N4000-13 Series Materials PCB Manufacturer
N4000-13 Series Materials PCB Manufacturer,The N4000-13 Series Materials PCB is a specialized substrate material tailored for high-frequency and microwave applications. Known for its exceptional electrical properties, this material is typically based on a ceramic or PTFE (polytetrafluoroethylene) composition, offering low dielectric loss and high thermal stability. N4000-13 PCBs are meticulously engineered with precise impedance control, optimized signal trace layouts, and effective shielding techniques to minimize signal distortion and electromagnetic interference. They are crucial in industries such as telecommunications, aerospace, and radar systems, where reliability and performance at microwave frequencies are paramount. N4000-13 Series Materials PCBs ensure robust signal integrity and efficiency in demanding electronic applications.
What is an N4000-13 Series Materials PCB?
The N4000-13 Series Materials PCB refers to a specific type of printed circuit board (PCB) designed to meet stringent requirements in various electronic applications. These PCBs are typically used in environments where reliability, performance, and durability are critical factors. The “N4000-13” designation suggests adherence to particular material and manufacturing standards, ensuring high-quality construction.
These PCBs are often employed in industries such as telecommunications, aerospace, medical devices, and military applications, where they must withstand harsh conditions and maintain stable performance over time. The materials used in N4000-13 Series PCBs are selected for their electrical properties, mechanical strength, thermal stability, and resistance to environmental factors like moisture and chemicals.
Manufacturers of N4000-13 Series Materials PCBs adhere to strict guidelines to ensure consistency and reliability across production batches. They may utilize advanced fabrication techniques such as multilayer stacking, controlled impedance routing, and surface finishes suitable for soldering and component mounting.
Engineers and designers often choose N4000-13 Series Materials PCBs for their ability to support high-frequency signals, maintain signal integrity, and provide a reliable platform for complex electronic circuits. These PCBs play a crucial role in the performance and longevity of electronic devices and systems where precision and reliability are paramount.
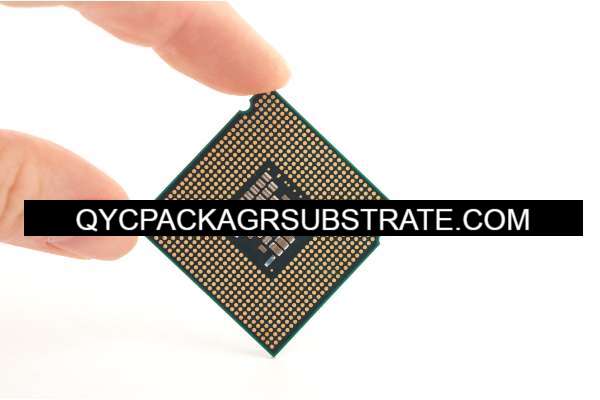
N4000-13 Series Materials PCB Manufacturer
What are the N4000-13 Series Materials PCB Design Guidelines?
The N4000-13 Series Materials PCB design guidelines typically encompass several key considerations to ensure the PCB meets performance, reliability, and manufacturing requirements. While specific guidelines may vary slightly depending on the manufacturer and application, here are common aspects covered:
- Material Selection: The N4000-13 series specifies certain laminate materials with specific dielectric constants (Dk) and dissipation factors (Df). These materials are chosen to ensure stable electrical performance, especially at high frequencies.
- Layer Stack-up: Guidelines typically include a recommended layer stack-up configuration to achieve desired impedance control, signal integrity, and thermal management. This involves specifying the number of layers, the order of signal and power planes, and the arrangement of ground layers.
- Trace Routing and Impedance Control:Design guidelines emphasize maintaining controlled impedance for critical signal traces. This involves calculating and adhering to specific trace widths, spacing, and layer-to-layer transitions to match required impedance values.
- Via Design: Recommendations cover via types (such as microvias), sizes, and placement to minimize signal degradation and ensure reliable electrical connections between layers.
- Thermal Management:Guidelines often include recommendations for thermal vias, copper pour areas, and placement of components to manage heat dissipation effectively, ensuring reliable operation and longevity of the PCB.
- Component Placement: Optimal component placement is crucial for signal integrity, minimizing electromagnetic interference (EMI), and ensuring ease of manufacturing and assembly.
- Design for Manufacturing (DFM): Considerations for DFM practices such as panelization, fiducial marker placement, and clearances for manufacturing processes like soldering and testing are typically part of the guidelines.
- Reliability and Testing: Recommendations may include design features to enhance reliability, such as conformal coating options, testing points, and testability features to facilitate testing and troubleshooting during manufacturing and maintenance.
- Environmental Considerations: Guidelines may address factors like resistance to moisture, chemicals, and mechanical stress, depending on the intended application and environmental conditions.
- Compliance and Standards: Ensuring compliance with industry standards and certifications relevant to the application area (e.g., IPC standards for PCB design and manufacturing) is often emphasized.
These guidelines are crucial for ensuring that N4000-13 Series Materials PCBs meet performance specifications, reliability targets, and manufacturing feasibility, ultimately supporting the quality and functionality of electronic systems in demanding applications.
What is the N4000-13 Series Materials PCB Fabrication Process?
The fabrication process for N4000-13 Series Materials PCBs involves several precise steps to ensure the boards meet stringent performance and reliability standards. Here’s an overview of the typical fabrication process:
- Material Selection: The process begins with selecting high-quality laminate materials that meet the specifications of the N4000-13 series. These materials are chosen based on their dielectric properties (dielectric constant and dissipation factor), thermal stability, mechanical strength, and suitability for high-frequency applications.
- Design Input: Engineers provide the PCB design files (Gerber files, CAD drawings) along with specific design guidelines tailored to the N4000-13 series materials. These guidelines include layer stack-up details, trace widths and spacing for controlled impedance, via types and sizes, thermal management considerations, and other design parameters.
- Preparation of Substrates: The chosen laminate materials are prepared by cutting them to size according to the PCB design specifications. Surface preparation may involve cleaning and treating the laminate surfaces to ensure proper adhesion of copper foils.
- Copper Cladding: Copper foils are typically bonded to both sides of the laminate material using an adhesive. The copper foils are chosen based on thickness requirements specified in the design. The bonding process ensures a strong, reliable connection between the copper and the substrate.
- Laser Drilling and Mechanical Drilling:Depending on the design, holes for vias and component mounting pads are drilled using either laser drilling (for microvias) or mechanical drilling (for through-holes). The drilling process must be precise to meet the design’s dimensional and positional tolerances.
- Electroless Copper Deposition: After drilling, the exposed surfaces inside the holes are chemically treated to promote adhesion, followed by electroless copper deposition. This step ensures that the inner surfaces of the holes are conductive, facilitating subsequent plating processes.
- Plating: Copper is plated onto the surfaces of the PCB to form the circuit traces and pads. This plating process builds up the required copper thickness on the surface and inside the drilled holes to meet the design specifications for electrical conductivity and mechanical strength.
- Etching: Excess copper that is not part of the circuit pattern is etched away using a chemical etchant. The etching process defines the final shape and dimensions of the circuit traces and pads according to the design files.
- Surface Finish: The PCB surface is finished with a coating that protects the copper traces from oxidation and provides a suitable surface for soldering components. Common surface finishes include HASL (Hot Air Solder Leveling), ENIG (Electroless Nickel Immersion Gold), and OSP (Organic Solderability Preservatives).
- Silkscreen and Legend Printing: Information such as component outlines, reference designators, and other markings are printed onto the PCB surface using silkscreen printing. This step helps during component assembly and troubleshooting.
- Testing and Inspection:The fabricated PCBs undergo rigorous testing and inspection to ensure they meet the design specifications and quality standards. This may include electrical testing, dimensional inspection, and checks for solderability and cleanliness.
- Final Finishing and Packaging: Once the PCBs pass inspection, they are trimmed to their final dimensions, cleaned if necessary, and packaged according to customer requirements for shipment.
Throughout the entire fabrication process, adherence to the N4000-13 series materials specifications and design guidelines is critical to producing PCBs that offer high performance, reliability, and longevity in demanding electronic applications. Each step involves precision and attention to detail to achieve consistent quality in the final product.
How do you manufacture an N4000-13 Series Materials PCB?
Manufacturing an N4000-13 Series Materials PCB involves a meticulous process to ensure high reliability and performance. Here’s a detailed outline of the typical manufacturing steps:
- Material Selection: Choose laminate materials that meet N4000-13 series specifications, focusing on factors like dielectric constant, dissipation factor, thermal stability, and mechanical strength.
- Design Input:Provide PCB design files (Gerber files, CAD drawings) with specific guidelines for layer stack-up, trace widths, controlled impedance, via types, and other design parameters tailored to N4000-13 series materials.
- Substrate Preparation: Cut laminate materials to size and clean surfaces for proper adhesion of copper foils.
- Copper Foil Lamination: Bond copper foils to laminate using adhesives, ensuring strong adhesion and uniform coverage.
- Drilling: Drill holes for vias and component pads using laser drilling (for microvias) or mechanical drilling (for through-holes), ensuring precision and alignment with design specifications.
- Electroless Copper Deposition: Treat drilled holes to promote adhesion, then deposit copper to form conductive paths inside vias and on the PCB surface.
- Plating: Plate additional copper to achieve desired trace thickness and build-up inside vias, ensuring electrical conductivity and mechanical integrity.
- Etching: Use chemical etching to remove excess copper, defining circuit traces and pad shapes according to design specifications.
- Surface Finish: Apply surface finish (e.g., HASL, ENIG, OSP) to protect copper traces, enhance solderability, and prevent oxidation.
- Silkscreen Printing: Print component outlines, reference designators, and other markings onto the PCB surface to aid assembly and troubleshooting.
- Testing and Inspection: Conduct electrical tests, dimensional checks, solderability tests, and visual inspections to verify PCB quality and compliance with design requirements.
- Final Finishing: Trim PCBs to final dimensions, clean if necessary, and package according to customer specifications for shipment.
Throughout the manufacturing process, strict adherence to N4000-13 series materials specifications and design guidelines ensures the PCBs meet high standards for performance, reliability, and durability in various electronic applications. Each step requires precision and quality control to produce PCBs that function reliably in demanding environments.
How much should an N4000-13 Series Materials PCB cost?
The cost of an N4000-13 Series Materials PCB can vary widely depending on several factors:
- Board Size and Complexity: Larger boards or those with intricate designs requiring more layers, tighter trace widths, and complex features will generally cost more to manufacture.
- Material Specifications: N4000-13 series materials typically have specific properties that may be more expensive compared to standard PCB materials. The cost can vary based on the exact laminate material chosen and its availability.
- Manufacturing Technology: Certain technologies such as laser drilling for microvias, high-precision etching, and advanced surface finishes (e.g., ENIG) can increase manufacturing costs.
- Quantity: Economies of scale apply, meaning larger production quantities generally reduce the cost per unit due to bulk purchasing of materials and optimized production processes.
- Lead Time: Expedited production schedules or quick-turn services may come with higher costs to prioritize faster delivery.
- Supplier and Location: PCB manufacturing costs can also vary based on the supplier’s capabilities, geographical location, and their pricing structure.
To provide a rough estimate, a standard 2-layer PCB using N4000-13 series materials, with moderate complexity and a standard lead time, might range from approximately $50 to $200 per board for small quantities. Prices can decrease significantly for larger production volumes, possibly ranging from $10 to $50 per board or lower.
For accurate pricing, it’s recommended to obtain quotes from multiple PCB manufacturers. They can provide tailored estimates based on your specific design requirements, material choices, volume needs, and desired delivery timelines. This approach ensures you get the best balance of cost, quality, and service for your N4000-13 Series Materials PCBs.
What is N4000-13 Series Materials PCB base material?
The base material used in N4000-13 Series Materials PCB typically refers to the laminate material that forms the core substrate of the printed circuit board. This material is chosen for its specific electrical, mechanical, and thermal properties that meet the stringent requirements of the N4000-13 series specifications.
While exact details of the base material can vary depending on the manufacturer and specific application, N4000-13 series materials generally include high-performance substrates that exhibit:
- Dielectric Constant (Dk):Consistent and stable electrical properties, especially at high frequencies, to ensure minimal signal loss and impedance control.
- Dissipation Factor (Df): Low dissipation factor for efficient signal transmission and minimal energy loss.
- Thermal Stability: Capability to withstand elevated temperatures encountered during manufacturing processes like soldering and assembly, as well as during operation in electronic devices.
- Mechanical Strength:Sufficient mechanical strength to support components and withstand mechanical stresses encountered during handling and operation.
- Dimensional Stability: Minimal dimensional changes under varying temperature and humidity conditions to ensure reliability over the PCB’s lifespan.
Common materials used in N4000-13 series PCBs may include specialized laminates such as:
– Polytetrafluoroethylene (PTFE) Based Materials: Examples include materials like Teflon, which offer excellent electrical performance and thermal stability.
– Hybrid Laminates: These may combine different materials to achieve a balance of electrical properties, mechanical strength, and cost-effectiveness.
– Ceramic Filled Laminates: Incorporating ceramic fillers to enhance thermal conductivity and mechanical properties.
– High-Frequency Laminates: Optimized for high-frequency applications where low loss tangent and consistent dielectric properties are critical.
The choice of base material is crucial in determining the overall performance and reliability of the PCB in applications where high-frequency signals, signal integrity, and reliability are paramount. Manufacturers of N4000-13 series materials ensure that the base materials used meet specific standards and undergo rigorous testing to ensure they adhere to the required electrical and mechanical specifications.
Which company makes N4000-13 Series Materials PCB?
The PCBs of the N4000-13 series are typically manufactured by specialized PCB manufacturing companies. These companies have a good reputation and extensive experience in the electronics manufacturing industry, capable of meeting high-performance and high-reliability requirements. Specifically regarding our company, we have the capability to produce PCBs that meet the specifications of the N4000-13 series materials. Here are our main strengths and capabilities:
- Advanced Manufacturing Facilities and Technology: We possess advanced PCB manufacturing facilities and technologies, including high-precision automated equipment and advanced process control systems. These facilities and technologies ensure that we can manufacture complex PCB designs such as multilayer boards, microvias, controlled impedance, and other advanced features.
- Professional Design and Engineering Team: We have an experienced team of designers and engineers who can provide comprehensive support from design consultation to sample validation. Our team can customize PCB design solutions that comply with the specifications of N4000-13 series materials based on specific customer requirements.
- Quality Management and Certifications: We strictly adhere to international PCB manufacturing standards and quality management systems, ensuring that each production step undergoes detailed inspection and testing. Our PCB products are certified under ISO 9001 quality management system, guaranteeing stable product quality and performance.
- Customized Customer Service: We prioritize communication and cooperation with our customers, offering flexible solutions to meet various project requirements and demands. Whether it is small batch production or large-scale mass production, we can provide high-quality and reliable PCB products made from N4000-13 series materials.
With our company’s capabilities and experience, we are able to deliver PCB solutions that meet the requirements of the N4000-13 series materials, committed to supporting and ensuring the success of our customers’ projects through continuous technological innovation and quality improvement.
What are the 7 qualities of good customer service?
Good customer service is characterized by several key qualities that contribute to a positive experience for customers. Here are seven important qualities:
- Responsiveness: Good customer service is prompt and responsive. It involves acknowledging customer inquiries, concerns, or issues quickly and providing timely assistance or solutions.
- Empathy: Empathy involves understanding and acknowledging the customer’s feelings, concerns, and perspectives. It means putting oneself in the customer’s shoes and showing genuine care and understanding.
- Clarity: Effective communication is essential in customer service. Clear communication ensures that information, instructions, and solutions are easily understood by customers, minimizing misunderstandings and confusion.
- Knowledgeability: Good customer service representatives possess adequate knowledge about the products or services offered. They can answer questions accurately, provide helpful information, and guide customers effectively.
- Professionalism: Professionalism in customer service means maintaining a courteous and respectful demeanor at all times, even in challenging situations. It involves staying calm, patient, and focused on resolving issues professionally.
- Problem-solving skills: Customers often seek assistance to resolve issues or challenges. Good customer service involves proactive problem-solving, identifying root causes, and offering effective solutions to meet customer needs.
- Personalization: Treating customers as individuals and addressing their specific needs and preferences enhances the customer experience. Personalized service involves tailoring interactions and solutions to match the customer’s unique situation.
These qualities collectively contribute to building strong customer relationships, fostering customer loyalty, and ensuring overall satisfaction with the products or services provided. Companies that prioritize and excel in these areas often distinguish themselves in competitive markets by delivering exceptional customer service experiences.
FAQs (Frequently Asked Questions)
What are N4000-13 series materials PCBs?
N4000-13 series materials PCBs refer to printed circuit boards manufactured using specific laminate materials that meet stringent performance standards. These materials are chosen for their high dielectric constant (Dk) and low dissipation factor (Df), making them suitable for high-frequency applications where signal integrity is critical.
What are the key features of N4000-13 series materials?
Key features include excellent electrical properties at high frequencies, thermal stability, mechanical strength, and resistance to environmental factors such as moisture and chemicals. These properties ensure reliable performance in demanding electronic applications.
What industries typically use N4000-13 series materials PCBs?
These PCBs are commonly used in industries such as telecommunications, aerospace, defense, medical devices, and high-speed digital applications. They are suitable for applications requiring high-frequency signal transmission and reliable operation in harsh environments.
What are the benefits of using N4000-13 series materials PCBs?
Benefits include enhanced signal integrity, reduced signal loss, improved thermal management, and increased reliability compared to standard PCB materials. They support the design of high-performance electronic devices and systems.
What design considerations are important for N4000-13 series materials PCBs?
Design considerations include controlled impedance routing, thermal management strategies, proper via design (including microvias), and adherence to manufacturer’s guidelines for material handling and processing. These ensure optimal performance and reliability.
Can N4000-13 series materials PCBs be customized?
Yes, these PCBs can be customized to meet specific design requirements and application needs. Manufacturers offer flexibility in layer stack-up configurations, surface finishes, and other design parameters to tailor PCBs to customer specifications.
What quality standards do N4000-13 series materials PCBs adhere to?
Manufacturers adhere to industry standards such as IPC (Association Connecting Electronics Industries) standards for PCB design, manufacturing, and testing. They also undergo rigorous quality control processes to ensure consistency and reliability.
How do I choose a supplier for N4000-13 series materials PCBs?
When choosing a supplier, consider factors such as their experience in manufacturing high-frequency PCBs, their capability to meet specific design requirements, their quality certifications, production capacity, and customer service reputation.