Packaging Substrate Seller. We offer BGA substrates from 2 layer to 20 layers.A Packaging Substrate refers to a fundamental component in electronic devices responsible for providing structural support and electrical connections for semiconductor chips (ICs) within the device. It serves as a crucial intermediary between the chip and the rest of the electronic system. The primary functions of a Packaging Substrate include facilitating electrical connections, aiding in heat dissipation, and providing mechanical support for the chip.
In simpler terms, it is a specialized board or material that houses and connects the chip, contributing to the overall functionality and reliability of the electronic device. The specific type and design of Packaging Substrate can vary, with different materials and configurations chosen based on the requirements of the device and the intended application.
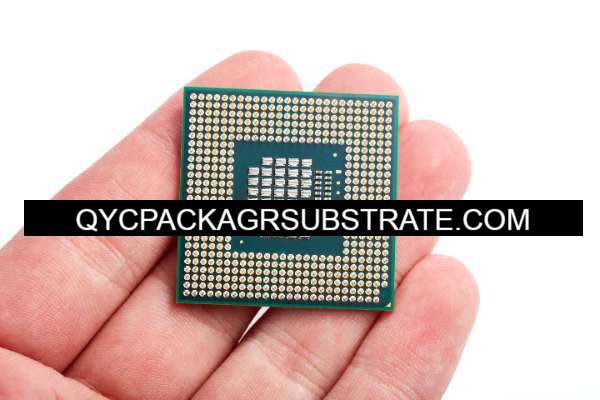
What Does “Packaging Substrate” Entail?
A “packaging substrate” is the foundational material or base layer utilized in the production of packaging.The packaging substrate serves as a foundational element in constructing the entire packaging structure, providing essential support to the product during storage, transportation, and handling. The careful selection of the packaging substrate is pivotal, as it directly impacts the overall performance, durability, and functionality of the packaging.
Key considerations for packaging substrates include:
-
Material Type:
-
- Paperboard/Cardboard: Commonly used for boxes, cartons, and folding cartons.
- Plastic: Includes materials like PET, PVC, HDPE, LDPE, and others, used for various flexible and rigid packaging applications.
- Metal: Often used for cans and other metal packaging.
-
Strength and Durability:
-
- The packaging substrate must possess sufficient strength to endure the weight and pressure exerted by the enclosed product.
- Durability is essential to prevent damage or deformation during handling and transportation.
-
Printability:
-
- The packaging substrate should be compatible with printing methods such as flexography, offset, or digital printing. This compatibility is essential to facilitate the incorporation of branding, product information, and decorative elements onto the packaging.
-
Barrier Properties:
-
- Depending on the product, packaging substrates may need specific barrier properties to protect against moisture, oxygen, light, or other environmental factors.
-
Environmental Impact:
-
- There is a growing emphasis on adopting environmentally friendly and sustainable packaging substrates to minimize the ecological footprint.
-
Cost Considerations:
-
- The cost of the substrate is a significant factor in packaging design. Balancing performance and cost is essential for cost-effective and efficient packaging solutions.
-
Compatibility with Printing and Finishing Processes:
-
- The packaging substrate should be adaptable to diverse printing and finishing processes, including varnishing, laminating, and embossing, to attain the intended visual and functional characteristics.
-
Regulatory Compliance:
- The choice of packaging substrate must comply with relevant regulations and standards, especially in industries with specific requirements such as food packaging.
The selection of a packaging substrate is a pivotal aspect of the overall packaging design process, impacting both the visual aesthetics and functional performance of the final product. Choosing the right substrate is contingent upon the unique needs of the packaged item, adherence to industry standards, and conscientious consideration of environmental factors.
What Functions Does It Encompass?
Eco-friendly packaging serves various functions aligned with environmental sustainability and responsible consumption. These functions include:
Reducing Environmental Impact: Eco-friendly packaging aims to minimize the negative effects of packaging on the environment. This entails the utilization of materials with a reduced carbon footprint, lower consumption of natural resources, and minimized pollution generation across their entire life cycle.
Promoting Recycling: Eco-friendly packaging materials are commonly crafted to be recyclable or composed of recycled content. Promoting recycling not only lessens the volume of waste destined for landfills but also preserves resources through the reuse of materials.
Biodegradability:Certain environmentally friendly packaging materials possess the quality of biodegradability, allowing them to naturally decompose into harmless substances over time. This feature contributes to reducing the persistence of packaging waste in the environment.
Sourcing from Renewable Resources: Utilizing materials derived from renewable resources, such as plant-based polymers or fibers, helps decrease dependence on finite resources and supports a more sustainable supply chain.
Energy Efficiency: Eco-friendly packaging may involve the use of manufacturing processes that consume less energy or emit fewer greenhouse gases, contributing to overall energy efficiency and reduced environmental impact.
Educating Consumers: Eco-friendly packaging often includes clear labeling and messaging to inform consumers about proper disposal methods, recycling instructions, and the environmental benefits of choosing sustainable packaging options.
Compliance with Regulations: As governments and regulatory bodies worldwide implement stricter environmental standards, eco-friendly packaging helps businesses stay compliant with these regulations and demonstrate a commitment to responsible business practices.
Building Brand Reputation: Adopting eco-friendly packaging can enhance a brand’s reputation by aligning with consumer preferences for sustainable products. It reflects a commitment to environmental responsibility and resonates with consumers who prioritize eco-conscious choices.
By encompassing these functions, eco-friendly packaging contributes to a more sustainable and responsible approach to packaging design and consumption.
How Do Various Types of Packaging Substrate Differ?
Various types of packaging substrates differ in terms of their material composition, properties, and applications. Here’s an overview of the distinctions between some common packaging substrates:
-
Paperboard/Cardboard:
-
- Material: Made from paper fibers.
- Properties: Sturdy, foldable, and printable.
- Applications: Commonly used for boxes, cartons, and folding cartons.
-
Corrugated Board:
-
- Material: Consists of a fluted corrugated sheet between two flat liner sheets, often made of paper.
- Properties: Provides strength, rigidity, and cushioning.
- Applications:Employed in the creation of shipping containers and robust packaging solutions.
-
Plastic:
-
- Material: Different varieties include polyethylene, polypropylene, and PET.
- Properties: Durable, lightweight, and may offer transparency.
- Applications: Versatile; used for bottles, containers, and flexible packaging.
-
Metal:
-
- Material: Tinplate or aluminum.
- Properties: Provides excellent protection against light, air, and moisture.
- Applications: Commonly used for canned goods and certain premium packaging.
-
Glass:
- Material: Primarily silica, soda ash, and limestone.
- Properties: Heavy, rigid, and impermeable to gases.
- Applications:Employed in specific food and beverage packaging, particularly for items that are vulnerable to the effects of light and air.
The selection of packaging substrate is influenced by various factors, including product characteristics, desired protection levels, aesthetics, and environmental considerations. The continuous advancement of sustainable packaging practices has spurred the creation of eco-friendly variants of these substrates, prioritizing features such as recyclability, biodegradability, and the incorporation of renewable resources.
How Is Packaging Substrate Connected to IC Packaging?
Packaging substrate and IC (Integrated Circuit) packaging are related in the context of semiconductor technology and electronics manufacturing. In IC packaging, the packaging substrate plays a critical role in providing a physical and electrical connection for the integrated circuit.
Here’s how packaging substrate is connected to IC packaging:
-
Physical Support:
-
- The IC itself is a small semiconductor device that contains numerous electronic components on a silicon wafer. The packaging substrate serves as a structural foundation, providing support and protection for the delicate IC.
-
Electrical Connections:
-
- The packaging substrate hosts the electrical connections between the IC and the external environment. Tiny wires or metal traces on the substrate connect the various pins or pads on the IC to the external leads or connectors.
-
Heat Dissipation:
-
- ICs generate heat during operation, and efficient heat dissipation is crucial for their proper functioning. The packaging substrate often incorporates materials and designs that facilitate the transfer of heat away from the IC, helping to maintain optimal operating temperatures.
-
Signal Routing:
-
- The packaging substrate is responsible for routing signals between different parts of the IC and connecting them to the external world. It ensures that electrical signals can flow between the IC and other components within a larger electronic system.
-
Materials and Technologies:
-
- The materials used in packaging substrates for ICs can vary and may include ceramics, organic substrates (such as FR-4), and advanced materials like silicon interposers. The choice of materials depends on factors like electrical performance, thermal properties, and cost considerations.
-
Advanced Packaging Techniques:
- As technology evolves, advanced packaging techniques like 3D packaging and System-in-Package (SiP) have emerged. These approaches often involve sophisticated packaging substrates to enable the integration of multiple components within a compact space.
In summary, the packaging substrate in IC packaging is the interface between the internal components of the integrated circuit and the external environment, providing physical support, electrical connections, and contributing to the overall functionality and performance of electronic devices.
How Does Packaging Substrate Differ from PCB?
Packaging substrate and PCB (Printed Circuit Board) are related elements in the field of electronics, but they serve different purposes and have distinct characteristics. Here are the key differences between packaging substrate and PCB:
- Function:
- Packaging Substrate: It primarily provides physical and electrical support for integrated circuits (ICs) within a packaged device. It facilitates the interconnection of the IC to the external world and contributes to heat dissipation and signal routing.
- PCB: It is a board that supports and connects various electronic components in a broader electronic system. PCBs serve as the foundation for mounting and interconnecting components like resistors, capacitors, and ICs.
- Component Integration:
- Packaging Substrate: It is specifically designed for the integration and packaging of ICs. It often includes features like pads, traces, and vias that are optimized for the specific requirements of the packaged IC.
- PCB: It accommodates a variety of electronic components beyond ICs. PCBs host a range of components and connectors, allowing for the assembly of complete electronic circuits.
- Size and Form Factor:
- Packaging Substrate: It is typically smaller in size and tailored to the dimensions of the specific IC package. The form factor is optimized for the individual IC or a group of closely related ICs.
- PCB:The size and configuration of PCBs can vary significantly, influenced by the intricacy of the electronic system they underpin. These boards are tailor-made to seamlessly integrate into specific electronic devices or systems, ranging from computers and smartphones to industrial equipment.
- Materials:
- Packaging Substrate: Materials like ceramics, organic substrates (such as FR-4), and advanced materials may be used, depending on the requirements of the IC packaging.
- PCB: Common materials include fiberglass-reinforced epoxy (FR-4), metal core (MCPCB), or other advanced materials. PCB materials are selected based on factors like electrical performance, thermal characteristics, and cost.
- Application Focus:
- Packaging Substrate: It is specifically designed for the packaging and integration of ICs into electronic devices. The focus is on the micro-level connections and features necessary for the functioning of the IC.
- PCB: It is designed for broader electronic system integration, connecting various components to create functional circuits at the macro level.
In summary, while both packaging substrates and PCBs play crucial roles in electronics, packaging substrates are specialized components within IC packaging, whereas PCBs provide a platform for the assembly and interconnection of a variety of electronic components in a larger electronic system.
What Structures and Production Technologies Define Packaging Substrate?
The structures and production technologies that define packaging substrate vary based on the type of substrate and the specific requirements of the packaging. Here are some common structures and production technologies associated with packaging substrates:
-
Composition of Materials:
-
- Packaging substrates incorporate an extensive array of materials, ranging from paper, cardboard, plastics, metals, to glass. Material selection is contingent upon variables such as the specific attributes of the packaged product, the required level of protection, and environmental considerations.
-
Layered Structures:
-
- Certain packaging substrates, such as corrugated board, have layered structures. For example, corrugated board consists of a fluted corrugated sheet sandwiched between two flat liner sheets. This structure enhances strength and rigidity.
-
Printing and Coating:
-
- Printing and coating technologies are employed to enhance the visual appeal and functionality of packaging substrates. Graphics, branding information, and product details can be printed directly on the substrate. Coatings may include protective layers for moisture resistance or special finishes for aesthetic purposes.
-
Die-Cutting and Folding:
-
- Die-cutting is a production technique that involves cutting the packaging substrate into specific shapes or patterns. Folding and scoring are used to create the desired form of packaging, such as boxes and cartons.
-
Plastic Molding:
-
- For packaging substrates made of plastics, various molding processes such as injection molding, thermoforming, and blow molding may be employed. These processes allow the production of plastic containers, bottles, and other packaging items with intricate shapes.
-
Lamination:
-
- Lamination involves bonding multiple layers of materials together to enhance strength, barrier properties, or visual appeal. This is commonly used in the production of flexible packaging materials.
-
Metal Forming:
-
- Packaging substrates made of metal, such as tinplate or aluminum, undergo metal forming processes like stamping or deep drawing to create cans, containers, or other metal packaging.
-
Sustainable and Eco-Friendly Technologies:
-
- The rising commitment to sustainability is driving a greater emphasis on environmentally friendly production technologies. This involves the adoption of recycled materials, water-based inks, and energy-efficient manufacturing processes, all aimed at minimizing the environmental footprint of the production process.
-
Advanced Packaging Technologies:
-
- In the realm of IC packaging, advanced technologies such as 3D packaging, wafer-level packaging, and flip-chip packaging involve sophisticated processes for creating compact and high-performance packaging substrates.
-
Quality Control and Inspection:
- Modern production technologies often include quality control and inspection processes to ensure that the packaging substrates meet specified standards. This may involve automated inspection systems and quality assurance measures throughout the manufacturing process.
The specific structures and production technologies employed depend on the type of packaging substrate and the intended application, whether it’s for consumer goods, electronics, or industrial products. Advances in technology continue to drive innovation in packaging substrate production, with an increasing emphasis on efficiency, sustainability, and customization.
FAQs: Addressing Common Questions
Frequently Asked Questions (FAQs): Providing Answers to Common Inquiries
What is a packaging substrate?
A packaging substrate plays a fundamental role in the creation of packaging, providing crucial structural support for various formats such as boxes and cartons. Crafted from a range of materials, including paper, cardboard, plastics, metals, and glass, it serves as the foundational element in packaging production.
How does packaging substrate differ from PCB?
While both serve roles in electronics, packaging substrate is specialized for the integration of integrated circuits (ICs), offering physical and electrical support. PCBs, or Printed Circuit Boards, are broader platforms that support and interconnect various electronic components in a larger electronic system.
What are the key functions of eco-friendly packaging substrates?
Eco-friendly packaging substrates aim to minimize their environmental footprint by utilizing materials that can be recycled, are biodegradable, or sourced from renewable origins. These substrates actively contribute to reducing waste, promoting conscientious consumption, and tackling concerns related to pollution, fostering an overall commitment to environmental sustainability.
How do packaging substrates relate to IC packaging?
Packaging substrates are integral in IC packaging, providing physical support, electrical connections, and heat dissipation for integrated circuits. They facilitate the integration of ICs into electronic devices and systems.
What factors influence the choice of packaging substrate?
The selection of packaging substrate is guided by various factors, including the product’s characteristics, the level of protection required, aesthetic preferences, and environmental considerations. Ongoing advancements in sustainable practices have given rise to eco-friendly substrates, placing emphasis on features like recyclability and the utilization of renewable resources.
What production technologies define packaging substrate manufacturing?
Packaging substrates undergo various production technologies, including printing, coating, die-cutting, molding, lamination, metal forming, and advanced techniques for IC packaging. Quality control and inspection processes are often incorporated to ensure adherence to standards.
How do packaging substrates contribute to sustainability?
Packaging substrates contribute to sustainability by adopting eco-friendly materials, promoting recyclability, and incorporating sustainable production practices. This helps minimize environmental impact and aligns with global efforts to address environmental concerns.
Why is the composition of packaging substrates important?
The composition of packaging substrates is crucial as it determines the substrate’s properties, including strength, flexibility, and environmental impact. The choice of materials directly impacts the overall functionality, recyclability, and sustainability of the packaging.
In Conclusion
In conclusion, packaging substrates are integral components in the world of packaging, offering essential structural support and contributing to the functionality and aesthetics of various packaging formats. The choice of materials, production technologies, and the increasing emphasis on sustainability collectively shape the landscape of packaging substrates. As the industry continues to evolve, the pursuit of eco-friendly alternatives and advanced production methods underscores a commitment to minimizing environmental impact and meeting the diverse needs of consumers and industries alike.