Radio Frequency & Microwave PCBs for Satellites Manufacturer
Radio Frequency & Microwave PCBs for Satellites Manufacturer,Radio Frequency (RF) & Microwave PCBs for satellites are specialized circuit boards designed to facilitate communication between satellites and ground stations. Utilizing high-frequency materials like PTFE-based substrates, these PCBs ensure minimal signal loss and reliable data transmission in the RF and microwave spectrum. Precision manufacturing techniques and stringent quality control measures are employed to meet the demanding requirements of space environments. RF & Microwave PCBs play a vital role in satellite applications, enabling functions such as weather monitoring, navigation, telecommunications, and scientific research, contributing to advancements in satellite technology and exploration.
What is a Radio Frequency & Microwave PCB for Satellites?
A Radio Frequency & Microwave PCB (Printed Circuit Board) for satellites is a specialized circuit board designed to operate at the high-frequency spectrum of radio waves and microwaves, typically ranging from a few MHz to several G Hz. These PCBs are crucial for satellite communications because they handle the transmission and reception of radio signals that facilitate data exchange between the satellite and ground stations.
The design of RF & Microwave PCBs involves the use of specific materials and techniques to minimize signal loss and ensure high signal integrity. Common materials include high-frequency laminates like PTFE (Polytetrafluoroethylene), often combined with ceramic fillers to enhance their electrical properties. These materials are chosen for their low dielectric losses and stable electrical characteristics at high frequencies.
Moreover, RF & Microwave PCBs in satellites must be engineered to withstand the harsh conditions of space, including extreme temperatures and radiation. Their layout is meticulously planned to reduce noise and crosstalk, critical for maintaining the clarity and reliability of the signal at microwave frequencies. Features such as controlled impedance, careful routing of signal paths, and shielding techniques are often employed to optimize performance.
The use of these advanced PCBs in satellites is vital for various functions, including communication, earth observation, navigation, and scientific research, making them indispensable in the growing field of satellite technology.
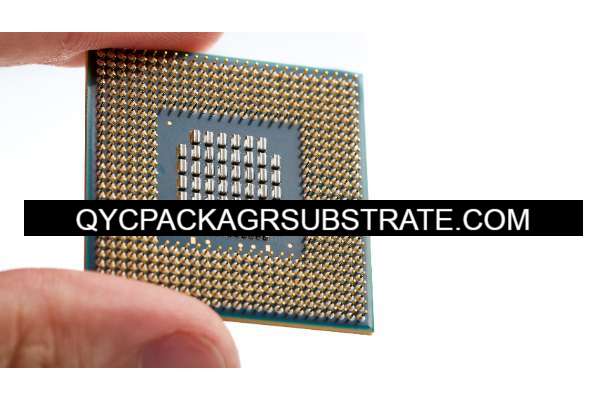
Radio Frequency & Microwave PCBs for Satellites Manufacturer
What are the Design Guidelines for Radio Frequency & Microwave PCBs for Satellites?
Designing Radio Frequency (RF) and Microwave PCBs for satellites requires careful consideration of several key guidelines to ensure optimal performance and reliability in the harsh space environment. Here are some essential design guidelines:
- Material Selection: Choose high-frequency laminate materials with low dielectric constants and low loss tangents to minimize signal loss. Common materials include PTFE-based substrates like Rogers RO4000 series or similar high-performance laminates.
- Controlled Impedance: Maintain controlled impedance throughout the transmission lines to minimize signal reflections and ensure signal integrity. Use impedance calculators and controlled impedance traces based on the chosen substrate material and layer stack-up.
- Grounding and Shielding: Implement proper grounding techniques to minimize ground loops and reduce electromagnetic interference (EMI). Use solid ground planes and partition sensitive RF circuits from digital or power circuits. Employ shielding techniques such as grounded metal enclosures or copper pours to contain electromagnetic radiation.
- Component Placement and Routing: Carefully place RF components and transmission lines to minimize parasitic effects and ensure signal integrity. Keep trace lengths short and use straight, wide traces for high-frequency signals. Maintain proper spacing between RF components to reduce coupling and crosstalk.
- Via Design: Optimize via structures to minimize impedance mismatch and signal distortion. Use via stubs or back-drilling techniques to remove excess via lengths that could cause signal reflections.
- Temperature Considerations: Account for temperature variations in space by selecting PCB materials with stable electrical properties over a wide temperature range. Consider thermal management techniques to dissipate heat generated by RF components.
- Radiation Hardening: Design PCBs to withstand the effects of radiation in space, which can cause degradation or failure of electronic components. Use radiation-hardened materials and design techniques such as redundancy, shielding, and error-correction coding to mitigate radiation effects.
- Testing and Validation: Perform thorough testing and validation of RF and microwave circuits using simulation tools, such as electromagnetic field solvers and circuit simulators. Conduct rigorous environmental testing to ensure PCB reliability under extreme conditions.
By adhering to these design guidelines, engineers can develop RF and Microwave PCBs for satellites that meet stringent performance requirements and operate reliably in the challenging space environment.
What is the Fabrication Process for Radio Frequency & Microwave PCBs for Satellites?
The fabrication process for Radio Frequency (RF) and Microwave PCBs for satellites involves several specialized steps to ensure the precise construction of high-frequency circuits capable of withstanding the rigors of space. Here’s a general overview of the fabrication process:
- Material Selection:Choose high-frequency laminate materials with low dielectric constants and low loss tangents suitable for RF and microwave applications. Common materials include PTFE-based substrates like Rogers RO4000 series or similar high-performance laminates.
- Design Preparation:Develop a detailed PCB design layout using specialized RF and microwave design software. Ensure that the layout adheres to the design guidelines for controlled impedance, grounding, shielding, and component placement.
- Preparation of Substrate: Cut the laminate material to the required dimensions based on the PCB design. Clean the substrate surface thoroughly to remove any contaminants that could affect adhesion or electrical properties.
- Copper Cladding: Apply a thin layer of copper foil to both sides of the substrate using a lamination process. The copper foil thickness should be chosen according to the design specifications for signal conductors and ground planes.
- Photoresist Application: Coat the copper-clad substrate with a layer of photoresist material using a spray or roller coating process. The photoresist acts as a protective layer for the subsequent etching process.
- Exposure and Development: Use a UV light source to expose the photoresist layer through a photomask, which contains the PCB pattern. Develop the exposed photoresist to reveal the underlying copper traces and pads.
- Etching: Immerse the substrate in an etchant solution, typically a chemical solution containing ferric chloride or ammonium persulfate, to remove the exposed copper and define the PCB traces. Monitor the etching process carefully to ensure precise control of trace widths and depths.
- Photoresist Stripping: Remove the remaining photoresist from the substrate using a stripping solution or mechanical methods, leaving behind the etched copper traces and pads.
- Drilling: Drill holes for through-hole components and vias using a precision drilling machine. Ensure accurate hole placement and size according to the PCB design specifications.
- Plating and Surface Finishing: Plate the drilled holes with conductive material, such as electroless copper or electrolytic copper, to provide electrical connectivity between layers. Apply surface finishes, such as immersion gold or immersion silver, to protect the copper traces and ensure solderability.
- Final Inspection: Perform visual inspection and electrical testing to verify the integrity of the fabricated PCB. Check for any defects, such as missing traces, shorts, or open circuits, and rectify them if necessary.
- Packaging and Assembly: Package the fabricated PCBs into protective enclosures suitable for space applications. Assemble the PCBs with RF components and connectors using specialized techniques to maintain signal integrity and reliability.
By following these fabrication steps with precision and attention to detail, engineers can produce RF and Microwave PCBs for satellites that meet the stringent performance and reliability requirements of space missions.
How Do You Manufacture a Radio Frequency & Microwave PCB for Satellites?
Manufacturing a Radio Frequency (RF) and Microwave PCB for satellites involves a series of specialized processes to ensure the precise construction of high-frequency circuits capable of operating in the demanding space environment. Here’s a step-by-step overview of the manufacturing process:
- Design Preparation: Develop a detailed PCB design layout using RF and microwave design software. Ensure that the design adheres to the specific requirements for controlled impedance, signal integrity, and thermal management.
- Material Selection: Choose high-frequency laminate materials suitable for RF and microwave applications, such as PTFE-based substrates like Rogers RO4000 series. Select materials with low dielectric constants and low loss tangents to minimize signal loss.
- Panelization: Arrange individual PCB designs into panels for efficient manufacturing. Optimize panel layouts to maximize material utilization and facilitate handling during the manufacturing process.
- Preparation of Substrate: Cut the laminate material into panel-sized sheets using precision cutting equipment. Clean the substrate surface thoroughly to remove any contaminants that could affect adhesion or electrical properties.
- Copper Cladding: Apply a thin layer of copper foil to both sides of the substrate using a lamination process. The copper foil thickness should be chosen according to the design requirements for signal conductors and ground planes.
- Photoresist Application: Coat the copper-clad substrate with a layer of photoresist material using spray or roller coating equipment. The photoresist acts as a protective layer for the subsequent etching process.
- Exposure and Development: Use a UV light source to expose the photoresist layer through a photomask, which contains the PCB pattern. Develop the exposed photoresist to reveal the underlying copper traces and pads.
- Etching: Immerse the substrate in an etchant solution, such as ferric chloride or ammonium persulfate, to remove the exposed copper and define the PCB traces. Monitor the etching process carefully to ensure precise control of trace widths and depths.
- Photoresist Stripping: Remove the remaining photoresist from the substrate using stripping solution or mechanical methods, leaving behind the etched copper traces and pads.
- Drilling: Drill holes for through-hole components and vias using precision drilling equipment. Ensure accurate hole placement and size according to the PCB design specifications.
- Plating and Surface Finishing: Plate the drilled holes with conductive material, such as electroless copper or electrolytic copper, to provide electrical connectivity between layers. Apply surface finishes, such as immersion gold or immersion silver, to protect the copper traces and ensure solderability.
- Final Inspection: Perform visual inspection and electrical testing to verify the integrity of the manufactured PCBs. Check for any defects, such as missing traces, shorts, or open circuits, and rectify them if necessary.
- Packaging and Assembly: Package the manufactured PCBs into protective enclosures suitable for space applications. Assemble the PCBs with RF components and connectors using specialized techniques to maintain signal integrity and reliability.
By following these manufacturing processes with precision and attention to detail, manufacturers can produce RF and Microwave PCBs for satellites that meet the stringent performance and reliability requirements of space missions.
How Much Should a Radio Frequency & Microwave PCB for Satellites Cost?
The cost of manufacturing a Radio Frequency (RF) and Microwave PCB for satellites can vary significantly depending on several factors, including the complexity of the design, the choice of materials, the manufacturing processes involved, and the required quantity. Here are some factors that can influence the cost:
- Design Complexity: The complexity of the RF and microwave circuitry, including the number of layers, the density of components, and the level of signal integrity required, can impact the cost of manufacturing. More intricate designs may require additional fabrication steps and higher precision, leading to increased costs.
- Materials: The choice of materials for the PCB substrate, copper cladding, and surface finishes can affect the overall cost. High-performance materials with low dielectric constants and low loss tangents, such as PTFE-based laminates, tend to be more expensive than standard FR-4 materials.
- Manufacturing Processes: Specialized manufacturing processes, such as controlled impedance routing, fine-pitch drilling, and surface finishing techniques, can add to the manufacturing cost. Complex processes that require advanced equipment and expertise may result in higher production expenses.
- Volume: The quantity of PCBs ordered can impact the unit cost. Generally, larger production volumes allow for economies of scale, reducing the cost per unit. However, prototypes or low-volume production runs may incur higher costs due to setup fees and lower efficiency.
- Quality Standards: Meeting stringent quality standards and certification requirements, such as IPC standards or space-grade specifications, may entail additional testing and documentation, contributing to the overall cost.
- Supplier Selection: The choice of PCB manufacturer or supplier can also influence the cost. Different suppliers may offer varying pricing structures, lead times, and levels of service, so it’s essential to consider these factors when selecting a supplier.
Given these factors, it’s challenging to provide a specific cost estimate without knowing the details of the RF and Microwave PCB design, materials, and manufacturing requirements. Typically, RF and Microwave PCBs for satellite applications are considered specialized and may incur higher costs compared to standard PCBs due to their unique design and performance characteristics. It’s advisable to consult with PCB manufacturers or suppliers to obtain accurate cost estimates based on the specific project requirements.
What is PCB Base Material?
The PCB (Printed Circuit Board) base material is the substrate upon which electronic components are mounted and interconnected to create a functioning circuit. It provides mechanical support and electrical insulation for the circuitry. The choice of base material significantly impacts the performance, reliability, and cost of the PCB.
Common PCB base materials include:
- FR-4 (Flame Retardant 4): FR-4 is the most widely used base material for PCBs due to its versatility, affordability, and ease of manufacturing. It consists of a woven fiberglass cloth impregnated with an epoxy resin binder. FR-4 is known for its good mechanical strength, electrical insulation properties, and flame resistance.
- FR-4 High-Tg (High Glass Transition Temperature): High-Tg FR-4 is a variant of FR-4 with a higher glass transition temperature, making it more suitable for applications requiring elevated temperature operation or lead-free soldering processes.
- Polyimide (PI): Polyimide is a high-performance base material known for its excellent thermal stability, chemical resistance, and flexibility. It is commonly used in flexible PCBs (FPCBs) and applications where high-temperature operation or harsh environments are encountered.
- PTFE (Polytetrafluoroethylene):PTFE-based materials, such as Rogers RO4000 series, are used in high-frequency and microwave applications due to their low dielectric constants and low loss tangents. PTFE materials offer superior electrical properties at high frequencies but tend to be more expensive than FR-4.
- Metal Core: Metal core PCBs feature a layer of metal (usually aluminum or copper) as the base material instead of fiberglass. Metal core PCBs offer enhanced thermal conductivity and heat dissipation, making them suitable for high-power LED lighting, power electronics, and automotive applications.
- Ceramic: Ceramic-based PCBs are used in specialized applications requiring high thermal conductivity, low dielectric loss, and excellent stability over a wide temperature range. Ceramic materials offer superior performance in high-power RF, microwave, and aerospace applications.
The selection of PCB base material depends on various factors, including the application requirements, operating environment, electrical performance, thermal management needs, and cost considerations. Designers must carefully evaluate these factors to choose the most suitable base material for their PCB design.
Which Company Makes Radio Frequency & Microwave PCBs for Satellites?
There are many companies that specialize in manufacturing Radio Frequency (RF) and Microwave PCBs for satellites. Some of these companies include Rogers Corporation, DuPont, Taconic Advanced Dielectric Division, Isola Group, and others. These companies have extensive experience and expertise in the RF and microwave PCB field, providing high-performance solutions for satellite applications.
As a PCB manufacturing company, we can also produce RF and Microwave PCBs to meet the needs of satellite applications. Our company has advanced manufacturing equipment and technology, as well as an experienced engineering team, to provide customized RF and Microwave PCB solutions for our customers.
We strictly follow industry standards and quality management systems in our manufacturing process to ensure the performance and reliability of our products. We use high-performance PCB substrates such as PTFE (Polytetrafluoroethylene) with low dielectric constant and low loss tangent, suitable for high-frequency and microwave applications. We also offer high-precision controlled impedance design and manufacturing to ensure the accuracy and stability of signal transmission.
During the manufacturing process, we implement strict quality control procedures, conducting thorough inspections and testing for each process to ensure that our products meet the specifications and performance standards required by our customers. We also provide customized surface treatments such as immersion gold, immersion silver, etc., to meet the requirements of different application scenarios.
Our goal is to provide customers with high-quality, reliable RF and Microwave PCB products to help them achieve success in satellite applications. We are committed to establishing long-term partnerships with our customers and contributing to the advancement and application of satellite technology.
What are the 7 Qualities of Good Customer Service?
Good customer service is essential for building strong relationships with customers and fostering loyalty. Here are seven qualities that define good customer service:
- Responsiveness:Good customer service involves being prompt and responsive to customer inquiries, requests, and concerns. Customers appreciate timely assistance and expect their needs to be addressed promptly.
- Empathy:Empathy is the ability to understand and share the feelings of customers. Good customer service representatives listen actively, show genuine concern for customers’ issues, and strive to put themselves in the customer’s shoes to provide personalized assistance.
- Professionalism: Good customer service is characterized by professionalism in communication and behavior. Customer service representatives should maintain a courteous and respectful attitude, communicate clearly and effectively, and adhere to company policies and procedures.
- Knowledgeability:Good customer service requires having a thorough understanding of the products or services offered by the company. Customer service representatives should be knowledgeable about the features, benefits, and usage of products/services to provide accurate information and assistance to customers.
- Problem-solving skills: Good customer service involves the ability to identify and resolve customer issues effectively. Customer service representatives should be proactive in addressing customer concerns, offering viable solutions, and following up to ensure customer satisfaction.
- Adaptability: Good customer service requires adaptability to different customer personalities, preferences, and situations. Customer service representatives should be flexible and adaptable in their approach, tailoring their communication style and problem-solving strategies to meet the needs of individual customers.
- Consistency: Consistency is key to providing good customer service. Customers expect a consistent level of service across all interactions with the company, whether in-person, over the phone, or online. Consistency in communication, response times, and problem resolution builds trust and confidence in the company.
By embodying these qualities, companies can deliver exceptional customer service experiences that leave a positive impression on customers and contribute to long-term success.
FAQs
What are RF & Microwave PCBs?
RF & Microwave PCBs are specialized circuit boards designed to operate at high frequencies, typically in the RF and microwave spectrum. They are used in applications such as satellite communication systems, radar systems, wireless networks, and more.
Why are RF & Microwave PCBs important for satellites?
RF & Microwave PCBs are crucial for satellite communication systems, allowing data transmission and reception between the satellite and ground stations. These PCBs enable reliable communication for various satellite applications, including weather monitoring, navigation, earth observation, and telecommunications.
What materials are used in RF & Microwave PCBs?
RF & Microwave PCBs use high-performance materials with low dielectric constants and low loss tangents to minimize signal loss at high frequencies. Common materials include PTFE-based substrates like Rogers RO4000 series, as well as specialty ceramics and metal core laminates.
What design considerations are important for RF & Microwave PCBs?
Design considerations for RF & Microwave PCBs include controlled impedance routing, careful component placement, shielding techniques to minimize interference, and thermal management to dissipate heat generated by high-power components.
How are RF & Microwave PCBs manufactured?
Manufacturing RF & Microwave PCBs involves specialized processes such as controlled impedance routing, precision drilling of microvias, and surface finishing techniques to ensure signal integrity and reliability. Advanced equipment and expertise are required to produce high-quality RF & Microwave PCBs.
What are the challenges in designing RF & Microwave PCBs for satellites?
Challenges in designing RF & Microwave PCBs for satellites include maintaining signal integrity at high frequencies, minimizing electromagnetic interference, ensuring reliability in harsh environmental conditions, and meeting stringent size and weight constraints for space applications.
How can I ensure the quality of RF & Microwave PCBs for satellite applications?
Ensuring the quality of RF & Microwave PCBs involves rigorous testing and validation, adherence to industry standards and specifications, collaboration with experienced PCB manufacturers, and thorough review of design and manufacturing processes to identify and address potential issues.