Organic Packaging Chip Substrates Manufacturer
What are Organic Packaging Chip Substrates?
Organic Packaging Chip Substrates Manufacturer. the Package Substrate will be made with Showa Denko and Ajinomoto High speed materials.or other types high speed materials and high frequency materials.
Organic Packaging Chip Substrates, also known as organic substrates or organic laminate substrates, are a type of material used in semiconductor packaging technology. They serve as a platform upon which semiconductor chips are mounted and interconnected to form electronic devices such as integrated circuits (ICs) and microchips.
Here’s a breakdown of the key features and components of organic packaging chip substrates:
Material Composition: Organic substrates are typically composed of organic materials such as epoxy resins, fiberglass (or other reinforcing materials), and various additives. These materials are chosen for their electrical insulation properties, mechanical strength, and compatibility with semiconductor manufacturing processes.
Layered Structure: Organic substrates are often composed of multiple layers of materials laminated together. These layers may include conductive traces (usually made of copper), insulating layers, and solder mask layers. The conductive traces form the electrical connections between the semiconductor chip and the external circuitry.
Interconnection Technology: Organic substrates utilize various interconnection technologies to connect the semiconductor chip to the substrate and to other components on the printed circuit board (PCB). Common interconnection methods include wire bonding, flip-chip bonding, and through-silicon vias (TSVs).
Advantages: Organic packaging chip substrates offer several advantages over alternative packaging technologies such as ceramic substrates. These advantages include lower cost, lighter weight, and better thermal performance. Organic substrates are also compatible with high-density interconnection schemes, allowing for the integration of more complex semiconductor devices.
Applications: Organic packaging chip substrates are widely used in various electronic devices, including smartphones, tablets, laptops, and other consumer electronics products. They are also used in automotive electronics, industrial equipment, and telecommunications infrastructure.
Overall, organic packaging chip substrates play a crucial role in semiconductor packaging technology, enabling the assembly and interconnection of semiconductor chips into functional electronic devices.
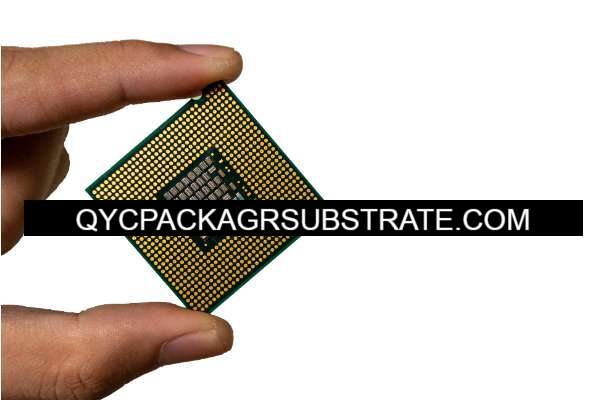
Organic Packaging Chip Substrates Manufacturer
What are the functions of Organic Packaging Chip Substrates?
Organic Packaging Chip Substrates serve several important functions in semiconductor packaging technology. These functions include:
Mounting Surface for Semiconductor Chips: The primary function of organic substrates is to provide a stable mounting surface for semiconductor chips. Chips are attached to the substrate using various bonding techniques such as wire bonding, flip-chip bonding, or die attach methods.
Electrical Interconnection: Organic substrates facilitate the electrical interconnection between the semiconductor chip and the rest of the electronic system. They contain conductive traces (usually made of copper) that connect the bond pads on the semiconductor chip to the external leads or solder balls, enabling the flow of electrical signals.
Signal Routing: Organic substrates route signals between the semiconductor chip and other components on the printed circuit board (PCB) or within the electronic system. They provide a pathway for signals to travel from the input/output (I/O) pads of the chip to other parts of the system, enabling communication between different components.
Power Distribution: Organic substrates distribute power to the semiconductor chip and other components in the electronic system. They include power distribution planes and traces that deliver power from the external power source to the chip and other critical components, ensuring stable operation.
Thermal Management: Organic substrates play a role in dissipating heat generated by the semiconductor chip during operation. They may include thermal vias or other thermal management features that help conduct heat away from the chip and distribute it across the substrate, improving overall thermal performance.
Mechanical Support: Organic substrates provide mechanical support and protection for the semiconductor chip. They help to protect the chip from mechanical stresses, such as bending or vibration, which could otherwise damage the chip or disrupt its operation.
Overall, organic packaging chip substrates are essential components in semiconductor packaging technology, enabling the assembly, interconnection, and reliable operation of semiconductor chips in a wide range of electronic devices.
What are the different types of Organic Packaging Chip Substrates?
There are several different types of Organic Packaging Chip Substrates, each with its own characteristics and advantages. Some of the most common types include:
Printed Circuit Boards (PCBs): PCBs are the most widely used type of organic substrate. They are composed of layers of fiberglass or other reinforcing materials laminated with epoxy resin. PCBs can be single-sided, double-sided, or multi-layered, depending on the complexity of the electronic device. They are versatile and cost-effective, making them suitable for a wide range of applications.
Chip-on-Board (COB) Substrates: COB substrates involve mounting semiconductor chips directly onto the substrate surface without the use of packaged components. This approach reduces package size and cost, making it suitable for high-volume, cost-sensitive applications such as consumer electronics.
Flexible Substrates: Flexible substrates are composed of flexible materials such as polyimide or polyester. They are used in applications where the substrate needs to conform to a curved or irregular surface, such as in wearable devices, flexible displays, and automotive electronics.
Build-up Substrates: Build-up substrates, also known as build-up PCBs, feature multiple layers of insulating and conductive materials stacked on top of each other. This design allows for higher density interconnects and smaller package sizes, making them suitable for high-performance and miniaturized electronic devices.
Embedded Substrates: Embedded substrates involve embedding semiconductor chips directly into the substrate material, rather than mounting them on the surface. This approach reduces package size and improves thermal performance by enabling more efficient heat dissipation.
Copper-Clad Laminates: Copper-clad laminates consist of a layer of copper bonded to an organic substrate material such as fiberglass or epoxy resin. They are commonly used in high-frequency and high-speed applications due to their excellent electrical properties and signal integrity.
Ceramic Substitutes: While not strictly organic, some substrates use ceramic-filled organic materials to combine the advantages of organic and ceramic substrates. These substrates offer improved thermal performance and reliability compared to traditional organic substrates.
These are just a few examples of the types of Organic Packaging Chip Substrates available in the market. The choice of substrate type depends on factors such as the application requirements, performance specifications, cost considerations, and manufacturing processes.
What is the relationship between Organic Packaging Chip Substrates and IC packaging?
Organic Packaging Chip Substrates and IC (Integrated Circuit) packaging are closely related components in the semiconductor industry, often working together to form a complete semiconductor package. Here’s how they are interconnected:
Organic Packaging Chip Substrates as a Component of IC Packaging: Organic Packaging Chip Substrates serve as a critical component within IC packaging. They provide the physical structure onto which the semiconductor chip is mounted, and they facilitate the electrical interconnection between the chip and the external circuitry. In many IC packaging designs, the substrate is an integral part of the package assembly.
IC Packaging Encapsulating the Semiconductor Chip and Substrate: IC packaging encapsulates the semiconductor chip and the organic substrate within a protective enclosure. This enclosure shields the chip and substrate from environmental factors such as moisture, dust, and mechanical stresses. Additionally, IC packaging often includes additional features such as leads, solder balls, or pins for external connections.
Variety of Packaging Technologies Utilizing Organic Substrates: Various IC packaging technologies utilize organic substrates, including leaded packages (such as Dual In-Line Packages – DIPs), surface mount packages (such as Quad Flat Packages – QFPs), ball grid array (BGA) packages, and chip-scale packages (such as Chip-Scale Packages – CSPs). Each of these packaging technologies may employ different types of organic substrates, depending on factors such as cost, performance requirements, and manufacturing processes.
Role in Performance and Reliability: The choice of organic substrate material and packaging technology can significantly impact the performance and reliability of the integrated circuit. Factors such as electrical properties, thermal conductivity, mechanical strength, and dimensional stability of the substrate influence the overall performance and reliability of the packaged IC.
Advancements in Packaging Technology Affect Substrate Design: Advancements in IC packaging technology often drive innovations in organic substrate design. For example, as demand grows for smaller, faster, and more power-efficient electronic devices, there is a need for thinner, denser, and more thermally efficient substrates to accommodate these requirements.
Overall, Organic Packaging Chip Substrates and IC packaging are interrelated components in the semiconductor industry, working together to encapsulate and interconnect semiconductor chips, ensuring their functionality, reliability, and performance in electronic devices.
How do Organic Packaging Chip Substrates differ from PCBs?
Organic Packaging Chip Substrates and Printed Circuit Boards (PCBs) are related components in the realm of electronic packaging, but they serve different purposes and have distinct characteristics. Here are some key differences between the two:
Functionality: Organic Packaging Chip Substrates primarily serve as a platform for mounting and interconnecting semiconductor chips within an integrated circuit (IC) package. Their primary function is to provide electrical connections between the chip and the external circuitry while offering mechanical support and thermal management. PCBs, on the other hand, are used to interconnect various electronic components within a system, including ICs, resistors, capacitors, and other active and passive devices. PCBs provide the electrical pathways for signals to travel between these components, forming the backbone of the electronic system.
Design Complexity: Organic Packaging Chip Substrates are typically designed to meet the specific requirements of a particular semiconductor package, such as die size, pin count, and thermal performance. They may feature multiple layers of conductive traces, insulating materials, and thermal vias, optimized for high-density interconnects and efficient heat dissipation. PCBs, on the other hand, can vary significantly in complexity depending on the application. They may range from simple single-sided or double-sided boards to complex multi-layered designs with high-speed signal routing, impedance control, and mixed-signal capabilities.
Manufacturing Process: The manufacturing process for Organic Packaging Chip Substrates is specialized and often tailored to the requirements of semiconductor packaging. It involves techniques such as laser drilling, electroplating, and dielectric lamination to create the necessary features and structures for mounting and interconnecting semiconductor chips. PCB manufacturing, on the other hand, follows a standardized process that includes steps such as board fabrication (etching, drilling, and plating), solder mask application, and component assembly (soldering).
Cost and Volume: Organic Packaging Chip Substrates are typically produced in lower volumes and are more specialized, which can result in higher manufacturing costs compared to standard PCBs. PCBs are produced in larger volumes and are used across a wide range of industries and applications, leading to economies of scale and lower costs per unit.
Application: Organic Packaging Chip Substrates are primarily used in semiconductor packaging applications, including ICs, microprocessors, memory modules, and other electronic components. PCBs, on the other hand, are used in a wide range of electronic devices and systems, including consumer electronics, telecommunications equipment, automotive electronics, medical devices, and industrial machinery.
In summary, while Organic Packaging Chip Substrates and PCBs both play crucial roles in electronic packaging, they differ in terms of functionality, design complexity, manufacturing process, cost, and application. Organic Packaging Chip Substrates are specialized components designed specifically for semiconductor packaging, while PCBs are more versatile and used across a broader range of electronic systems and devices.
What are the structure and production technology of Organic Packaging Chip Substrates?
The structure and production technology of Organic Packaging Chip Substrates can vary depending on factors such as the specific application, performance requirements, and manufacturing capabilities of the semiconductor packaging industry. However, here’s a general overview of the structure and production technology of organic substrates:
Structure:
Base Material: Organic substrates are typically composed of a base material, which is often a thermosetting polymer such as epoxy resin. This base material provides the structural support for the substrate and serves as the foundation for subsequent layers.
Conductive Traces: Multiple layers of conductive traces, usually made of copper, are patterned onto the substrate to create electrical pathways for interconnecting semiconductor chips and external circuitry. These traces are formed using processes such as lithography, etching, and plating.
Dielectric Layers: Insulating dielectric layers are interspersed between the conductive traces to prevent electrical short circuits and provide isolation between different circuit elements. These dielectric layers are typically made of materials such as epoxy resin or polyimide and are applied using techniques such as lamination or deposition.
Solder Mask: A solder mask layer is applied over the conductive traces to protect them from environmental factors such as moisture, dust, and mechanical damage. The solder mask also helps to define the locations for soldering components onto the substrate and provides insulation between adjacent traces.
Surface Finish: The substrate surface may undergo surface finishing processes to improve solderability and corrosion resistance. Common surface finishes include hot air solder leveling (HASL), electroless nickel immersion gold (ENIG), and organic surface protection (OSP).
Production Technology:
Substrate Fabrication: The production process typically begins with the fabrication of the substrate base material. This involves mixing and curing thermosetting polymers to form sheets or panels of the desired thickness and dimensions.
Lamination: Multiple layers of base material, conductive traces, and dielectric materials are laminated together to form the substrate stack. Pressure and heat are applied during lamination to ensure proper adhesion and consolidation of the layers.
Patterning and Etching: Photolithography techniques are used to pattern the conductive traces onto the substrate surface. After patterning, the excess copper is etched away using chemical etchants, leaving behind the desired trace patterns.
Via Formation: Holes are drilled or laser-ablated through the substrate layers to create vias, which are used to establish electrical connections between different layers of the substrate. These vias are typically filled with conductive materials such as copper or plated with metals such as nickel and gold.
Surface Finishing: Once the substrate fabrication is complete, surface finishing processes are applied to the substrate surface to improve solderability and protect against corrosion.
Testing and Inspection: The finished substrates undergo testing and inspection to ensure they meet the required electrical, mechanical, and dimensional specifications. This may involve electrical continuity testing, visual inspection, and dimensional measurement techniques.
Overall, the production technology of Organic Packaging Chip Substrates involves a combination of materials processing, patterning, lamination, and finishing techniques to create high-performance substrates suitable for semiconductor packaging applications.
Frequently Asked Questions (FAQs)
What are Organic Packaging Chip Substrates?
Organic Packaging Chip Substrates, also known as organic substrates or organic laminate substrates, are materials used in semiconductor packaging technology. They provide a platform for mounting and interconnecting semiconductor chips within integrated circuits (ICs) and other electronic devices.
What are the functions of Organic Packaging Chip Substrates?
Organic Packaging Chip Substrates serve several functions, including providing a mounting surface for semiconductor chips, facilitating electrical interconnection, routing signals, distributing power, managing thermal dissipation, and offering mechanical support and protection to the chips.
How do Organic Packaging Chip Substrates differ from PCBs?
While both Organic Packaging Chip Substrates and Printed Circuit Boards (PCBs) are used in electronics, they serve different purposes. Organic substrates primarily facilitate semiconductor chip mounting and interconnection within IC packages, while PCBs interconnect various electronic components within a system.
What types of Organic Packaging Chip Substrates are available?
There are various types of Organic Packaging Chip Substrates, including printed circuit boards (PCBs), chip-on-board (COB) substrates, flexible substrates, build-up substrates, embedded substrates, copper-clad laminates, and ceramic substitutes.
What is the relationship between Organic Packaging Chip Substrates and IC packaging?
Organic Packaging Chip Substrates are integral components of IC packaging, providing the structural support and electrical interconnection for semiconductor chips within the packaged IC. IC packaging encapsulates the chip and substrate within a protective enclosure, forming a complete semiconductor package.
How are Organic Packaging Chip Substrates produced?
The production process for Organic Packaging Chip Substrates involves fabricating the substrate material, laminating multiple layers together, patterning conductive traces, forming vias, applying surface finishes, and conducting testing and inspection to ensure quality and performance.
Conclusion
In conclusion, Organic Packaging Chip Substrates are essential components in semiconductor packaging technology, providing the structural support, electrical interconnection, and thermal management required for mounting semiconductor chips within integrated circuits (ICs) and other electronic devices. They serve several functions, including facilitating chip mounting, routing signals, distributing power, managing thermal dissipation, and offering mechanical support and protection to the chips.
Organic Packaging Chip Substrates differ from Printed Circuit Boards (PCBs) in terms of functionality, design complexity, manufacturing process, cost, and application. While organic substrates primarily focus on semiconductor chip mounting and interconnection within IC packages, PCBs interconnect various electronic components within a system.
There are various types of Organic Packaging Chip Substrates available, including printed circuit boards (PCBs), chip-on-board (COB) substrates, flexible substrates, build-up substrates, embedded substrates, copper-clad laminates, and ceramic substitutes. Each type offers unique advantages and is selected based on specific application requirements.
The relationship between Organic Packaging Chip Substrates and IC packaging is intertwined, with organic substrates serving as integral components of IC packaging, providing the necessary support and interconnection for semiconductor chips within the packaged IC.
The production technology of Organic Packaging Chip Substrates involves fabricating the substrate material, laminating multiple layers together, patterning conductive traces, forming vias, applying surface finishes, and conducting testing and inspection to ensure quality and performance.
Overall, Organic Packaging Chip Substrates play a crucial role in semiconductor packaging technology, enabling the assembly, interconnection, and reliable operation of semiconductor chips in a wide range of electronic devices. Their continued development and innovation contribute to advancements in electronics, driving progress in various industries and applications.