Omega Materials PCB Manufacturer
Omega Materials PCB Manufacturer. We offer Omega Materials PCBs from 2 layer to 50 layers, Microtrace and minimum clearance.
Omega Materials PCBs represent the pinnacle of printed circuit board technology, integrating advanced materials and cutting-edge manufacturing techniques to deliver unmatched performance and reliability. Engineered with precision and innovation, Omega Materials PCBs leverage specialized substrates, conductive layers, and insulating materials to optimize electrical, thermal, and mechanical properties.
These PCBs excel in high-frequency applications, such as RF/microwave systems, where signal integrity is paramount. Their superior thermal management capabilities make them ideal for dissipating heat in high-power electronic devices, ensuring stable operation even in challenging environments.
Omega Materials PCBs offer exceptional durability and mechanical strength, providing longevity and reliability for mission-critical systems in aerospace, automotive, and medical industries. Customizable to specific requirements, Omega Materials PCBs empower engineers to push the boundaries of performance and innovation in their designs.
In summary, Omega Materials PCBs epitomize excellence in PCB technology, delivering unparalleled performance, reliability, and versatility for a wide range of demanding applications.
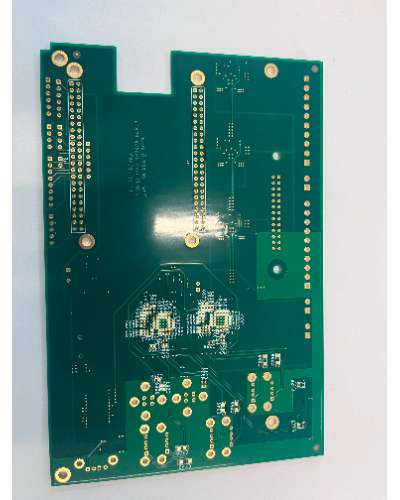
Omega Materials PCB
What is Omega Materials PCB?
Omega Materials PCB (Printed Circuit Board) is a type of circuit board renowned for its exceptional performance and durability. Unlike traditional PCBs, Omega Materials PCB utilizes advanced materials and manufacturing techniques to enhance its electrical and mechanical properties. The key feature of Omega Materials PCB is its incorporation of high-quality materials such as specialized substrates, conductive layers, and insulating materials.
One of the standout characteristics of Omega Materials PCB is its superior thermal management capability. This is achieved through the integration of materials with excellent thermal conductivity, allowing for efficient heat dissipation during operation. As a result, Omega Materials PCBs are often favored for applications where thermal management is critical, such as in high-power electronic devices or systems operating in harsh environments.
Furthermore, Omega Materials PCBs are known for their excellent electrical performance, offering low signal loss, reduced crosstalk, and improved signal integrity. This is attributed to the carefully selected materials and precise manufacturing processes employed in their production. As a result, Omega Materials PCBs are widely used in high-frequency and high-speed applications where signal integrity is paramount, such as in telecommunications, aerospace, and medical devices.
In addition to their exceptional thermal and electrical properties, Omega Materials PCBs also exhibit excellent mechanical strength and reliability. The use of robust materials and construction techniques ensures that these PCBs can withstand mechanical stresses, environmental factors, and prolonged use without compromising performance or integrity.
Overall, Omega Materials PCB represents a significant advancement in circuit board technology, offering unmatched performance, reliability, and versatility for a wide range of applications. Its innovative design and high-quality materials make it a preferred choice for demanding electronic systems where performance and durability are paramount.
What are Omega Materials PCB Design Guidelines?
Omega Materials PCB design guidelines are a set of recommendations and best practices to follow when designing a printed circuit board (PCB) using Omega Materials, which are advanced materials optimized for performance and reliability. These guidelines are intended to ensure that the PCB design maximizes the benefits of Omega Materials and meets the specific requirements of the intended application. While specific guidelines may vary depending on the exact composition of Omega Materials and the application requirements, some common design principles include:
- Material Selection: Choose Omega Materials that best suit the application’s requirements, considering factors such as thermal conductivity, dielectric constant, and mechanical properties.
- Layer Stackup Design: Optimize the layer stackup to achieve desired electrical performance, impedance control, and thermal management. Consider factors such as signal integrity, power distribution, and thermal dissipation requirements.
- Trace and Space Design: Maintain appropriate trace widths and spacing to meet impedance requirements, minimize signal loss, and prevent crosstalk. Pay attention to high-speed signal routing and differential pair routing for optimal signal integrity.
- Via Design: Use vias strategically to connect different layers of the PCB while minimizing signal distortion, impedance mismatches, and thermal issues. Consider via placement, size, and type (e.g., through-hole vias, blind vias, buried vias) based on the application’s requirements.
- Thermal Management: Incorporate thermal vias, thermal pads, and copper pours to efficiently dissipate heat from high-power components and sensitive areas of the PCB. Ensure adequate airflow and heat sinking capabilities in the overall system design.
- Component Placement: Optimize component placement to minimize signal path lengths, reduce parasitic effects, and enhance thermal performance. Follow good practices for separating analog and digital components, placing high-speed components strategically, and avoiding critical signal paths near noisy components.
- Grounding and Power Distribution: Implement a robust grounding scheme and power distribution network to minimize noise, ground loops, and voltage drops. Use multiple ground planes, split planes, and decoupling capacitors strategically to ensure stable power delivery and signal integrity.
- Design for Manufacturability (DFM): Consider manufacturability aspects such as minimum feature sizes, aspect ratios, and material compatibility during the design phase. Follow industry-standard design rules and guidelines to facilitate smooth PCB fabrication and assembly processes.
- Signal Integrity Analysis: Perform thorough signal integrity analysis, including simulation and modeling, to verify the electrical performance of the PCB design. Evaluate factors such as impedance matching, signal reflections, and electromagnetic interference (EMI) to ensure reliable operation.
- Reliability and Compliance: Design the PCB to meet reliability standards and regulatory requirements relevant to the application, such as IPC standards, RoHS compliance, and electromagnetic compatibility (EMC) regulations.
By adhering to these Omega Materials PCB design guidelines, designers can create high-performance, reliable, and cost-effective PCBs that leverage the unique properties of Omega Materials for a wide range of applications.
What is the Omega Materials PCB Fabrication Process?
The fabrication process for Omega Materials PCB involves several steps to transform raw materials into a functional printed circuit board optimized for performance and reliability. While specific details may vary depending on the exact composition of Omega Materials and the desired specifications of the PCB, the general fabrication process typically includes the following steps:
- Material Preparation: The fabrication process begins with the preparation of Omega Materials, including specialized substrates, conductive layers, and insulating materials. These materials are selected based on the application’s requirements for thermal conductivity, dielectric constant, mechanical strength, and other properties.
- Layer Preparation: Multiple layers of Omega Materials may be laminated together to form the core structure of the PCB. Each layer may consist of a substrate material, copper foil for conductive traces, and dielectric material for insulation between layers. The layers are cleaned, inspected, and prepared for subsequent processing.
- Copper Cladding: Copper foils are bonded to the surfaces of the substrate layers through a process known as copper cladding. The copper foils provide the conductive pathways for electrical signals on the PCB. The thickness and properties of the copper foils are carefully controlled to meet the design requirements for conductivity, impedance, and thermal performance.
- Circuit Patterning: The conductive traces and features of the PCB are defined through a process known as circuit patterning. This typically involves using photolithography or etching techniques to selectively remove copper from the surface of the substrate, leaving behind the desired circuit pattern.
- Insulation and Surface Treatment: Insulating layers may be applied between conductive layers to provide electrical isolation and mechanical support. Surface treatment processes such as solder mask application, surface finish plating, and legend printing are performed to protect the PCB and enhance its functionality.
- Drilling and Via Formation: Holes are drilled or punched through the PCB substrate to create vias, which provide electrical connections between different layers of the PCB. Advanced techniques such as laser drilling or mechanical drilling may be used to achieve precise via placement and dimensions.
- Plating and Plating Through Holes (PTH): The vias and through-holes are plated with conductive materials such as copper to establish electrical continuity between layers. This process, known as plating or plating through holes (PTH), ensures reliable electrical connections and enhances the mechanical strength of the vias.
- Final Inspection and Testing: The fabricated PCB undergoes rigorous inspection and testing to ensure quality and adherence to design specifications. Various tests may be performed, including electrical continuity testing, impedance measurement, solderability testing, and visual inspection.
- Surface Mount Technology (SMT): If surface-mount components are used, the PCB may undergo surface mount technology (SMT) assembly processes, where components are mounted directly onto the surface of the PCB and soldered in place using reflow soldering techniques.
- Final Finishing and Packaging: Once all fabrication and assembly processes are complete, the PCB undergoes final finishing steps such as edge trimming, cleaning, and surface coating to prepare it for installation and use in electronic systems. The finished PCBs are then packaged and shipped to customers for integration into their products.
Overall, the Omega Materials PCB fabrication process involves a series of precise and carefully controlled steps to create high-performance, reliable printed circuit boards tailored to the specific requirements of the application. Advanced materials and manufacturing techniques are employed to optimize electrical performance, thermal management, and mechanical reliability, making Omega Materials PCBs suitable for a wide range of demanding applications.
How do you manufacture an Omega Materials PCB?
Manufacturing an Omega Materials PCB involves a series of steps that combine advanced materials and precision manufacturing techniques. Here’s a generalized overview of the manufacturing process:
- Design Preparation: The process starts with the design of the PCB using specialized software. Designers specify the layout, dimensions, layer stackup, and other parameters based on the requirements of the application.
- Material Selection: Omega Materials are selected based on their properties such as thermal conductivity, dielectric constant, and mechanical strength. These materials may include specialized substrates, conductive layers (copper foils), and insulating materials (dielectrics).
- Preparation of Substrates: The chosen substrates are prepared by cleaning and inspecting them to ensure they are free from contaminants and defects. Surface treatments may be applied to enhance adhesion and compatibility with subsequent processes.
- Copper Cladding: Copper foils are bonded to the surfaces of the substrate layers through a process called copper cladding. This involves laminating or bonding the copper foils to the substrate surfaces using heat and pressure.
- Circuit Patterning: The desired circuit pattern is defined on the copper foils using photolithography or etching techniques. A photoresist layer is applied to the copper surface, exposed to UV light through a photomask, developed to remove unwanted resist, and then the exposed copper is etched away to form the circuit traces and features.
- Insulation and Surface Treatment: Insulating layers may be applied between conductive layers to provide electrical isolation and mechanical support. Surface treatment processes such as solder mask application, surface finish plating, and legend printing are performed to protect the PCB and enhance its functionality.
- Drilling and Via Formation: Holes are drilled or punched through the PCB substrate to create vias, which provide electrical connections between different layers of the PCB. Advanced techniques such as laser drilling or mechanical drilling may be used to achieve precise via placement and dimensions.
- Plating and PTH (Plating Through Holes): The vias and through-holes are plated with conductive materials such as copper to establish electrical continuity between layers. This process ensures reliable electrical connections and enhances the mechanical strength of the vias.
- Final Finishing and Testing: The fabricated PCB undergoes final finishing steps such as edge trimming, cleaning, and surface coating to prepare it for installation and use in electronic systems. The finished PCBs are then subjected to rigorous testing to ensure quality and adherence to design specifications.
- Assembly (Optional): Depending on the application, surface mount technology (SMT) assembly processes may be employed to mount components onto the PCB surface and solder them in place using reflow soldering techniques.
Throughout the manufacturing process, strict quality control measures are implemented to ensure that the Omega Materials PCBs meet the required specifications for performance, reliability, and durability. Advanced manufacturing equipment and techniques are utilized to achieve precise tolerances and high-quality finishes, making Omega Materials PCBs suitable for a wide range of demanding applications.
How much should an Omega Materials PCB cost?
The cost of an Omega Materials PCB can vary significantly depending on several factors such as the size, complexity, materials used, manufacturing processes involved, and the quantity ordered. Omega Materials PCBs are often considered high-performance and may incorporate advanced materials and manufacturing techniques, which can influence the overall cost. Additionally, factors such as customization, special requirements, and additional services (e.g., assembly, testing) can also impact the final price.
As a rough estimate, the cost of an Omega Materials PCB can range from a few dollars for simple, small-scale designs to several hundred or even thousands of dollars for complex, high-density PCBs with specialized materials and features. Mass production of Omega Materials PCBs typically reduces the unit cost due to economies of scale, whereas low-volume or prototype orders may incur higher costs per unit.
To obtain an accurate cost estimate for an Omega Materials PCB, it’s advisable to consult with PCB manufacturers or suppliers who specialize in Omega Materials and provide quotations based on your specific requirements, including design specifications, quantities, and any additional services needed. Comparing quotes from multiple suppliers can help you find the best balance between cost, quality, and lead time for your project.
What is Omega Materials PCB base material?
Omega Materials PCBs can be constructed using a variety of base materials depending on the specific requirements of the application and desired performance characteristics. These materials may include specialized substrates, laminates, and composite materials engineered to meet the demanding needs of high-performance PCBs.
Some common base materials used in Omega Materials PCBs include:
- High-Frequency Laminates: These laminates are designed to maintain stable electrical properties at high frequencies, making them suitable for applications such as telecommunications, RF/microwave systems, and high-speed digital circuits. Examples of high-frequency laminates include polytetrafluoroethylene (PTFE)-based materials like Rogers Corporation’s RO4000 series or Isola’s IS620.
- Thermal Management Substrates: Omega Materials PCBs often incorporate substrates with enhanced thermal conductivity to efficiently dissipate heat generated by high-power components. Materials like metal core PCBs (MCPCBs), aluminum-backed laminates, or thermally conductive dielectrics are commonly used for thermal management in Omega Materials PCBs.
- High-Temperature Substrates: Some applications require PCBs to withstand elevated temperatures without sacrificing performance or reliability. High-temperature substrates, such as polyimide (PI) or ceramic-filled materials, are used to ensure stability and durability in harsh operating environments.
- Flex and Rigid-Flex Materials: Omega Materials PCBs may also utilize flexible and rigid-flex substrates to accommodate complex form factors, bending, or dynamic movement in applications like wearable electronics, aerospace, and automotive electronics. These materials typically include polyimide or polyester-based substrates with copper conductors.
- Specialized Dielectric Materials: Omega Materials PCBs may incorporate specialized dielectric materials with tailored properties such as low-loss tangent, controlled impedance, or reduced signal distortion. Examples include low-loss dielectrics like polytetrafluoroethylene (PTFE) or ceramic-filled materials.
- Advanced Composite Materials: In some cases, Omega Materials PCBs may utilize advanced composite materials that offer a combination of properties such as high strength, lightweight, and excellent electrical performance. Carbon fiber composites or hybrid materials are examples of advanced substrates used in Omega Materials PCBs.
Overall, the choice of base material for an Omega Materials PCB depends on factors such as the application’s requirements for electrical performance, thermal management, mechanical stability, and environmental conditions. Designers and manufacturers select the most appropriate base material to optimize the PCB’s performance, reliability, and cost-effectiveness for the intended application.
Which company makes Omega Materials PCB?
Currently, there are many companies that manufacture Omega Materials PCBs, some of which include prominent names like Rogers Corporation, Isola Group, Taconic Advanced Dielectric Division, and others. These companies are dedicated to researching and producing various advanced PCB materials, including Omega Materials suitable for special applications such as high-frequency, high-temperature, and thermal management.
As for our company, we can also manufacture Omega Materials PCBs. Equipped with advanced manufacturing equipment, sophisticated techniques, and an experienced engineering team, we are capable of meeting customers’ demands for high-performance PCBs. Our manufacturing process includes:
- Material Selection and Procurement: We select and procure high-quality Omega Materials, choosing the most suitable substrate materials, conductive layers, and insulating materials based on customers’ requirements and application scenarios.
- Precision Machining and Production: We utilize advanced processing equipment and precise manufacturing techniques to carry out accurate machining and production of PCBs. This involves processes such as substrate lamination, circuit pattern definition, hole drilling, conductor layer formation, surface treatment, and more.
- Quality Control and Inspection: We strictly adhere to quality control standards to ensure that every production step meets design requirements and industry standards. Multiple inspections, including visual inspection, electrical testing, dimensional measurement, etc., are conducted to ensure the quality and performance of the PCBs.
- Customized Services and Technical Support: We provide customized services to tailor PCB designs and manufacturing processes according to customers’ specific requirements. Our engineering team offers professional technical support to help customers optimize designs, solve technical challenges, and ensure the final products meet expectations.
- Reliability Assurance and After-sales Service: We are committed to delivering reliable products and excellent after-sales service. Our PCBs undergo rigorous reliability testing and validation to ensure stable and reliable operation under various environments and working conditions. Additionally, we offer timely after-sales support to address any issues or difficulties encountered by customers during use.
As a professional PCB manufacturer, we can produce various types of Omega Materials PCBs, including high-frequency PCBs, high-temperature PCBs, thermal management PCBs, etc., to meet the diverse needs of different application fields. Our goal is to provide customers with high-quality, reliable products and services, collaborate for mutual success, and grow together.
What are the 7 qualities of good customer service?
Good customer service is characterized by several key qualities that contribute to a positive and satisfying experience for customers. Here are seven qualities of good customer service:
- Responsiveness: Good customer service involves being responsive to customers’ needs, inquiries, and concerns in a timely manner. This includes promptly answering phone calls, emails, and messages, as well as addressing customer issues and resolving problems quickly and efficiently.
- Empathy: Empathy is the ability to understand and relate to customers’ feelings, concerns, and perspectives. Good customer service representatives demonstrate empathy by actively listening to customers, acknowledging their emotions, and showing genuine concern for their well-being.
- Clarity:Clear communication is essential for good customer service. This involves providing accurate and easily understandable information to customers, explaining products or services clearly, and avoiding jargon or technical language that may confuse or frustrate customers.
- Professionalism:Good customer service requires professionalism in all interactions with customers. This includes being courteous, respectful, and polite at all times, maintaining a positive attitude, and representing the company in a professional manner.
- Problem-solving skills: Effective problem-solving skills are essential for resolving customer issues and complaints. Good customer service representatives are proactive in identifying and addressing customer problems, finding creative solutions, and taking ownership of issues until they are fully resolved.
- Consistency: Consistency is important for building trust and confidence in the company’s products or services. Good customer service should be consistent across all channels and interactions, ensuring that customers receive the same level of service regardless of how they contact the company.
- Follow-up: Following up with customers after their initial interaction or purchase demonstrates a commitment to their satisfaction and loyalty. Good customer service involves following up to ensure that customers’ needs have been met, gathering feedback on their experience, and addressing any remaining concerns or questions they may have.
By embodying these qualities, companies can provide exceptional customer service that not only meets but exceeds customers’ expectations, fostering long-term relationships and loyalty.
FAQs (Frequently Asked Questions)
What are Omega Materials PCBs?
Omega Materials PCBs are printed circuit boards that utilize advanced materials optimized for performance and reliability. These materials, known as Omega Materials, offer enhanced electrical, thermal, and mechanical properties compared to traditional PCB materials.
What are the benefits of using Omega Materials PCBs?
Omega Materials PCBs offer several benefits, including improved thermal management, enhanced electrical performance, greater mechanical strength, and increased reliability. These properties make Omega Materials PCBs well-suited for demanding applications in industries such as telecommunications, aerospace, and medical devices.
What types of Omega Materials are commonly used in PCBs?
Common Omega Materials used in PCBs include high-frequency laminates, thermal management substrates, high-temperature substrates, specialized dielectric materials, and advanced composite materials. These materials are selected based on the specific requirements of the application.
What are some typical applications of Omega Materials PCBs?
Omega Materials PCBs are used in a wide range of applications where high performance, reliability, and durability are essential. Some typical applications include RF/microwave systems, high-speed digital circuits, power electronics, automotive electronics, and aerospace systems.
How do Omega Materials PCBs differ from traditional PCBs?
Omega Materials PCBs differ from traditional PCBs in their use of advanced materials and manufacturing techniques to achieve superior performance and reliability. Omega Materials offer properties such as high thermal conductivity, low dielectric loss, and excellent mechanical strength that are not typically found in traditional PCB materials.
Can Omega Materials PCBs be customized for specific applications?
Yes, Omega Materials PCBs can be customized to meet the specific requirements of different applications. This includes selecting the appropriate Omega Materials, designing the PCB layout and stackup, and optimizing the manufacturing process to achieve the desired performance and functionality.
Where can I find suppliers or manufacturers of Omega Materials PCBs?
Suppliers and manufacturers of Omega Materials PCBs can be found through online directories, industry trade shows, and networking events. It’s important to research and evaluate potential suppliers based on factors such as their experience, capabilities, quality standards, and customer reviews.
What factors should I consider when selecting Omega Materials for my PCB?
When selecting Omega Materials for your PCB, consider factors such as thermal conductivity, dielectric constant, mechanical strength, cost, availability, and compatibility with other materials and processes. It’s also important to consult with material suppliers and PCB manufacturers to ensure the chosen materials meet your specific requirements.dle