R&D Circuit Board Manufacturer
R&D Circuit Board Manufacturer,R&D Circuit Boards (PCBs) are specialized prototypes crafted for research and development purposes in electronics. These boards are meticulously designed to facilitate testing, experimentation, and innovation in new technologies and products. R&D PCBs often incorporate advanced features like multilayered designs, high-frequency capabilities, and precise signal integrity management. They serve as essential tools in validating and refining electronic designs before full-scale production, ensuring optimal functionality and performance. R&D PCBs enable engineers and researchers to push the boundaries of technology, paving the way for advancements across various industries, from telecommunications to renewable energy.
What is an R&D Circuit Board (PCB)?
An R&D (Research and Development) Circuit Board, commonly known as R&D PCB, is a specialized type of printed circuit board used primarily in the early stages of product development. Unlike final production PCBs, which are designed for mass manufacturing and reliability, R&D PCBs serve the purpose of testing and prototyping new designs and functionalities.
These boards are crucial in the iterative process of refining and perfecting electronic products before they are mass-produced. They allow engineers and designers to experiment with different components, configurations, and circuit layouts without committing to large-scale manufacturing costs. R&D PCBs often incorporate features like easy access test points, debugging interfaces, and flexibility in component mounting to facilitate rapid adjustments and troubleshooting.
Due to their nature, R&D PCBs may have shorter lifespans and be less optimized for durability compared to production PCBs. However, they play a vital role in the innovation cycle by enabling engineers to validate concepts, assess performance, and make informed design decisions early in the development process. This iterative approach helps ensure that final products meet performance requirements and market expectations while minimizing risks and costs associated with design flaws or unforeseen technical challenges.
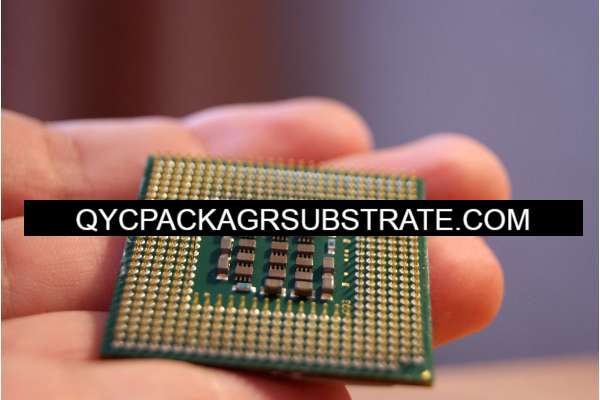
R&D Circuit Board Manufacturer
What are R&D Circuit Board Design Guidelines?
R&D (Research and Development) Circuit Board Design Guidelines are principles and best practices that engineers and designers follow when developing prototype and testing PCBs in the early stages of product development. These guidelines help ensure that R&D PCBs are designed effectively for experimentation, testing, and iterative refinement. Here are some key design guidelines typically considered for R&D circuit boards:
- Prototype-Friendly Layout: Design the PCB layout to facilitate easy modifications and component swaps. Use larger pads and through-holes to accommodate manual soldering and desoldering, if needed.
- Component Accessibility: Ensure easy access to critical components for testing and measurement purposes. Use test points and probe pads strategically placed near key signals and components.
- Debugging Features: Include debugging aids such as extra ground points, dedicated voltage measurement points, and test pads for oscilloscope probes or logic analyzers.
- Flexibility in Component Selection: Design the PCB to support various types and sizes of components to allow flexibility in testing different configurations and specifications.
- Design for Ease of Modification: Use jumper pads or zero-ohm resistors to easily change configurations and test different circuit options without redesigning the entire PCB.
- Modular Design Approach: Divide the PCB into functional modules to isolate sections of the circuit for independent testing and debugging.
- Signal Integrity Considerations: While not as stringent as in production PCBs, consider signal integrity principles such as proper trace routing, impedance matching for critical signals, and minimizing noise coupling.
- Document Design Changes: Maintain clear documentation of design iterations, modifications, and test results to track the evolution of the PCB design and facilitate collaboration among team members.
- Design for Reliability Testing: Implement features to simulate environmental conditions and stress tests relevant to the intended application, if feasible within the R&D phase.
- Cost and Time Considerations: Balance the trade-offs between cost, time, and complexity to achieve the objectives of the R&D phase efficiently while considering potential scalability to production.
By adhering to these guidelines, engineers can expedite the development cycle, identify and resolve design issues early, and ultimately optimize the transition from prototype to production-ready PCBs. These practices contribute to efficient R&D processes and ensure that final products meet performance, reliability, and manufacturability requirements.
What is the R&D Circuit Board Fabrication Process?
The R&D (Research and Development) circuit board fabrication process involves several steps aimed at creating prototype PCBs for testing and iteration in the early stages of product development. Here’s an overview of the typical fabrication process for R&D circuit boards:
- Design: Engineers start by creating a PCB design using CAD (Computer-Aided Design) software. The design includes schematic capture, component placement, routing of traces, and generation of Gerber files (standard file format used in PCB fabrication).
- Material Selection: Choose the appropriate PCB substrate material based on electrical performance requirements, mechanical properties, and cost considerations. Common materials include FR-4 (a type of fiberglass-reinforced epoxy laminate), flexible PCB materials, or specialized substrates for high-frequency applications.
- Gerber File Preparation: Export the PCB design files in Gerber format, which include layers such as copper traces, solder mask, silkscreen, and drill files. These files provide instructions for the fabrication process.
- Manufacturing Setup: PCB manufacturers receive the Gerber files and begin the manufacturing setup. This involves preparing the production panel, applying a photosensitive layer to the substrate, and using the Gerber files to create the necessary patterns on the PCB layers.
- Imaging and Etching: Use UV light and a photographic process to transfer the PCB design patterns onto the photosensitive layer. After exposure and development, etch away the unwanted copper from the substrate using chemical processes, leaving behind the circuit traces.
- Drilling: Drill holes at specified locations for component mounting and through-hole vias. Automated drilling machines use the drill files from the Gerber data to accurately position holes according to the design.
- Plating and Surface Finish: Plate the PCB with a thin layer of copper to enhance conductivity and protect the exposed copper traces. Apply a surface finish such as HASL (Hot Air Solder Leveling), ENIG (Electroless Nickel Immersion Gold), or OSP (Organic Solderability Preservatives) to ensure solderability and protect against oxidation.
- Solder Mask and Silkscreen: Apply solder mask over the PCB to insulate copper traces and prevent solder bridges during assembly. Add silkscreen legends to indicate component placement, reference designators, and other necessary information.
- Testing and Inspection: Conduct electrical testing to verify the integrity of the circuit connections and functionality. Inspect the PCB for any defects in manufacturing, such as short circuits, open circuits, or incorrect dimensions.
- Assembly and Testing: Mount components onto the PCB using soldering techniques (either manual or automated). Perform functional testing to evaluate the performance of the assembled prototype PCB, including electrical characteristics, signal integrity, and overall functionality.
- Iterative Design Process: Based on test results and design evaluations, iterate on the PCB design as necessary. This may involve making modifications to the schematic, layout, or component selection to improve performance or address issues identified during testing.
Throughout the R&D circuit board fabrication process, collaboration between design engineers and PCB manufacturers is crucial to ensure that the prototype PCBs meet the design specifications and performance goals. The iterative nature of R&D allows for refinement and optimization of the PCB design before moving towards mass production.
How do you manufacture an R&D Circuit Board (PCB)?
Manufacturing an R&D (Research and Development) circuit board involves several key steps, tailored to accommodate the iterative and experimental nature of prototype development. Here’s a detailed outline of the typical process:
- PCB Design: Begin with creating the PCB design using CAD (Computer-Aided Design) software. This includes schematic capture, component placement, routing of traces, and generating Gerber files (standard format for PCB manufacturing).
- Material Selection: Choose the PCB substrate material based on electrical requirements, mechanical properties, and cost considerations. Common materials include FR-4 for standard applications, flexible materials for specialized needs, or high-frequency materials for RF applications.
- Gerber File Preparation: Export the PCB design files (Gerber files) that contain all necessary information for manufacturing, including copper layers, solder mask, silkscreen, and drill files.
- Manufacturing Setup: Provide the Gerber files to the PCB manufacturer. They will prepare the production panel, apply the substrate material with a copper layer, and apply the photosensitive layer needed for imaging.
- Imaging: Use UV light and a photomask to transfer the PCB design onto the photosensitive layer. After exposure and development, the unwanted copper is removed through etching, leaving behind the circuit traces.
- Drilling: Drill holes at specified locations for component mounting and through-hole vias. This is done using automated drilling machines guided by the drill files from the Gerber data.
- Plating and Surface Finish: Plate the PCB with a thin layer of copper to enhance conductivity and apply a surface finish to protect the copper and ensure solderability. Surface finishes like HASL (Hot Air Solder Leveling), ENIG (Electroless Nickel Immersion Gold), or OSP (Organic Solderability Preservatives) are commonly used.
- Solder Mask and Silkscreen: Apply solder mask over the PCB to insulate copper traces and prevent solder bridges. Add silkscreen legends to indicate component placement, reference designators, and other necessary markings.
- Testing and Inspection: Perform electrical testing to verify the connectivity and functionality of the PCB. Inspect the PCB for any defects such as short circuits or open circuits. This step ensures the prototype meets initial design specifications.
- Component Assembly: Mount components onto the PCB using soldering techniques. This can be done manually for prototypes or using automated pick-and-place machines for larger-scale prototypes.
- Functional Testing: After assembly, conduct functional testing to evaluate the performance of the prototype PCB. This includes testing electrical characteristics, signal integrity, and overall functionality according to the intended application.
- Iterative Refinement: Based on testing results and design evaluations, iterate on the PCB design as needed. Make adjustments to the schematic, layout, or component selection to improve performance or address any issues identified during testing.
Throughout the manufacturing process of R&D circuit boards, collaboration between design engineers and PCB manufacturers is crucial. Effective communication ensures that design specifications are met and any adjustments needed during prototyping are implemented efficiently. This iterative approach allows for rapid development and refinement of electronic designs before moving towards final production.
How much should an R&D Circuit Board (PCB) cost?
The cost of an R&D (Research and Development) circuit board can vary widely depending on several factors, including the complexity of the design, the size of the board, the number of layers, the choice of materials, and the quantities ordered. Here are some general considerations that impact the cost of R&D PCBs:
- Design Complexity: PCBs with complex designs, such as those with densely packed components, high-speed signal requirements, or specialized features like impedance control, will typically cost more to manufacture due to the advanced manufacturing techniques required.
- Board Size and Layers: Larger PCBs and those with multiple layers (e.g., 4-layer, 6-layer) will generally be more expensive than smaller, single-layer PCBs. Each additional layer adds complexity to the manufacturing process.
- Material Selection: The choice of PCB substrate material (e.g., FR-4, flexible materials, high-frequency materials) and surface finish (e.g., HASL, ENIG, OSP) affects the cost. High-frequency materials and advanced surface finishes tend to increase costs.
- Quantity Ordered: Typically, PCB manufacturers offer economies of scale, where ordering larger quantities reduces the cost per unit. However, for R&D purposes, smaller quantities are often ordered, which can result in higher per-unit costs.
- Turnaround Time: Expedited manufacturing services (quick-turn PCB fabrication) often come with a premium cost compared to standard lead times. R&D projects may require faster turnaround times to accelerate development cycles.
- Additional Services: Costs may also include additional services such as stencil manufacturing for solder paste application, electrical testing, and assembly if required.
As a rough estimate, the cost of an R&D PCB can range from tens to hundreds of dollars per board, depending on the above factors. For very simple single-layer prototypes, costs might be lower (e.g., $20 – $50 per board), while more complex multi-layer or high-frequency prototypes could cost several hundred dollars or more per board.
It’s important for project managers and engineers to work closely with PCB manufacturers to optimize designs for cost-effective production while meeting performance and quality requirements. Getting quotes from multiple manufacturers and balancing cost with desired features and quality is key to managing R&D budget effectively.
What is R&D Circuit Board base material?
The base material used for R&D (Research and Development) circuit boards, as well as for most standard PCBs, is typically a type of laminate composed of reinforcing materials (usually fiberglass) and a resin binder. The most commonly used base material for PCBs is known as FR-4, which stands for Flame Retardant 4. Here are the key components of FR-4 and why it’s widely favored in PCB manufacturing:
- Fiberglass Reinforcement: The core of FR-4 PCBs is typically made from woven fiberglass cloth impregnated with epoxy resin. This fiberglass provides mechanical strength and stability to the PCB.
- Epoxy Resin: The fiberglass cloth is bonded together with epoxy resin, which acts as a strong adhesive and also provides insulation properties. Epoxy resin is chosen for its excellent electrical insulation characteristics and ability to withstand high temperatures during soldering.
- Flame Retardant Properties: FR-4 materials are designed to be flame retardant, meaning they are resistant to catching fire and spreading flames. This is crucial for safety in electronics applications.
- Laminate Construction: FR-4 laminate typically consists of multiple layers of fiberglass cloth impregnated with epoxy resin, compressed and cured under high temperature and pressure to form a solid, durable substrate.
- Electrical Properties: FR-4 materials have consistent electrical properties, such as dielectric constant and loss tangent, which are important for maintaining signal integrity in high-frequency and digital circuits.
- Compatibility with Manufacturing Processes: FR-4 is compatible with standard PCB manufacturing processes, including drilling, etching, plating, and solder mask application, making it versatile for various types of circuit designs.
- Availability and Cost: FR-4 is widely available from multiple suppliers and is relatively cost-effective compared to more specialized PCB materials, making it suitable for both prototyping and production.
While FR-4 is the most common base material for R&D and production PCBs, there are also specialized materials available for specific applications. For example, high-frequency PCBs may use materials like Rogers RO4003C for enhanced signal integrity at microwave frequencies, while flexible PCBs utilize materials such as polyimide for flexibility and durability.
Choosing the appropriate base material depends on the specific requirements of the R&D project, including electrical performance, mechanical properties, and cost considerations. Working closely with PCB manufacturers can help in selecting the right material to meet the project’s goals effectively.
Which company makes R&D Circuit Boards (PCBs)?
Many companies are capable of producing R&D (Research and Development) circuit boards (PCBs), including specialized electronic manufacturing service providers and companies dedicated to PCB production. For example, some companies specialize in rapid prototyping, capable of quickly manufacturing small batches of PCB samples according to customer design specifications. Other companies specialize in high-performance or specific-purpose PCBs, such as high-frequency PCBs or flexible PCBs, which often require special materials and processes to ensure stability and signal integrity at design frequencies.
Our company, as a professional electronic manufacturing service provider, has the capabilities to manufacture R&D circuit boards (PCBs) with the following strengths:
- Professional Design Support:We have an experienced team of engineers capable of providing comprehensive support from circuit design and PCB layout to process optimization. Whether it’s initial concept validation or complex circuit design, we can provide customized solutions for our clients.
- Flexible Manufacturing Capability: We can flexibly handle production of PCBs in different specifications and requirements. Whether it’s single-layer, double-layer, or multi-layer PCBs, or special materials like high-frequency materials or flexible PCBs, we can produce according to customer demands.
- Rapid Prototyping: In the R&D phase, rapid prototyping is crucial. We offer fast turnaround cycles to help clients quickly validate design concepts, identify issues, and make adjustments, thereby shortening time to market.
- Advanced Manufacturing Equipment and Processes: We are equipped with advanced PCB manufacturing equipment and precise process control systems to ensure the quality and consistency of every PCB. We use the latest technology to guarantee PCB accuracy and reliability, meeting the requirements of various applications.
- Comprehensive Quality Management System: We strictly adhere to ISO quality management systems, ensuring rigorous control from raw material procurement to manufacturing and final testing. Every step is carefully monitored to ensure stable and reliable product quality.
Through our professional manufacturing services, clients can obtain high-quality, customized R&D circuit boards that help them iterate quickly, validate designs, and ultimately achieve successful commercialization of their products. We are committed to being a long-term partner for our clients in the field of electronic manufacturing, providing comprehensive technical support and efficient production solutions.
What are the 7 qualities of good customer service?
Good customer service is characterized by several key qualities that contribute to positive customer experiences and satisfaction. Here are seven essential qualities:
- Responsiveness: Good customer service involves being prompt in responding to customer inquiries, concerns, and requests. This includes acknowledging customer communication promptly and providing timely resolutions to issues.
- Empathy: Empathy is crucial in understanding and addressing customer needs and emotions. It involves listening actively to customers, showing genuine concern for their issues, and putting oneself in their shoes to provide appropriate support.
- Patience: Dealing with customers may sometimes require patience, especially in challenging situations. Good customer service representatives remain calm, courteous, and composed, even when faced with frustrated or upset customers.
- Clear Communication:Effective communication is essential for delivering good customer service. This includes conveying information clearly and concisely, using simple language, and ensuring customers understand the information provided.
- Product Knowledge: Having a good understanding of the products or services offered allows customer service representatives to answer questions accurately, provide helpful recommendations, and troubleshoot effectively.
- Problem-Solving Skills: Good customer service involves the ability to identify and address customer issues promptly and effectively. This includes taking ownership of problems, proposing viable solutions, and following through until the issue is resolved to the customer’s satisfaction.
- Professionalism: Professionalism in customer service encompasses maintaining a positive attitude, being courteous and respectful towards customers, and representing the company in a favorable manner. It also includes adhering to company policies and procedures while interacting with customers.
By embodying these qualities, businesses can enhance customer loyalty, foster positive relationships, and differentiate themselves in competitive markets by delivering exceptional customer service experiences.
FAQs
What are R&D Circuit Boards (PCBs)?
R&D Circuit Boards are prototypes or early-stage versions of printed circuit boards used in the research and development phase of product development. They are designed for testing and iterating new electronic designs before finalizing for mass production.
Why are R&D Circuit Boards important?
R&D PCBs play a crucial role in validating new electronic designs, identifying potential issues early in the development cycle, and allowing engineers to make necessary adjustments before investing in mass production.
What are the differences between R&D PCBs and production PCBs?
R&D PCBs are typically smaller in quantity and may use simpler or more flexible manufacturing processes compared to production PCBs. They are optimized for prototyping and testing rather than mass manufacturing efficiency and durability.
What materials are used in R&D Circuit Boards?
R&D PCBs often use standard materials like FR-4 (fiberglass-reinforced epoxy laminate), which provide a good balance of cost-effectiveness, electrical properties, and ease of manufacturing. However, they can also utilize specialized materials depending on specific design requirements.
Can R&D PCBs be customized?
Yes, R&D PCBs can be highly customized to meet specific design goals and testing requirements. Engineers can choose different layer counts, materials, surface finishes, and features tailored to their experimental needs.
How can R&D PCBs help in product development?
R&D PCBs allow engineers to iterate quickly on design concepts, validate functionality, and perform feasibility tests. They help reduce development risks, optimize product performance, and shorten time-to-market for new electronic products.
What are the typical turnaround times for R&D PCBs?
Turnaround times for R&D PCBs can vary depending on complexity, quantity, and manufacturing capabilities of the PCB manufacturer. Rapid prototyping services often offer shorter lead times to support fast iteration and testing cycles.
How do you choose a PCB manufacturer for R&D projects?
When selecting a PCB manufacturer for R&D projects, consider factors such as their experience with prototyping, capability to handle custom requirements, quality assurance processes, responsiveness, and cost-effectiveness.
What testing methods are used for R&D PCBs?
Common testing methods for R&D PCBs include electrical testing (e.g., continuity testing, functional testing), thermal testing, and reliability testing to ensure performance under various conditions.