Organic Substrate FC-BGA Design Guideline. Design rules of substrate in packaging and package substrate manufacturer. We use advanced Msap and Sap technology to produce the BGA substrates, High multilayer interconnection substrates from 4 to 20 layers,
In the world of advanced engineering and cutting-edge technology, substrate packaging emerges as a fundamental component of electronic and industrial applications. This often overlooked, yet essential element plays a pivotal role in guaranteeing the seamless and dependable performance of the everyday devices we rely on.
While it’s easy to take for granted the hidden components within our electronic devices, the significance of well-executed packaging design cannot be emphasized enough.Substrate packaging is like the hidden foundation of a skyscraper, supporting the towering structure above. Just as a skyscraper’s foundation must be designed meticulously to withstand various stresses and ensure stability, substrate packaging must be carefully crafted to ensure the efficient functioning of electronic devices and systems.
appreciate the significance of substrate packaging, one must recognize the vital connection it shares with design rules. These design rules are like the guiding principles that engineers and manufacturers adhere to when creating substrates. The harmony between design rules and substrate packaging is what leads to the successful creation of products that excel in performance, durability, and reliability. Without a thorough understanding of these design rules, achieving product success can be an elusive goal.
In the upcoming sections, we will take a closer look at the complexities of substrate packaging, delve into the essential factors to consider, and uncover the fundamental design principles that guide its development. By the conclusion of this article, you will acquire invaluable knowledge regarding how meticulous packaging design can profoundly influence the excellence and performance of electronic and industrial products.
Understanding Substrate Packaging
Defining Substrate Packaging
Substrate packaging, in the realm of electronics and advanced manufacturing, refers to the crucial art and science of designing, fabricating, and assembling the foundational layers that support electronic components. Think of it as the hidden backbone behind your devices, whether it’s your smartphone, computer, or even intricate medical equipment. These substrates are essentially the unsung heroes of modern technology, providing a stable platform for the intricate interplay of components and connections.
The significance of substrate packaging becomes evident when you consider the complexity and miniaturization of electronic devices in the 21st century. Without a robust substrate, the delicate electronic components wouldn’t have a solid foundation to function reliably. Substrate packaging is all about ensuring the stability, connectivity, and performance of the intricate electronic ecosystem that powers our daily lives.
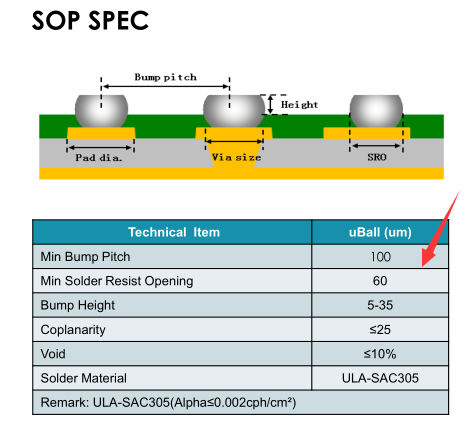
The Role of Substrates in Electronics and Beyond
Substrates are not exclusive to the electronics industry. They play a pivotal role in various sectors, ranging from automotive and aerospace to healthcare and telecommunications. Understanding their versatile role is essential:
1.Electronics:In the realm of electronics, substrates serve as the fundamental foundation upon which integrated circuits, processors, memory chips, and various other electronic components are affixed. Their pivotal role lies in furnishing both the essential electrical connections and the necessary mechanical support to ensure the seamless and efficient operation of these components.
2.Automotive: In the automotive sector, substrates find application within engine control modules, infotainment systems, and safety systems. They must withstand extreme temperature variations and vibrations while ensuring the reliability of critical electronic functions.
3.Aerospace:In the aerospace industry, substrates hold a pivotal role in bolstering critical systems, including avionics, navigation, communication, and control systems. These substrates are held to exacting standards to guarantee reliability and longevity, thus upholding the highest levels of safety and performance throughout flight operations
4.Healthcare: In the healthcare sector, substrates are employed in medical devices and equipment, enabling precise data collection, diagnostics, and patient care. Reliability and accuracy are paramount.
Telecommunications: The telecommunications industry relies on substrates for various components, such as routers, switches, and base station equipment, ensuring that data transmission and network stability are maintained.
A unifying element across these varied industries lies in the essential function of substrates, which play a foundational role in upholding the structural integrity, electrical connectivity, and effective thermal regulation of electronic systems. As technology continually advances, the significance of substrates further amplifies, as they underpin the advancements propelling our interconnected world towards progress and innovation.
Key Considerations in Substrate Packaging Design
Designing substrate packaging is a multifaceted task that demands careful attention to various critical factors. These considerations can be categorized into three key aspects: electrical and thermal performance, material selection, and component placement. These facets collectively determine the overall functionality and effectiveness of electronic devices.
Electrical and Thermal Performance
1.Maximizing Electrical Efficiency: The design of the substrate plays a pivotal role in determining the electrical efficiency of a device. The arrangement of traces, vias, and electrical components on the substrate directly impacts the electrical properties, such as impedance, signal speed, and power distribution. Engineers must meticulously plan the substrate layout to minimize signal distortion and energy loss.
2.Significance of Heat Dissipation:Efficient heat dissipation is a crucial aspect of electronic device design, ensuring that components remain within safe temperature limits and preventing overheating issues. An effectively designed substrate should incorporate elements that promote the swift and efficient removal of heat from heat-generating components. This ensures that the device can operate within its designated temperature limits.This is particularly important in high-performance electronics where excess heat can lead to reduced lifespan or even failure.
Material Selection
1.Choosing the Right Materials: Choosing the right materials for substrate construction is a crucial decision in the packaging design process. Material selection significantly impacts a device’s performance, reliability, and overall cost. It is imperative to meticulously assess factors such as thermal conductivity, dielectric constant, and mechanical strength to make informed material choices. These considerations have a profound impact on the quality and economics of the final product.Different applications may require specific materials – for instance, FR-4 for standard PCBs, ceramic for high-frequency applications, or flexible substrates for bendable devices.
2.Types of Substrates: Substrate packaging designs are not one-size-fits-all. Engineers have a range of substrate types at their disposal, each tailored to specific requirements. For example, FR-4 (Flame Retardant-4) is a common choice for conventional PCBs due to its cost-effectiveness and versatility. Ceramic substrates are favored in radio frequency (RF) and microwave applications due to their excellent electrical properties. Flexible substrates, also known as flex PCBs, are essential for applications where bending or flexibility is required, such as wearable devices.
Component Placement
1.Strategic Component Placement: Proper component placement on the substrate is a critical element of successful substrate packaging design. Engineers must strategically position components like integrated circuits, resistors, capacitors, and connectors to ensure efficient signal routing, minimize interference, and enable ease of assembly. The placement of components should also take into account thermal considerations to avoid concentrated heat zones.
2.Balancing Signal Integrity and Thermal Management: The positioning of components can have a dual impact on signal integrity and thermal management. An optimized layout will ensure minimal signal crosstalk or interference, preserving the integrity of high-speed data or sensitive analog signals. Simultaneously, it will facilitate the efficient distribution of heat, preventing localized hotspots and ensuring the overall thermal stability of the device.
By addressing these key considerations in substrate packaging design, engineers can create robust and efficient electronic devices that meet the demands of their intended applications while considering factors like electrical performance, material suitability, and component placement. These considerations are essential in achieving product success and reliability.
Design Rules for Substrate Packaging
Signal Integrity Considerations
1.Optimizing Trace Routing: To ensure high signal integrity, the careful routing of traces on the substrate is paramount. Designers should follow specific guidelines based on signal frequency and amplitude. For high-speed signals, shorter and wider traces with controlled impedance are essential to minimize signal loss and maintain integrity.
2.Impedance Control: Impedance mismatches can lead to signal reflections, distortion, and interference. It’s critical to maintain consistent impedance across the signal traces. This is achieved by controlling the width, spacing, and dielectric constant of the traces, as well as minimizing impedance changes in transitions.
Thermal Management
1.Strategies for Effective Heat Dissipation: Overheating can seriously affect both the substrate and the components it houses. Designers must incorporate strategies for efficient heat dissipation. This may involve the strategic placement of copper planes and thermal vias to conduct heat away from critical components.
2.The Role of Vias and Thermal Vias: Vias are crucial for conducting heat away from the PCB. Thermal vias, in particular, are specifically designed to enhance heat dissipation. They connect the copper layers on the substrate to transfer heat efficiently. Proper placement and design of these vias can significantly impact thermal performance.
Layer Stackup and Routing Guidelines
1.Importance of Layer Arrangement: The arrangement of substrate layers in a stackup can greatly affect the performance of the packaging. Different applications may require varying layer counts and configurations. A well-planned stackup minimizes signal interference, reduces crosstalk, and optimizes the overall electrical and thermal characteristics.
2.Routing Best Practices for Different Designs: Routing guidelines can differ based on the specific design requirements. High-speed digital designs may demand controlled impedance routing, while analog circuits might focus on minimizing noise and interference. Understanding the specific needs of the design and applying best practices accordingly is crucial for a successful substrate package.
Design for Manufacturability (DFM)
1.Design for Ease of Manufacturing and Assembly: The design phase is the ideal time to consider how the substrate will be manufactured and assembled. This includes designing features that simplify production, such as standardized component footprints, fiducial marks for alignment, and easy access for testing.
2.Reducing Cost and Lead Time through Thoughtful Design: DFM principles not only improve the manufacturability but also have a direct impact on cost and lead time. Designs that reduce complexity, minimize the need for custom tooling, and ensure components can be easily sourced can lead to cost savings and shorter production times.
By incorporating these design rules into substrate packaging, designers can create solutions that optimize signal integrity, thermal performance, layer stackup, and manufacturability while also reducing costs and lead times. This holistic approach ensures the success of the final product.
Case Studies and Examples
Real-World Success Stories
1.High-Performance PCB for 5G Devices
Showcase a case study where a company designed a high-performance printed circuit board (PCB) for 5G communication devices.
Emphasize how adhering to design rules led to reduced signal loss and improved signal integrity, supporting seamless 5G connectivity.
Highlight the role of carefully planned trace routing and layer stackup in achieving optimal electrical performance.
2.Ceramic Substrate in Aerospace
Discuss a real-world application in the aerospace industry where a ceramic substrate was used in a critical component.
Illustrate how the choice of materials, specifically ceramics, met stringent thermal and electrical requirements.
Emphasize the benefits of excellent thermal management and longevity due to proper design.
Benefits of Adhering to Design Rules
1.Cost Savings and Efficiency
Showcase how adhering to design rules can result in cost savings during manufacturing.
Discuss examples where well-optimized designs led to reduced waste and fewer manufacturing errors.
Highlight the importance of design for manufacturability (DFM) principles in streamlining production processes.
2.Enhanced Product Reliability
Share instances where following design rules led to improved product reliability.
Discuss the importance of minimizing signal loss through impedance control and trace routing, leading to fewer product failures.
Emphasize the long-term cost benefits and customer trust associated with reliable products.
3.Competitive Advantage
Present cases where companies gained a competitive edge by adhering to substrate packaging design rules.
Illustrate how innovative designs and adherence to signal integrity and thermal management principles led to superior products.
Highlight the ability to offer high-performance solutions in a competitive market as a key benefit.
4.Reduced Time-to-Market
Share examples where efficient substrate packaging design accelerated the time-to-market for products.
Discuss how well-planned designs facilitated faster prototyping, testing, and production.
Stress the benefits of being the first to market with a reliable product in rapidly evolving industries.
By incorporating these real-world examples and highlighting the benefits of adhering to design rules, readers can gain a deeper understanding of the practical implications of proper substrate packaging design, which can ultimately lead to successful and cost-effective product development.