Rigid-flex BGA substrate Vender and package substrate manufacturer. We use advanced Msap and Sap technology, High multilayer interconnection substrates from 4 to 18 layers,
In the dynamic landscape of electronics, the Rigid-Flex BGA Substrate emerges as a pioneer, embodying the constant evolution of technology. This progressive Printed Circuit Board (PCB) technology seamlessly integrates rigid and flexible materials, marking a departure from the traditional norms of PCB design.
The rigid element of this substrate is intricately fashioned from standard materials like FR-4, establishing a robust foundation for components. In contrast, the flexible counterpart incorporates materials such as polyimide, introducing a pliable quality that empowers the PCB to bend and flex, deviating from the accustomed rigidity of conventional boards.
At the core of this groundbreaking technology is the Ball Grid Array (BGA), a surface-mount packaging technique distinguished by a grid of solder balls on the underside of the integrated circuit package. This not only ensures a compact design but also optimizes thermal efficiency, a critical consideration in the ever-evolving landscape of modern electronics.
The fusion of rigidity and flexibility in Rigid-Flex BGA Substrate opens doors for PCBs to adapt to unconventional shapes and seamlessly integrate into confined spaces. Industries spanning aerospace, medical devices, and consumer electronics are poised to benefit from the streamlined assembly process, reduced dependence on connectors, and heightened durability offered by this avant-garde technology.
In essence, Rigid-Flex BGA Substrate transcends the established norms of PCB design, presenting a solution that prioritizes adaptability, spatial efficiency, and reliability. It stands as a testament to the ever-changing dynamics of technology, showcasing the capacity to meet the dynamic demands of our perpetually evolving digital era.
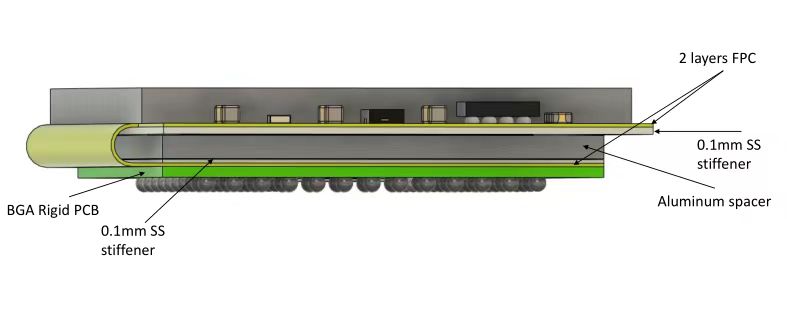
What are the basic characteristics and functions of Rigid-Flex BGA Substrate in the context of PCB technology?
Rigid-Flex BGA Substrate, within the domain of PCB technology, emerges as a distinctive player, showcasing a set of characteristics and functions that redefine electronic design. Let’s delve into its fundamental traits and roles:
Distinct Features:
Harmony of Rigid and Flexible Elements:
Rigid-Flex BGA Substrate seamlessly melds rigid and flexible materials, striking a harmonious balance between structural stability and adaptability.
Sturdy Rigid Foundation (Typically FR-4):
The rigid facet is meticulously crafted from conventional materials like FR-4, ensuring a robust base for components and upholding structural integrity.
Flexible Composition (Often Polyimide):
Introduces flexible materials, like polyimide, into the mix, bestowing a supple quality that allows the PCB to flex and bend—a departure from the rigid norms of traditional boards.
Integration of Ball Grid Array (BGA) Packaging:
Adopts Ball Grid Array (BGA) packaging, featuring a grid of solder balls beneath the integrated circuit package. BGA’s compact design and effective heat dissipation capabilities are notable.
Functional Roles:
Adaptability to Complex Shapes:
Facilitates the adaptation of PCBs to intricate shapes, fitting snugly into irregular spaces and providing a level of design flexibility essential in contemporary electronic applications.
Space Optimization:
Eliminates the need for excess connectors and cables, streamlining the layout and reducing the overall footprint of the device—particularly advantageous in environments where space is a premium.
Enhanced Resilience:
The fusion of rigid and flexible materials elevates the PCB’s durability, mitigating the risks of mechanical failures and fractures often associated with rigid-only counterparts.
Efficient Assembly Processes:
Simplifies the assembly process by minimizing interconnects and bypassing the necessity for additional connectors, thereby enhancing reliability and minimizing potential failure points.
Effective Thermal Management:
Incorporates BGA packaging and a thoughtful blend of materials, contributing to efficient heat dissipation—a crucial factor in applications where thermal performance is a priority.
Weight Reduction:
The flexible design not only enhances adaptability but also contributes to a reduction in overall weight, catering to industries where weight considerations, such as in aerospace, are paramount.
In essence, Rigid-Flex BGA Substrate brings forth a unique synergy of adaptability, durability, and streamlined design processes, positioning itself as a preferred solution for industries seeking innovation and reliability in electronic applications.
What functions does Rigid-Flex BGA Substrate serve?
In the domain of PCB technology, the Rigid-Flex BGA Substrate assumes a role of paramount significance, orchestrating a symphony of functions that enhance the versatility, dependability, and operational efficiency of electronic devices. Let’s delve into the multifaceted roles that characterize this technology:
Adaptive Design Dynamics:
Function: Rigid-Flex BGA Substrate empowers PCBs with the ability to gracefully conform to intricate and non-traditional shapes, granting designers the creative latitude to navigate complex spatial configurations and unique form factors.
Efficient Space Utilization:
Function: By eliminating connectors and fine-tuning interconnects, the substrate orchestrates a meticulous optimization of PCB layouts, resulting in a more condensed and spatially efficient design—a particularly coveted trait in applications constrained by spatial limitations.
Weight Reduction Elegance:
Function: The intrinsic flexibility woven into the substrate contributes to an overarching reduction in the overall weight of devices—a virtue especially cherished in weight-sensitive sectors such as aerospace, where minimizing weight stands as a paramount design objective.
Streamlined Assembly Choreography:
Function: With a flair for simplification, Rigid-Flex BGA Substrate refines the assembly process by minimizing the number of components and intricacies in interconnects. This not only elevates the overall reliability of the device but also curtails potential points of failure.
Fortified Durability Foundations:
Function: The fusion of robust rigid elements and flexible materials fortifies the durability of the PCB, effectively mitigating the vulnerabilities tied to mechanical failures and fractures—a challenge often encountered in the rigidity of traditional PCBs.
Thermal Prowess Optimization:
Function: Proficiently utilizing Ball Grid Array (BGA) packaging and a pliant design, Rigid-Flex BGA Substrate emerges as a maestro in dissipating heat effectively—a critical attribute for applications where adept thermal management is essential for sustained operational excellence.
Flexibility Flourish in Dynamic Environments:
Function: Rigid-Flex BGA Substrate not only meets but exceeds the demands of dynamic applications, facilitating the creation of PCBs that seamlessly flex and adapt. This quality proves indispensable in realms such as wearable devices and medical instruments.
Connector Independence Elegance:
Function: By integrating flexible sections, the technology gracefully reduces dependence on connectors. This deliberate simplification not only streamlines the design but also fortifies the reliability of the electronic device by minimizing potential points of failure.
Circuit Density Symphony:
Function: The BGA packaging method orchestrates a crescendo in circuit density, allowing for the accommodation of a higher number of solder balls and connections within a confined space. This capability proves instrumental in applications that demand advanced integration.
In essence, Rigid-Flex BGA Substrate emerges as a virtuoso in the orchestration of PCB technology, seamlessly weaving together adaptability, spatial optimization, durability, and thermal efficiency. Its versatile functions position it as an instrumental solution across industries where the pursuit of innovative and reliable PCB solutions stands as a non-negotiable imperative.
What types of Rigid-Flex BGA Substrate exist?
Rigid-Flex BGA Substrates come in a diverse array of types, each meticulously crafted to cater to unique design specifications and application demands. These classifications hinge on factors such as layer composition, flexibility nuances, and overall structural configuration. Let’s delve into the various incarnations of Rigid-Flex BGA Substrates:
Single-Sided Flex:
Description: Marked by a solitary rigid layer and a lone flexible layer, Single-Sided Flex ushers in a fundamental level of flexibility, primarily orientated in one direction. It’s apt for applications where restrained bending suffices.
Double-Sided Flex:
Description: Flaunting a tandem of flexible layers separated by a central rigid layer, Double-Sided Flex amplifies flexibility in both directions. This variant finds its niche in applications that demand intricate bending capabilities.
Multi-Layer Flex:
Description: Multi-Layer Flex intricately weaves together multiple flexible layers interspersed with rigid counterparts. This intricate composition delivers heightened flexibility, catering to intricate designs and ventures requiring advanced bending dynamics.
Single-Sided Rigid-Flex:
Description: Fusing a singular rigid layer with a lone flexible counterpart, Single-Sided Rigid-Flex strikes a harmonious equilibrium between rigidity and suppleness. It’s a fitting choice for scenarios necessitating a degree of flexibility alongside structural stability.
Double-Sided Rigid-Flex:
Description: Double-Sided Rigid-Flex orchestrates a tandem of rigid layers flanking a central flexible layer, achieving a delicate balance between steadfastness and adaptability. It’s an optimal solution for applications craving a measured dose of flexibility.
Multilayer Rigid-Flex:
Description: A symphony of multiple rigid and flexible layers harmoniously stacked, Multilayer Rigid-Flex delivers an elevated echelon of flexibility. Tailor-made for intricate applications demanding sophisticated design prerequisites.
Dynamic Flex:
Description: Crafted to endure repetitive bending and flexing, Dynamic Flex Rigid-Flex Substrates find their forte in applications where the PCB undergoes frequent motion without compromising on reliability.
Conductive Flex:
Description: Adorned with conductive traces on flexible layers, Conductive Flex Rigid-Flex Substrates facilitate electrical connections across flexible sections. This variant is a prudent choice when electrical connectivity is a requisite in flexible zones.
3D Flex:
Crafted for seamless adaptation to intricate three-dimensional configurations, 3D Flex Rigid-Flex Substrates stand as the preferred choice for applications demanding the PCB to gracefully conform to complex spatial arrangements.
The selection of a particular Rigid-Flex BGA Substrate hinges on the nuanced demands of the application, encompassing the desired level of flexibility, the intricacy of the design, and the environmental challenges the PCB is poised to encounter. Designers and manufacturers navigate this diverse spectrum to pinpoint the most fitting type, ensuring an optimal marriage of performance and reliability across a spectrum of applications.
How does Rigid-Flex BGA Substrate differ from traditional PCBs?
Rigid-Flex BGA Substrates represent a transformative departure from the conventional stiffness inherent in traditional PCBs. Let’s delve into the distinctive features that set them apart:
Flexibility:
Rigid-Flex BGA Substrates: Imbued with the suppleness of materials like polyimide, these substrates elegantly conform to intricate shapes or seamlessly integrate into confined spaces, showcasing a dynamic flexibility absent in traditional PCBs.
Traditional PCBs: Maintain unwavering rigidity, lacking the inherent adaptability woven into the flexible layers of Rigid-Flex BGA Substrates.
Construction:
Rigid-Flex BGA Substrates: Pioneering a fusion of rigid and flexible materials, these substrates craft a unified board where rigid components anchor stability, and flexible counterparts introduce fluid adaptability.
Traditional PCBs: Crafted exclusively from rigid materials like FR-4, traditional PCBs offer structural stability but fall short of the versatile flexibility interwoven into Rigid-Flex BGA Substrates.
Space Utilization:
Rigid-Flex BGA Substrates: Excel in spatial efficiency by forsaking connectors, streamlining the overall device profile. This proves advantageous in applications prioritizing spatial optimization.
Traditional PCBs: Often tethered to connectors and cables, traditional PCBs may contribute to bulkier dimensions. Their layout tends to be less pliable in addressing spatial constraints.
Applications:
Rigid-Flex BGA Substrates: Emerge as stalwarts in applications craving a fusion of flexibility, adaptability, and spatial efficiency—finding resonance in aerospace, medical devices, and consumer electronics.
Traditional PCBs: Exhibit versatility across diverse applications but might encounter constraints in scenarios where the dynamic flexibility of Rigid-Flex BGA Substrates proves indispensable.
Assembly Complexity:
Rigid-Flex BGA Substrates: Streamline assembly processes by curtailing connectors and cables, fostering heightened reliability and durability.
Traditional PCBs: Assembly might entail a web of connectors and intricate components, potentially introducing complexity to the process.
Durability:
Rigid-Flex BGA Substrates: The fusion of rigid and flexible materials fortifies overall durability, presenting a robust shield against mechanical failures—an advantage over the steadfast but less adaptive traditional rigid PCBs.
Traditional PCBs: While stalwart, traditional PCBs may be more susceptible to mechanical stress, especially in scenarios where the adaptive flexibility of Rigid-Flex BGA Substrates proves indispensable.
Cost:
Rigid-Flex BGA Substrates: Manufacturing intricacies might tip the scale towards higher production costs, reflecting the sophistication of these substrates.
Traditional PCBs: Typically adhere to a more straightforward manufacturing process, potentially resulting in more economical production costs.
In essence, Rigid-Flex BGA Substrates carve a distinctive niche with their amalgamation of flexibility, adaptability, and spatial optimization—a paradigm shift from the entrenched rigidity of traditional PCBs. The choice between the two hinges on specific application requirements and the delicate interplay between flexibility, complexity, and cost considerations.
What is the structure and manufacturing technology of Rigid-Flex BGA Substrate?
Crafting Rigid-Flex BGA (Ball Grid Array) Substrates involves a strategic fusion of rigid and flexible materials, ushering in a versatile solution tailored for specific applications. Let’s delve into the nuanced structure and the intricate manufacturing process:
Structure of Rigid-Flex BGA Substrate:
Rigid Layers:
At its core, Rigid-Flex BGA Substrates boast robust rigid layers, commonly fashioned from materials like FR-4 (Fiberglass Reinforced Epoxy). These layers lay the foundation for structural stability.
Flexible Layers:
Woven into the substrate are flexible layers, often composed of materials like polyimide (PI) or polyester. These layers introduce a dynamic flexibility, enabling the PCB to gracefully adapt to non-planar configurations.
Adhesive Layers:
To fortify the union between rigid and flexible components, adhesive layers come into play. These layers not only strengthen the substrate but also contribute to the overall cohesiveness of the board.
Copper Foils:
Conduits for electrical pathways come in the form of copper foils, seamlessly laminated onto both rigid and flexible layers. These foils serve as the vital conduits for the seamless flow of electrical signals.
BGA Pads:
Strategically positioned on the substrate’s surface are BGA pads, acting as docking stations for Ball Grid Array components. Solder balls facilitate the secure attachment of these components, enhancing the PCB’s functionality.
Manufacturing Technology:
Design Phase:
The journey commences with the meticulous design of the Rigid-Flex BGA Substrate. Specialized software becomes the canvas for engineers, allowing them to craft a layout that harmoniously integrates rigid and flexible domains, aligning with the application’s demands.
Material Selection:
Material curation assumes a pivotal role. Meticulous choices of rigid materials like FR-4 and flexible counterparts like polyimide hinge on mechanical, thermal, and electrical considerations.
Layer Preparation:
Preparing the stage involves treating rigid and flexible layers separately. Rigid layers undergo pre-etching and drilling, while flexible layers are endowed with the requisite properties for pliability.
Lamination:
The marriage of rigid and flexible layers transpires through the art of lamination. Heat and pressure converge to create a unified structure, with adhesive layers cementing the symbiotic relationship between rigidity and flexibility.
Copper Cladding:
The introduction of copper foils, a process known as copper cladding, embellishes the substrate. These foils adorn both rigid and flexible layers, fashioning the vital conductive pathways.
Circuit Patterning:
Precision takes center stage during circuit patterning. Copper is selectively removed through techniques like etching, giving birth to intricate conductive traces that weave the tapestry of connectivity.
Drilling:
Paving the way for inter-layer connections involves drilling holes for through-hole components and vias, fostering electrical links across the substrate.
BGA Pad Application:
The surface adorns BGA pads, pivotal for the orchestrated attachment of Ball Grid Array components. These pads serve as the anchor points for seamless component integration.
Final Inspection:
The curtain falls with a meticulous inspection, ensuring every component, trace, and connection aligns with the precise design criteria.
Assembly:
The grand finale sees the Rigid-Flex BGA Substrate seamlessly integrating into the broader electronic ecosystem, with BGA components finding their home on the corresponding pads.
The manufacturing odyssey of Rigid-Flex BGA Substrates is a symphony of precision, harmonizing flexibility, rigidity, and electrical prowess—a testament to technology’s prowess when tailored for applications demanding versatile and spatially efficient PCB solutions.
What are the frequently asked questions about Rigid-Flex BGA Substrate?
What advantages does a Rigid-Flex BGA Substrate offer?
Key benefits include enhanced flexibility, efficient space utilization, reduced dependence on connectors, improved reliability, and suitability for applications requiring dynamic or non-planar configurations.
What materials are typically used in constructing Rigid-Flex BGA Substrates?
Rigid layers often employ materials like FR-4, while flexible layers commonly use substances such as polyimide (PI) or polyester. Adhesive layers play a crucial role in bonding these materials together.
Are there limitations to the flexibility of Rigid-Flex BGA Substrates?
While more flexible than traditional rigid PCBs, Rigid-Flex BGA Substrates may have limitations in applications requiring extreme bending. The degree of flexibility depends on specific design choices and material selection.
How do Rigid-Flex BGA Substrates contribute to space optimization in electronic devices?
By eliminating the need for connectors and accommodating non-traditional shapes, Rigid-Flex BGA Substrates enable more efficient utilization of space within electronic devices, contributing to overall miniaturization.
What considerations are crucial during the design phase of Rigid-Flex BGA Substrates?
Designers must consider specific application requirements, desired flexibility levels, thermal considerations, and the strategic placement of components—especially BGA components. Collaborative efforts between mechanical and electrical designers are often crucial.
Conclusion
To encapsulate, the Rigid-Flex BGA Substrates signify a paradigm shift in PCB design, deviating from conventional norms. This integration of both rigid and flexible elements introduces a myriad of advantages, positioning it as a transformative force in various industries.
The marriage of structural robustness and adaptability within Rigid-Flex BGA Substrates directly caters to the evolving needs of electronic devices. The seamless fusion of rigidity and flexibility not only fortifies reliability but also optimizes spatial efficiency, a pivotal consideration in contemporary design landscapes.
The intricacies woven into the manufacturing process underscore the precision required to achieve the delicate balance of diverse materials. Rigid layers, featuring stalwarts like FR-4, provide a sturdy foundation, while the suppleness introduced by flexible layers, adorned with materials like polyimide, conforms to unconventional shapes with ease.
These substrates carve out a distinctive niche across industries, spanning aerospace, medical devices, consumer electronics, automotive, and communication systems. Their versatility positions them as pivotal components for applications where traditional rigid PCBs might falter.
Navigating the landscape of Rigid-Flex BGA Substrates demands an understanding of their construction intricacies, a strategic application of their advantages during the design phase, and a recognition of the transformative impact they bring to electronic devices.
In the relentless march of technology, Rigid-Flex BGA Substrates serve as a testament to the industry’s dedication to innovation, challenging established norms, and steering towards a future where flexibility, adaptability, and efficiency take precedence in the ever-evolving domain of electronic design.