Different types of packaging substrate suppliers, Advanced technology, the use of Sap and Msap production process, stable quality, fast delivery. we produce any types FC BGA substrates.
Brief Overview of IC Packaging Substrates
Packaging substrates, serving as the essential infrastructure for integrated circuits (ICs), assume a critical role in safeguarding the functionality, reliability, and overarching performance of semiconductor devices. These substrates act as the tangible base on which semiconductor components find their placement, establish connections, and receive protection. From traditional FR-4 to cutting-edge 3D IC packaging materials, the diversity in substrate types reflects the evolving landscape of electronics manufacturing.
In this exploration, we’ll delve into the diverse materials that constitute IC packaging substrates, shedding light on their unique properties and applications. From the conventional to the avant-garde, understanding these materials is crucial for both engineers and SEO specialists, influencing not only the technical aspects of semiconductor design but also optimizing online visibility and accessibility.
Importance of Substrate Materials in Semiconductor Packaging
The choice of substrate materials is more than a technical decision; it’s a strategic one that profoundly impacts the performance, cost, and market positioning of semiconductor devices. The right substrate can enhance thermal conductivity, reduce signal interference, and accommodate the miniaturization demands of modern electronics. This engineering precision, coupled with a keen awareness of SEO dynamics, ensures that the description of these substrates resonates with both technical audiences and online search algorithms.
As we navigate through the intricacies of FR-4, ceramics, and emerging technologies, keep in mind the delicate balance between engineering excellence and SEO relevance. This synthesis not only optimizes the understanding of IC packaging substrates for professionals but also enhances the discoverability of this critical information in the vast landscape of online searches.
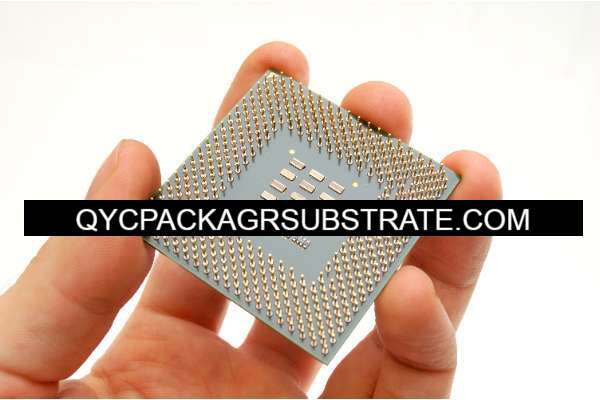
Common Substrate Materials
FR-4 (Flame Retardant 4)
Composition and Characteristics
- Composition: FR-4 is a composite material composed of layers of woven fiberglass cloth impregnated with epoxy resin. The “4” in FR-4 indicates the material’s flame-retardant properties.
- Characteristics: FR-4 is known for its excellent electrical insulation, high strength, and flame resistance. It is a cost-effective option for various applications.
Common Applications in IC Packaging
- Printed Circuit Boards (PCBs): FR-4 is widely used as the substrate material for PCBs due to its electrical insulation properties.
- Lead Frames: FR-4 is employed in the fabrication of lead frames, providing structural support and electrical connectivity.
- Consumer Electronics: Its affordability and versatility make FR-4 a popular choice in consumer electronic devices such as smartphones and tablets.
Ceramic Substrates
Types of Ceramics Used
- Alumina (Al2O3): Alumina ceramics are common due to their high thermal conductivity and electrical insulation properties. They are suitable for various IC packaging applications.
- Aluminum Nitride (AlN): Aluminum nitride is the favored choice in scenarios demanding superior thermal management, rendering it well-suited for high-power IC applications.
Advantages and Disadvantages
- Advantages:
- Thermal Performance: Ceramics provide exceptional thermal conductivity, a pivotal attribute essential for effectively managing heat dissipation in high-performance integrated circuits.
- Mechanical Stability: Ceramics provide robust mechanical support, enhancing the durability of packaged ICs.
- Disadvantages:
- Brittleness: Ceramics can be brittle, requiring careful handling during manufacturing.
- Cost: Ceramic substrates can be more expensive compared to FR-4, impacting overall production costs.
Applications in High-Performance ICs
- Power Modules: The utilization of ceramics in power modules is favored due to their capacity to efficiently manage and dissipate high thermal loads.
- Radio Frequency (RF) Devices: Ceramics exhibit high-frequency characteristics that render them well-suited for applications in radio frequency (RF), particularly in devices related to wireless communication.
By understanding the composition, applications, and pros/cons of FR-4 and ceramic substrates, manufacturers can make informed decisions based on cost, performance, and specific use cases. These materials play a crucial role in the diverse landscape of IC packaging.
Advanced Substrate Materials
High-Temperature Co-Fired Ceramic (HTCC)
Features and Benefits
- High Thermal Stability: HTCC substrates excel in maintaining structural integrity at elevated temperatures, ensuring reliability in demanding environments.
- Low Dielectric Loss: This property enhances signal integrity and reduces energy loss in high-frequency applications.
- Excellent Mechanical Strength: HTCC’s robustness makes it suitable for harsh conditions, providing durability in aerospace and automotive settings.
- Hermetic Packaging Capability: HTCC’s composition allows for effective hermetic sealing, crucial in applications requiring protection against environmental factors.
Applications in Aerospace and Automotive Industries
- Sensor Packaging: HTCC’s ability to withstand extreme temperatures makes it ideal for encapsulating sensors in aerospace and automotive systems.
- Microelectronics in Engines: Due to its high thermal stability, HTCC is used in packaging microelectronics within engine components, ensuring reliability under intense heat.
Low-Temperature Co-Fired Ceramic (LTCC)
Key Properties
- Multilayer Integration: LTCC supports the integration of multiple layers, facilitating the design of compact and complex electronic circuits.
- Dielectric Constant Control: This property allows for fine-tuning the dielectric constant, making LTCC suitable for RF and microwave applications.
- Low Signal Loss: LTCC’s low loss characteristics are crucial in maintaining signal integrity, especially in high-frequency communication devices.
Applications in RF and Microwave Devices
- Antenna Modules: LTCC’s dielectric properties make it an ideal substrate for compact antenna modules, enabling efficient signal transmission.
- RF Filters: LTCC’s low signal loss makes it well-suited for manufacturing RF filters, ensuring minimal signal degradation in communication devices.
By delving into the features and applications of HTCC and LTCC substrates, we gain a deeper understanding of their contributions to high-performance electronics in aerospace, automotive, and RF/microwave applications. These advanced substrate materials play a pivotal role in pushing the boundaries of electronic packaging, meeting the stringent requirements of modern technology.
Organic Substrates
Organic substrates play a crucial role in modern IC packaging, offering versatility and adaptability to various design needs. This section delves into two innovative aspects of organic substrates: Build-up Layers (BUL) and Flexible Substrates.
Build-up Layers (BUL)
Explanation of Build-up Layer Technology
Build-up layers (BUL) represent a technological leap in IC packaging. Unlike traditional substrates, BUL involves stacking multiple layers of thin-film materials atop the core layer. This enables the creation of intricate, three-dimensional circuit structures.
Benefits in Complex IC Designs
BUL technology brings several advantages, especially in addressing the demands of complex IC designs.
Enhanced Routing Density: With the ability to stack layers, BUL facilitates a higher routing density, allowing for more intricate and compact circuit layouts.
Improved Signal Integrity: Reduced signal interference and crosstalk contribute to enhanced signal integrity, critical for high-performance applications.
Miniaturization: The compact nature of BUL supports the trend toward smaller and more portable electronic devices.
Keywords: Routing density, signal integrity, miniaturization, complex IC designs.
Flexible Substrates
Advantages for Flexible Electronics
Flexible substrates have gained prominence in the era of flexible electronics, offering a paradigm shift from rigid structures. Key advantages include:
Bendability and Flexibility: Flexible substrates enable the creation of bendable and foldable electronic devices, catering to the growing demand for flexible form factors.
Weight Reduction: The use of lightweight materials contributes to overall weight reduction in electronic devices, crucial for applications like wearable technology.
Durability: Flexible substrates often exhibit robustness against mechanical stress, contributing to the durability of flexible electronic products.
Applications in Wearables and Foldable Devices
The adaptability of flexible substrates finds practical applications in emerging electronic trends.
Wearable Technology: Flexible substrates enable the integration of electronics into clothing, accessories, and health monitoring devices, enhancing user comfort.
Foldable Devices: In the realm of smartphones and tablets, flexible substrates facilitate the development of foldable screens, offering a blend of portability and expansive display options.
Incorporating build-up layers and flexible substrates into IC packaging not only fosters innovation in design but also aligns with the industry’s pursuit of miniaturization, portability, and enhanced functionality in electronic devices.
Emerging Trends in Substrate Technology
Embedded Substrates
- Overview of Embedded Substrate Technology
– Brief Explanation: Embedded substrate technology involves integrating components within the substrate, enhancing the overall compactness of the integrated circuit (IC).
– Material Integration: Various materials like polymers or ceramics are utilized for embedding, offering a seamless integration of components.
- Applications in Miniaturization and Performance Enhancement
– Miniaturization Impact: Embedded substrates play a pivotal role in reducing the physical size of ICs, critical for applications in compact devices.
– Performance Enhancement: Enhanced signal integrity and reduced parasitic effects contribute to improved performance, making embedded substrates ideal for high-density and high-speed applications.
3D IC Packaging
- Explanation of Three-Dimensional IC Packaging
– Vertical Integration: Three-dimensional IC packaging involves stacking multiple IC layers vertically, optimizing space utilization.
– Interconnects: Advanced through-silicon via (TSV) technology facilitates vertical connections between stacked layers.
- Advantages in Improving Power Efficiency and Reducing Footprint
– Power Efficiency: Shorter interconnects in 3D ICs lead to reduced resistance and improved power efficiency, critical for energy-sensitive applications.
– Footprint Reduction: Stacking components vertically reduces the overall footprint, addressing space constraints in modern electronic devices.
Emerging Trends Insights:
SEO Integration: The adoption of embedded substrates and 3D IC packaging aligns with the industry’s pursuit of smaller, efficient, and high-performance electronics. This technological evolution not only caters to engineering demands but also aligns with SEO priorities, emphasizing innovation and relevance.
User Experience Considerations: As devices become more compact and powerful, users benefit from sleek designs and improved functionality. Optimizing content to reflect these advancements ensures that users are informed about the latest in IC packaging technology, enhancing their overall experience.