Package Substrate manufacturer.High speed and high frequency material packaging substrate manufacturing. Advanced packaging substrate production process and technology.
PCB substrates are the backbone of the electronics industry, providing the essential groundwork for assembling electronic components and circuits. Selecting the right PCB substrate is comparable to selecting the perfect canvas for a work of art. It marks the initial and crucial step in guaranteeing the functionality, durability, and endurance of your electronic creations.
Brief Overview of the Importance of PCB Substrates
In the ever-evolving realm of electronics, PCB substrates are the unsung heroes, silently supporting and connecting the intricate web of components that bring our devices to life. They serve as the foundation, often overlooked, yet instrumental in the world of modern technology. Whether you’re crafting a smartphone, launching a satellite, or developing a medical device, the selection of PCB substrate material has the potential to be a project-defining factor.
Emphasizing the Critical Role of Choosing the Right Substrate Material
The success of any electronic design hinges on a critical decision – the selection of the PCB substrate material.The decision regarding the PCB substrate is of paramount importance, as it has a profound impact on not just the electrical characteristics but also the mechanical and thermal attributes of the end product. It goes beyond merely accommodating components; it revolves around enhancing their operational efficiency and dependability.
The importance of choosing the right substrate material cannot be overstated. It affects signal integrity, heat dissipation, and the overall lifespan of the electronic device.Selecting the ideal PCB substrate is much like choosing the perfect ingredient for a recipe. The right material can significantly enhance performance, while the wrong choice could result in a disastrous outcome.
In our exploration of the complexities of PCB substrate selection, we will examine the fundamental requirements, the various available materials, and offer guidance on making well-informed decisions tailored to specific application requirements. Whether you’re an engineer, a designer, or simply someone intrigued by the realm of electronics, grasping the significance of PCB substrates is paramount to ensuring that your creations not only operate but thrive in the dynamic world of digital technology.
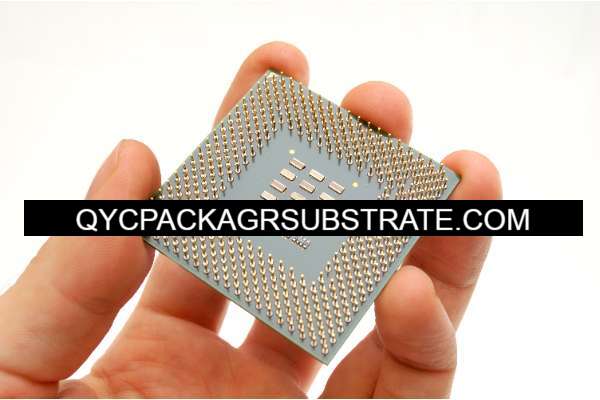
Basic Requirements for PCB Substrates
When selecting the ideal PCB substrate, it’s crucial to consider a range of factors that encompass electrical performance, mechanical properties, and thermal performance, all of which play pivotal roles in determining the substrate’s suitability for the application. Let’s delve into these key aspects:
Electrical Performance
Dielectric Constant: also known as relative permittivity, is a fundamental characteristic of a substrate material. It quantifies the material’s capacity to store electrical energy within an electric field.
Dissipation Factor: The dissipation factor, also known as loss tangent, quantifies the energy loss in a substrate when subjected to an alternating current. A low dissipation factor is desirable in high-frequency applications as it ensures minimal signal attenuation. It’s particularly crucial for RF circuits where signal loss should be minimized.
Mechanical Properties
Flexural Strength: Flexural strength determines a substrate’s ability to withstand mechanical stress and bending without deformation or fracture. PCBs are often subjected to various forces during manufacturing and usage, making flexural strength vital for ensuring the board’s structural integrity.
Coefficient of Thermal Expansion: The coefficient of thermal expansion (CTE) measures how much a material expands or contracts with changes in temperature. A PCB substrate should have a CTE that closely matches that of the components mounted on it. A well-matched CTE helps prevent stress-related issues such as solder joint failures due to temperature variations.
Thermal Performance
Thermal Conductivity: Thermal conductivity plays a crucial role in effectively dispersing heat generated by high-power electronic components on a PCB. A substrate with excellent thermal conductivity efficiently moves this heat away, safeguarding against overheating and potential component damage. In applications with substantial power dissipation, such as power electronics, opting for a substrate with high thermal conductivity becomes imperative.
Environmental Temperature Range: The environmental temperature range defines the expected operating temperature conditions for the PCB. It is essential to select a substrate that can endure these temperature extremes, whether it’s in frigid environments or high-temperature applications.This ensures the PCB’s reliable performance and longevity under varying conditions.
In summary, selecting the appropriate PCB substrate material involves a careful assessment of its electrical, mechanical, and thermal properties. These properties should align with the specific requirements of the application, ensuring that the PCB functions reliably and efficiently within its intended environment.
Common PCB Substrate Materials
FR-4, also known as Flame Retardant 4, stands as one of the most commonly employed materials for PCB substrates. Its widespread adoption can be attributed to a multitude of essential attributes that render it a favored selection for a diverse array of applications:
Introduction to the characteristics of FR-4 material:
Dielectric Constant: FR-4 possesses a comparatively low dielectric constant, rendering it well-suited for high-frequency applications.
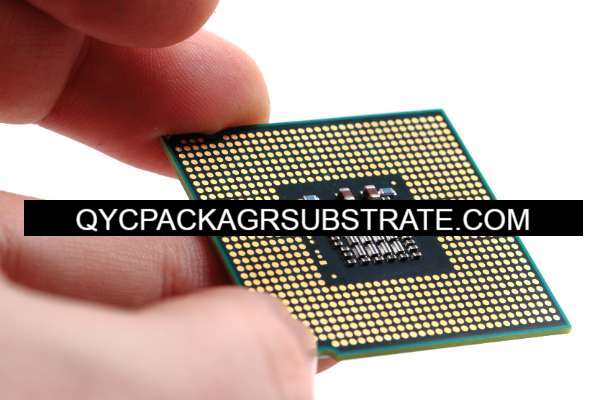
Thermal Stability: FR-4 demonstrates robust thermal stability, enabling it to endure elevated temperatures encountered during soldering processes.
Cost-Effective: FR-4 is cost-effective and readily available, making it a preferred choice for many projects.
Flame Retardancy: As the name suggests, it has excellent flame-retardant properties, enhancing safety in electronic devices.
Application areas and limitations:
FR-4 is a widely favored option suitable for various applications such as consumer electronics, industrial controls, and automotive applications. Nevertheless, while it excels in typical usage scenarios, it may not be the most ideal choice for high-frequency and high-speed designs, primarily due to its limited signal integrity when operating at elevated frequencies.
Metal Substrates
Metal substrates, typically made of materials like aluminum or copper, provide an alternative to traditional FR-4 materials. These substrates have their own unique characteristics:
Introduction to Metal Substrate Characteristics:
Superior Thermal Conductivity: Metal substrates exhibit outstanding thermal conductivity, rendering them well-suited for applications necessitating efficient heat dissipation.
Robustness and Longevity: These substrates are known for their rigidity and durability, delivering robust mechanical stability and reliable support for electronic components.
Well-Suited for High-Power Applications: Metal substrates are the preferred choice for high-power electronic devices owing to their exceptional heat dissipation capabilities.
Application areas and limitations:
Metal substrates find frequent application in LED lighting, power electronics, and high-power RF amplifiers. Nonetheless, their inherent stiffness can pose constraints in situations that demand flexibility. Moreover, they might not be well-suited for low-frequency circuits due to their electrical characteristics.
In contrast, high-frequency materials are purposefully designed to fulfill the requirements of RF and microwave applications, where preserving signal integrity and minimizing signal loss are of paramount importance.These materials possess specific characteristics.
Introduction to the characteristics of high-frequency materials:
Low Dielectric Constant: High-frequency materials have a low dielectric constant, reducing signal loss at higher frequencies.
Controlled Impedance: They allow for controlled impedance designs, crucial for RF circuits.
Minimal Loss Tangent: These materials have a low loss tangent, minimizing signal distortion.
Case Studies
Examples Illustrating Substrate Choices for Different Application Scenarios
High-Speed Digital Circuits:
Discuss a project where high-speed digital circuits were the primary application.
Explain the substrate material choice, such as FR-4, for its electrical properties.
Emphasize the importance of low dielectric constant and low dissipation factor.
RF Applications:
Share a case study involving RF (Radio Frequency) applications.
Highlight the selection of specialized high-frequency substrate materials.
Explain how materials with low loss and controlled impedance were crucial.
High-Temperature Environments:
Present a scenario where the PCB was exposed to elevated temperatures.
Describe the selection of a substrate material with a low coefficient of thermal expansion.
Discuss the outcome in terms of reliability in high-temperature conditions.
Analysis of the Chosen Materials’ Performance and Outcomes
High-Speed Digital Circuits:
Evaluate the performance of the chosen FR-4 material.
Discuss how it contributed to signal integrity and reduced interference.
Present data or metrics showcasing the success of this material choice.
RF Applications:
Analyze the performance of the high-frequency substrate materials used.
Emphasize the achievement of controlled impedance and minimal signal loss.
Share any measurements or results that demonstrate the effectiveness.
High-Temperature Environments:
Examine the behavior of the selected substrate in high-temperature conditions.
Discuss any thermal management solutions employed in conjunction with the material.
Provide real-world data or testing results to support the choice’s suitability.
By exploring these case studies, readers can gain insights into how specific substrate materials were chosen to address distinct application scenarios, emphasizing the critical role of substrate selection in achieving desired performance and outcomes in PCB design. These examples help reinforce the importance of aligning material properties with project requirements, while also considering cost-effectiveness.
How to Choose the Right Substrate Material
Choosing the right substrate material for your PCB is a crucial decision that hinges on a thorough evaluation of various essential factors:
Defining Project Requirements: To initiate the substrate selection process, it’s imperative to gain a comprehensive understanding of your project’s specific needs. This involves identifying the operational environment, including temperature ranges, humidity levels, and any distinct conditions that your PCB will encounter.
Determine the electrical performance needs, including the desired dielectric constant and dissipation factor. Whether your project involves high-speed digital circuits, RF applications, or high-temperature environments, these requirements will guide your choice.
Material Cost and Availability: Cost and material availability are significant considerations when selecting a PCB substrate. Different materials come with varying price points and may not always be readily available in the quantities you need. Assess your budget constraints and the feasibility of acquiring the chosen material in the necessary quantity. It’s important to remember that while certain specialized materials can deliver exceptional performance, their cost might make them unsuitable for some projects.
Balancing Performance and Cost: Achieving the perfect equilibrium between performance and cost can be a daunting endeavor.High-performance materials may deliver exceptional electrical characteristics, but they can also be expensive. On the flip side, cost-effective choices such as FR-4 could serve well in numerous scenarios but might not align with the requirements of high-frequency designs. It’s essential to weigh the trade-offs between achieving the desired performance and staying within your budget, while also evaluating the long-term advantages associated with the use of particular materials.
Collaborating with Manufacturers: Collaborating with experienced PCB manufacturers is a valuable step in the material selection process. Manufacturers have in-depth knowledge of various substrate materials and can provide insights into which materials align best with your project’s requirements. They can also advise on the manufacturability of your design with the chosen material. Initiating discussions with manufacturers during the design phase is a prudent approach to tap into their knowledge and streamline the journey from concept to production.
By factoring in these considerations and working closely with industry experts, you can arrive at an educated choice when it comes to selecting the most suitable substrate material for your PCB. This strategy guarantees that your project aligns with its performance objectives, financial limitations, and manufacturability, all while catering to the unique requirements of your application, be it high-speed digital circuits, RF applications, or demanding high-temperature settings.