials PCBs:
- Impedance Control: MW2000 materials typically have specific dielectric constants and loss tangents. To maintain signal integrity, it’s crucial to design traces with controlled impedance matching the characteristic impedance of the transmission lines.
- Layer Stackup: Choose an appropriate layer stackup configuration that meets the requirements of your design. Consider factors such as signal layers, power planes, and ground planes, ensuring proper signal isolation and return paths.
- Trace Width and Spacing: Determine the appropriate trace widths and spacing based on the desired impedance and current-carrying capacity. Ensure that traces are sufficiently spaced to prevent crosstalk and signal interference.
- Via Design: Use vias strategically to connect different layers of the PCB. Pay attention to via placement and sizing to minimize signal reflections and impedance mismatches.
- Grounding: Implement a solid ground plane on the PCB to provide a low-impedance return path for signals and minimize electromagnetic interference (EMI). Proper grounding techniques, such as star grounding or stitching vias, can help reduce noise and improve signal integrity.
- High-Frequency Considerations: MW2000 materials are often used in high-frequency applications. Take into account high-frequency effects such as skin effect, dielectric losses, and parasitic capacitance when designing the PCB layout.
- Thermal Management: MW2000 materials may have different thermal properties compared to standard FR-4 substrates. Consider thermal management techniques such as thermal vias, heatsinks, or copper pours to dissipate heat effectively and prevent overheating of components.
- Component Placement: Place components strategically to minimize signal path lengths and reduce signal distortion. Consider signal integrity, thermal dissipation, and assembly constraints when arranging components on the PCB.
- Signal Integrity Simulation:Perform signal integrity simulations using specialized software tools to analyze the behavior of high-speed signals on the PCB. This helps identify and mitigate potential signal integrity issues before fabrication.
- Manufacturability: Consider manufacturability aspects such as fabrication tolerances, material availability, and PCB manufacturing processes when designing with MW2000 materials. Consult with your PCB manufacturer to ensure that the design meets their capabilities and requirements.
By following these guidelines, you can design MW2000 Materials PCBs that meet the performance, reliability, and manufacturability requirements of your specific application.
What is the MW2000 Materials PCB Fabrication Process?
The fabrication process for MW2000 Materials PCBs is similar to that of traditional printed circuit boards but requires special attention to the unique properties of MW2000 materials. Here’s an overview of the fabrication process:
- Material Selection: The first step is to select the MW2000 material suitable for the specific requirements of the PCB design. MW2000 materials are typically available in various grades and thicknesses, so choose the appropriate material based on factors such as dielectric constant, loss tangent, and thermal properties.
- Design: Create the PCB layout using PCB design software. Follow design guidelines specific to MW2000 materials, such as impedance control, high-frequency considerations, and thermal management. Ensure that the design meets the electrical, mechanical, and manufacturability requirements.
- Preparation of Substrate: Prepare the MW2000 substrate for the fabrication process. This may involve cleaning the substrate surface to remove any contaminants and ensuring uniformity of the substrate material.
- Lamination: In the lamination process, multiple layers of MW2000 material are bonded together to create the PCB stackup. This may involve stacking alternating layers of copper foil and MW2000 substrate material. The stackup configuration should follow the design requirements, including the number of signal layers, power planes, and ground planes.
- Drilling: Precision drills are used to create holes in the PCB for through-hole components and vias. Careful attention is paid to drill accuracy and alignment to ensure proper registration between layers.
- Through-hole Plating: After drilling, the holes are plated with conductive material to establish electrical connections between different layers of the PCB. Through-hole plating ensures reliable electrical continuity and mechanical strength.
- Circuit Patterning: A layer of copper is deposited onto the surface of the PCB substrate through a process called copper plating or electroplating. This copper layer forms the conductive traces and pads of the PCB. Photolithography and etching techniques are then used to define the circuit pattern on the copper layer.
- Surface Finishing: After circuit patterning, the PCB surface is coated with a surface finish to protect the copper traces from oxidation and ensure solderability. Common surface finishes for MW2000 Materials PCBs include immersion gold, immersion silver, and HASL (Hot Air Solder Leveling).
- Final Inspection: The fabricated PCB undergoes a series of inspections to ensure quality and reliability. This may include electrical testing, dimensional inspection, and visual inspection to check for defects or irregularities.
- Assembly: Once the PCBs pass inspection, they are ready for component assembly. Surface-mount and through-hole components are soldered onto the PCB according to the assembly instructions.
- Testing: After assembly, the PCBs undergo functional testing to verify proper operation and performance. This may involve electrical testing, environmental testing, and reliability testing to ensure that the PCB meets the specified requirements.
By following these steps, manufacturers can fabricate MW2000 Materials PCBs with high precision and reliability, suitable for a wide range of high-frequency applications.
How do you manufacture MW2000 Materials PCB?
Manufacturing MW2000 Materials PCBs involves a series of steps tailored to the unique properties of MW2000 materials. Here’s a detailed overview of the manufacturing process:
- Material Selection: Choose the appropriate MW2000 material based on the specific requirements of the PCB design, including dielectric constant, loss tangent, and thermal properties. MW2000 materials are available in various grades and thicknesses to suit different applications.
- Preparation of Substrate: Prepare the MW2000 substrate for the fabrication process. This may involve cleaning the substrate surface to remove any contaminants and ensuring uniformity of the material.
- Layer Stackup: Determine the layer stackup configuration based on the PCB design requirements. MW2000 Materials PCBs often involve multiple layers of substrate bonded together with copper foils sandwiched in between. Ensure proper alignment and registration of the layers.
- Drilling: Precision drills are used to create holes in the PCB for through-hole components and vias. The drilling process requires careful attention to accuracy and alignment to ensure proper registration between layers.
- Through-hole Plating: After drilling, the holes are plated with conductive material to establish electrical connections between different layers of the PCB. Through-hole plating ensures reliable electrical continuity and mechanical strength.
- Circuit Patterning: A layer of copper is deposited onto the surface of the PCB substrate through a process called copper plating or electroplating. This copper layer forms the conductive traces and pads of the PCB. Photolithography and etching techniques are then used to define the circuit pattern on the copper layer.
- Surface Finishing: Apply a surface finish to the PCB to protect the copper traces from oxidation and ensure solderability. Common surface finishes for MW2000 Materials PCBs include immersion gold, immersion silver, and HASL (Hot Air Solder Leveling).
- Final Inspection: The fabricated PCB undergoes a series of inspections to ensure quality and reliability. This may include electrical testing, dimensional inspection, and visual inspection to check for defects or irregularities.
- Component Assembly: Once the PCBs pass inspection, they are ready for component assembly. Surface-mount and through-hole components are soldered onto the PCB according to the assembly instructions.
- Testing: After assembly, the PCBs undergo functional testing to verify proper operation and performance. This may involve electrical testing, environmental testing, and reliability testing to ensure that the PCB meets the specified requirements.
By following these manufacturing steps, PCB manufacturers can produce high-quality MW2000 Materials PCBs suitable for a wide range of high-frequency applications. It’s essential to adhere to industry standards and best practices to ensure the reliability and performance of the finished PCBs.
How much should a MW2000 Materials PCB cost?
The cost of a MW2000 Materials PCB can vary significantly depending on several factors such as the size, complexity, layer count, material thickness, surface finish, and quantity needed. Additionally, factors like the manufacturer’s capabilities, location, and current market conditions can also influence pricing.
As a rough estimate, MW2000 Materials PCBs typically cost more than standard FR-4 PCBs due to the specialized properties of MW2000 materials and the manufacturing processes involved. However, without specific details about your PCB design and requirements, it’s challenging to provide an exact cost.
For a more accurate cost estimation, it’s best to reach out to PCB manufacturers or suppliers directly and provide them with detailed specifications of your design. They can then provide you with a quote based on your specific requirements and quantities needed. Additionally, you may consider obtaining quotes from multiple manufacturers to compare prices and ensure you’re getting a competitive offer.
Keep in mind that factors such as quality, reliability, lead time, and customer support are also crucial considerations when selecting a PCB manufacturer, so it’s essential to evaluate these aspects along with pricing.
What is MW2000 Materials PCB base material?
MW2000 materials are a type of high-frequency laminate used as the base material for MW2000 Materials PCBs. These materials are specifically designed to meet the demanding requirements of high-frequency applications, offering characteristics such as low dielectric constant (Dk), low dissipation factor (Df), and excellent dimensional stability.
MW2000 materials are often composed of a combination of woven glass fabric or non-woven aramid fiber reinforcement impregnated with a thermosetting resin matrix, such as polytetrafluoroethylene (PTFE) or polyimide (PI). The resin matrix provides mechanical strength and stability, while the reinforcement materials offer excellent electrical properties and thermal stability.
One common example of a MW2000 material is Rogers Corporation’s RO4000® series, which includes substrates like RO4350B™ and RO4360G2™. These materials are widely used in high-frequency PCB applications due to their exceptional electrical performance, reliable mechanical properties, and compatibility with standard PCB fabrication processes.
MW2000 Materials PCB base materials are engineered to provide consistent electrical performance across a wide range of frequencies, making them suitable for applications such as telecommunications, aerospace, radar systems, and high-speed data transmission. Their low loss tangent and stable dielectric properties make them ideal for high-frequency circuit designs where signal integrity is critical.
Which company makes MW2000 Materials PCB?
The production of MW2000 Materials PCBs is typically undertaken by specialized PCB manufacturing companies. Some well-known PCB manufacturers such as Rogers Corporation and Taconic Advanced Dielectric Division produce MW2000 materials and related PCB substrates. Their products are widely used in high-frequency electronic devices, wireless communications, aerospace, and other industries.
In our company, we also have the capability to produce MW2000 Materials PCBs. We have advanced production equipment and technology, a professional engineering team, and extensive experience to meet customers’ various needs for high-frequency PCBs. We adhere to strict quality control processes to ensure that each PCB meets the requirements of customers and industry standards.
We can provide a variety of MW2000 material options, including the RO4000 series and other commonly used high-frequency PCB materials. We can customize PCB layer thickness, stackup configurations, surface treatments, and other specific requirements according to customer needs. Whether it’s for prototyping or mass production orders, we can deliver high-quality MW2000 Materials PCBs on time.
Our engineering team has extensive experience in PCB design and manufacturing and can provide customers with professional technical support and advice. We are committed to working with customers to ensure the success of their projects. If you have a project that requires the production of MW2000 Materials PCBs, please feel free to contact us, and we will provide you with the highest quality service and products.
What are the 7 qualities of good customer service?
Good customer service is essential for maintaining customer satisfaction and loyalty. Here are seven qualities that characterize good customer service:
- Responsiveness: Good customer service involves promptly addressing customer inquiries, concerns, and issues. Responding to customer queries in a timely manner shows that you value their time and are committed to providing assistance when needed.
- Empathy: Empathy involves understanding and acknowledging the customer’s feelings, perspectives, and needs. Good customer service representatives demonstrate empathy by listening actively, showing compassion, and expressing genuine concern for the customer’s situation.
- Clear Communication: Effective communication is crucial for providing good customer service. Clear and concise communication helps ensure that customers understand the information provided and can make informed decisions. Customer service representatives should communicate in a friendly, professional manner and avoid using jargon or technical language that may confuse customers.
- Problem-solving Skills: Good customer service involves effectively resolving customer issues and addressing their concerns. Customer service representatives should be knowledgeable about products or services, able to troubleshoot problems, and offer appropriate solutions or alternatives to meet customer needs.
- Positive Attitude: Maintaining a positive attitude is important for delivering good customer service. Customer service representatives should be courteous, enthusiastic, and optimistic, even when dealing with challenging situations or difficult customers. A positive attitude helps create a pleasant customer experience and fosters customer satisfaction.
- Adaptability: Good customer service requires flexibility and adaptability to meet the diverse needs of customers. Customer service representatives should be able to adjust their approach based on individual customer preferences, communication styles, and problem-solving strategies. Being adaptable allows for better customization of service and enhances the overall customer experience.
- Follow-up and Feedback: Following up with customers after resolving their issues or completing a transaction demonstrates commitment to customer satisfaction. Good customer service involves seeking feedback from customers to understand their experiences, preferences, and areas for improvement. Customer feedback helps identify opportunities to enhance service quality and build stronger customer relationships.
By embodying these qualities, businesses can deliver exceptional customer service that builds trust, loyalty, and positive brand perception among customers.
FAQs
What are MW2000 Materials PCBs?
MW2000 Materials PCBs are printed circuit boards constructed using MW2000 materials, which are specialized high-frequency laminates designed for applications requiring excellent electrical performance at high frequencies.
What are the advantages of MW2000 Materials PCBs?
MW2000 Materials PCBs offer low dielectric constant, low dissipation factor, and excellent dimensional stability, making them ideal for high-frequency applications where signal integrity is critical. They also provide good thermal properties and mechanical strength.
What are the typical applications of MW2000 Materials PCBs?
MW2000 Materials PCBs are commonly used in industries such as telecommunications, aerospace, radar systems, high-speed data transmission, and other applications requiring high-frequency signal transmission and reliability.
How do MW2000 Materials PCBs differ from standard FR-4 PCBs?
MW2000 Materials PCBs offer superior electrical performance, particularly at high frequencies, compared to standard FR-4 PCBs. They have lower dielectric loss and better impedance control, making them suitable for high-frequency designs.
What design considerations are important for MW2000 Materials PCBs?
Design considerations for MW2000 Materials PCBs include impedance control, layer stackup configuration, trace width and spacing, grounding techniques, high-frequency effects, and thermal management to ensure optimal performance and reliability.
Can MW2000 Materials PCBs be manufactured using standard PCB fabrication processes?
Yes, MW2000 Materials PCBs can typically be manufactured using standard PCB fabrication processes, although some adjustments may be necessary to accommodate the unique properties of MW2000 materials, such as lower processing temperatures and specialized handling.
Where can I find a reliable manufacturer for MW2000 Materials PCBs?
Reliable PCB manufacturers with expertise in high-frequency designs, such as Rogers Corporation and Taconic Advanced Dielectric Division, produce MW2000 Materials PCBs. Additionally, many other specialized PCB manufacturers offer MW2000 Materials PCB fabrication services.