Rigid-flex BGA Substrate Supplier. the Package Substrate will be made with Showa Denko and Ajinomoto High speed materials.or other types high speed materials and high frequency materials.
A Rigid-Flex BGA substrate is a tailored circuit board that harmoniously integrates both rigid and flexible components. This unique design not only facilitates sophisticated Ball Grid Array (BGA) packaging but also imparts flexibility, thereby augmenting its adaptability for applications in restricted spaces.
This circuit board integrates both rigid and flexible materials. The rigid portion typically uses common rigid circuit board materials like FR-4, providing structural support and stability. The flexible part employs materials such as polyimide, allowing the circuit board to bend or stretch to some extent without breaking.
The integrated structure of the Rigid-Flex BGA substrate is ideal for intricate three-dimensional electronic devices, particularly in confined spaces. Moreover, it reduces dependence on connectors and cables, improving both the reliability and spatial efficiency of the design.
Rigid-Flex BGA substrates are frequently utilized in applications with limited space requirements, including wearable devices, medical equipment, and aerospace applications. This is especially relevant in scenarios where conventional rigid circuit boards might be deemed excessively large or impractical.
Leveraging Ball Grid Array (BGA) packaging significantly broadens the capabilities of Rigid-Flex BGA substrates, especially in scenarios requiring advanced integration and miniaturization. BGA packages offer an extensive array of connections within a confined space, rendering them exceptionally suitable for contemporary electronic devices characterized by densely packed components.
What Functions Do Rigid-Flex BGA Substrates Serve
Rigid-Flex BGA substrates play a multifaceted role in electronic devices, extending beyond their conventional function as interconnectors. Tailored to accommodate the unique form factors of devices, these substrates enhance the design flexibility of compact electronic products. Key among their diverse functions are:
Supporting High-Density Integrated Circuits:
Rigid-Flex BGA substrates demonstrate a superior capability in supporting high-density integrated circuits. Through the integration of Ball Grid Array (BGA) packaging, these substrates enable the smooth incorporation of advanced electronic functionalities into confined spaces, guaranteeing an efficient utilization of available real estate.
Facilitating Flexibility for Three-Dimensional Structures:
An inherent characteristic of Rigid-Flex BGA substrates lies in their remarkable flexibility, enabling seamless adaptation to three-dimensional structures. This pliability plays a crucial role in addressing the spatial requirements of applications that demand inventive and adaptable designs.
Integrating Rigid and Flexible Regions Seamlessly:
These substrates seamlessly integrate both rigid and flexible regions on a single board. This harmonious integration ensures a balanced combination of structural stability from rigid elements and adaptability from flexible components. The removal of extra connectors and cables enhances the development of designs that are not only more reliable but also more space-efficientThis streamlined methodology minimizes potential failure points, enhancing overall reliability, and concurrently optimizing space utilization within electronic devices.
At its core, Rigid-Flex BGA substrates play a crucial role in elevating the efficiency and compactness of electronic devices. This is accomplished through their support for high-density integrated circuits, provision of flexibility for three-dimensional structures, and seamless integration of both rigid and flexible elements. These substrates are instrumental in guaranteeing a streamlined and space-efficient design for electronic components.
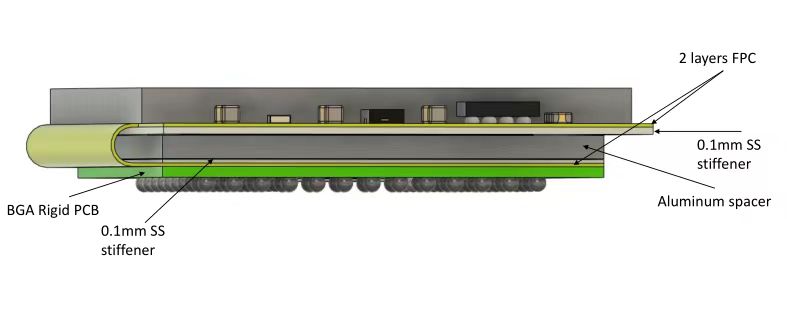
How Do Rigid-Flex BGA Substrates Differ from Traditional Substrates?
Distinguished by their distinctive structural and performance benefits, Rigid-Flex BGA substrates set themselves apart from traditional counterparts. Unlike standard rigid and flexible substrates, these substrates present a customized resolution to the challenges typically encountered by their more conventional counterparts.
An essential differentiator is their capacity to accommodate intricate three-dimensional structures. Unlike traditional substrates, be they rigid or flexible, which frequently encounter challenges in conforming to intricate device shapes, Rigid-Flex BGA substrates are intentionally crafted with a combination of rigid and flexible components. This intentional design enables them to effortlessly conform to a spectrum of device shapes, addressing the varied form factors prevalent in modern electronics.
The incorporation of Ball Grid Array (BGA) packaging further sets Rigid-Flex BGA substrates apart. BGA packaging enhances interconnect density, enabling more compact designs and facilitating the placement of densely packed integrated circuits. This feature contributes to improved performance and miniaturization in electronic devices.
Moreover, Rigid-Flex BGA substrates enhance reliability by minimizing the reliance on connectors and cables. Traditional substrates often incorporate these additional components, leading to increased points of failure and decreased overall reliability. In contrast, the integrated design of rigid and flexible regions in Rigid-Flex BGA substrates eliminates the need for such connectors, resulting in a more robust and dependable electronic system.
In essence, the distinct advantages of Rigid-Flex BGA substrates, including their adaptability to three-dimensional structures, utilization of BGA packaging for higher density, and reduction of connectors, position them as a superior choice for applications where traditional substrates may struggle to meet the evolving demands of modern electronics.
What Are the Manufacturing Technologies of Rigid-Flex BGA Substrates?
Manufacturing Rigid-Flex BGA substrates involves employing advanced technologies to ensure their unique characteristics and superior performance. Key manufacturing processes include:
Advanced Lamination Techniques:
The production of Rigid-Flex BGA substrates relies on sophisticated lamination processes. This entails bonding multiple layers of rigid and flexible materials through precise control measures. Techniques like controlled impedance lamination are crucial for achieving consistent electrical performance across the entire substrate.
Material Selection for Flexible Components:
A critical aspect is the careful selection of materials for the flexible components, typically composed of polyimide. These materials must possess high thermal stability, excellent dielectric properties, and resilience to bending and flexing. The selected materials are pivotal in guaranteeing the dependability and robustness of the flexible sections across diverse operational conditions.
High-Density Interconnect (HDI) Technology:
Rigid-Flex BGA substrates harness the capabilities of High-Density Interconnect (HDI) technology to elevate interconnection density. This incorporates sophisticated methods, including microvias, blind vias, and buried vias, facilitating the development of compact and intricate circuit patterns. The application of HDI plays a pivotal role in device miniaturization and the enhancement of signal integrity.
Precision Manufacturing Processes:
Precision is a priority in Rigid-Flex BGA substrate manufacturing, utilizing modern fabrication techniques such as laser drilling and automated optical inspection systems. These processes guarantee accuracy and consistency in creating intricate circuit patterns, enhancing overall reliability and minimizing the risk of defects.
Surface Finishing Techniques:
The surface finishing process for Rigid-Flex BGA substrates consists of applying protective coatings to the exposed copper surfaces. Widely used finishes encompass gold plating, electroless nickel immersion gold (ENIG), and organic solderability preservatives (OSP). These coatings serve to bolster corrosion resistance, thwart oxidation, and guarantee the dependability of solder joints during the assembly phase.
The integration of these advanced technologies not only elevates the reliability of Rigid-Flex BGA substrates but also enhances overall production efficiency. This comprehensive approach allows for the creation of sophisticated, high-performance substrates that meet the stringent requirements of contemporary electronic applications without unnecessary repetition.
In What Real-World Applications Are Rigid-Flex BGA Substrates Utilized?
Rigid-Flex BGA substrates exhibit versatility and effectiveness in various real-world applications, enhancing device functionality and reliability. Let’s examine practical case studies across different fields:
Medical Devices:
In the realm of medical devices, a prominent player successfully incorporated Rigid-Flex BGA substrates into the innovative design of advanced pacemakers. The inherent flexibility of the substrate played a pivotal role in achieving a more compact and curved design, seamlessly adapting to the distinctive shape of the medical implant. By harnessing BGA packaging, the integration of intricate circuitry was streamlined, resulting in notable enhancements to the pacemaker’s performance and overall longevity.
Drones:
Within the drone manufacturing industry, a company strategically employed Rigid-Flex BGA substrates to enhance the flight control system of a high-performance drone. The inherent flexibility of the substrate seamlessly facilitated integration within the drone’s compact frame, optimizing space utilization. Meanwhile, the incorporation of high-density interconnects played a pivotal role in efficiently placing vital sensors and communication modules, contributing to the drone’s overall performance. The durability of the Rigid-Flex design proved critical in withstanding the operational vibrations and environmental challenges encountered during drone flights.
Portable Electronic Products:
A prominent smartphone manufacturer embraced Rigid-Flex BGA substrates in the creation of a flagship device. The substrate’s flexibility allowed it to bend around the device’s edges, maximizing internal space utilization. High-density interconnects played a key role in integrating advanced processors and sensors, contributing to the device’s high-performance features. The reliability of the Rigid-Flex design was essential in maintaining structural integrity despite frequent handling and bending.
These examples illustrate how Rigid-Flex BGA substrates serve as integral components across diverse industries. Whether in medical devices, drones, or portable electronic products, these substrates consistently prove their ability to enhance functionality, optimize space, and ensure reliability in challenging operational environments.
What Are Frequently Asked Questions (FAQs) About Rigid-Flex BGA Substrates?
How do Rigid-Flex BGA substrates set themselves apart from traditional counterparts?
Rigid-Flex BGA substrates distinguish themselves by incorporating both rigid and flexible components on a single board. This unique design enables adaptability to three-dimensional structures, addressing a limitation in traditional substrates.
What advantages characterize Rigid-Flex BGA substrates?
Key advantages include support for high-density integrated circuits, flexibility for accommodating three-dimensional structures, and seamless integration of rigid and flexible elements, reducing reliance on additional connectors.
In which industries are Rigid-Flex BGA substrates commonly applied?
These substrates find utility in diverse industries such as medical devices, aerospace, wearable technology, and portable electronic products.
How are Rigid-Flex BGA substrates crafted during manufacturing?
Manufacturing involves advanced lamination techniques, material selection for flexible components, utilization of High-Density Interconnect (HDI) technology, precision in manufacturing processes, and application of surface finishing techniques.
Can you provide real-world examples of Rigid-Flex BGA substrate applications?
Instances include integration into medical devices like pacemakers, incorporation into the flight control systems of drones, and usage in flagship smartphones for heightened functionality and reliability.
How well do Rigid-Flex BGA substrates withstand environmental challenges?
These substrates are designed for durability and can effectively withstand diverse environmental challenges, making them suitable for applications in varying conditions.
Conclusion
In conclusion, Rigid-Flex BGA substrates stand as a pivotal innovation in electronics engineering, successfully meeting the evolving demands of modern electronic devices, including the imperative for miniaturization and high performance. Beyond their technical capabilities, these substrates empower designers with increased creative flexibility in product development. As technology advances persist, it is evident that Rigid-Flex BGA substrates will maintain their crucial role, shaping the future landscape of electronic devices. Their adaptability and integration capabilities position them at the forefront of electronic engineering, ensuring ongoing relevance in the dynamic world of technology.