RF Modules Substrate Manufacturer
RF Modules Substrate Manufacturer, We offer The RF packaging Substrate from 2 layer to 22 layers,Microtrace and spacing, We will produce such substrates according to the materials you require.
RF module substrates are physical materials or boards used to support and integrate radio frequency (RF) components. They are crucial components in wireless communication systems, housing RF amplifiers, filters, oscillators, antennas, and more. These substrates must possess excellent electrical properties to ensure efficient transmission and reception of RF signals, especially across high-frequency ranges. Common materials for RF module substrates include specialized laminates (such as Rogers, Duroid), ceramics, and semiconductor materials like gallium arsenide (GaAs) or gallium nitride (GaN). Designing and manufacturing RF module substrates involve multiple processes, including material selection, circuit pattern design, metallization, via formation, layer stacking, and surface treatments. High-quality RF module substrates offer stable and reliable performance, supporting the transmission of RF signals across various frequencies, thus playing a critical role in the seamless operation of wireless communication systems.
What is an RF Modules Substrate?
An RF (Radio Frequency) module substrate refers to the physical material or board on which radio frequency components, such as amplifiers, filters, oscillators, and antennas, are mounted or integrated. These substrates are designed to facilitate the transmission and reception of radio frequency signals with minimal interference or signal loss.
RF module substrates are typically made from materials with properties suitable for high-frequency applications, such as ceramics, specialized laminates, or semiconductor materials like gallium arsenide (GaAs) or gallium nitride (GaN). These materials offer characteristics like low dielectric loss, high thermal conductivity, and good electrical insulation to ensure optimal performance of the RF components.
The design and choice of substrate material are critical in RF module development, as they can significantly impact the module’s efficiency, reliability, and performance in terms of signal transmission, reception, and interference rejection.
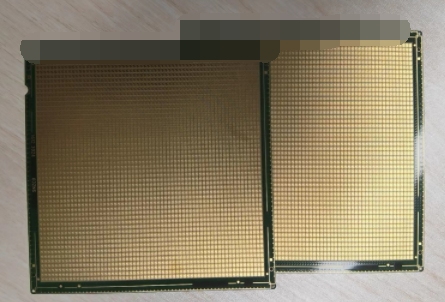
RF Modules Substrate
What are the RF Modules Substrate Design Guidelines?
Designing RF module substrates involves several guidelines to ensure optimal performance. Here are some key considerations:
- Substrate Material Selection: Choose a substrate material with properties suitable for RF applications, such as low dielectric loss, high thermal conductivity, and good electrical insulation. Common substrate materials include ceramic, specialized laminates (e.g., Rogers, Duroid), and semiconductor materials like GaAs or GaN.
- Dielectric Constant (εr): The substrate’s dielectric constant affects the propagation speed of RF signals. It’s crucial to select a substrate with a consistent dielectric constant to maintain signal integrity and minimize impedance mismatch.
- Substrate Thickness: The substrate thickness impacts the characteristic impedance of transmission lines on the board. Proper thickness selection ensures impedance matching and minimizes signal loss.
- Transmission Line Geometry: Design transmission lines (e.g., microstrip, stripline) with appropriate dimensions and spacing to achieve the desired impedance and minimize losses. Pay attention to trace width, spacing, and via placement.
- Grounding: Implement proper grounding techniques to minimize ground loops and reduce electromagnetic interference (EMI). Use solid ground planes and strategically place vias to connect ground layers.
- Component Placement: Place RF components carefully to minimize signal path lengths, reduce parasitic capacitance and inductance, and optimize signal integrity. Consider the RF module’s overall layout and the placement of critical components like amplifiers, filters, and antennas.
- Heat Dissipation: Ensure effective heat dissipation to prevent overheating of RF components, which can degrade performance and reliability. Use thermal vias and thermal pads to conduct heat away from hotspots.
- Isolation and Crosstalk: Maintain adequate isolation between RF traces and components to prevent crosstalk and interference. Proper spacing and shielding techniques help minimize signal coupling between adjacent traces.
- Manufacturability: Consider manufacturability aspects such as substrate material availability, fabrication processes, and cost-effectiveness during substrate design. Optimize the design for ease of assembly and testing.
- Simulation and Prototyping: Use electromagnetic simulation software to model and analyze RF substrate designs before fabrication. Prototyping and testing are essential to validate the design’s performance and make necessary adjustments.
By following these guidelines, designers can develop RF module substrates that meet the performance requirements for various wireless communication applications.
What is the RF Modules Substrate Fabrication Process?
The fabrication process for RF module substrates involves several steps to produce a board or substrate capable of supporting RF components and facilitating efficient signal transmission. Here’s an overview of the typical fabrication process:
- Design and Layout: The process begins with the design and layout of the RF module substrate using electronic design automation (EDA) software. Designers create a layout that includes the placement of RF components, transmission lines, vias, and grounding structures based on the design requirements and guidelines.
- Substrate Material Selection: Choose a substrate material suitable for RF applications, such as specialized laminates (e.g., Rogers, Duroid), ceramic, or semiconductor materials like gallium arsenide (GaAs) or gallium nitride (GaN). The choice of material depends on factors such as dielectric constant, thermal conductivity, and cost.
- Preparation of Substrate Material: The selected substrate material is prepared for fabrication by cutting it to the required size and shape. This step may involve processes such as cutting, drilling, or machining to achieve the desired dimensions and surface finish.
- Surface Preparation: The substrate surface is cleaned and prepared to ensure proper adhesion of the circuitry and components. Surface preparation may involve processes such as degreasing, etching, or surface roughening.
- Circuit Patterning: Circuitry patterns, including transmission lines, pads, and vias, are created on the substrate surface using techniques such as photolithography, screen printing, or chemical etching. These patterns define the electrical connectivity and layout of the RF module.
- Metallization: Metal deposition is performed to create conductive traces and pads on the substrate surface. Common metals used for RF applications include copper, gold, and silver. Metal deposition techniques may include sputtering, electroplating, or evaporation.
- Etching and Cleaning: Excess metal is removed from the substrate surface through etching processes, leaving behind the desired circuitry patterns. The substrate is then cleaned to remove any residues or contaminants that may affect performance.
- Via Formation: Vias, which provide electrical connections between different layers of the substrate, are created using drilling or laser ablation techniques. The vias are plated with metal to ensure conductivity between layers.
- Layer Stacking and Lamination: Multiple substrate layers may be stacked and laminated together to create a multi-layered RF module substrate. Lamination bonds the layers together under heat and pressure, forming a unified structure.
- Surface Finish: The substrate surface may undergo additional finishing processes, such as solder mask application, surface coating, or surface treatment, to enhance performance, protect against corrosion, and improve solderability.
- Quality Control and Testing: The fabricated RF module substrate undergoes quality control inspections and testing to ensure compliance with design specifications and performance requirements. Testing may include checks for dimensional accuracy, electrical continuity, impedance matching, and signal integrity.
Once the RF module substrate has been fabricated and tested, it is ready for the assembly of RF components such as amplifiers, filters, antennas, and integrated circuits to create a complete RF module for use in wireless communication systems.
How do you manufacture RF Modules Substrate?
Manufacturing RF module substrates involves a series of specialized processes to create the necessary circuitry and structure to support RF components. Here’s a more detailed explanation of how RF module substrates are manufactured:
- Substrate Material Selection: Choose a substrate material suitable for RF applications based on factors such as dielectric constant, thermal conductivity, and cost. Common substrate materials include specialized laminates (e.g., Rogers, Duroid), ceramic, or semiconductor materials like gallium arsenide (GaAs) or gallium nitride (GaN).
- Preparation of Substrate Material: Prepare the substrate material for fabrication by cutting it to the required size and shape. This step may involve processes such as cutting, drilling, or machining to achieve the desired dimensions and surface finish.
- Cleaning and Surface Preparation: Clean the substrate surface to remove any contaminants that could affect adhesion or performance. Surface preparation may involve processes such as degreasing, etching, or surface roughening to improve bonding.
- Circuit Patterning: Create circuitry patterns on the substrate surface using techniques such as photolithography, screen printing, or chemical etching. These patterns define the layout of transmission lines, pads, and vias on the substrate.
- Metallization: Deposit metal onto the substrate surface to create conductive traces and pads. Common metals used for RF applications include copper, gold, and silver. Metal deposition techniques may include sputtering, electroplating, or evaporation.
- Etching and Cleaning: Remove excess metal from the substrate surface through etching processes, leaving behind the desired circuitry patterns. The substrate is then cleaned to remove any residues or contaminants that may affect performance.
- Via Formation: Create vias, which provide electrical connections between different layers of the substrate. Vias are typically formed using drilling or laser ablation techniques, followed by metal plating to ensure conductivity between layers.
- Layer Stacking and Lamination: Stack multiple substrate layers together to create a multi-layered structure if needed. Lamination bonds the layers together under heat and pressure, forming a unified substrate.
- Surface Finish:Apply surface finishes such as solder mask, surface coating, or surface treatment to enhance performance, protect against corrosion, and improve solderability.
- Quality Control and Testing: Inspect and test the fabricated RF module substrate to ensure compliance with design specifications and performance requirements. Testing may include checks for dimensional accuracy, electrical continuity, impedance matching, and signal integrity.
Once the RF module substrate has been manufactured and tested, it is ready for the assembly of RF components such as amplifiers, filters, antennas, and integrated circuits to create a complete RF module for use in wireless communication systems.
How much should RF Modules Substrate cost?
The cost of RF module substrates can vary widely depending on several factors, including the substrate material, manufacturing complexity, size, and quantity. Here are some considerations that can influence the cost:
- Substrate Material: Different substrate materials have varying costs. For example, specialized laminates like Rogers or Duroid tend to be more expensive than standard FR-4. Semiconductor materials like GaAs or GaN can also be costly due to their specialized properties.
- Manufacturing Complexity: The complexity of the fabrication processes involved in creating the substrate, such as circuit patterning, metallization, and via formation, can impact the cost. More complex designs with finer features or multiple layers may require additional manufacturing steps and resources, increasing the cost.
- Size and Thickness: The size and thickness of the substrate can affect the material usage and manufacturing time, thus influencing the overall cost. Larger or thicker substrates may require more material and processing, leading to higher costs.
- Quantity: Economies of scale often apply in manufacturing, meaning that larger production quantities can lead to lower per-unit costs. Ordering substrates in bulk may result in volume discounts from manufacturers.
- Quality Requirements: Higher quality substrates with tighter tolerances and performance specifications may command a premium price compared to standard-grade substrates. Meeting stringent quality standards may require additional testing and quality control measures, contributing to the overall cost.
- Customization and Special Features: Customized substrates with specific design requirements or additional features, such as embedded passive components or integrated heat sinks, may incur additional costs compared to standard off-the-shelf substrates.
- Supplier and Location: The choice of substrate supplier and manufacturing location can also influence costs. Suppliers with advanced fabrication capabilities or located in regions with lower labor and production costs may offer more competitive pricing.
Given these factors, it’s challenging to provide a specific cost range for RF module substrates without knowing the specific requirements of the project. However, it’s common for RF module substrates to range in cost from a few dollars to several hundred dollars per unit, depending on the factors mentioned above. Companies involved in RF module design and manufacturing typically work closely with substrate suppliers to optimize costs while meeting performance and quality requirements.
What is RF Modules Substrate base material?
The choice of base material for RF module substrates depends on various factors such as frequency range, performance requirements, and cost considerations. Here are some common base materials used for RF module substrates:
- Specialized Laminates (e.g., Rogers, Duroid): These laminates are composed of woven fiberglass cloth impregnated with epoxy resin and reinforced with ceramic or PTFE (Polytetrafluoroethylene) fillers. They offer excellent electrical properties, low dielectric loss, and stable performance over a wide frequency range. Rogers and Duroid are popular brands known for their high-frequency PCB materials suitable for RF and microwave applications.
- FR-4 (Fire-Resistant 4): FR-4 is a widely used substrate material for general-purpose PCBs. It consists of woven fiberglass cloth impregnated with epoxy resin. While not specifically designed for RF applications, FR-4 can be suitable for lower frequency RF modules or applications with less stringent performance requirements due to its lower cost and availability.
- Ceramic: Ceramic substrates, such as alumina (Al2O3) or aluminum nitride (AlN), offer excellent thermal conductivity, high electrical insulation, and stability over a wide temperature range. Ceramic substrates are often used in high-power RF applications, microwave circuits, and applications requiring superior thermal management.
- Semiconductor Materials (e.g., GaAs, GaN): Gallium arsenide (GaAs) and gallium nitride (GaN) are semiconductor materials used in RF and microwave applications, particularly in high-frequency power amplifiers and RF integrated circuits (RFICs). These materials offer high electron mobility and are suitable for high-frequency operation.
The choice of base material depends on factors such as operating frequency, power requirements, thermal considerations, and cost constraints. Designers often select the substrate material that best balances performance, manufacturability, and cost for a given RF module application. Additionally, substrate materials may undergo further processing, such as metallization and surface treatments, to enhance their RF performance and reliability.
Which company makes RF Modules Substrate?
Many companies produce RF module substrates, and some of them are industry leaders. For example, Rogers Corporation, DuPont, Taconic Advanced Dielectric Division, Isola Group, and Mitsubishi Electric have extensive experience and reputation in the RF and microwave application fields. These companies offer various types of substrate materials, including special coatings, ceramics, and semiconductor materials, to meet different frequency ranges and performance requirements.
As an RF module manufacturer, our company is also capable of producing RF module substrates. We have advanced manufacturing equipment and a professional technical team capable of designing and manufacturing high-quality RF module substrates that meet customer requirements. Our manufacturing process strictly follows industry standards to ensure product quality and stable performance. We can also customize substrate materials, sizes, layers, and surface treatments according to specific customer requirements, providing tailored solutions to customers.
In terms of RF module substrate manufacturing, our company focuses on technological innovation and quality management, continuously improving production efficiency and product performance to meet customers’ changing needs. We work closely with customers, actively participating in various stages of projects from requirements analysis to design and development, production, and quality control, ensuring that the final products meet customer expectations and exceed their expectations. We are committed to providing customers with high-performance, high-reliability RF module substrates to support their wireless communication applications.
What are the 7 qualities of good customer service?
Good customer service is essential for building positive relationships with customers and fostering loyalty. Here are seven qualities of good customer service:
- Responsiveness: Customers appreciate prompt responses to their inquiries, whether it’s through phone calls, emails, or live chat. Being responsive shows that you value their time and are committed to addressing their needs promptly.
- Empathy: Empathy involves understanding and acknowledging the customer’s feelings and concerns. It’s important to listen actively, show empathy, and demonstrate that you genuinely care about resolving their issues or addressing their questions.
- Clear Communication: Effective communication is key to providing good customer service. Clearly explain products, services, policies, and procedures in a way that is easy for customers to understand. Avoid jargon and technical language when communicating with customers.
- Problem-Solving Skills: Good customer service representatives are adept at identifying and solving problems. They actively seek solutions to customer issues, whether it involves troubleshooting technical problems, addressing billing discrepancies, or resolving complaints.
- Positive Attitude: Maintaining a positive attitude, even in challenging situations, can help diffuse tensions and create a more pleasant interaction for customers. A friendly demeanor, along with a willingness to help, can go a long way in providing good customer service.
- Knowledgeability: Customers expect customer service representatives to have a thorough understanding of products, services, and company policies. Being knowledgeable allows representatives to answer questions accurately, provide helpful recommendations, and offer valuable assistance.
- Consistency: Consistency is crucial for building trust and reliability. Customers should receive the same level of service and attention regardless of the channel they use to interact with your company—whether it’s in person, over the phone, via email, or through social media.
By embodying these qualities, businesses can deliver exceptional customer service experiences that leave customers satisfied and eager to return.
FAQs
What is an RF module substrate?
An RF module substrate is the physical material or board on which radio frequency components, such as amplifiers, filters, oscillators, and antennas, are mounted or integrated. It provides the foundation for building RF modules used in wireless communication systems.
What are the key characteristics of a good RF module substrate?
A good RF module substrate should have properties such as low dielectric loss, high thermal conductivity, excellent electrical insulation, and stable performance over a wide frequency range. It should also support precise circuitry patterns and provide reliable interconnections between components.
What materials are commonly used for RF module substrates?
Common materials used for RF module substrates include specialized laminates (e.g., Rogers, Duroid), ceramics, and semiconductor materials like gallium arsenide (GaAs) or gallium nitride (GaN). The choice of material depends on the specific application requirements and performance considerations.
How are RF module substrates manufactured?
The manufacturing process for RF module substrates involves steps such as substrate material preparation, circuit patterning, metallization, via formation, layer stacking, lamination, surface finishing, and quality control testing. These processes are performed to create a substrate capable of supporting RF components and facilitating efficient signal transmission.
What factors should be considered when selecting an RF module substrate?
Factors to consider when selecting an RF module substrate include operating frequency, power requirements, thermal management needs, signal integrity considerations, cost constraints, and manufacturability. It’s essential to choose a substrate that meets the specific requirements of the RF module design and application.
How can I optimize the performance of RF modules using substrates?
Optimizing the performance of RF modules involves careful substrate design, component placement, transmission line routing, grounding techniques, and thermal management strategies. Employing advanced simulation tools, conducting thorough testing, and collaborating with experienced substrate manufacturers can help achieve optimal RF module performance.
What are some common challenges in working with RF module substrates?
Common challenges in working with RF module substrates include impedance matching issues, signal loss, electromagnetic interference (EMI), thermal management challenges, and manufacturability constraints. Addressing these challenges requires careful design consideration, testing, and collaboration between design engineers and substrate manufacturers.