RF/microwave Package Substrates Manufacturer
RF/microwave Package Substrates Manufacturer,RF/Microwave Package Substrates are specialized materials crucial for high-frequency electronic circuits. Engineered with low dielectric loss and high thermal conductivity, these substrates serve as the foundation for RF and microwave components, ensuring optimal signal integrity and performance. Commonly made from ceramics or polymer composites, they enable the construction of compact and efficient devices used in telecommunications, radar systems, and satellite communication. With precise manufacturing techniques like photolithography and thin-film deposition, RF/microwave package substrates support the development of advanced electronics for diverse applications in aerospace, defense, and wireless technologies.
What is an RF/Microwave Package Substrate?
An RF/microwave package substrate is a critical component used in the packaging of radio frequency (RF) and microwave circuits, which are integral to communication systems, radar, and various sensing technologies. These substrates provide the mechanical base and electrical interconnections for various components such as transistors, diodes, capacitors, and resistors.
Typically, these substrates are fabricated from materials with specific electrical properties to minimize signal loss at high frequencies. Common materials include ceramics like alumina, aluminum nitride, or advanced polymer composites, each chosen for their ability to provide low dielectric losses, high thermal conductivity, and stable electrical properties across a range of temperatures and frequencies.
The design of an RF/microwave package substrate involves careful consideration of the layout to ensure signal integrity. This means that the paths through which RF signals travel must be optimized to minimize signal reflections, impedance mismatches, and attenuation. The substrate often incorporates multiple layers with embedded passive components and interconnects that are configured in a way to preserve the integrity of the signals at microwave frequencies.
Furthermore, the substrates are engineered to enable efficient heat dissipation, which is crucial in high-frequency electronic devices where thermal management can significantly impact performance and reliability. Advanced technologies like microvias and built-in heat sinks can be integrated into these substrates to enhance their functionality.
In summary, RF/microwave package substrates are specialized platforms that not only physically support the components but also play an intricate role in ensuring optimal performance of high-frequency circuits by managing both electrical signals and thermal characteristics.
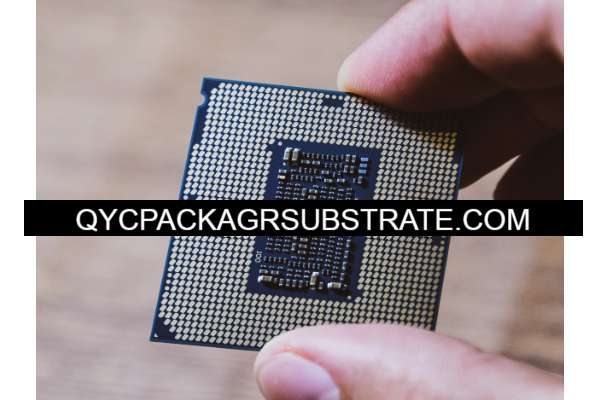
RF/microwave Package Substrates Manufacturer
What are the RF/Microwave Package Substrate Design Guidelines?
Designing RF/microwave package substrates involves a detailed and cautious approach to ensure that the final product delivers the intended electrical performance while also addressing mechanical and thermal issues. Here are some key guidelines that are typically followed in the design of RF/microwave package substrates:
- Material Selection: The choice of substrate material is critical due to its impact on the electrical performance. Materials with low dielectric constants and low loss tangents are preferred because they minimize signal loss and dispersion at high frequencies. Common materials include ceramics (like alumina and aluminum nitride), PTFE composites (such as Teflon), and liquid crystal polymers (LCP).
- Control of Dielectric Properties: The dielectric properties of the substrate must be closely controlled. This includes not only the dielectric constant but also the thickness and uniformity of the dielectric layers, as these factors affect the impedance and propagation characteristics of the RF signals.
- Impedance Matching: Impedance matching is crucial in RF circuit design to minimize reflections and ensure maximum power transfer. The trace widths, spacing, and the substrate’s dielectric constant must be carefully calculated to match the impedance requirements of the circuit.
- Minimization of Parasitic Effects: At high frequencies, parasitic capacitance and inductance can significantly affect circuit performance. Design strategies must include minimizing these effects through proper layout practices, such as reducing trace lengths, using ground planes effectively, and employing shielding where necessary.
- Thermal Management: RF components can generate significant amounts of heat, and the substrate must be able to dissipate this heat effectively. This can involve the use of materials with high thermal conductivity, the design of thermal vias, and possibly the integration of heat sinks or other cooling mechanisms.
- Signal Integrity: Maintaining signal integrity involves careful routing of signal traces, avoiding sharp bends, and maintaining consistent trace widths to prevent impedance discontinuities. Additionally, the separation between power and signal lines must be optimized to reduce noise coupling.
- Layout and Partitioning:Sensitive RF components should be isolated from digital and other high-speed components to avoid interference. This often involves physical separation and the use of ground shields or dedicated ground layers to partition different sections of the circuit.
- Use of Advanced Technologies: Techniques such as the use of microvias for interlayer connections and buried or blind vias can help reduce signal path lengths and minimize interference, thus preserving the integrity of the RF signals.
- Reliability and Testing: Given the critical applications of many RF/microwave components, the substrate design must consider reliability under various environmental conditions. This includes temperature cycling, humidity resistance, and mechanical stability. Rigorous testing protocols are essential to verify that the substrate meets all design specifications.
By adhering to these guidelines, designers can ensure that RF/microwave package substrates perform effectively within their intended applications, delivering reliable and efficient functionality in complex electronic systems.
What is the RF/Microwave Package Substrate Fabrication Process?
The fabrication process of RF/microwave package substrates involves several steps, each crucial for achieving the desired electrical and mechanical properties. Here’s a generalized overview of the typical fabrication process:
- Substrate Material Selection: The process begins with selecting the appropriate substrate material based on the desired electrical properties, thermal conductivity, and mechanical strength. Common materials include ceramics (alumina, aluminum nitride), PTFE-based composites (Teflon), and liquid crystal polymers (LCP).
- Substrate Preparation: The chosen substrate material is prepared by cutting it into the desired size and shape using techniques such as laser cutting or mechanical sawing. The surfaces may also be polished to achieve smoothness and flatness.
- Layer Formation:Depending on the complexity of the design, multiple layers may be required. These layers can be formed by various methods, including screen printing, thin film deposition (such as sputtering or chemical vapor deposition), or lamination of pre-fabricated sheets.
- Pattern Definition: The desired circuit pattern is defined on the substrate layers using techniques such as photolithography or laser ablation. This involves applying a photoresist layer, exposing it to UV light through a photomask with the circuit pattern, and then developing it to remove the unexposed areas.
- Metal Deposition: Conductive metal layers (typically copper) are deposited onto the substrate to create the conductive traces and interconnects. This can be done using techniques such as electroplating, sputtering, or chemical deposition.
- Etching:The excess metal that is not part of the desired circuit pattern is removed through etching processes. This can be achieved using wet etching with chemical solutions or dry etching methods such as plasma etching.
- Via Formation:Vias are small holes drilled or etched through the substrate layers to provide vertical interconnections between different layers of the substrate. Techniques such as laser drilling or photolithography followed by etching are commonly used for via formation.
- Surface Finish: The substrate surface may undergo surface finishing processes to improve solderability, corrosion resistance, and electrical properties. Common surface finishes include immersion tin, immersion silver, ENIG (Electroless Nickel Immersion Gold), and OSP (Organic Solderability Preservatives).
- Assembly and Packaging: Once the substrate fabrication is complete, it is assembled with other components such as integrated circuits, passive devices, and connectors. This assembly process may involve soldering, wire bonding, or flip-chip bonding. The packaged substrate is then tested to ensure functionality and performance.
- Quality Control and Testing: Throughout the fabrication process, quality control measures are implemented to ensure that the substrate meets design specifications. Testing procedures, including electrical testing and inspection under various environmental conditions, are conducted to validate the performance and reliability of the fabricated substrates.
By following these steps meticulously, manufacturers can produce RF/microwave package substrates that meet the stringent requirements of high-frequency electronic applications.
How do you manufacture an RF/Microwave Package Substrate?
Manufacturing an RF/microwave package substrate involves a series of intricate steps to ensure that the final product meets the stringent requirements for high-frequency applications. Here’s a detailed overview of the typical manufacturing process:
- Material Selection: The process begins with selecting the appropriate substrate material based on the desired electrical, thermal, and mechanical properties. Common materials include ceramics (such as alumina and aluminum nitride), PTFE-based composites (like Teflon), and liquid crystal polymers (LCP).
- Substrate Preparation: The selected substrate material is prepared by cutting it into the desired size and shape using techniques such as laser cutting, mechanical sawing, or punching. The surfaces may also undergo processes like polishing to achieve smoothness and flatness.
- Layer Formation: Depending on the complexity of the design, multiple layers may be required. These layers can be formed by various methods, including screen printing, thin film deposition (such as sputtering or chemical vapor deposition), or lamination of pre-fabricated sheets.
- Circuit Pattern Definition: The desired circuit pattern is defined on the substrate layers using techniques such as photolithography or laser ablation. This involves applying a photoresist layer, exposing it to UV light through a photomask with the circuit pattern, and then developing it to remove the unexposed areas.
- Conductive Traces Deposition: Conductive metal layers (typically copper) are deposited onto the substrate to create the conductive traces and interconnects. This can be done using techniques such as electroplating, sputtering, or chemical deposition.
- Etching: The excess metal that is not part of the desired circuit pattern is removed through etching processes. This can be achieved using wet etching with chemical solutions or dry etching methods such as plasma etching.
- Via Formation: Vias are small holes drilled or etched through the substrate layers to provide vertical interconnections between different layers of the substrate. Techniques such as laser drilling or photolithography followed by etching are commonly used for via formation.
- Surface Finish: The substrate surface may undergo surface finishing processes to improve solderability, corrosion resistance, and electrical properties. Common surface finishes include immersion tin, immersion silver, ENIG (Electroless Nickel Immersion Gold), and OSP (Organic Solderability Preservatives).
- Assembly and Packaging: Once the substrate fabrication is complete, it is assembled with other components such as integrated circuits, passive devices, and connectors. This assembly process may involve soldering, wire bonding, or flip-chip bonding. The packaged substrate is then tested to ensure functionality and performance.
- Quality Control and Testing: Throughout the manufacturing process, rigorous quality control measures are implemented to ensure that the substrate meets design specifications. Testing procedures, including electrical testing and inspection under various environmental conditions, are conducted to validate the performance and reliability of the manufactured substrates.
By following these steps meticulously, manufacturers can produce high-quality RF/microwave package substrates that meet the demanding requirements of modern high-frequency electronic systems.
How much should an RF/Microwave Package Substrate cost?
The cost of an RF/microwave package substrate can vary significantly depending on several factors such as:
- Material:The type of substrate material used greatly influences the cost. Ceramics like alumina and aluminum nitride tend to be more expensive compared to polymer-based materials like liquid crystal polymers (LCP) or PTFE composites (Teflon).
- Complexity of Design: Substrates with intricate circuit patterns, multiple layers, and high-density interconnects typically require more sophisticated fabrication processes, leading to higher costs.
- Manufacturing Volume: Economies of scale play a significant role in determining the cost. Larger production volumes often lead to lower per-unit costs due to efficiencies in materials procurement, equipment utilization, and labor.
- Surface Finishes and Features: Additional surface finishes, advanced features like controlled impedance traces, and special requirements such as fine-pitch vias can increase the cost of the substrate.
- Quality and Reliability Requirements:Substrates designed for critical applications may need to undergo additional testing and quality control measures, which can add to the overall cost.
- Supplier and Geographic Location: The pricing structure of substrate manufacturers varies, and factors such as location, reputation, and capabilities can influence pricing.
Generally, the cost of an RF/microwave package substrate can range from a few dollars for simple, low-volume designs to hundreds or even thousands of dollars for complex, high-performance substrates used in advanced applications. For a specific project, it’s best to consult with substrate manufacturers or suppliers to get accurate pricing based on the project’s requirements and specifications.
What is RF/Microwave Package Substrate Base Material?
The base material of an RF/microwave package substrate refers to the primary material used to construct the substrate itself. This material serves as the foundation upon which the circuitry, conductive traces, and other components are built. The choice of base material is crucial as it significantly influences the electrical, thermal, and mechanical properties of the substrate. Common base materials for RF/microwave package substrates include:
- Ceramics: Ceramics such as alumina (Al2O3) and aluminum nitride (AlN) are widely used for their excellent electrical properties, high thermal conductivity, and mechanical strength. Alumina substrates offer good performance at lower frequencies, while aluminum nitride is preferred for higher frequency applications due to its superior thermal conductivity.
- Polymer Composites: Polymer-based materials like liquid crystal polymers (LCP) and polytetrafluoroethylene (PTFE) composites (e.g., Teflon) are lightweight and offer good electrical insulation properties. They are suitable for applications requiring lower cost and flexibility but may have limitations in terms of thermal conductivity and mechanical strength compared to ceramics.
- Glass-Reinforced Epoxy (FR4): FR4 is a popular substrate material in electronics manufacturing due to its affordability and ease of processing. While commonly used in PCBs, it can also be employed for RF/microwave package substrates in less demanding applications.
- Metal Substrates: Metal-based substrates, such as aluminum or copper, are sometimes used for specific applications requiring high thermal conductivity or structural rigidity. These substrates can provide efficient heat dissipation but may introduce challenges related to electrical insulation and signal integrity.
- Semiconductor Substrates: Silicon and other semiconductor materials can be utilized as substrates for integrated RF/microwave circuits, particularly in monolithic microwave integrated circuit (MMIC) applications. These substrates offer high integration density and compatibility with semiconductor fabrication processes but may require specialized handling and processing techniques.
The selection of the base material depends on various factors including the desired operating frequency, power handling capabilities, thermal management requirements, cost constraints, and manufacturing considerations. Designers must carefully evaluate these factors to choose the most suitable base material for their RF/microwave package substrate to ensure optimal performance and reliability in the target application.
Which company makes RF/Microwave Package Substrates?
There are many companies that produce RF/microwave package substrates, and some of the leading manufacturers include Rogers Corporation, DuPont, and Murata Manufacturing Co., Ltd. These companies have advanced technology and extensive experience in providing high-quality substrate solutions for various RF and microwave applications.
As for our company, we are also a specialized manufacturer of RF/microwave package substrates. We have advanced manufacturing equipment and a skilled technical team capable of providing a variety of materials and complex designs to meet the needs of customers in fields such as communication, radar, satellite communications, wireless sensing, and more.
Our production process strictly adheres to international standards and quality management systems. We collaborate with customers to provide customized solutions from initial concept to final product. Our strengths include:
- High-performance material selection: We work with multiple material suppliers to offer a range of options, including high-frequency, low-loss ceramics, high-strength polymer composites, and more, to meet different application needs.
- Advanced manufacturing technology: We possess advanced production equipment and technologies, including precise chemical deposition, thin-film deposition, laser processing, and more, to achieve complex circuit patterns and small structures.
- Strict quality control: We implement rigorous quality control measures at every stage, from raw material procurement to production, conducting thorough inspections and testing to ensure products meet customer requirements and standards.
- Customized solutions: Our team has extensive experience and expertise to provide customized solutions tailored to customer needs and specifications.
- Timely technical support and after-sales service:We offer prompt technical support and after-sales service to ensure customers receive timely assistance and support during product use.
In summary, our company is committed to providing high-quality, high-performance RF/microwave package substrates to meet the needs of customers in communication, radar, satellite communication, and other fields. Our professional team and advanced manufacturing capabilities make us a reliable partner in driving the development of wireless communication technology.
What are the 7 qualities of good customer service?
Good customer service is essential for building strong relationships with customers and fostering loyalty. Here are seven qualities that contribute to excellent customer service:
- Responsiveness: Responding promptly to customer inquiries, concerns, and feedback demonstrates attentiveness and shows that their needs are valued. Whether it’s through phone, email, chat, or in-person interactions, being available and responsive helps reassure customers and build trust.
- Empathy: Empathy involves understanding and sharing the feelings of others, including customers. Being empathetic means actively listening to their concerns, acknowledging their emotions, and showing genuine compassion. This helps customers feel heard and understood, leading to more positive experiences.
- Clear Communication: Effective communication is key to providing good customer service. It involves conveying information clearly and concisely, avoiding jargon or technical language that may confuse customers. Providing accurate and relevant information helps customers make informed decisions and resolves issues more efficiently.
- Problem-Solving Skills: Good customer service representatives are adept at identifying and resolving customer issues and complaints. They approach problems with a positive attitude, remain calm under pressure, and use creative problem-solving techniques to find solutions that satisfy customers’ needs.
- Product Knowledge: Having a deep understanding of the products or services being offered is crucial for delivering excellent customer service. Knowledgeable representatives can answer questions, provide recommendations, and offer valuable insights to help customers make informed choices. Continuous training and education ensure that representatives stay updated on product features, updates, and best practices.
- Professionalism: Professionalism involves maintaining a courteous and respectful demeanor at all times, regardless of the situation. This includes being punctual, following through on commitments, and maintaining confidentiality when handling sensitive information. Professional behavior builds credibility and trust with customers.
- Proactive Engagement: Anticipating and addressing customer needs before they become problems is a hallmark of good customer service. Proactive engagement involves reaching out to customers to gather feedback, offer assistance, or provide updates. By being proactive, companies can demonstrate their commitment to customer satisfaction and build stronger relationships.
By embodying these qualities, businesses can deliver exceptional customer service experiences that not only meet but exceed customer expectations, leading to increased satisfaction, loyalty, and advocacy.
FAQs
What are RF/microwave package substrates?
RF/microwave package substrates are specialized materials used as the base for packaging and interconnecting electronic components operating at radio frequency (RF) and microwave frequencies. They provide the foundation for building high-frequency circuits and systems, ensuring optimal electrical performance.
What are the key characteristics of RF/microwave package substrates?
Key characteristics of RF/microwave package substrates include low dielectric loss, high thermal conductivity, excellent dimensional stability, and precise control over electrical properties such as impedance and signal integrity. These properties are essential for minimizing signal loss and distortion in high-frequency applications.
What materials are commonly used for RF/microwave package substrates?
Common materials for RF/microwave package substrates include ceramics like alumina and aluminum nitride, polymer composites such as liquid crystal polymers (LCP) and polytetrafluoroethylene (PTFE), and specialized materials like glass-reinforced epoxy (FR4) and metal substrates.
What are the applications of RF/microwave package substrates?
RF/microwave package substrates find applications in various industries, including telecommunications, aerospace, defense, automotive, medical devices, and consumer electronics. They are used in RF amplifiers, filters, antennas, transceivers, radar systems, wireless communication devices, and more.
How are RF/microwave package substrates manufactured?
The manufacturing process for RF/microwave package substrates involves several steps, including material selection, substrate preparation, circuit pattern definition, conductive traces deposition, via formation, surface finishing, assembly, and testing. Advanced fabrication techniques like photolithography, thin-film deposition, and laser processing are commonly used.
What factors should be considered when selecting RF/microwave package substrates?
When selecting RF/microwave package substrates, factors to consider include operating frequency, power handling capabilities, thermal management requirements, mechanical strength, cost considerations, and compatibility with manufacturing processes.
How can I ensure the reliability and performance of RF/microwave package substrates?
Ensuring the reliability and performance of RF/microwave package substrates involves rigorous testing, quality control measures, adherence to industry standards and specifications, and collaboration with experienced substrate manufacturers or suppliers who can provide customized solutions tailored to specific application requirements.