RF High Frequency substrates Manufacturer
RF High Frequency substrates Manufacturer and package substrate Manufacturer. We use advanced Msap and Sap technology, High multilayer interconnection substrates from 4 to 18 layers,
RF High Frequency substrates are specialized materials crucial for the efficient transmission of high-frequency signals in electronic circuits. Engineered with specific electrical properties, these substrates minimize signal loss and maintain signal integrity, making them essential in applications like radio communications, radar systems, and wireless devices.
These substrates typically feature low dielectric constants, minimizing signal dispersion, and low loss tangents to reduce energy dissipation. High thermal conductivity ensures effective heat dissipation, crucial for maintaining performance under high-power conditions. Additionally, mechanical stability ensures reliability in demanding environments.
Manufacturing RF High Frequency substrates involves precise processes, including material selection, thin film deposition, photolithography, and metallization. Design considerations encompass transmission line geometry, grounding techniques, and thermal management.
RF High Frequency substrates find applications in RF filters, power amplifiers, antennas, and more, enabling the functionality of electronic systems operating at high frequencies. With their critical role in modern communication and radar technologies, these substrates are indispensable components in advanced electronic devices.
What is an RF High Frequency substrate?
An RF (Radio Frequency) High Frequency substrate is a specialized material used in electronic circuits, particularly in applications requiring high-frequency signals, such as in radio communications, radar systems, and wireless devices.
These substrates are engineered to have specific electrical properties that are crucial for efficient signal transmission and minimal signal loss at high frequencies. They typically have low dielectric constants and loss tangents, which help in maintaining signal integrity. Additionally, they often have high thermal conductivity to dissipate heat generated during operation.
Common materials used for RF High Frequency substrates include specialized ceramics like alumina (Al2O3), aluminum nitride (AlN), and certain types of polytetrafluoroethylene (PTFE) composites such as Rogers Corporation’s RO4000 series or Taconic’s TLY-5A. These materials offer a balance of electrical, thermal, and mechanical properties suitable for RF applications.
Manufacturing processes for RF High Frequency substrates involve precise control over material properties and layer thicknesses to ensure consistency and performance across the entire substrate. Advanced techniques such as thin-film deposition, laser drilling, and chemical etching may be employed to create intricate circuit patterns and features on these substrates.
Overall, RF High Frequency substrates play a critical role in enabling the functionality and performance of electronic systems operating at high frequencies, making them essential components in modern communication and radar technologies.
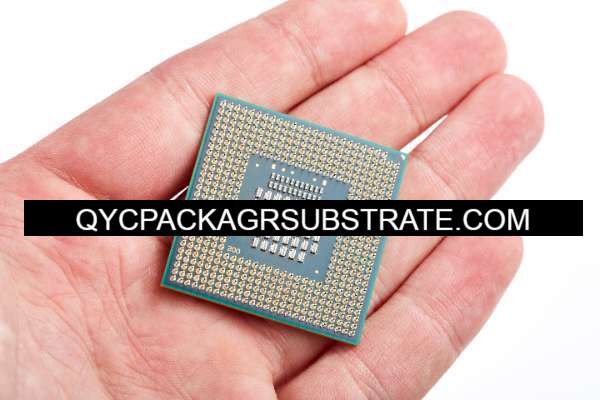
RF High Frequency substrates Manufacturer
What are the RF High Frequency substrate Design Guidelines?
Designing with RF High Frequency substrates requires careful consideration of various factors to ensure optimal performance. Here are some general design guidelines:
- Material Selection: Choose the appropriate substrate material based on your application requirements. Consider factors such as dielectric constant (εr), loss tangent (tanδ), thermal conductivity, mechanical properties, and cost.
- Transmission Line Geometry: Use controlled impedance transmission lines to minimize signal loss and impedance mismatch. Design transmission lines with appropriate widths and spacing to achieve the desired characteristic impedance (e.g., 50 ohms).
- Grounding: Implement effective grounding techniques to minimize ground loops and ensure signal integrity. Use solid ground planes whenever possible to provide low impedance return paths for RF signals.
- Component Placement: Carefully place components to minimize signal distortion and interference. Keep high-frequency components close together to reduce parasitic capacitance and inductance. Consider the impact of component placement on signal routing and impedance matching.
- Signal Routing: Route RF traces with short, direct paths to minimize signal loss and electromagnetic interference. Avoid sharp bends and right angles in trace routing, as they can lead to signal reflections and impedance mismatches.
- Via Design: Use vias strategically to transition signals between different layers of the substrate. Optimize via placement and design to minimize signal distortion and maintain controlled impedance.
- Decoupling and Filtering: Include decoupling capacitors and filtering components to suppress noise and interference. Place decoupling capacitors as close as possible to power and ground pins of active components to provide high-frequency noise isolation.
- Thermal Management: Incorporate thermal vias and thermal relief patterns to dissipate heat efficiently from high-power components. Ensure proper ventilation and heat sinking to prevent overheating and maintain signal integrity.
- EMI Shielding:Implement EMI shielding techniques such as grounded enclosures or shielding layers to minimize electromagnetic interference from external sources and adjacent components.
- Testing and Validation: Perform thorough testing and validation of the RF circuit design using simulations, prototypes, and measurement techniques such as network analyzers and spectrum analyzers. Validate key parameters such as impedance matching, insertion loss, return loss, and isolation.
By following these design guidelines, you can optimize the performance and reliability of RF circuits implemented on High Frequency substrates.
What is the RF High Frequency substrate Fabrication Process?
The fabrication process for RF High Frequency substrates involves several steps to create the desired material properties and circuit structures. Here’s an overview of the typical fabrication process:
- Material Selection: Choose the appropriate substrate material based on the desired electrical, thermal, and mechanical properties. Common materials include ceramics like alumina (Al2O3), aluminum nitride (AlN), and PTFE-based composites.
- Substrate Preparation: Prepare the substrate material by cutting it into the desired size and shape. The surface may be cleaned and treated to remove contaminants and improve adhesion for subsequent processing steps.
- Thin Film Deposition: Apply thin film layers of conductive materials such as copper or gold onto the substrate surface using techniques like sputtering or evaporation. These conductive layers form the basis for circuit traces and components.
- Photolithography: Use photolithography to define the circuit patterns on the substrate. A photoresist material is deposited on the substrate surface, exposed to UV light through a photomask containing the desired circuit pattern, and developed to remove the exposed areas, leaving behind the patterned photoresist.
- Etching: Etch away the unwanted areas of the thin film layers using chemical etchants or plasma etching. The patterned photoresist acts as a mask to protect the desired circuit traces while the exposed areas are etched away, defining the circuit features.
- Dielectric Layer Deposition: Deposit dielectric material layers onto the substrate surface to insulate the circuit traces and provide mechanical support. These dielectric layers may be deposited using techniques like spin coating, chemical vapor deposition (CVD), or screen printing.
- Via Formation: Create vias (plated-through holes) in the substrate to allow interconnection between different layers of the circuit. Vias are typically formed by drilling holes in the substrate and then metallizing the hole walls to provide electrical conductivity.
- Metallization and Surface Finish: Deposit additional metallization layers on the substrate surface to create solder pads, wire bond pads, and other surface features. Apply surface finishes such as immersion gold or immersion silver to improve solderability and corrosion resistance.
- Surface Planarization:Optionally, perform surface planarization techniques such as chemical-mechanical polishing (CMP) to flatten the substrate surface and improve the uniformity of circuit features.
- Final Inspection and Testing: Inspect the fabricated substrate for defects and dimensional accuracy. Perform electrical testing to verify circuit continuity, impedance matching, and other performance parameters.
Once the fabrication process is complete, the RF High Frequency substrate can be assembled with other components to create RF circuits and systems for various applications such as wireless communication, radar systems, and microwave devices.
How do you manufacture an RF High Frequency substrate?
Manufacturing an RF High Frequency substrate involves a series of intricate processes to achieve the desired electrical, thermal, and mechanical properties required for high-frequency applications. Here’s a step-by-step overview of the manufacturing process:
- Material Selection: Choose a substrate material with properties suitable for RF applications, such as low dielectric constant (εr), low loss tangent (tanδ), high thermal conductivity, and mechanical stability. Common materials include specialized ceramics like alumina (Al2O3), aluminum nitride (AlN), and certain PTFE-based composites.
- Substrate Preparation: Cut the substrate material into the desired size and shape using techniques like sawing or laser cutting. Clean the substrate surface to remove contaminants and ensure proper adhesion for subsequent processing steps.
- Thin Film Deposition: Deposit thin film layers of conductive materials such as copper or gold onto the substrate surface. This can be achieved through techniques like sputtering or evaporation, creating a conductive layer that will serve as the basis for circuit traces and components.
- Photolithography: Use photolithography to define the circuit patterns on the substrate. A layer of photoresist material is deposited on the substrate surface, exposed to UV light through a photomask containing the desired circuit pattern, and then developed to remove the exposed areas, leaving behind the patterned photoresist.
- Etching: Etch away the unwanted areas of the thin film layers using chemical etchants or plasma etching. The patterned photoresist acts as a mask to protect the desired circuit traces while the exposed areas are etched away, defining the circuit features.
- Dielectric Layer Deposition: Deposit dielectric material layers onto the substrate surface to insulate the circuit traces and provide mechanical support. Dielectric materials with low εr and tanδ are preferred to minimize signal loss and maintain signal integrity.
- Via Formation: Create vias (plated-through holes) in the substrate to allow interconnection between different layers of the circuit. Vias are typically formed by drilling holes in the substrate and then metallizing the hole walls to provide electrical conductivity.
- Metallization and Surface Finish: Deposit additional metallization layers on the substrate surface to create solder pads, wire bond pads, and other surface features. Apply surface finishes such as immersion gold or immersion silver to improve solderability and corrosion resistance.
- Surface Planarization: Optionally, perform surface planarization techniques such as chemical-mechanical polishing (CMP) to flatten the substrate surface and improve the uniformity of circuit features.
- Final Inspection and Testing: Inspect the manufactured substrate for defects and dimensional accuracy. Perform electrical testing to verify circuit continuity, impedance matching, and other performance parameters.
Once the RF High Frequency substrate is manufactured, it can be assembled with other components to create RF circuits and systems for applications such as wireless communication, radar systems, and microwave devices. Each step of the manufacturing process requires precision and careful control to ensure the substrate meets the stringent requirements of high-frequency operation.
How much should an RF High Frequency substrate cost?
The cost of an RF High Frequency substrate can vary significantly depending on several factors including the material used, the substrate size and thickness, the complexity of the circuit design, and the manufacturing processes involved. Here are some factors to consider when estimating the cost:
- Material Cost: The choice of substrate material can have a significant impact on the cost. Specialized materials like alumina (Al2O3), aluminum nitride (AlN), and certain PTFE-based composites tend to be more expensive compared to standard FR-4 or other common PCB materials.
- Manufacturing Processes: The complexity of the manufacturing processes required to fabricate the RF substrate will influence the cost. Processes such as thin film deposition, photolithography, and precision etching may incur higher costs compared to standard PCB manufacturing techniques.
- Circuit Design Complexity: The complexity of the RF circuit design, including the number of layers, the density of circuit features, and the level of precision required, can impact the manufacturing cost. More complex designs with finer features may require additional processing steps and higher manufacturing tolerances, resulting in higher costs.
- Volume and Scale: The volume of production and economies of scale can also affect the cost per unit. Larger production volumes typically result in lower per-unit costs due to efficiencies in manufacturing and purchasing.
- Quality and Tolerance Requirements: Higher quality standards and tighter tolerances may increase the cost of manufacturing. RF High Frequency substrates often require strict adherence to dimensional tolerances, material properties, and electrical performance specifications, which can add to the manufacturing cost.
- Additional Features:Additional features such as surface finishes, impedance control, EMI shielding, and surface planarization may add to the overall cost of the substrate.
As a rough estimate, the cost of an RF High Frequency substrate can range from tens to hundreds of dollars per square inch, depending on the factors mentioned above. It’s essential to work closely with a manufacturing partner to determine the most cost-effective approach that meets the requirements of your RF application.
What is RF High Frequency substrate base material?
RF High Frequency substrates can be made from various materials, each with its own set of properties tailored to meet the requirements of high-frequency applications. Some common base materials used for RF High Frequency substrates include:
- Alumina (Al2O3): Alumina substrates offer excellent electrical insulation properties, high thermal conductivity, and good mechanical stability. They are suitable for applications requiring high power handling and stability over a wide temperature range.
- Aluminum Nitride (AlN): Aluminum nitride substrates have high thermal conductivity, low dielectric loss, and excellent stability at high frequencies. They are ideal for applications where thermal management and signal integrity are critical, such as in power amplifiers and microwave devices.
- PTFE-Based Composites: PolyTetraFluoroEthylene (PTFE) composites, such as those containing woven glass or ceramic fillers, offer low dielectric constants, low loss tangents, and excellent dimensional stability. These substrates are widely used in high-frequency PCBs and RF/microwave circuits.
- Rogers Corporation’s RO4000 Series: The RO4000 series is a family of high-performance laminates based on PTFE and ceramic fillers. These substrates offer stable electrical properties over a wide frequency range, making them suitable for demanding RF and microwave applications.
- Taconic’s TLY-5A: Taconic’s TLY-5A is a PTFE-based composite material with low dielectric loss and excellent electrical performance at high frequencies. It is often used in RF/microwave circuits, antennas, and wireless communication systems.
These base materials provide the foundation for fabricating RF High Frequency substrates with the required electrical, thermal, and mechanical properties for various high-frequency applications. The choice of substrate material depends on factors such as frequency range, power handling requirements, thermal management considerations, and cost constraints.
Which companies make RF High Frequency substrates?
Many companies produce RF high-frequency substrates, including well-known names like Rogers Corporation, Taconic Advanced Dielectric Division, DuPont, Isola, Arlon Electronic Materials, and others. These companies specialize in researching and manufacturing high-performance RF and microwave substrate materials to meet the demands of wireless communications, radar systems, satellite communications, and other fields.
Just like these companies, our company is also capable of producing RF high-frequency substrates. With advanced manufacturing equipment and a professional technical team, we can provide various types of RF substrates to meet different customer requirements. We employ advanced materials and processing techniques to ensure that our substrates exhibit stable electrical performance, excellent thermal management characteristics, and good mechanical stability.
Our RF high-frequency substrates can be applied in various RF and microwave circuit designs, such as power amplifiers, RF filters, antennas, mixers, and more. Our manufacturing process rigorously controls each step to ensure that the quality and performance of the substrates meet our customers’ requirements. Additionally, we can customize RF high-frequency substrates according to specific customer needs, including different materials, thicknesses, sizes, and special processing requirements.
As your partner, we are committed to providing you with high-quality, high-performance RF high-frequency substrates to help you achieve success in wireless communication and microwave applications. With our wealth of experience and professional technical team, we can offer comprehensive technical support and customized solutions. We look forward to working with you to advance the development and application of RF and microwave technology.
What are the 7 qualities of good customer service?
Good customer service is essential for maintaining positive relationships with customers and fostering loyalty. Here are seven qualities that characterize excellent customer service:
- Responsiveness: Respond promptly to customer inquiries, concerns, and requests. Customers appreciate timely assistance and expect their issues to be addressed in a timely manner. Whether it’s answering phone calls, replying to emails, or assisting customers in person, being responsive shows that you value their time and are committed to meeting their needs.
- Empathy: Demonstrate empathy and understanding towards customers’ situations, feelings, and concerns. Put yourself in their shoes to better comprehend their perspective and tailor your responses accordingly. Showing empathy helps build rapport and trust with customers, making them feel valued and heard.
- Clarity: Communicate clearly and effectively with customers to ensure mutual understanding. Use simple language, avoid jargon, and provide concise explanations to address their questions or issues. Clear communication helps prevent misunderstandings and facilitates a smoother resolution process.
- Professionalism: Maintain professionalism in all interactions with customers, regardless of the situation or their demeanor. Remain calm, courteous, and respectful, even in challenging or stressful situations. Upholding professional standards fosters a positive impression of your business and promotes customer satisfaction.
- Knowledgeability: Possess thorough knowledge about your products, services, policies, and procedures. Be well-informed and equipped to address customer inquiries, provide accurate information, and offer relevant solutions. Customers appreciate dealing with knowledgeable representatives who can effectively assist them and offer valuable insights.
- Flexibility:Be adaptable and flexible in accommodating customers’ needs and preferences. Recognize that each customer may have unique requirements or circumstances, and be willing to tailor your approach accordingly. Being flexible demonstrates a commitment to finding solutions that meet individual customer needs, enhancing their overall experience.
- Consistency:Strive for consistency in delivering high-quality customer service across all touchpoints and interactions. Ensure that customers receive a consistent level of service whether they interact with your business online, over the phone, or in person. Consistency builds trust and reliability, strengthening customer relationships over time.
By embodying these qualities, businesses can provide exceptional customer service that exceeds expectations, fosters customer satisfaction, and contributes to long-term success.
FAQs (Frequently Asked Questions)
What are RF High Frequency substrates?
RF High Frequency substrates are specialized materials used in electronic circuits, particularly in applications requiring high-frequency signals, such as in radio communications, radar systems, and wireless devices. These substrates are engineered to have specific electrical properties that are crucial for efficient signal transmission and minimal signal loss at high frequencies.
What are the key properties of RF High Frequency substrates?
Key properties of RF High Frequency substrates include low dielectric constants, low loss tangents, high thermal conductivity, and mechanical stability. These properties are essential for maintaining signal integrity, minimizing signal loss, and dissipating heat generated during operation.
What materials are commonly used for RF High Frequency substrates?
Common materials used for RF High Frequency substrates include specialized ceramics like alumina (Al2O3), aluminum nitride (AlN), and certain types of polytetrafluoroethylene (PTFE) composites such as Rogers Corporation’s RO4000 series or Taconic’s TLY-5A.
What are the applications of RF High Frequency substrates?
RF High Frequency substrates are used in various applications, including wireless communication systems, radar systems, microwave devices, satellite communications, RF filters, power amplifiers, antennas, and more. They are critical components in enabling the functionality and performance of electronic systems operating at high frequencies.
How are RF High Frequency substrates manufactured?
The manufacturing process for RF High Frequency substrates involves several steps, including material selection, substrate preparation, thin film deposition, photolithography, etching, dielectric layer deposition, via formation, metallization, surface finish, surface planarization, and final inspection/testing. Advanced techniques and precise control are required to ensure optimal performance.
What factors should be considered when designing with RF High Frequency substrates?
When designing with RF High Frequency substrates, factors to consider include material selection, transmission line geometry, grounding techniques, component placement, signal routing, via design, decoupling and filtering, thermal management, and EMI shielding.
Where can RF High Frequency substrates be sourced?
RF High Frequency substrates can be sourced from various manufacturers and suppliers specializing in electronic materials and components. Companies like Rogers Corporation, Taconic Advanced Dielectric Division, and others offer a range of RF High Frequency substrates tailored to different application requirements.