Organic FC BGA substrate Manufacturer and package substrate production. We use advanced Msap and Sap technology, High multilayer interconnection substrates from 2 to 20 layers,
Diving into the realm of electronic packaging, let’s unravel the enigma known as “Organic Substrate FC BGA.”
To begin, “Organic Substrate” is the unsung hero, a material woven from carbon-based composites. Its role? To be the sturdy foundation, weaving connections and offering support to the diverse elements on integrated circuit chips. Think of it as the silent conductor orchestrating the symphony of support, insulation, and connectivity in electronic devices.
Now, onto the stage comes “FC BGA,” the rebel of packaging techniques, short for “Flip-Chip Ball Grid Array.” Picture this – the chip takes a bold flip, landing upside-down on the substrate. How do they connect? Through dainty, ball-shaped solder points. This unconventional ballet not only amps up density and performance but also flaunts an artistry in managing heat – a true maverick move.
In the saga of “Organic Substrate FC BGA,” envision a tango between the Flip-Chip Ball Grid Array and the organic substrate. It’s a dynamic duo, blending the organic substrate’s perks like being lightweight, budget-friendly, and electrically savvy, with the FC BGA’s allure of high-performance and density.
This tag team is gearing up to revolutionize electronic manufacturing and packaging. Picture chips, processors, and cutting-edge electronic devices reaping the benefits of this fusion. By elevating performance, reliability, and heat dissipation, this packaging technique seamlessly aligns with the ever-shifting tech landscape.
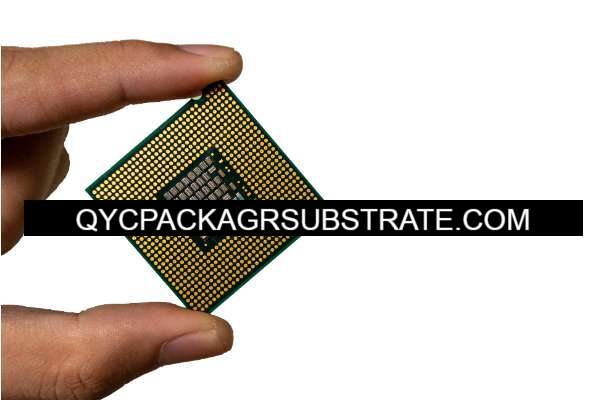
What are the Functions of Organic Substrate FC BGA?
Step into the electronic packaging arena, where the “Organic Substrate FC BGA” steals the spotlight, fusing the organic substrate’s prowess with the avant-garde features of FC BGA. Let’s unravel the tapestry of its functions:
Structural Nexus: The organic substrate plays the role of an unyielding scaffold, cradling IC chips with finesse. It intricately weaves electrical connections among chip components, creating a harmonious symphony of support.
Electrical Guardian: A dependable insulator, the organic substrate shields against unwarranted electrical crossfires. This guardianship ensures the purity of signals, staving off short circuits and ensuring a smooth operational cadence.
Thermal Maestro: FC BGA’s daring flip-chip dance, coupled with its balletic solder points, conducts a symphony of thermal control. Heat dissipation becomes an art, warding off overheating specters and ensuring the device dances to its optimum rhythm.
Densification Dynamo: Renowned for high-density packaging, FC BGA orchestrates a compact congregation of components on the substrate. The result? Devices that defy spatial constraints, a vital attribute in size-conscious applications.
Signal Virtuosity: The marriage of organic substrate nuances with FC BGA’s connectivity finesse amplifies the overall signal virtuosity. This partnership elevates the electrical prowess of the encapsulated IC, ensuring a reliable transmission of signals.
Economical Alchemy: Harnessing the economic magic of organic substrates, Organic Substrate FC BGA strikes a chord between performance and cost-effectiveness. This financial pragmatism makes it a magnetic choice across a spectrum of electronic applications.
Reliability Luminary: Crafted for the long haul, the design and structure of Organic Substrate FC BGA exude reliability. Robust connections and an adept thermal embrace collectively fortify the device, ensuring steadfast and unwavering operation.
In essence, the Organic Substrate FC BGA is not merely a packaging solution; it’s a dynamic amalgamation of support ballet, electrical guardianship, thermal symphony, densification wizardry, signal virtuosity, economical alchemy, and reliability luminary. This versatile blend caters to electronic applications with finesse, from microprocessors to the zenith of integrated circuits.
What are the Different Types of Organic Substrate FC BGA?
The diverse landscape of “Organic Substrate FC BGA” unfolds into various specialized types, each tailored to meet specific technological demands. Let’s explore these variations:
Standard Organic Substrate FC BGA:
The fundamental variant, amalgamating organic substrates with the Flip-Chip Ball Grid Array setup. Suited for general applications where conventional packaging suffices.
High-Performance Organic Substrate FC BGA:
Engineered for applications craving heightened performance, this type optimizes materials and configurations to elevate speed, signal integrity, and overall functionality.
Low-Cost Organic Substrate FC BGA:
Catering to cost-conscious applications, this variant maintains essential functionality while prioritizing affordability through judicious material choices and streamlined manufacturing processes.
High-Density Organic Substrate FC BGA:
Tailored to host a plethora of interconnections and components in a confined space. Ideal for applications where miniaturization takes precedence.
Power-Delivery Optimized Organic Substrate FC BGA:
Focused on adeptly managing power delivery within the package, crucial for power-intensive applications like high-performance processors or graphics chips.
Fine-Pitch Organic Substrate FC BGA:
Marked by smaller pitch sizes between solder balls, facilitating a denser interconnect array. Beneficial for applications demanding a more intricate network of connections.
Multi-Chip Module (MCM) Organic Substrate FC BGA:
Tailored to accommodate multiple chips within a single package, fostering integration and minimizing the need for additional components. Common in complex electronic systems.
3D-Stacked Organic Substrate FC BGA:
Harnessing three-dimensional stacking, this type enables the vertical layering of multiple ICs, enhancing performance and reducing physical footprint.
System-in-Package (SiP) Organic Substrate FC BGA:
Transcending traditional IC packaging, SiP integrates diverse functions (memory, processing, communication) into a single package. Promotes space efficiency and simplifies system design.
Custom or Application-Specific Variants:
Manufacturers innovate to meet specific application needs, crafting specialized versions tailored to particular industries or use cases.
As technology evolves, so does the array of Organic Substrate FC BGA types. Each variation addresses unique challenges and requirements, contributing to the dynamic landscape of electronic packaging.
What is the Relationship Between Organic Substrate FC BGA and IC Packaging?
The intertwining relationship between “Organic Substrate FC BGA” and IC (Integrated Circuit) packaging is akin to a dance where each partner plays a crucial role in the harmony of semiconductor device assembly and performance.
Cornerstone of IC Packaging:
At the heart of IC packaging lies the organic substrate, a foundational element that provides a stable canvas for the intricate assembly of integrated circuits. It sets the stage for the performance of semiconductor devices.
Physical Support and Connection Choreography:
Picture the organic substrate as a supportive partner, not only bearing the weight of IC chips but also choreographing the dance of connections between various elements on the chip. This collaborative effort ensures seamless connectivity.
Electrical Insulation Ballet:
The organic substrate takes center stage in an electrical insulation ballet, shielding against the risk of short circuits. This performance guarantees the flawless functioning of integrated circuits, preserving the purity of signals and preventing interference.
Flip-Chip Configuration Drama:
The drama unfolds with the flip-chip configuration, a daring move where the IC chip is inverted and mounted on the organic substrate. This unconventional stance facilitates direct and efficient connections, enhancing the overall electrical performance.
Ball Grid Array Interconnection Waltz:
The ball grid array enters the scene, a well-coordinated waltz where solder balls on the underside of the IC chip form a grid, elegantly connecting with corresponding pads on the organic substrate. This intricate interplay ensures a dense network of connections and smooth signal transmission.
Thermal Pas de Deux:
As the performance heats up, the organic substrate takes on a thermal pas de deux, gracefully dissipating the heat generated by the IC chip. This dance prevents overheating, ensuring a reliable and enduring performance of the semiconductor device.
Package Miniaturization Symphony:
The culmination of this performance leads to a symphony of package miniaturization. The combination of organic substrate and FC BGA allows for high-density packaging, bringing a crescendo of compact and lightweight semiconductor devices to the stage.
Varied IC Packaging Ensemble:
Beyond the spotlight on Organic Substrate FC BGA, the relationship extends to a diverse ensemble of IC packaging types. From chip-on-board to quad flat packages, each has its unique characteristics, contributing to the richness and diversity of the semiconductor performance.
In essence, the relationship between Organic Substrate FC BGA and IC packaging is an orchestrated performance, where the organic substrate and its flip-chip counterpart create a dynamic synergy. Together, they define the rhythm and melody of semiconductor devices, adapting to the ever-evolving demands of electronic applications.
How Does Organic Substrate FC BGA Differ from Traditional PCBs?
In the realm of electronic components, “Organic Substrate FC BGA” and traditional PCBs showcase distinctive choreographies, each contributing its own flair to the dance of design and functionality.
Mounting Elegance:
Organic Substrate FC BGA: Imagine a dynamic flip-chip routine where IC chips gracefully invert and join an organic substrate, creating a visually captivating array with solder ball precision.
Traditional PCBs: In the traditional dance, ICs take center stage through surface-mount or through-hole techniques, each step meticulously planned on the board’s surface or through perforations.
Interconnection Rhythm:
Organic Substrate FC BGA: FC BGA leads with a rhythmic ball grid array, where solder balls beneath the chip dance in harmony with corresponding pads on the organic substrate. This synchronized interplay results in a dense network of connections.
Traditional PCBs: Traditional PCBs contribute their own beat, relying on varied methods like traces and vias to connect the electronic ensemble, although achieving the same density requires a larger dancefloor.
Density Waltz and Miniaturization Flourish:
Organic Substrate FC BGA: FC BGA takes the lead in a high-density waltz, elegantly compacting components to create a visually striking performance—a necessity in the grand ballroom of modern electronic devices.
Traditional PCBs: While traditional PCBs have their own dance, achieving the same level of component density might necessitate a more expansive floor to accommodate the intricate steps.
Thermal Ballet:
Organic Substrate FC BGA: The flip-chip and ball grid array collaboration in FC BGA creates a thermal ballet, gracefully dissipating heat to prevent the dance floor from overheating.
Traditional PCBs: In the traditional performance, thermal management may call upon additional partners like heat sinks or fans to maintain a cool and harmonious rhythm.
Application Symphony:
Organic Substrate FC BGA: FC BGA takes center stage in applications where stellar performance, compact design, and graceful thermal management take the lead—an orchestra often seen in advanced microprocessors and GPUs.
Traditional PCBs: Traditional PCBs, versatile in their own right, compose a symphony across various electronic devices, where the spotlight is shared among performance, cost-effectiveness, and adaptability.
Complexity and Cost Opera:
Organic Substrate FC BGA: The production and assembly of FC BGA unfold as a complex opera, potentially demanding a higher production cost for this intricate performance.
Traditional PCBs: Traditional PCBs, with their cost-effectiveness, play a more budget-friendly tune for applications where the dance is less intricate.
In essence, the duet between Organic Substrate FC BGA and traditional PCBs unfolds as a captivating performance, each contributing its unique moves to the electronic symphony. FC BGA takes the lead in high-performance, while traditional PCBs offer versatility across a broader spectrum of electronic applications.
What are the Main Structures and Production Technologies of Organic Substrate FC BGA?
The construction and manufacturing processes of “Organic Substrate FC BGA” (Flip-Chip Ball Grid Array) form a sophisticated tapestry, combining specific structures and production technologies to achieve optimal performance and reliability. Let’s delve into the intricacies of these elements:
Foundation of Organic Substrate:
Base Material: The organic substrate relies on materials like FR-4 or advanced substrates, providing both electrical insulation and structural support. These materials create a robust foundation for the integrated circuits (ICs).
Layered Complexity: Multiple layers within the organic substrate are strategically crafted to serve diverse functions. Signal, power, and ground layers work harmoniously to facilitate efficient electrical connections.
Innovative Flip-Chip Configuration:
Upside-Down Mounting: The distinctive flip-chip configuration places IC chips in an inverted position on the organic substrate. This unconventional arrangement fosters direct connections, optimizing signal pathways and minimizing inductance.
Ball Grid Array (BGA) Interplay:
Solder Ball Ensemble: The BGA feature shines through with solder balls intricately arranged beneath the IC chip, forming a precise grid. These solder balls act as the primary conduits for electrical connections between the chip and the organic substrate.
Microvias and Through Vias Ballet:
Microvias Precision: Small-diameter microvias weave intricate connections between different substrate layers, enhancing connection density and enabling complex signal routing.
Through Vias Grandeur: Larger through vias gracefully facilitate vertical connections between layers, allowing signals, power, and ground to traverse the substrate.
Copper Trace Choreography:
Conductive Paths: Copper traces on the substrate’s surface choreograph the journey of electrical signals. These paths connect diverse components, ensuring the seamless flow of signals across the ICs and other substrate elements.
Pads as Staging Grounds: Pads serve as stable platforms for the solder balls, creating a reliable interface between the organic substrate and the IC chip.
Dielectric Harmony:
Insulating Layers Performance: Dielectric materials create protective layers, preventing electrical interference and short circuits. This ensures the purity of signals and the overall robustness of the FC BGA.
Build-Up Technology Crescendo:
Layer Stacking Brilliance: Build-up technology allows for successive layer stacking, elevating connection density and enabling the formation of intricate circuits within confined spaces.
Surface Finish Grand Finale:
Surface Elegance: Surface finishes like solder mask safeguard exposed areas, while treatments like ENIG or HASL enhance solderability, contributing to the overall reliability of the FC BGA.
Precision Manufacturing Choreography:
Die Attach and Wire Bonding Performance: Manufacturing processes involve die attach, securely affixing IC chips to the substrate. Wire bonding establishes essential electrical connections.
Solder Ball Ballet: Solder balls, critical for connectivity, are delicately attached beneath the IC chip through reflow soldering, ensuring secure and reliable electrical links.
Quality Control Symphony:
X-ray Inspection Artistry: Given the complexity, X-ray inspection unveils the quality of solder joints, ensuring precision and reliability.
AOI Precision Gaze: Automated Optical Inspection acts as a discerning eye, identifying defects and ensuring the overall excellence of the manufacturing process.
In essence, the construction and production technologies of Organic Substrate FC BGA are a finely orchestrated composition, blending materials, configurations, and manufacturing finesse to create a high-density, high-performance packaging solution.
Frequently Asked Questions (FAQs)
What defines the essence of Organic Substrate FC BGA?
Organic Substrate FC BGA, or the Flip-Chip Ball Grid Array, is a captivating packaging technology for integrated circuits. It involves the daring act of mounting IC chips upside down on an organic substrate, where solder balls choreograph an intricate grid for seamless electrical connections.
What role does the organic substrate play in the FC BGA spectacle?
The organic substrate takes on a multi-faceted role—it acts as a sturdy stage for IC chip performances, dons the cloak of electrical insulation to thwart short circuits, and orchestrates the interconnection ballet through its copper traces and vias.
Who are the maestros behind the production of Organic Substrate FC BGA substrates?
The creators of the Organic Substrate FC BGA symphony include renowned manufacturers like Amkor Technology, ASE Group, and Unimicron, among other virtuosos in the industry.
What are the materials that compose the spellbinding Organic Substrate FC BGA substrates?
The magical materials often include the likes of FR-4 or advanced high-performance substrates. These materials, with their enchanting properties, strike a harmonious balance in the substrate’s composition.
How is the enchanting production of Organic Substrate FC BGA substrates orchestrated?
The production unfolds as a captivating saga involving acts like die attach, wire bonding, solder ball attachment, and the creation of microvias and through vias. Advanced manufacturing techniques, akin to mystical arts, contribute to the intricate dance of production.
What are the enchanting benefits bestowed by the magic of Organic Substrate FC BGA technology?
Organic Substrate FC BGA casts spells of high-density packaging, wizardry in thermal management, and a mystical enhancement of electrical performance. It’s a potion crafted for applications desiring compact dimensions and heightened connectivity.
Can the enchanting Organic Substrate FC BGA substrates be tailored for specific quests?
Indeed, manufacturers wield the power of customization, allowing substrates to don different cloaks tailored to the specific needs of diverse quests. This may include variations in substrate materials, layers, and an overall design tailored to unique adventures.
How does one unveil the enchanting quality of Organic Substrate FC BGA substrates?
The journey involves magical quality control rituals, such as peering through the lens of X-ray inspection and the discerning gaze of automated optical inspection (AOI). These incantations ensure the sanctity of solder joints and the overall magical quality of the substrate.
In what mystical realms does Organic Substrate FC BGA technology find its purpose?
The magical prowess of Organic Substrate FC BGA is summoned in high-performance realms, enchanting microprocessors, casting spells on graphics processing units (GPUs), and gracing other magical integrated circuits that demand miniaturization and spellbinding thermal management.
How does one choose a trustworthy wizard among Organic Substrate FC BGA substrate manufacturers?
Seek the wise ones with a storied reputation, a legacy of experiences in the enchanted industry, a commitment to quality standards, and the ability to craft customized spells. Reviews, certifications, and industry alliances are like ancient runes, guiding you to the most reliable enchanters.
Conclusion
In conclusion, the realm of “Organic Substrate FC BGA” unfolds as a captivating narrative, where technology and innovation converge to create a symphony of high-performance packaging for integrated circuits. The flip-chip ballet, intricate ball grid array, and the strategic dance of materials on the organic substrate showcase a harmonious collaboration in the quest for miniaturization and enhanced connectivity.
Manufacturers, akin to skilled choreographers, craft these substrates with precision and finesse, utilizing advanced materials and production technologies. The organic substrate serves as a foundational stage, supporting the graceful performance of IC chips while ensuring electrical insulation and thermal equilibrium.
The enchanting benefits of Organic Substrate FC BGA, from high-density packaging to efficient thermal management, position it as a leading protagonist in the world of semiconductor devices. It takes center stage in applications demanding a delicate balance between performance and compact design, captivating audiences in the realms of microprocessors and GPUs.
As users embark on their quest for these magical substrates, the choice of a manufacturer becomes a crucial decision. Seekers are encouraged to navigate the enchanted landscape, considering reputation, experience, and the ability to weave customized solutions as guiding stars.
In essence, the tale of Organic Substrate FC BGA is one of innovation, precision, and the continual quest for technological excellence. As the narrative evolves, the dance between substrates and semiconductor devices continues, promising a future where advancements in packaging technology contribute to the unfolding saga of electronic progress.