Packaging Substrate Manufacturer. the Package Substrate will be made with Showa Denko and Ajinomoto High speed materials.or other types high speed materials and high frequency materials.
The package substrate holds a pivotal role in the intricate assembly of integrated circuits (ICs), establishing both the physical and electrical foundations that tether the IC to the broader electronic system. Fabricated from materials ranging from fiberglass-reinforced epoxy to advanced options like silicon interposers, this substrate not only provides essential structural support to the IC but also facilitates the necessary electrical connections between the IC and the circuit board of the system.
Its significance extends to determining the performance and reliability of electronic devices. Operating as a conduit for signal transmission, power distribution, and heat dissipation, the substrate is indispensable for ensuring the overall speed and functionality of the electronic system. A seamless power delivery mechanism and efficient heat dissipation play crucial roles in enhancing the reliability and lifespan of the IC.
Furthermore, the design intricacies and quality of the package substrate can exert an influence on the thermal performance of the IC. Effective dissipation of heat becomes paramount in preventing overheating, a condition that could otherwise compromise performance and potentially lead to failures in electronic components.
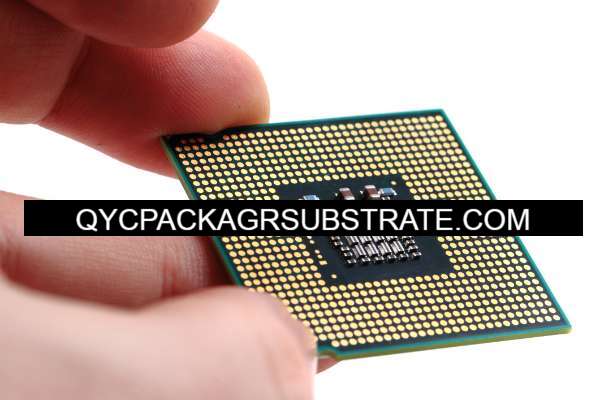
What Functions Can Package Substrate Manufacturers Provide?
Package substrate manufacturers play a pivotal role in delivering advanced substrates that form the backbone of electronic components, offering a suite of functions critical for optimal device performance.
At the forefront is their expertise in refining signal transmission. Employing cutting-edge materials and advanced manufacturing techniques, manufacturers skillfully address signal loss and distortion, ensuring a fluid and uninterrupted data flow. This meticulous approach not only boosts the speed and efficiency of electronic systems but also enhances their overall functionality.
In parallel, these manufacturers are adept at developing robust solutions for heat dissipation.By incorporating heat-conductive materials and pioneering design concepts, these manufacturers facilitate the effective dispersion of heat emanating from electronic components. This proactive approach acts as a protective measure against overheating, thereby safeguarding the dependability and longevity of electronic devices.
In the realm of power distribution, package substrate manufacturers excel. Their substrate designs incorporate low-impedance pathways and resilient power distribution networks, guaranteeing a steady and reliable power supply to integrated circuits. This commitment to power dynamics contributes significantly to the stability and consistency of electronic components.
Additionally, manufacturers consider aspects such as electrical insulation and mechanical strength in their designs. Rigorous insulation measures prevent unwanted interference and crosstalk, while robust mechanical strength shields components from physical stress and environmental factors, ensuring the substrate’s structural resilience.
Essentially, manufacturers of package substrates offer refined substrates designed to meet specific functionalities. They excel in fine-tuning signal transmission, optimizing heat dissipation, and ensuring smooth power distribution. These contributions are pivotal in elevating the holistic performance, dependability, and longevity of electronic devices.
What Are the Differences Between Various Types of Package Substrates?
Package substrate manufacturers specialize in crafting a range of substrates to cater to diverse requirements in electronic devices. Two primary categories include conventional substrates and high-density interconnect (HDI) substrates, each tailored for specific applications.
Conventional Substrates:
Material Composition: Traditional substrates commonly employ standard materials such as fiberglass-reinforced epoxy, presenting an economical solution suitable for a broad spectrum of electronic applications.
Design and Functionality: Geared towards applications prioritizing standard electrical connections, conventional substrates provide an economical choice where cost considerations play a crucial role.
Manufacturing Processes: The production processes for conventional substrates are well-established, employing traditional techniques for layering and connecting electronic components.
High-Density Interconnect (HDI) Substrates:
Material Composition: HDI substrates employ advanced materials, including specialized laminates and thin films. This enables a higher density of interconnections within the substrate.
Design and Functionality: Crafted to meet the challenges of miniaturization and intricate circuitry, HDI substrates boast a streamlined design characterized by finer lines and spaces. This intricacy enables heightened connection density, catering to the evolving demands of modern electronics.
Manufacturing Processes: HDI substrate production involves advanced techniques such as laser drilling and sequential build-up (SBU) technology. These methods enable the creation of intricate, high-density circuitry.
Manufacturers leverage their expertise to customize these substrate types based on specific device requirements. They navigate the trade-off between cost-effectiveness and advanced features, offering tailored solutions that align with the application’s demands.
By specializing in the production of both conventional substrates for standard applications and HDI substrates for high-performance, miniaturized devices, manufacturers ensure flexibility to meet the diverse needs of the electronics industry. This adaptability in substrate options proves crucial in supporting the development of various electronic devices, ranging from everyday consumer electronics to cutting-edge computing and communication systems.
Is There a Close Connection Between Package Substrate and IC Packaging?
The relationship between package substrates and IC packaging is indeed profound, forming a crucial alliance in the progression of chip packaging technology. In this symbiotic connection, package substrate manufacturers play a pivotal role as architects ensuring the stability and performance of integrated circuits (ICs).
Package substrates serve as the linchpin within IC packaging, furnishing the essential physical and electrical foundation that links the IC to the broader electronic system. They enable smooth interconnections, optimizing the transmission of signals, distribution of power, and dissipation of heat within the confines of the IC package. The careful selection of substrate materials, combined with inventive designs and manufacturing processes, exerts a profound influence on the reliability and functionality of the IC packaging.
In response to the dynamic shifts in chip packaging technology, which are driven by the need for reduced form factors, enhanced performance, and increased functionality, manufacturers of package substrates adapt and progress in unison. They pioneer advanced materials and techniques, contributing to the development of more compact and efficient substrates that align with the trend of miniaturization in IC packaging.
Furthermore, the collaboration between package substrate manufacturers and IC packaging specialists is crucial. This collaboration tackles specific challenges, especially in the domains of 3D packaging and heterogeneous integration. Package substrates play a crucial role in enabling the stacking of multiple ICs within limited spatial confines. This facilitation ensures a seamless integration that fosters both stability and optimal performance.
In essence, the synergy between package substrates and IC packaging is intricate and dynamic. Package substrate manufacturers, as integral contributors, not only adapt to evolving packaging trends but also proactively provide solutions that elevate the stability, reliability, and overall performance of integrated circuits. Their pivotal role propels the continuous advancement of IC packaging technology.
Where Does the Distinction Lie Between Package Substrate and PCB?
Package Substrates and Printed Circuit Boards (PCBs) play distinct roles in the electronic components landscape. PCBs, foundational in devices like motherboards, offer mechanical support and electrical pathways for components such as processors and memory modules. In contrast, Package Substrates are specialized bases crafted exclusively for semiconductor packaging.
Motherboard PCBs act as the central framework, providing essential connectivity and support for diverse electronic components. In contrast, the specialized role of Package Substrates lies in the intricate process of mounting and interconnecting integrated circuits (ICs) or chips. Their primary objective is to facilitate essential electrical connections between the chip and the broader system.
Substrate-like PCBs (SLP) and high-density interconnect (HDI) substrates, though related to PCBs, extend beyond semiconductor packaging. They are engineered to achieve higher circuit density and superior performance, sharing certain characteristics with Package Substrates.
The unique aspect of Package Substrates lies in their specialization for semiconductor packaging, incorporating advanced technologies like flip-chip packaging and wire bonding. This specialization ensures optimal electrical connectivity, efficient thermal management, and heightened signal integrity for integrated circuits. In the ever-evolving landscape of electronic devices, where compact size and enhanced performance are paramount, Package Substrates emerge as pivotal contributors to the progression of semiconductor technology.
What Are the Main Structures and Production Technologies of Package Substrate?
This section thoroughly examines the intricate structures and cutting-edge production technologies utilized by package substrate manufacturers. It offers a detailed insight into the composition of package substrates, emphasizing the advanced High-Density Interconnect (HDI) manufacturing technology and innovative semi-additive manufacturing methods.
The primary structures of package substrates involve layered configurations, employing materials like fiberglass-reinforced epoxy or sophisticated options such as silicon interposers. Each layer serves a specific function, ranging from providing structural support to facilitating electrical connections with the system’s circuit board.
Within the realm of production technologies, the focus is on the advancements in HDI manufacturing. This technology incorporates specialized laminates and thin films, allowing for a denser network of interconnections within the substrate. The section explores how HDI contributes to achieving more compact designs, finer lines, and increased connection density, meeting the growing demands for miniaturization in electronic devices.
Furthermore, the discussion extends to the innovative semi-additive manufacturing methods adopted by package substrate manufacturers. These methods entail a precision-oriented approach, selectively adding material to create intricate circuit patterns. This precision enhances the overall efficiency and performance of the package substrate, contributing significantly to the evolution of electronic systems.
By delving into these advanced production technologies, the section aims to provide a comprehensive understanding of how package substrate manufacturers leverage improved HDI manufacturing and innovative semi-additive methods. These technological strides play a crucial role in meeting the dynamic requirements of the electronics industry, supporting the development of high-performance and compact electronic devices.
FAQs
What sets packaging substrates apart from traditional PCBs, and how do they cater specifically to semiconductor packaging needs?
Packaging substrates are distinct boards tailored for mounting and connecting integrated circuits. Unlike traditional PCBs, they focus exclusively on semiconductor packaging rather than supporting a variety of electronic components.
How do packaging substrate manufacturers actively contribute to industry standards and ensure compatibility with a diverse array of electronic components?
A commitment to adhering to industry standards, coupled with collaborative efforts with stakeholders, ensures that packaging substrates not only comply but also seamlessly integrate and interact with a wide spectrum of electronic systems.
What strategies are employed to optimize costs in the manufacturing of packaging substrates without compromising on high-quality standards?
Cost optimization strategies center around the implementation of efficient processes, prudent material selection, and ongoing initiatives for improvement while upholding stringent quality standards.
What are the pivotal manufacturing processes integral to the production of packaging substrates?
Layer buildup, laser drilling, metallization, and the application of advanced packaging technologies like flip-chip bonding constitute fundamental processes essential for crafting high-quality packaging substrates.
How is the utmost reliability and quality ensured in packaging substrates, and what meticulous testing protocols are in place?
Adhering to stringent quality control measures and unwavering industry standards ensures the reliability and longevity of packaging substrates, with exhaustive testing protocols at the forefront.
Conclusion
To sum up, Package Substrate manufacturers wield a pivotal influence in the realm of electronic components, leaving an indelible and transformative mark on the broader electronics industry. Their pivotal position within this ecosystem is characterized by a multitude of facets, each marked by significant contributions that jointly drive forward technological progress.
Leading the charge is their pivotal role as catalysts for innovation, continuously at the forefront of pioneering and applying cutting-edge materials and manufacturing technologies. This unwavering dedication to innovation proves vital in addressing the dynamic demands of electronic devices, propelling advancements, and pushing the frontiers of technological possibilities.
Moreover, manufacturers of Package Substrates skillfully navigate the persistent trend towards miniaturization, facilitating the development of more compact and efficient electronic products while maintaining optimal performance.Their expertise in crafting compact and dependable substrates is foundational to realizing sleek and powerful devices.
Furthermore, these manufacturers serve as orchestrators of enhanced performance, meticulously optimizing signal transmission, power delivery, and heat dissipation. This meticulous attention to functionality ensures that electronic devices not only operate at peak efficiency but also contribute to the overall success and reliability of electronic systems.
Looking ahead, Package Substrate manufacturers shoulder the responsibility of steering continued technological progress. They stand at the forefront with the opportunity to lead the charge in developing substrates that align with emerging semiconductor technologies, thereby assuming a pivotal role in shaping innovative electronic systems. The establishment of collaborative partnerships with semiconductor companies and electronic system designers will be of utmost importance in navigating the intricate terrain of evolving technology.
In conclusion, the role of Package Substrate manufacturers extends far beyond mere component production; it stands as a cornerstone for progress in the electronics industry. As technology advances, these manufacturers stand poised at the forefront, embracing responsibility and seizing opportunities to shape a future characterized by ever-advancing electronic capabilities.