RF Module Packaging Substrate Manufacturer
RF Module Packaging Substrate Manufacturer,The RF module packaging substrate plays a crucial role in electronic devices by integrating RF circuits and providing a stable environment for signal transmission. These substrates typically use materials with excellent high-frequency characteristics, such as PTFE (polytetrafluoroethylene), to ensure low loss and highly reliable performance. Their design considers the requirements for RF signal transmission and electromagnetic interference suppression, often employing multilayer structures and optimized layouts to minimize signal attenuation and crosstalk. RF module packaging substrates find wide applications in wireless communication and radar systems, crucially impacting device performance and stability.
What is an RF Module Packaging Substrate?
An RF module packaging substrate is a specialized material used in the construction of radio frequency (RF) modules, which are essential components in wireless communication systems. The substrate serves as a foundation for mounting various electronic components such as integrated circuits, capacitors, and resistors that make up the RF module.
Key characteristics of an RF module packaging substrate include high thermal conductivity to dissipate heat generated during operation, excellent electrical insulation properties to prevent interference and signal loss, and mechanical stability to ensure durability under varying environmental conditions. These substrates are often made from materials like ceramic or specialized types of laminate that offer these properties.
In addition to providing a stable platform for component mounting, RF module packaging substrates also play a crucial role in maintaining signal integrity and performance. They are designed to minimize parasitic effects such as lossy dielectric properties or electromagnetic interference (EMI), which could otherwise degrade the efficiency and reliability of the RF module.
Overall, the choice of substrate material and design is critical in optimizing the performance, efficiency, and reliability of RF modules used in applications ranging from wireless communication networks to radar systems and satellite communications.
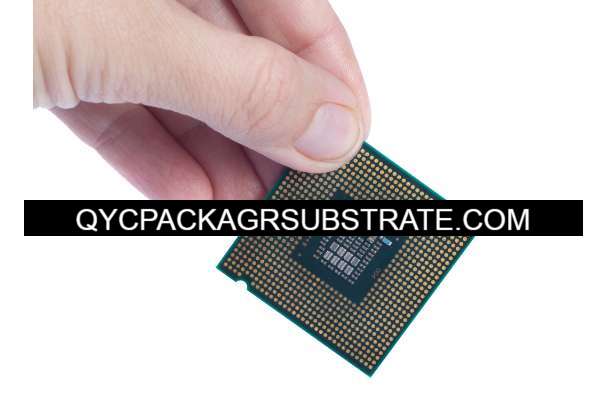
RF Module Packaging Substrate Manufacturer
What are RF Module Packaging Substrate Design Guidelines?
Designing RF module packaging substrates involves adhering to several key guidelines to ensure optimal performance and reliability in wireless communication systems. Here are some important design guidelines for RF module packaging substrates:
- Material Selection: Choose substrate materials with high thermal conductivity (to dissipate heat efficiently), excellent dielectric properties (to minimize signal loss and interference), and mechanical stability (to withstand environmental stresses). Common materials include ceramics (such as alumina and aluminum nitride) and specialized laminates (like PTFE-based materials).
- Dielectric Constant (εr) and Loss Tangent (tanδ): Select substrates with stable and predictable dielectric constants (εr) and low loss tangents (tanδ). These characteristics are crucial for maintaining signal integrity and minimizing insertion loss in RF circuits.
- Thickness Control:Ensure precise control over substrate thickness to maintain impedance matching and minimize parasitic effects. Variations in substrate thickness can affect the characteristic impedance of transmission lines and impedance matching networks.
- Surface Smoothness: Surface roughness can lead to increased signal losses and EMI. Maintain a smooth substrate surface to minimize these effects and ensure consistent RF performance.
- Via Design and Placement: Vias are used for electrical connections between different layers of the substrate. Design vias carefully to minimize inductance and impedance discontinuities. Proper via placement is crucial to avoid interference with RF signal paths and minimize parasitic capacitance.
- Thermal Management: Incorporate thermal vias or other cooling techniques to manage heat dissipation effectively, especially in high-power RF modules. Efficient thermal management helps prevent overheating and ensures long-term reliability.
- EMI Shielding: Consider integrating EMI shielding features into the substrate design to prevent electromagnetic interference from affecting sensitive RF circuits. This can include using conductive layers or coatings strategically placed within the substrate.
- Manufacturability and Reliability:Design substrates with manufacturability and reliability in mind. Ensure that the chosen materials and design can be manufactured consistently and meet performance specifications over the module’s operational lifetime.
- Testing and Validation: Perform thorough testing and validation of substrate designs to verify RF performance characteristics such as insertion loss, return loss, and impedance matching. This ensures that the substrate meets the required specifications and performs reliably in real-world applications.
By following these design guidelines, engineers can develop RF module packaging substrates that optimize performance, reliability, and efficiency in wireless communication systems. Each guideline contributes to minimizing signal loss, maintaining signal integrity, and enhancing overall system performance.
What is the RF Module Packaging Substrate Fabrication Process?
The fabrication process of RF module packaging substrates involves several critical steps to ensure the materials meet the stringent requirements of high-frequency applications in wireless communication systems:
- Material Selection: Choose appropriate substrate materials based on factors such as thermal conductivity, dielectric constant (εr), loss tangent (tanδ), and mechanical stability. Common materials include ceramics (like alumina or aluminum nitride) and specialized laminates (such as PTFE-based materials).
- Substrate Preparation: Begin with raw substrate materials in the form of sheets or panels. These materials undergo preparation steps such as cleaning and surface treatment to ensure optimal adhesion and performance of subsequent layers and coatings.
- Layer Deposition: Depending on the substrate design, layers of conductive and dielectric materials are deposited onto the substrate. Techniques such as screen printing, sputtering, or chemical vapor deposition (CVD) are used to achieve precise layer thicknesses and material properties.
- Pattern Definition: Define the required circuit patterns and features on the substrate using photolithography or similar techniques. This involves applying a photoresist layer, exposing it to UV light through a photomask, and developing the pattern to transfer circuit designs onto the substrate.
- Via Formation: Create vias (small holes) in the substrate to establish electrical connections between different layers. Vias are formed using techniques such as laser drilling or mechanical drilling followed by metallization to ensure conductivity and low impedance.
- Conductor Patterning: Define and pattern the conductive traces and pads using techniques like etching or additive processes (e.g., electroplating). This step forms the essential interconnects and transmission lines that carry RF signals throughout the module.
- Dielectric Layer Integration: Apply additional dielectric layers as needed to insulate conductive traces and provide mechanical support. These layers help maintain signal integrity, minimize crosstalk, and manage impedance characteristics within the substrate.
- Surface Finishing: Finish the substrate surfaces with coatings or finishes to improve electrical performance, such as enhancing solderability or providing EMI shielding properties. Surface finishes may include immersion gold, OSP (Organic Solderability Preservative), or ENIG (Electroless Nickel Immersion Gold).
- Quality Assurance and Testing: Conduct rigorous quality control checks and testing throughout the fabrication process. This includes inspecting layer thicknesses, evaluating electrical properties (e.g., impedance matching, signal integrity), and verifying dimensional accuracy to ensure compliance with design specifications.
- Packaging and Delivery: Once fabricated and tested, RF module packaging substrates are packaged according to industry standards to protect them during transport and storage. They are then delivered to assembly facilities where they are integrated into complete RF modules for use in wireless communication systems.
By following these fabrication steps with precision and attention to detail, manufacturers can produce RF module packaging substrates that meet the demanding requirements of high-frequency applications, ensuring reliable performance and durability in wireless communication technologies.
How do you manufacture an RF Module Packaging Substrate?
Manufacturing an RF module packaging substrate involves a series of meticulous steps to ensure the substrate meets the stringent requirements of high-frequency applications in wireless communication systems:
- Material Selection: Choose substrate materials based on thermal conductivity, dielectric constant (εr), loss tangent (tanδ), and mechanical stability. Common choices include ceramics (e.g., alumina, aluminum nitride) and specialized laminates (e.g., PTFE-based materials) known for their RF-friendly properties.
- Substrate Preparation: Start with raw substrate materials in sheet or panel form. Clean and treat the substrate surfaces to ensure proper adhesion and performance of subsequent layers.
- Layer Deposition: Depose conductive and dielectric materials onto the substrate using techniques like screen printing, sputtering, or chemical vapor deposition (CVD). This step forms the base layers necessary for circuitry and insulation.
- Pattern Definition: Define circuit patterns using photolithography. Apply a photoresist layer, expose it to UV light through a photomask, and develop the pattern to transfer designs onto the substrate accurately.
- Via Formation: Create vias (electrical pathways) between substrate layers for interconnectivity. Techniques such as laser drilling or mechanical drilling followed by metallization ensure vias are conductive and low impedance.
- Conductor Patterning:Pattern conductive traces and pads using etching or additive processes (e.g., electroplating). This step creates interconnects and transmission lines crucial for carrying RF signals.
- Dielectric Layer Integration: Integrate additional dielectric layers to insulate conductive traces and provide mechanical support. These layers safeguard signal integrity, reduce crosstalk, and manage impedance.
- Surface Finishing: Apply surface finishes like immersion gold, OSP (Organic Solderability Preservative), or ENIG (Electroless Nickel Immersion Gold) to enhance electrical performance and solderability. Optionally, apply EMI shielding coatings.
- Quality Assurance and Testing: Conduct thorough quality checks throughout fabrication. Inspect layer thickness, evaluate electrical properties (e.g., impedance, signal integrity), and verify dimensions against specifications to ensure consistency and reliability.
- Packaging and Delivery: Package substrates according to industry standards to protect them during transport and storage. Deliver to assembly facilities where they are integrated into complete RF modules for wireless communication systems.
By meticulously following these steps, manufacturers can produce RF module packaging substrates that meet demanding requirements for performance, reliability, and durability in wireless communication applications. Each stage—from material selection to quality control—plays a crucial role in ensuring substrates perform optimally in high-frequency environments.
How much should an RF Module Packaging Substrate cost?
The cost of an RF module packaging substrate can vary significantly depending on several factors:
- Material Type: Different substrate materials have varying costs. For example, ceramic substrates like alumina or aluminum nitride tend to be more expensive than organic laminates due to their superior electrical and thermal properties.
- Complexity of Design: Substrates with intricate designs, multiple layers, fine pitch features, and high-density interconnects require more advanced manufacturing techniques and may incur higher costs.
- Size and Thickness: Larger substrates or those with specific thickness requirements can affect material usage and manufacturing complexity, thereby influencing the overall cost.
- Quality Requirements: Higher quality standards, such as tighter tolerances, stringent electrical performance characteristics (e.g., low insertion loss, precise impedance control), and reliability standards (e.g., thermal cycling resistance), can increase costs due to additional testing and manufacturing precision.
- Volume and Manufacturing Scale: Economies of scale apply in substrate manufacturing. Larger production volumes generally lead to lower per-unit costs as fixed costs are spread across more units.
- Supplier and Geographical Location: Costs can vary based on the supplier, their expertise, and geographical location. Local suppliers may have different cost structures compared to international ones.
- Additional Features: Optional features such as EMI shielding coatings, specific surface finishes (e.g., gold plating), or custom packaging can add to the substrate cost.
To provide a rough estimate, RF module packaging substrates can range from a few dollars for simple designs in standard materials to tens or even hundreds of dollars per substrate for complex designs with high-performance requirements. It’s common for manufacturers to request quotes based on specific design requirements and quantities to get an accurate cost estimation tailored to their needs.
What is RF Module Packaging Substrate base material?
The base materials used for RF module packaging substrates are chosen for their electrical, thermal, and mechanical properties that are critical for high-frequency applications. The most commonly used base materials include:
- Ceramics: Ceramics such as alumina (Al2O3) and aluminum nitride (AlN) are popular choices due to their excellent electrical insulation properties, high thermal conductivity, and mechanical stability. Alumina is widely used for its relatively lower cost and good electrical properties, while aluminum nitride offers higher thermal conductivity, making it suitable for applications requiring efficient heat dissipation.
- Laminates: Laminates are another category of base materials that include various types of substrates composed of layers of fiberglass (FR4), polytetrafluoroethylene (PTFE, commonly known as Teflon), and other resin materials reinforced with glass or aramid fibers. These materials offer flexibility in design, ease of processing, and can be tailored for specific dielectric constants and loss tangents.
- Metals: In some specialized applications, metal substrates such as copper-clad laminates or metal-backed substrates may be used. These substrates provide excellent thermal conductivity but require careful consideration of electrical insulation and impedance control.
Each type of base material offers distinct advantages and is selected based on the specific requirements of the RF module, including frequency of operation, power handling capabilities, thermal management needs, and cost considerations. The choice of base material significantly impacts the overall performance, reliability, and cost of RF module packaging substrates in wireless communication systems.
Which company makes RF Module Packaging Substrates?
Manufacturing RF module packaging substrates involves several companies, including internationally renowned electronic materials manufacturers and specialized packaging solution providers. These companies utilize their technological expertise and manufacturing capabilities to produce high-performance packaging substrates for various applications in wireless communication systems.
In this field, major suppliers include Murata, Rogers Corporation, TTM Technologies, DuPont, and Mitsubishi Electric in Japan. They leverage advanced materials science, manufacturing techniques, and packaging design experience to develop and manufacture packaging substrates that meet the requirements of high-frequency applications.
Our company, as a manufacturer of packaging substrates, also produces high-quality RF module packaging substrates for wireless communication systems. We possess advanced production equipment and a professional technical team capable of manufacturing various types of packaging substrates, including:
- Ceramic Substrates: We use high-purity ceramic materials such as alumina (Al2O3) and aluminum nitride (AlN), which offer excellent electrical insulation properties and high thermal conductivity, suitable for applications requiring effective thermal management in high-frequency environments.
- Laminates: We specialize in using various laminate materials, such as FR4 fiberglass laminates and PTFE-based laminates (e.g., Teflon materials), allowing us to adjust dielectric constants and loss tangents according to customer requirements.
- Metal Substrates: For specialized applications requiring high thermal conductivity, we also provide copper-clad laminates or metal-backed substrates to ensure superior thermal management and electrical performance.
We prioritize product quality and customer satisfaction, ensuring that our RF module packaging substrates meet industry standards and technical requirements through rigorous quality control and continuous technological innovation. Our team has extensive experience and expertise in design, manufacturing, and testing, providing excellent support and service throughout the product lifecycle.
In summary, as a manufacturer of RF module packaging substrates, we are committed to delivering high-quality, reliable products that enable our customers to achieve outstanding performance and stable operation in wireless communication systems.
What are the 7 qualities of good customer service?
Good customer service is characterized by several key qualities that contribute to a positive experience for customers. Here are seven essential qualities:
- Responsiveness: Responding promptly to customer inquiries, concerns, or requests is crucial. Customers appreciate timely assistance and feel valued when their needs are addressed promptly.
- Empathy: Showing empathy means understanding and acknowledging the customer’s feelings and perspectives. Empathetic responses demonstrate care and build rapport, even in challenging situations.
- Clarity: Communication should be clear, concise, and easily understood. Providing accurate information and avoiding jargon or confusion helps customers make informed decisions and feel confident in the service provided.
- Patience: Dealing with customer issues often requires patience, especially when customers are frustrated or confused. Patient interactions help defuse tension and lead to more effective problem-solving.
- Consistency:Consistency in service delivery across all interactions and channels is essential. Customers expect a reliable experience each time they engage with a company, whether in person, over the phone, or online.
- Professionalism: Maintaining professionalism means handling interactions with courtesy, respect, and integrity. Professional behavior builds trust and reflects positively on the company’s image.
- Resourcefulness: Being resourceful involves finding solutions and offering alternatives when standard procedures may not suffice. Resourceful service providers are proactive in resolving issues and meeting customer needs effectively.
By embodying these qualities, companies can foster strong relationships with customers, enhance satisfaction levels, and build a reputation for excellent customer service.
FAQs
What are the common applications of RF Module Packaging Substrates?
RF Module Packaging Substrates are used in wireless communication devices, radar systems, satellite communication systems, and various RF applications.
How can I ensure the reliability of RF Module Packaging Substrates?
Ensuring reliable RF Module Packaging Substrates involves adhering to strict fabrication standards, testing for signal integrity and RF performance, and using high-quality materials.
What are some challenges in designing RF Module Packaging Substrates?
Challenges include managing electromagnetic interference (EMI), maintaining impedance control, optimizing thermal management, and ensuring compatibility with high-frequency signals.
What are the environmental considerations in RF Module Packaging Substrate production?
Environmental considerations include the choice of materials (recyclability and sustainability), compliance with regulations (such as RoHS), and minimizing waste during manufacturing processes.
What are RF module packaging substrates?
RF module packaging substrates are specialized materials used as the foundation for mounting electronic components in radio frequency (RF) modules. These substrates are crucial for maintaining signal integrity, managing thermal dissipation, and supporting reliable operation in wireless communication systems.
What materials are commonly used for RF module packaging substrates?
Common materials include ceramics such as alumina (Al2O3) and aluminum nitride (AlN), known for their high thermal conductivity and excellent electrical properties. Laminates, including FR4 and PTFE-based materials like Teflon, are also used for their flexibility and dielectric properties.