Rigid-flex BGA substrate Provider. we can produce the best samllest bump pitch with 100um, the best smallest trace are 9um. and the smallest gap are 9um. most of the design are 15um to 30um trace and spacing.
Rigid-flex BGA Substrate: a type of printed circuit board (PCB) commonly employed in electronic devices. This PCB seamlessly integrates rigid and flexible materials.
The “rigid” component is crafted from a sturdy and inflexible material, usually the FR4 substrate. In contrast, the “flex” section utilizes a flexible polyimide material.
BGA, a surface-mount packaging for integrated circuits, employs solder balls for IC-PCB connections. By combining BGA technology with a rigid-flex design, a more adaptable and space-efficient PCB layout is achieved. This proves especially advantageous in electronic devices with spatial constraints, requiring the PCB to conform to irregular surfaces.
Applications of Rigid-flex BGA substrates span various electronic devices, encompassing smartphones, wearables, medical devices, and compact electronic gadgets. The PCB’s flexibility enables it to bend and adapt to the device’s contours, fostering inventive and space-saving electronic designs.
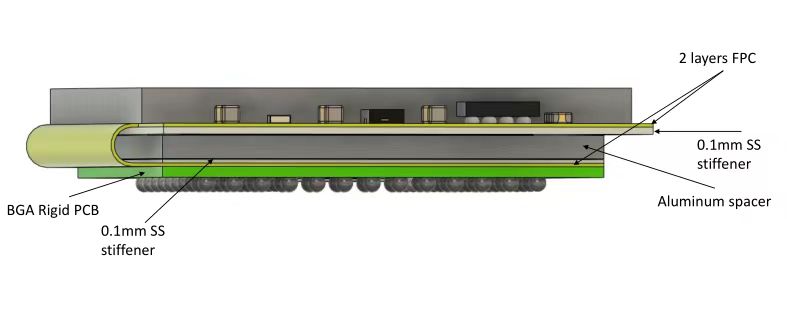
What is the Functionality of Rigid-flex BGA Substrate?
Rigid-flex BGA Substrate stands out as a versatile powerhouse in the realm of electronic components, demonstrating adaptability and efficiency in applications that prioritize flexibility and compact design. Let’s delve into its key functionalities:
Dynamic Flexibility at the Core: The pliable nature of its flexible segment enables seamless integration with devices, especially beneficial for unconventional shapes or curved surfaces where traditional rigid PCBs may encounter limitations.
Spatial Optimization in Action: The harmonious interplay of rigid and flexible elements ensures the judicious use of space within electronic devices. This proves particularly advantageous in the realm of compact gadgets and wearables, where spatial constraints demand a strategic approach to spatial utilization.
Incorporation of BGA Technology: The infusion of BGA technology ensures a high-density interconnection of integrated circuits (ICs) on the substrate. The utilization of BGA’s solder ball connections provides a compact and reliable solution, significantly contributing to the ongoing trend of downsizing electronic components.
Adaptability in Design: Rigid-flex BGA substrates showcase a commendable degree of adaptability to diverse form factors and design specifications. The availability of customization options empowers designers to tailor the substrate to the unique shapes and sizes of devices, fostering a culture of creativity and innovation in electronic product designs.
Dependable Connections as a Cornerstone: The strategic use of solder ball connections within BGA technology elevates the overall dependability of connections between ICs and the substrate. This dependability is not just a feature but a cornerstone, ensuring sustained optimal performance and durability in electronic devices.
Wide-reaching Applications Across Industries: From smartphones and wearables to medical devices and an array of compact electronic gadgets, Rigid-flex BGA substrates assert their versatility. They effectively meet the diverse and intricate demands of electronic applications across various industries.
In essence, the functionality of Rigid-flex BGA Substrate is a testament to its prowess in providing a pliable, spatially efficient, and reliable platform for seamlessly integrating electronic components. This capability positions it as a crucial player in addressing the ever-evolving design landscape of contemporary electronic devices.
What are the Different Types of Package Substrate?
In the realm of electronic packaging, a rich tapestry of package substrates unfolds, providing the essential canvas for the mounting and interconnection of semiconductor devices. Let’s explore the diverse textures within this fabric, each substrate weaving its unique pattern into the design landscape:
Printed Circuit Board (PCB): A stalwart in electronics, PCBs form a robust foundation with materials like FR4, offering a stable platform for the intricate dance of mounting and interconnecting various components.
Ceramic Substrates: For applications where the spotlight is on efficient heat dissipation, ceramic substrates, crafted from materials like alumina or aluminum nitride, take center stage, especially in the realm of power devices.
Organic Substrates: Woven from organic fibers like BT or FR4, these substrates navigate the delicate balance between cost-effectiveness, performance, and manufacturing simplicity, finding their niche in the symphony of consumer electronics.
Leadframe Substrates: A choreography of metal sheets with integrated leads, leadframe substrates provide a reliable structure, gracefully supporting semiconductor devices encased in plastic.
Copper Substrates: Tailored for applications demanding the fluidity of thermal conductivity, copper substrates pirouette through the world of power electronics and illuminate the stage of LED applications.
Ceramic Multilayer Substrates: Unfurling layers of ceramic material with interlayer conductive traces, these substrates create a mosaic of high density, catering to the intricate brushstrokes of advanced circuit designs.
Liquid Crystal Polymer (LCP) Substrates: With a virtuoso performance in electrical properties, low moisture absorption, and resilience to high temperatures, LCP substrates take the lead in the high-frequency cadence of electronic designs.
Flex Substrates: Embracing a ballet of flexibility through materials like polyimide, these substrates pirouette gracefully, adding a layer of adaptability to electronic designs, particularly in applications that demand conformity to non-flat surfaces.
System-in-Package (SiP) Substrates: Pioneering the art of integration, SiP substrates choreograph a seamless fusion of diverse components – from chips to passive elements – into a harmonious package, ushering in an era of compact and highly integrated electronic ensembles.
Glass Substrates: Exhibiting the precision and stability of a finely tuned performance, glass substrates take center stage in applications like sensors and display technologies, where the precision of every movement is imperative.
The selection of a specific package substrate involves a nuanced ballet, where factors such as application requirements, thermal considerations, electrical performance, and cost dynamics dance together. This diverse ensemble of substrates caters to the intricate needs of industries spanning consumer electronics, automotive applications, and the expansive canvas of industrial settings.
How are Package Substrate and IC Packaging Related?
Package substrate and IC (Integrated Circuit) packaging engage in a harmonious dance within the intricate landscape of semiconductor devices, orchestrating a seamless integration and ensuring the peak performance of electronic components. Let’s explore the intricate choreography between these two indispensable elements:
Architectural Pillars:
Package Substrate: Serving as the architectural backbone, the package substrate provides a robust stage for mounting and interconnecting a myriad of components, including the pivotal IC.
IC Packaging: Nestled within the confines of IC packaging, the integrated circuit finds its sanctuary. The packaging encapsulates an ensemble of chips and components, shielding them from the external elements.
Conductive Ballet:
Package Substrate: Carving pathways for connectivity, the substrate, often in the guise of a printed circuit board (PCB), hosts an intricate ballet of wiring. This intricate dance facilitates communication among diverse components, orchestrating a symphony that includes the IC.
IC Packaging: Internally, the IC packaging conducts its own ballet, choreographing connections through wire bonds or flip-chip configurations. This dance ensures the fluid movement of signals and data within the integrated circuit.
Thermal Pas de Deux:
Package Substrate: Some substrates, like ceramic or metal-core PCBs, gracefully join the thermal pas de deux. They play a crucial role in dissipating heat, a key consideration in applications where thermal management is in the spotlight.
IC Packaging: In tandem, IC packaging takes the lead in the thermal ballet. Features like heat sinks or thermal pads are elegantly incorporated, waltzing with the task of dissipating heat generated during the IC’s performance.
Protective Ensemble:
Package Substrate: The substrate dons the role of a protective ensemble, shielding mounted components from the elements—be it the gentle drizzle of moisture, the gusts of dust, or the pressures of physical stress.
IC Packaging: Elevating protection to an art form, IC packaging encapsulates delicate semiconductor elements within a resilient casing. This protective ensemble enhances durability and fortifies against the influences of the external world.
Form Factor Waltz:
Package Substrate: The design and form factor of the substrate set the stage for the overall aesthetics, determining the size and shape of the electronic device. The options span from the rigidity of traditional forms to the flexibility of innovative hybrids.
IC Packaging: The choice of IC packaging partners in the waltz, introducing variations such as surface-mount packages or the intimate embrace of chip-on-board configurations. This dance shapes the integration possibilities within the intricate ensemble of electronic systems.
In essence, the collaboration between package substrate and IC packaging is a ballet, a symphony of movements ensuring the coherence and reliability of semiconductor devices. The substrate establishes the stage, both physically and electrically, while IC packaging encapsulates and guards the integrated circuit, fostering optimal functionality across the diverse melodies of electronic applications.
What are the Differences Between Rigid-flex BGA Substrate and Traditional PCB?
Rigid-flex BGA substrates and traditional PCBs embark on divergent journeys within the intricate realm of electronic design, each weaving its narrative through unique attributes in structure, flexibility, and application versatility. Let’s delve into a comparative exploration, unveiling the distinct features that set them apart:
Architectural Fusion:
Rigid-flex BGA Substrate: Conducting a symphony of fusion, the Rigid-flex BGA substrate elegantly blends rigidity and flexibility. Rigid segments provide a stable foundation for components like Ball Grid Array (BGA) packages, while the flexible counterparts introduce a dynamic dimension, allowing the substrate to gracefully adapt and conform.
Traditional PCB: In contrast, traditional PCBs adhere to a steadfast structure, composed predominantly of rigid materials like fiberglass. Their rigidity confines them to applications where a flat and unyielding form factor is the norm.
Flexibility Ballet:
Rigid-flex BGA Substrate: The ballet of flexibility takes center stage with Rigid-flex BGA substrates. This inherent flexibility allows them to dance with the contours of devices or enclosures, providing a canvas for unconventional shapes and form factors.
Traditional PCB: In the traditional PCB realm, rigidity defines the performance. Their lack of flexibility positions them in applications where a stable and unyielding structure is not only sufficient but optimal.
Applications Canvas:
Rigid-flex BGA Substrate: Unveiling its versatility in applications constrained by space or those demanding intricate geometries, Rigid-flex BGA substrates find expression in wearable devices, medical implants, and other compact electronic marvels.
Traditional PCB: Stepping onto the canvas of adaptability, traditional PCBs shine in scenarios where a stable and rigid foundation meets the electronic needs of consumer electronics, computer motherboards, and a diverse array of industrial equipment.
Design Choreography and Flexibility:
Rigid-flex BGA Substrate: The dance of design flexibility takes center stage with Rigid-flex BGA substrates. Engineers are empowered to choreograph intricate and compact designs, leveraging the interplay between rigid stability and flexible adaptability.
Traditional PCB: While versatile, the design palette of traditional PCBs is more restrained. They excel in orchestrating standard electronic designs that do not necessitate the graceful moves of bending or flexibility.
Manufacturing Ballet:
Rigid-flex BGA Substrate: The manufacturing journey of Rigid-flex BGA substrates unfolds as a ballet of intricacy, often involving specialized processes. The seamless integration of rigid and flexible elements demands meticulous choreography in the production realm.
Traditional PCB: In the world of traditional PCBs, manufacturing follows a classical rhythm. Well-established processes guide them through a straightforward and cost-effective production route, making them the reliable choice for standard electronic applications.
In essence, the narrative of Rigid-flex BGA substrates and traditional PCBs weaves through a tapestry of structural fusion, flexibility dynamics, application diversity, design adaptability, and manufacturing nuances. Each plays its distinct role, contributing to the symphony of electronic innovation based on the unique demands of the application at hand.
What is the Main Structure and Production Technology of Rigid-flex BGA Substrate?
The creation of Rigid-flex BGA substrates involves a meticulous process, blending rigid and flexible elements to form a specialized electronic component. Let’s delve into the main structure and production technology, traversing the key steps in their fabrication:
Material Symphony:
Rigid Components: The rigid segments of the substrate embrace traditional PCB materials, often opting for the stability of fiberglass-reinforced epoxy (FR4).
Flexible Components: In a contrasting note, the flexible sections unfold with materials like polyimide or polyester, bestowing upon the substrate the ability to gracefully bend and flex.
Design Choreography of Layers:
Engineers embark on the design journey, orchestrating the layer stackup. This intricate dance of layers determines the arrangement of rigid and flexible elements, shaping the substrate’s electrical and mechanical characteristics.
Circuit Artistry:
The circuitry takes center stage, unveiled through precision patterning on both rigid and flexible layers. Photolithography and etching processes craft the desired circuit patterns, a delicate dance of applying photoresist, exposing it to UV light, and etching away unwanted copper.
Copper Tapestry:
The substrate adorns itself with copper features, intricate traces, and vias. These copper elements weave the conductive pathways, ensuring the connectivity essential for electronic harmony.
Solder Mask Elegance:
A solder mask is applied, akin to an artist’s brush defining the canvas. This protective layer covers areas where soldering is unnecessary, creating a visual masterpiece and safeguarding the substrate.
BGA Component Ballet:
BGA components gracefully take their places on the rigid segments, guided by the precision of pick-and-place machines. The solder balls beneath these components, akin to dance shoes, await the reflow stage.
Reflow Soldering Waltz:
The assembly engages in the reflow soldering waltz. Controlled heat sweeps through, melting the solder balls, and enchanting the formation of secure solder joints that bind the BGA components to the substrate.
Integration of Flexibility:
The flexible segments join the ensemble, seamlessly integrating to bring forth the desired flexibility. This integration, whether through bonding or lamination, solidifies the union between rigid and flexible elements.
Finale: Inspection and Testing Overture:
The completed Rigid-flex BGA substrate takes its place on the stage for a grand finale. Thorough inspection and testing become the overture, ensuring that the electrical connectivity sparkles, and the mechanical integrity hits the right notes.
In essence, the production technology of Rigid-flex BGA substrates unfolds as a symphony, requiring precision, artistry, and a dance between rigid and flexible elements. This intricate dance results in versatile designs tailored for applications demanding flexibility, space efficiency, and unconventional form factors.
Expert Insights (Quotes):
Here are some expert insights or quotes related to Rigid-flex BGA substrates and electronic design:
“Rigid-flex technology represents a paradigm shift in electronic design, offering engineers the freedom to create innovative and compact devices that were once deemed impossible.” – Electronic Design Expert
“The marriage of rigid and flexible elements in Rigid-flex BGA substrates is a game-changer, enabling the seamless integration of electronics in applications where space and form factor are critical.” – Materials Scientist
“In the world of electronic design, Rigid-flex BGA substrates showcase the marriage of structural stability and design flexibility, providing a canvas for engineers to push the boundaries of innovation.” – PCB Design Specialist
“The precision required in the production of Rigid-flex BGA substrates is a testament to the evolution of manufacturing technologies. It’s a delicate dance between rigidity and flexibility, demanding expertise at every step.” – Manufacturing Engineer
“Rigid-flex technology not only solves the challenges posed by space constraints but also opens up new possibilities for creating electronic devices with unique shapes and functionalities.” – Technology Innovator
“The versatility of Rigid-flex BGA substrates is reshaping the landscape of wearables, medical devices, and other compact electronics. It’s not just about components; it’s about the harmonious integration of technology into our daily lives.” – Industry Analyst
“The design freedom offered by Rigid-flex BGA substrates is empowering engineers to think beyond traditional form factors. It’s a shift towards more organic and adaptable electronic systems.” – Researcher in Electronic Design
“As we delve into the era of IoT and miniaturization, Rigid-flex BGA substrates stand as a technological cornerstone, enabling the development of smart and interconnected devices that seamlessly blend into our environment.” – Technology Futurist
These quotes capture the essence of Rigid-flex BGA substrates in the realm of electronic design, highlighting their significance and transformative impact on innovation and manufacturing.
Conclusion
In summary, Rigid-flex BGA substrates mark a significant evolution in electronic design, bridging the rigidity of traditional PCBs with the adaptability of advanced materials. This cutting-edge technology provides engineers with a versatile solution to surmount spatial limitations and explore new realms of design flexibility. The intricate interplay between rigid and flexible elements during production results in a dynamic canvas, enabling the creation of electronic devices with distinctive shapes and functionalities.
The convergence of structural stability and design adaptability in Rigid-flex BGA substrates is reshaping industries such as wearables, medical devices, and compact electronics. It transcends conventional component integration, offering a seamlessly integrated solution for applications that prioritize unconventional form factors and versatile design.
As we navigate the era of IoT and an increasing demand for miniaturization, Rigid-flex BGA substrates emerge as a pivotal technological cornerstone. They empower the development of smart, interconnected devices that seamlessly blend into our daily lives. Beyond addressing challenges related to spatial constraints, this technology unleashes new avenues for creating electronic systems that are not only efficient but also aesthetically innovative.
In essence, the journey of Rigid-flex BGA substrates unfolds as a symphony, blending precision, design freedom, and manufacturing expertise. As electronic systems continue to evolve, these substrates stand as a testament to the dynamic nature of innovation within the realm of electronic design.