Organic Packaging Substrate Manufacturing. we can produce the best samllest bump pitch with 100um, the best smallest trace are 9um. and the smallest gap are 9um. most of the design are 15um to 30um trace and spacing.
Within the realm of Printed Circuit Boards (PCBs), the expression “organic packaging” frequently refers to Organic Substrate or Organic PCBs. It’s crucial to clarify that this terminology doesn’t suggest the integration of materials associated with organic farming. Rather, it acts as a counterpart to the term “ceramic substrate.”
Organic PCBs are composed of materials like glass-reinforced epoxy laminates, featuring layers of fiberglass cloth infused with epoxy resin. Opting for an organic substrate provides a cost-effective solution for PCBs, widely adopted in various electronic devices.
Organic PCBs boast several advantages:
Cost-Efficiency: Organic materials typically come at a lower cost than ceramics, making Organic PCBs a more financially judicious option.
Weight Considerations: Organic PCBs exhibit a lighter profile compared to their ceramic counterparts, a crucial consideration in applications where weight is of utmost importance.
Manufacturing Streamlining: The manufacturing processes for organic PCBs are often simplified and well-established compared to those for ceramic PCBs.
Dielectric Prowess: Organic materials frequently showcase commendable dielectric properties, vital for insulating diverse layers of a PCB.
However, it’s essential to acknowledge the limitations of organic PCBs. They may not dissipate heat as efficiently as ceramic substrates and might lack the same mechanical resilience. The decision between organic and ceramic PCBs hinges on the specific requirements of the electronic application.
In summary, when the term “organic packaging” arises in discussions about Printed Circuit Boards (PCBs), it generally denotes PCBs fashioned from organic substrate materials like epoxy and fiberglass.
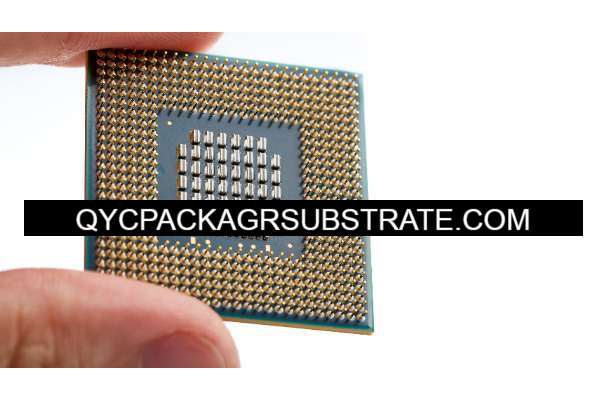
What Functions Does Organic Packaging substate Serve?
Organic packaging, as applied in the realm of Printed Circuit Boards (PCBs), assumes pivotal roles, addressing various crucial functions that enhance the overall efficacy and efficiency of electronic devices. The following delineates key responsibilities organic packaging fulfills within PCBs:
Electrical Insulation: Organic materials, particularly glass-reinforced epoxy laminates, excel in furnishing robust electrical insulation. This function is paramount for averting undesirable electrical interactions, ensuring the seamless functionality of diverse circuit components on the PCB.
Cost-Effective Solutions: Organic PCBs typically present a more economically viable production alternative when compared to materials such as ceramic PCBs. This cost advantage positions them favorably across a spectrum of electronic applications, contributing to cost-effectiveness.
Lightweight Construction: The incorporation of organic substrates, lighter than counterparts like ceramics, plays a pivotal role in achieving an overall lightweight design for electronic devices. This aspect is particularly critical in weight-sensitive applications, such as aerospace and portable consumer electronics.
Streamlined Manufacturing Processes: Organic PCBs benefit from manufacturing processes characterized by simplicity and well-established procedures, distinguishing them from alternatives like ceramic PCBs. This streamlined manufacturing contributes to expedited production cycles and heightened operational efficiency.
Dielectric Proficiency: Organic materials selected for PCBs commonly exhibit commendable dielectric properties. This attribute is indispensable for efficient insulation between distinct layers of the PCB, preventing electrical interference, and ensuring the steadfast reliability of electronic components.
Flexible Design Parameters: Organic PCBs offer design flexibility, accommodating intricate and customized circuit layouts. This adaptability proves advantageous in tailoring PCB designs to meet the specific requirements and functionalities of diverse electronic applications.
Environmentally Considerate Practices: The choice of organic materials aligns with environmentally conscious practices, given their relatively lower environmental impact compared to certain alternatives. This consideration spans both the production and disposal phases of organic PCBs, contributing to sustainability.
Mechanical Adequacy: While not possessing the same mechanical robustness as materials like ceramic substrates, organic PCBs still offer satisfactory mechanical compatibility for a myriad of applications. Thoughtful design considerations can further enhance their resilience to mechanical stress.
In summary, organic packaging in PCBs assumes a multifaceted role, serving as a linchpin for electrical insulation, cost-effectiveness, lightweight design, streamlined manufacturing, dielectric efficacy, design flexibility, environmentally conscious practices, and mechanical compatibility across diverse electronic applications.
What Are the Different Types of Organic Packaging substrate?
Within the intricate realm of Printed Circuit Boards (PCBs), the notion of organic packaging unfolds through deliberate utilization of diverse organic substrate materials. Departing from conventional packaging paradigms, often associated with end-user products, this exploration delves deep into the nuanced composition and structural intricacies of PCBs. The canvas of organic packaging materials unfolds as follows:
FR-4 (Flame Retardant-4): Taking a lead role, FR-4 serves as a stalwart organic substrate material in PCBs. Concocted as a glass-reinforced epoxy laminate, it not only guarantees robust electrical insulation but also showcases commendable flame resistance. Its ubiquity stems from the harmonious blend of cost-effectiveness and consistent performance across an array of electronic applications.
FR-2: Running parallel to FR-4, FR-2, another organic substrate material, typically originates from phenolic resin-impregnated paper. Although not as pervasive, it finds its niche in specific scenarios where cost considerations exert considerable influence.
Polyimide (PI): Revered for its resilience against high temperatures and intrinsic flexibility, polyimide plays a versatile role as an organic polymer material. Frequently enlisted as a substrate in flexible PCBs (FPCBs) or rigid-flex PCBs, it facilitates the adaptability of the board to bend or conform to specific shapes.
Bismaleimide Triazine (BT): Stepping into the spotlight, BT earns its reputation as a high-performance organic substrate material celebrated for its exceptional thermal and electrical properties. Its deployment is frequent in applications demanding high-frequency signals, particularly in cutting-edge technologies like microwave and radio frequency (RF) applications.
Liquid Crystal Polymer (LCP): Representing another facet of organic material, LCP claims its position in high-frequency and high-speed PCBs. Recognized for favorable electrical properties, low moisture absorption, and dimensional stability, LCP often takes the stage in demanding applications such as telecommunications and aerospace.
The nuanced selection of a specific organic packaging material is akin to a delicate dance, intertwined with considerations spanning cost, thermal properties, electrical performance, flexibility requisites, and the targeted application of the PCB. Each variant of organic material unfurls its unique advantages, seamlessly aligning with the diverse needs inherent in electronic devices.
What is the Relationship Between Organic Packaging substates and IC Encapsulation?
Organic packaging and IC (Integrated Circuit) encapsulation, though distinct in their functions, intricately intertwine within the sophisticated tapestry of electronics manufacturing. Let’s navigate the nuanced connection between these two pivotal elements:
Organic Packaging:
Definition: Organic packaging, nestled in the domain of Printed Circuit Boards (PCBs), revolves around the strategic utilization of organic substrate materials such as epoxy and fiberglass. These materials, akin to the foundation of a structure, underpin the assembly’s structural integrity.
Role: As the substrate, organic packaging assumes the role of a canvas, facilitating the mounting and interconnection of electronic components, including integrated circuits. It stands as a cornerstone, offering not just insulation but also crucial mechanical support.
IC Encapsulation:
Definition: IC encapsulation, a protective ritual, involves encapsulating individual integrated circuits within a shielding cocoon. This encapsulation acts as a guardian, warding off external adversaries like moisture, dust, and mechanical stresses.
Function: Paramount for the sustained vitality of integrated circuits, the encapsulation materials construct a shield that not only insulates against environmental elements but also aids in the judicious dissipation of heat during operation.
Interplay Between Organic Packaging and IC Encapsulation:
Intrinsic Connection: The interplay between organic packaging and IC encapsulation is not just incidental but rather inherent. The organic substrate, forming the very canvas for the assembly, becomes the stage where ICs are strategically positioned.
Cohesive Integration: In the meticulous dance of assembly, ICs find their place on the organic substrate. Following this choreography, IC encapsulation takes center stage, fortifying and shielding these mounted ICs, ensuring their resilience across diverse operational landscapes.
Material Symphony: Both organic packaging and IC encapsulation choreograph a symphony of material compatibility, ensuring a seamless integration of electronic components within the assembly.
Collective Elevation: In a collaborative crescendo, organic packaging and IC encapsulation harmonize to elevate the overall functionality, reliability, and endurance of electronic devices. This synergy constructs a robust environment, fostering the optimal performance of integrated circuits.
In essence, organic packaging and IC encapsulation engage in a dance of collaboration within the realm of electronics manufacturing. While organic packaging sets the stage for electronic components, IC encapsulation adds a protective layer, ensuring the sustained functionality and durability of individual integrated circuits. Their compatibility and collaborative functionality emerge as the choreographers, shaping the resilience and performance of electronic devices.
What Are the Differences Between Organic Packaging substrate and Traditional PCBs?
Organic packaging and traditional PCBs (Printed Circuit Boards) converge in the expansive field of electronics, each wielding a distinct influence. Let’s explore the attributes that set these two components apart:
Definition:
Organic Packaging: This term narrows its focus to the materials forming the substrate of a PCB. It revolves around the purposeful utilization of organic elements like epoxy and fiberglass, casting a spotlight on the foundational bedrock of the electronic assembly.
Traditional PCBs: This term paints a broader stroke, encompassing the entirety of the PCB architecture. It encapsulates not just the substrate but also the conductive elements, typically copper traces intricately weaving the circuit. It symbolizes the comprehensive canvas hosting an array of electronic components.
Material Composition:
Organic Packaging: Places a premium on organic polymers like epoxy and fiberglass, acting as the sturdy underpinning for the substrate. These materials lay the groundwork for securing electronic components.
Traditional PCBs: Encompass a wider spectrum of materials, ranging from organic substrates like FR-4 to potential alternatives such as ceramics or metal-core materials. Traditional PCBs go beyond the substrate, involving conductive layers and protective features like solder masks.
Function:
Organic Packaging: Primarily contributes to the structural robustness of the PCB, providing both mechanical support and electrical insulation. It establishes the foundational platform for affixing electronic components.
Traditional PCBs: Serve as the comprehensive stage for hosting intricate electronic circuits, offering the necessary structure and pathways for the seamless transmission of electrical signals.
Versatility:
Organic Packaging: Tends to exhibit greater design flexibility owing to the infusion of organic polymers. This flexibility allows for intricate and customized circuit layouts.
Traditional PCBs: Present a degree of flexibility, yet constraints may emerge based on the chosen substrate material. Widely-used options like FR-4 strike a balance between cost and performance.
Complexity:
Organic Packaging: Concentrates specifically on the substrate, playing a pivotal role within the broader PCB assembly process. It is a crucial element but not the sole determinant of the PCB structure.
Traditional PCBs: Encompass the entire structural landscape of the board, including the substrate, conductive layers, solder masks, and potentially additional features like vias and specialized surface finishes.
In essence, while organic packaging hones in on substrate materials, traditional PCBs embrace the holistic architecture of the board, constituting both the substrate and the intricate conductive elements. Organic packaging emerges as a critical influencer, shaping the foundational materials of PCBs and impacting their structural resilience and overall functionality.
What is the Main Structure and Production Technologies of Organic Packaging?
In the intricate domain of Printed Circuit Boards (PCBs), the crafting of organic packaging involves a meticulous interplay of materials and advanced manufacturing techniques. Let’s navigate through the key components and production methodologies in a distinctive manner:
Elemental Symphony of Organic Packaging:
Foundation of Marvels:
Organic Alchemy: At the core of organic packaging lies a symphony of organic polymers, notably the dynamic duo of epoxy and fiberglass. These materials form an unyielding and insulating foundation, setting the stage for the entire assembly.
Layers Unveiled:
Copper Tapestry: With precision akin to an unfolding tapestry, conductive layers, often adorned in copper brilliance, grace the substrate. Copper, a virtuoso in conductivity, intricately weaves the essential circuit pathways.
Solder Mask Veil: An elegant solder mask layer enters the scene, gracefully shielding the copper intricacies from unintended soldering and adding a layer of enchanting insulation.
Silkscreen Sonata: This layer, akin to a lyrical sonata, displays markings, labels, or symbols, providing a harmonious guide to component placement, reference designators, and other pertinent details.
Electronic Harmony:
Mounting Crescendos and Vias Verse: Designated zones for electronic components’ mounting, coupled with vias performing a poetic interconnection between different layers, create a symphony of electronic harmony.
Integrated Circuitry Overture: A diverse ensemble of electronic components, featuring the overture of Integrated Circuits (ICs), resistors, capacitors, and an assortment of active and passive instruments, finds its designated positions on the PCB stage.
Choreography of Production Techniques:
Substrate Prelude:
Cutting Crescendo and Cleansing Ballet: The substrate material, often in grand sheet format, engages in a carefully choreographed dance of cutting and cleansing, ensuring purity and precision.
Copper Cadence:
Copper Foil Elegance: The substrate engages in a dance of elegance with copper foil, where heat and pressure perform a sophisticated ballet to establish the indispensable conductive layers.
Circuit Composition:
Photoresist Pas de Deux: A delicate application of photoresist initiates a graceful pas de deux with the copper-clad substrate.
Exposure and Development Waltz: Bathed in the glow of UV light, the PCB engages in a waltz of exposure and development, where unexposed photoresist gracefully exits the stage, revealing the enchanting circuit pattern.
Etching Elegance: Chemical etching takes center stage, selectively removing exposed copper and leaving behind the meticulously designed circuit traces.
Layer Lyrical Build-Up:
Symphonic Layer Stacking: In the creation of multilayer PCBs, layers engage in a lyrical dance, stacking and aligning with precision. Vias join the symphony, establishing seamless interconnections and crafting a three-dimensional circuit opus.
Surface Finish Sonata:
Applause-Worthy Surface Finish: To protect exposed copper and enhance solderability, a surface finish takes the stage. Options like HASL, ENIG, and OSP perform an applause-worthy finale.
Component Choreography and Soldering Serenade:
Automated Assembly Ballet: Utilizing automated pick-and-place machines, electronic components, including the maestros of ICs, gracefully find their positions on the PCB stage.
Reflow Soldering Rhapsody: The PCB undergoes a reflow soldering rhapsody, where solder paste melts in a crescendo of heat, forming robust connections between components and the PCB.
Testing Tutelage:
Electrical Testing Tutelage: Rigorous electrical testing takes on the role of a knowledgeable tutor, ensuring correct connections and validating adherence to specified electrical parameters.
Final Inspection Finale and Packaging Pinnacle:
Visual Inspection Vignette: A visual inspection, akin to a captivating finale, unfolds to identify any defects or irregularities.
Packaging Prestige: Following a flawless inspection, the PCB takes its bow, being attentively packaged and readied for its grand performance in the realm of electronics.
These steps offer a distinctive exploration of the intricate dance between materials and methodologies in the creation of organic packaging for PCBs. The choreography may vary based on specific requirements, industry standards, and the unique design intricacies of the PCB.
Frequently Asked Questions (FAQs)
Are Organic Packaging substrates Materials Environmentally Sustainable?
Answer: Indeed, organic packaging materials are generally recognized for their environmental sustainability when compared to conventional packaging materials. They often exhibit ease of decomposition, contributing to reduced environmental impact.
Is Recyclability a Feature of Organic Packaging substrates Materials?
Answer: Many organic packaging materials are designed with recyclability or compostability in mind. However, the specific recyclability may vary based on the material and its composition.
Do Organic Packaging Manufacturers Offer Customization Options?
Answer: Absolutely, many organic packaging manufacturers provide customization services to meet the unique needs and branding specifications of their clients. This could involve tailored sizes, prints, and designs.
Is Organic Packaging More Expensive than Traditional Options?
Answer: While organic packaging materials might carry a slightly higher cost, attributed to their sustainable and eco-friendly sources, prices can vary depending on factors such as volume and material type.
How Should I Dispose of Organic Packaging Materials?
Answer: Many organic packaging materials are designed for composting or recycling. It is crucial to adhere to local waste disposal guidelines for proper and responsible disposal.
Can Organic Packaging be Utilized for Food Products?
Answer: Certainly, organic packaging is commonly employed for food items, encompassing materials such as compostable plastics, recycled paper, or other biodegradable options.
Conclusion
To sum up, the dynamic landscape of organic packaging unfolds as a canvas of sustainable innovation, guided by manufacturers committed to eco-friendly principles. These industry trailblazers hold the key to shaping materials that go beyond mere functionality, making substantial strides toward minimizing our environmental impact.
By tapping into the potential of organic polymers, exemplified by the dynamic interplay of epoxy and fiberglass, these manufacturers give rise to packaging solutions that not only fulfill practical needs but also embody a dedication to reducing our ecological footprint. The distinctive features of biodegradability, recyclability, and the embrace of renewable resources position organic packaging as a paradigm shift away from traditional alternatives.
Engaging with these manufacturers promises a diverse array of customizable products, spanning from bags to containers and wraps. This broad spectrum not only caters to specific demands but also aligns with a broader ethos of sustainable manufacturing. Certifications such as “USDA Organic,” “Compostable,” and “FSC Certified” serve as steadfast assurances, affirming products that rigorously adhere to eco-friendly production standards.
While the initial cost of organic packaging materials may carry a slight premium, it signifies a commitment to conscientious and sustainable practices. Considerate end-of-life considerations underscore these materials, with many options tailored for composting or recycling, steering us toward a circular and environmentally attuned product lifecycle.
In essence, the reciprocal relationship between discerning consumers and organic packaging manufacturers propels us into an era where packaging solutions not only serve utilitarian purposes but also embody a dedication to a lush and sustainable future. As the resonance for eco-friendly practices amplifies, organic packaging emerges as a pioneering force, heralding a new era for the packaging industry—one that harmonizes functionality with a profound reverence for our planet.