RF Antenna PCB ManufacturerRF Antenna PCB Manufacturer
RF Antenna PCB ManufacturerRF Antenna PCB Manufacturer,RF Antenna PCBs are specialized printed circuit boards meticulously designed for efficient transmission and reception of radio frequency signals. These boards incorporate precise arrangements of conductive traces, components, and antenna structures optimized to operate at specific frequencies. Key design considerations include impedance matching, signal integrity, and minimizing electromagnetic interference (EMI). RF Antenna PCBs are crucial components in various wireless communication systems, satellite communication, radar systems, and IoT devices, where reliable wireless connectivity and high performance are essential. Their design and manufacturing involve advanced techniques to ensure optimal signal propagation, minimal losses, and adherence to stringent performance standards.
What is an RF Antenna PCB?
An RF antenna PCB (Printed Circuit Board) is a specialized circuit board designed to efficiently transmit or receive radio frequency signals. It incorporates various elements such as conductive traces, pads, and components like capacitors, inductors, and transistors, all optimized for high-frequency operations. The design of an RF antenna PCB is crucial as it directly impacts the antenna’s performance in terms of signal strength, range, and interference rejection.
These PCBs are used in a wide range of applications including wireless communication systems (like Wi-Fi, Bluetooth), radar systems, satellite communication, and RFID (Radio Frequency Identification). The layout and construction of an RF antenna PCB must carefully consider factors such as impedance matching, signal integrity, and minimizing electromagnetic interference (EMI). Engineers often use simulation tools to optimize the design before manufacturing, ensuring the antenna meets stringent performance requirements.
Overall, an RF antenna PCB is a sophisticated piece of technology essential for modern wireless communications, enabling the transmission and reception of high-frequency signals in a compact and efficient manner.
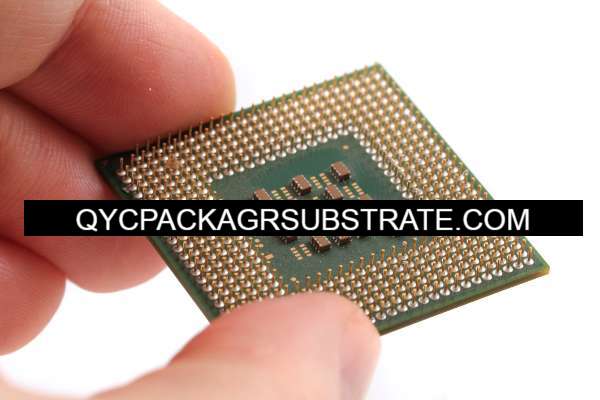
RF Antenna PCB ManufacturerRF Antenna PCB Manufacturer
What are RF Antenna PCB Design Guidelines?
Designing an RF antenna PCB requires careful consideration of several guidelines to ensure optimal performance. Here are some key RF antenna PCB design guidelines:
- Impedance Matching: Ensure that the impedance of the antenna matches the impedance of the transmission line (usually 50 ohms). This minimizes signal reflection and maximizes power transfer.
- PCB Material Selection: Choose a PCB material with low dielectric constant (εr) and loss tangent (tan δ) to minimize signal losses and maintain signal integrity at high frequencies.
- Antenna Placement: Place the antenna on the PCB in a location that minimizes interference from other components and maximizes radiation efficiency. Ground planes and other conductive elements should be carefully positioned to avoid detuning the antenna.
- Antenna Size and Shape: The size and shape of the antenna on the PCB affect its resonant frequency and radiation pattern. Design the antenna to resonate at the desired frequency and to radiate in the desired direction.
- Keepout Zones: Define keepout zones around the antenna to prevent other components, traces, or metal structures from interfering with the antenna’s radiation pattern.
- Ground Planes: Use solid ground planes on both sides of the PCB to provide a low-impedance return path for RF signals and to reduce electromagnetic interference (EMI). Proper grounding is critical for maintaining signal integrity.
- Signal Traces: Keep RF signal traces as short and direct as possible to minimize losses due to resistance, capacitance, and inductance. Use wide traces to lower resistance and impedance.
- Component Placement: Place RF components such as matching networks, filters, and amplifiers close to the antenna to minimize signal losses and improve overall system efficiency.
- Shielding: Use shielding techniques, such as RF shielding cans or shields made of conductive materials, to prevent external electromagnetic interference from affecting the antenna’s performance.
- Simulation and Testing: Use simulation tools (e.g., electromagnetic field simulators) to analyze the RF performance of the antenna design before fabrication. Conduct thorough testing of prototypes to validate the design against performance requirements.
By adhering to these RF antenna PCB design guidelines, engineers can optimize the performance of RF antennas in terms of signal strength, range, efficiency, and resistance to interference, ensuring reliable operation in various wireless communication applications.
What is the RF Antenna PCB Fabrication Process?
The fabrication process of an RF antenna PCB involves several critical steps to ensure the antenna’s performance meets design specifications. Here’s an overview of the typical RF antenna PCB fabrication process:
- Design and Layout: Engineers begin by designing the RF antenna PCB layout using specialized PCB design software. This involves placing the antenna element, matching networks, and other components according to design guidelines to optimize performance.
- Material Selection: Choose PCB materials suitable for RF applications. Typically, materials with low dielectric constant (εr) and low loss tangent (tan δ) are preferred to minimize signal losses and maintain signal integrity at high frequencies.
- Layer Stackup Design: Determine the layer stackup of the PCB, considering factors such as signal trace routing, impedance control, and grounding. RF antennas often require controlled impedance traces and solid ground planes for optimal performance.
- PCB Manufacturing: The PCB manufacturing process begins with preparing the substrate material (typically FR-4 or specialized RF materials). This includes cutting the substrate to size and cleaning it thoroughly to remove any contaminants.
- Printing Conductive Layers: The conductive layers are printed onto the substrate using techniques such as etching or additive processes (e.g., screen printing for conductive inks). These layers form the antenna traces, pads, and other conductive elements.
- Adding Dielectric Layers: Dielectric layers (insulating materials) are added between conductive layers to maintain isolation and to provide support for component mounting.
- Component Mounting: Surface-mount and/or through-hole components are mounted onto the PCB. RF components such as capacitors, inductors, and possibly active components like amplifiers or filters are placed close to the antenna to minimize signal losses.
- Soldering:Components are soldered onto the PCB using reflow soldering or wave soldering processes, depending on component type and PCB design.
- Testing and Inspection: After soldering, the PCB undergoes rigorous testing and inspection. RF testing may include impedance measurements, VSWR (Voltage Standing Wave Ratio) measurements, and antenna radiation pattern testing to ensure it meets performance specifications.
- Packaging and Protection: Once tested and verified, the RF antenna PCB may be coated with protective materials (e.g., conformal coating) to enhance durability and reliability in various environmental conditions.
- Final Quality Control: The final PCBs undergo a final inspection to check for any defects or issues before being packaged and shipped.
Throughout the RF antenna PCB fabrication process, strict adherence to design guidelines, precise manufacturing techniques, and comprehensive testing are essential to ensure the antenna meets the required performance criteria for its intended application in wireless communication systems, radar systems, RFID, and other RF applications.
How do you manufacture an RF Antenna PCB?
Manufacturing an RF antenna PCB involves several precise steps to ensure the antenna performs optimally for its intended application in wireless communication systems, radar systems, RFID, and other RF applications. Here’s a detailed overview of the manufacturing process:
- Design Phase: Engineers begin by designing the RF antenna PCB layout using specialized PCB design software. This involves placing the antenna elements, matching networks, and other components according to design guidelines. Key considerations include impedance matching, signal trace routing, ground plane placement, and component placement to optimize RF performance.
- Material Selection: Choose PCB materials suitable for RF applications. Common materials include FR-4 (standard PCB substrate) and specialized RF substrates with low dielectric constant (εr) and low loss tangent (tan δ) to minimize signal losses at high frequencies.
- Layer Stackup Design: Determine the layer stackup of the PCB, which includes defining the number of layers, thickness of each layer, and material properties. RF antennas often require controlled impedance traces and solid ground planes to ensure signal integrity and minimize electromagnetic interference (EMI).
- Substrate Preparation: Prepare the substrate material by cutting it to size and cleaning it thoroughly to remove any contaminants that could affect adhesion or electrical properties.
- Conductive Layer Preparation: The conductive layers are prepared by printing conductive traces, pads, and other elements onto the substrate. Techniques such as etching or additive processes (e.g., screen printing with conductive inks) are used depending on the design requirements and materials.
- Dielectric Layer Application:Apply dielectric layers (insulating materials) between conductive layers to provide electrical isolation and mechanical support. These layers help maintain the integrity of signal paths and prevent short circuits.
- Component Mounting: Surface-mount and/or through-hole components are mounted onto the PCB according to the design specifications. RF components such as capacitors, inductors, and possibly active components like amplifiers or filters are placed close to the antenna to minimize signal losses and interference.
- Soldering: Components are soldered onto the PCB using precise soldering techniques. This may involve reflow soldering for surface-mount components and wave soldering for through-hole components. Careful control of soldering temperatures and profiles is crucial to prevent damage to sensitive RF components.
- Testing and Inspection: After soldering, the PCB undergoes rigorous testing and inspection. RF testing may include impedance measurements, VSWR (Voltage Standing Wave Ratio) measurements, and antenna radiation pattern testing using specialized equipment to ensure the PCB meets performance specifications.
- Packaging and Protection: Once tested and verified, the RF antenna PCB may be coated with protective materials such as conformal coating to enhance durability and reliability in various environmental conditions. This step also helps prevent corrosion and insulation breakdown over time.
- Final Quality Control: The final PCBs undergo a thorough inspection to check for any defects or issues before being packaged and prepared for shipment to customers or assembly into final products.
Throughout the RF antenna PCB manufacturing process, meticulous attention to detail, adherence to design guidelines, precise manufacturing techniques, and comprehensive testing are essential to ensure the antenna meets the stringent performance requirements demanded by modern wireless communication and RF applications. Each step contributes to the overall quality and reliability of the RF antenna PCB, ensuring it performs optimally in its intended operational environment.
How much should an RF Antenna PCB cost?
The cost of an RF antenna PCB can vary significantly depending on several factors:
- Complexity of Design: The complexity of the antenna design and PCB layout influences the cost. More intricate designs with multiple layers, controlled impedance requirements, and tight tolerances will generally cost more to manufacture.
- Materials Used: The choice of PCB substrate material (e.g., FR-4 vs. specialized RF materials), copper thickness, and the presence of additional features such as shielding or special coatings can impact the cost.
- Quantity: Economies of scale apply, meaning larger production runs typically lower the cost per unit. Prototype quantities or small batch orders may be more expensive per unit compared to larger production orders.
- Manufacturing Process: The specific manufacturing processes used (e.g., etching, additive printing, soldering techniques) and the level of automation can affect costs.
- Testing and Certification: Additional costs may arise from rigorous RF testing and certification to ensure the antenna meets performance standards and regulatory requirements.
- Supplier and Location: Costs can vary based on the PCB manufacturer’s location, their capabilities, and their reputation for quality and reliability.
As a rough estimate, the cost of an RF antenna PCB for a basic design and prototype quantities might range from tens to a few hundred dollars per unit. For larger production quantities and more complex designs, costs could be lower per unit due to economies of scale but might still vary widely based on the factors mentioned.
For accurate pricing, it’s advisable to consult with PCB manufacturers or suppliers who specialize in RF antennas. Providing them with detailed specifications of your design (including material requirements, dimensions, and expected quantity) will help them provide a more precise quote.
What is RF Antenna PCB base material?
The base material used for RF antenna PCBs plays a crucial role in determining the performance and reliability of the antenna. Here are some common materials used as the base substrate for RF antenna PCBs:
- FR-4: This is the most widely used standard substrate material for PCBs. FR-4 is a fiberglass-reinforced epoxy laminate with good mechanical strength and electrical insulation properties. It is cost-effective and suitable for many RF applications, particularly at lower frequencies.
- PTFE (Polytetrafluoroethylene): Also known by the brand name Teflon, PTFE-based materials offer excellent electrical properties, including low dielectric loss and stable electrical characteristics over a wide range of frequencies. PTFE is commonly used in high-frequency RF applications due to its low dielectric constant (εr) and low loss tangent (tan δ).
- Rogers Corporation Materials: Rogers Corporation produces a range of high-frequency laminate materials specifically designed for RF and microwave applications. These materials, such as RO4000 series, RO3000 series, and RT/duroid series, offer low dielectric loss, tight control of dielectric constant, and excellent dimensional stability.
- Ceramic-based Materials: Some RF antennas require ceramic-based substrates for their superior electrical properties, including high dielectric constant and low loss tangent. These materials are used in applications demanding very high frequencies or where miniaturization is critical.
- Other Specialized RF Substrates: Various manufacturers offer specialized RF substrate materials tailored for specific performance requirements. These substrates often feature controlled impedance characteristics, good thermal stability, and reduced moisture absorption, enhancing the antenna’s performance in demanding RF environments.
The choice of base material depends largely on the operating frequency, signal integrity requirements, thermal considerations, and cost constraints of the RF antenna design. Designers typically select a material that provides the best balance of electrical performance, mechanical stability, and cost-effectiveness for their specific application.
Which company makes RF Antenna PCBs?
Many companies specialize in manufacturing RF antenna PCBs, including major manufacturers like Rogers Corporation, Mouser Electronics, and Digi-Key Electronics in the United States. In China, well-known manufacturers such as Oupai Electronics, LCEDA, and BOE have the capability to produce RF antenna PCBs.
The production of RF antenna PCBs requires advanced technology and precise craftsmanship. As a professional PCB manufacturer, our company has years of experience and technical expertise to provide high-quality RF antenna PCB manufacturing services.
Here are the capabilities of our manufacturing:
- Professional Design and Engineering Team: We have experienced engineers who can design and optimize the layout and structure of RF antenna PCBs according to customer requirements, ensuring optimal signal performance and interference resistance.
- Advanced Manufacturing Equipment: We utilize advanced manufacturing equipment and technology, including high-precision CNC machines, automated surface-mount production lines, precise film cutting, and welding equipment to ensure PCB manufacturing accuracy and consistency.
- High-Quality Material Selection: We choose high-quality PCB materials, including specialized materials for RF applications such as FR-4, PTFE (Polytetrafluoroethylene), and Rogers Corporation’s high-frequency material series, ensuring PCB stability and electrical performance.
- Strict Quality Control and Testing Processes: We implement rigorous quality control and testing processes, from material inspection to every stage of the production process. We use advanced testing equipment and methods such as impedance testing, VSWR (Voltage Standing Wave Ratio) testing, and antenna radiation pattern testing to ensure each RF antenna PCB meets design requirements and customer expectations.
- Customized Service and Technical Support: We provide customized services and comprehensive technical support, from prototype development to mass production. We can flexibly address various customer needs and provide professional advice and solutions to help customers achieve success in their RF applications.
With our company’s professional manufacturing capabilities and commitment to delivering high-quality products and services, we are able to meet various customer demands and challenges in RF antenna PCBs, contributing our technology and expertise to the success of our customers’ projects.
What are the 7 qualities of good customer service?
Good customer service is characterized by several key qualities that contribute to a positive customer experience and build customer loyalty. Here are seven important qualities of good customer service:
- Responsiveness:Good customer service involves responding promptly to customer inquiries, concerns, and requests. Customers appreciate timely assistance and acknowledgment of their needs.
- Empathy: Empathy is essential in understanding and relating to customers’ feelings, concerns, and situations. Showing empathy helps in building rapport and demonstrating that their concerns are understood and taken seriously.
- Patience: Patience is crucial when dealing with customers, especially in challenging situations or when resolving complex issues. Maintaining a calm and patient demeanor helps in providing effective assistance and support.
- Clear Communication: Effective communication involves listening attentively to customers, asking clarifying questions, and providing clear and understandable information or instructions. Clear communication prevents misunderstandings and ensures that customers receive accurate solutions or guidance.
- Knowledgeability: Good customer service representatives possess a deep knowledge of the products or services they support. They can answer customer questions accurately, offer relevant advice, and provide solutions efficiently.
- Professionalism: Professionalism encompasses maintaining a positive attitude, respecting customers’ time and privacy, and adhering to company policies and procedures. It involves conducting oneself with integrity and demonstrating competence in handling customer interactions.
- Problem-solving Skills: Effective customer service involves the ability to identify issues, analyze problems, and find appropriate solutions. This may include troubleshooting technical problems, resolving complaints, or addressing customer concerns effectively.
By embodying these qualities, businesses can create a customer-centric culture that prioritizes customer satisfaction and fosters long-term relationships. Good customer service not only resolves immediate issues but also leaves a positive impression that encourages repeat business and referrals.
FAQs
What materials are used in RF Antenna PCBs?
RF Antenna PCBs use materials with low dielectric constant (εr) and low loss tangent (tan δ) to minimize signal losses. Common materials include FR-4, PTFE (Teflon), and specialized RF laminates from manufacturers like Rogers Corporation.
What are the key design considerations for RF Antenna PCBs?
Key considerations include impedance matching, antenna placement, ground plane design, minimizing electromagnetic interference (EMI), and optimizing the antenna structure for desired radiation patterns and frequencies.
What are the typical applications of RF Antenna PCBs?
RF Antenna PCBs are used in wireless communication systems (Wi-Fi, Bluetooth), cellular networks, radar systems, satellite communication, RFID (Radio Frequency Identification), and IoT (Internet of Things) devices where wireless connectivity is crucial.
How do you optimize an RF Antenna PCB design?
Optimization involves simulation tools for electromagnetic analysis to ensure proper impedance matching, radiation efficiency, and minimal interference. It also includes careful component placement, ground plane design, and testing to verify performance.
What testing methods are used for RF Antenna PCBs?
Testing methods include impedance testing to ensure proper signal transmission, VSWR (Voltage Standing Wave Ratio) measurements to assess antenna performance, and antenna radiation pattern testing to verify directional characteristics and coverage.
How can RF Antenna PCBs be protected from environmental factors?
RF Antenna PCBs can be protected using conformal coatings to guard against moisture, dust, and mechanical damage. Proper enclosure design and shielding techniques also help in minimizing external interference.