Rigid-flex packaging substrate manufacturing. High speed and high frequency material packaging substrate supplier. Advanced packaging substrate production process and technology.
The integration of Rigid-Flex Packaging Substrate into electronic device design promises a significant transformation. By harmonizing rigid and flexible elements, this advanced packaging technology introduces unparalleled design flexibility, allowing exploration of innovative shapes and dimensions.
A standout feature of Rigid-Flex Packaging Substrate lies in its ability to transcend the constraints of conventional designs. Unlike rigid boards dictating fixed forms, this technology empowers designers to explore unconventional shapes and configurations. This newfound flexibility is particularly impactful in applications where space is a premium.
Rigid-Flex Packaging Substrate’s adaptability to complex spatial constraints is a game-changer. In situations where three-dimensional space is restricted, such as within small medical devices or intricately designed consumer electronics, the flexibility of Rigid-Flex Packaging Substrate becomes crucial.
This adaptability not only optimizes space utilization but also contributes to the reduction of overall device dimensions. In an era where compactness is a key trend, Rigid-Flex Packaging Substrate emerges as a vital tool for designers seeking a balance between form and function in smaller electronic devices.
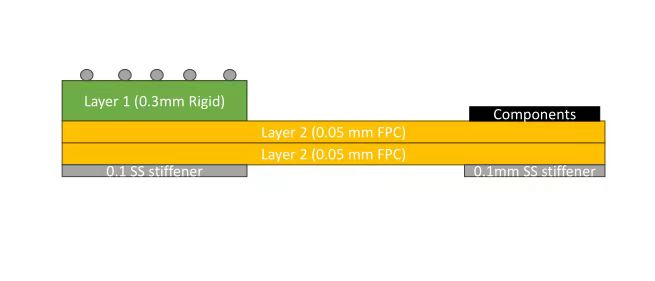
What Functions Does Rigid-Flex Packaging Substrate Serve?
Rigid-flex packaging substrates are crucial in electronic device manufacturing, providing numerous functions to enhance design flexibility and enable devices to conform adeptly to intricate shapes and spatial limitations. Here are key functionalities and advantages associated with these substrates:
Flexibility and Structure:
Rigid-flex substrates seamlessly combine the strength inherent in traditional rigid boards with the flexibility of circuits that can bend and adapt.
This combination enables the substrates to flex and adapt to surfaces that are not flat, facilitating a variety of designs that are both diverse and space-efficient.
Optimized Space Utilization:
These substrates excel in efficiently utilizing available space, particularly in devices with irregular shapes or confined spatial dimensions.
Designers can leverage their flexibility to intricately route traces in three dimensions, optimizing spatial usage and minimizing the need for excessive connectors and cables.
Compactness through Weight and Volume Reduction:
Integration of flexible components contributes to an overall reduction in the weight and volume of electronic devices.
This proves advantageous in applications with stringent constraints on weight and size, such as wearable devices and aerospace technologies.
Enhanced Reliability and Durability:
Rigid-flex technology minimizes points of failure by reducing interconnects and solder joints, thus enhancing the overall reliability of electronic devices.
This reduction in potential failure points results in improved durability, as there are fewer opportunities for mechanical stress or fatigue.
Signal Integrity Optimization:
Rigid-flex substrates excel in minimizing signal degradation and mitigating electromagnetic interference (EMI) through the reduction of signal paths and the mitigation of crosstalk. This capability is achieved by shortening the routes that signals traverse and by minimizing the interference between adjacent signal paths.
This becomes particularly vital in high-frequency applications, guaranteeing the utmost signal integrity, especially in devices focused on communication.
Simplified Assembly and Testing Processes:
Integration of rigid and flexible components streamlines the assembly process, minimizing the number of individual parts and connectors.
This simplification not only reduces manufacturing costs but also improves testing processes.
Unrestricted Design Freedom:
Rigid-flex substrates afford designers greater freedom to conceptualize innovative and unconventional shapes for electronic devices.
This flexibility proves invaluable in applications where standard rectangular or planar designs may be impractical or limiting.
Temperature Resilience:
Rigid-flex materials are chosen for their capacity to endure a wide spectrum of temperatures, rendering them well-suited for use in challenging environmental conditions.
In summary, the integration of rigid-flex packaging substrates provides electronic device designers with a versatile solution to effectively overcome challenges associated with intricate shapes and spatial limitations. This integration enhances design flexibility and proves instrumental in navigating the complexities of spatial constraints.By amalgamating the advantages of rigid and flexible materials, these substrates significantly enhance design flexibility, elevate reliability, and contribute to the development of more compact and innovative electronic devices across diverse industries.
How Does Rigid-Flex Packaging Substrate Relate to Traditional Package Substrate?
Rigid-flex packaging substrates mark a notable advancement in electronic packaging technology, standing in contrast to conventional package substrates. Typically, traditional package substrates utilize rigid boards, a design that falls short in meeting the evolving demands of modern electronic products. The emergence of rigid-flex packaging substrates introduces numerous benefits in enhancing adaptability for today’s electronic product designs.
Mechanical Flexibility:
Traditional package substrates exhibit a rigid nature, lacking the flexibility essential for contemporary designs that frequently demand adaptability to non-traditional shapes.
Rigid-flex packaging substrates provide a key advantage in terms of mechanical flexibility. This flexibility allows them to bend and flex, enabling seamless adaptation to the non-planar shapes required by contemporary electronic devices.
Space Utilization:
Traditional Package Substrate: Rigid boards limit the options for spatial utilization in electronic devices, especially those with compact or irregular designs.
Rigid-flex packaging substrates enhance space utilization through their inherent flexibility. This flexibility allows for three-dimensional trace routing, optimizing spatial efficiency and adapting to the spatial constraints of modern designs.
Reduced Weight and Volume:
In traditional package substrates, the inclusion of rigid substrates contributes to both the overall weight and physical dimensions of electronic devices.
The integration of flexible components into rigid-flex packaging substrates results in a notable decrease in both weight and volume. This quality makes them particularly well-suited for electronic devices that emphasize portability and a lightweight design.
Design Freedom:
Traditional package substrates limit design options because of their rigid characteristics.
Rigid-flex packaging substrates provide designers with expanded creative freedom, allowing them to explore non-traditional shapes and bring imaginative, space-efficient designs to life.
Streamlined Assembly:
Traditional Package Substrate: Assemblies involving traditional substrates may require additional connectors and complex wiring.
The integration of rigid and flexible components in rigid-flex packaging substrates simplifies the assembly process. This integration minimizes the requirement for additional connectors, resulting in a simplified overall assembly.
Adaptability to Complex Shapes:
Traditional Package Substrate: Traditional substrates struggle to adapt to complex shapes and forms.
Rigid-flex packaging substrates excel in their capacity to adapt to intricate and distinct shapes, offering designers a versatile solution for products characterized by unique and complex designs.
Temperature Resistance:
Traditional Package Substrate: Some traditional materials may have limited temperature resistance.
Rigid-flex packaging substrates, often selected for their temperature resilience, possess the capability to endure a diverse range of temperatures. This quality renders them well-suited for applications across various environmental conditions.
To sum up, rigid-flex packaging substrates offer significant advantages compared to traditional package substrates. These benefits include mechanical flexibility, efficient space utilization, weight reduction, improved reliability, design freedom, simplified assembly, adaptability to complex shapes, and temperature resistance. These characteristics collectively position rigid-flex substrates as a vital and versatile solution for contemporary electronic product designs, particularly in scenarios where flexibility, reliability, and innovation are of utmost importance.
What is the Structure and Manufacturing Technologies of Rigid-Flex Packaging Substrate?
Rigid-flex packaging substrates showcase a distinctive structure, integrating both rigid and flexible materials. This exclusive hybrid design strategically harnesses the inherent strengths of each material, resulting in a versatile and adaptable substrate tailored for electronic encapsulation.
Rigid Layers:
The rigid portion typically consists of traditional rigid printed circuit boards (PCBs). These layers provide structural integrity and support for components that require stability.
Rigid layers often contain the critical components of the electronic device and serve as a foundation for the overall structure.
Flexible Layers:
Flexible layers, usually made of polyimide or similar materials, introduce flexibility to the substrate. These layers can bend and conform to non-planar shapes, facilitating three-dimensional designs.
Flexible layers accommodate the need for dynamic and adaptable structures, allowing the substrate to fit into unconventional spaces within electronic devices.
Adhesive Layers:
The inclusion of adhesive layers plays a critical role in establishing a strong connection between the rigid and flexible layers in rigid-flex packaging substrates. This adhesive bonding is essential for upholding the structural integrity of the substrate and ensuring a stable, secure linkage between the rigid and flexible components.
Manufacturing Technologies:
Rigid-flex packaging substrates are manufactured through fundamental technologies that enable the smooth integration of both rigid and flexible materials.
Layer Lamination:
Specialized adhesives are utilized to laminate rigid and flexible layers together in a precise manner. This critical process demands precision to guarantee accurate alignment and secure bonding among the diverse layers.
Circuit Patterning:
The rigid and flexible layers undergo circuit patterning to create the desired electrical connections. This includes techniques like photolithography and etching to delineate circuit traces and components on the substrate.
Drilling and Vias:
In the manufacturing process, precise drilling operations are conducted through the rigid layers to create vias, which act as conductive pathways enabling electrical connections between different layers. This crucial step is essential to ensure uninterrupted electrical continuity throughout the entire substrate.
Component Placement:
Utilizing pick-and-place machines, electronic components find placement on the stable surfaces of the rigid sections of the substrate. These rigid areas serve as secure mounting points for crucial components, including integrated circuits, resistors, and capacitors.
Flexible Material Processing:
The flexible layers undergo special processing techniques, such as laser cutting or mechanical cutting, to achieve the desired shape and flexibility. This step is essential for allowing the substrate to adapt to surfaces that are not flat.
Encapsulation:
The complete structure can undergo encapsulation procedures to shield electronic components from environmental influences like moisture, dust, and mechanical stress. This protective measure may include applying coatings or utilizing specific encapsulation materials.
The unique structure of rigid-flex packaging substrates, combining rigid and flexible materials, indeed creates conditions for their widespread application in electronic encapsulation. This design allows for greater adaptability to various form factors and spatial constraints, making them suitable for a diverse range of electronic devices, from medical implants to aerospace systems. The key manufacturing technologies involved ensure the seamless integration of rigid and flexible elements, resulting in reliable and versatile substrates for modern electronic applications.
In What Applications Can Rigid-Flex Packaging Substrate Be Utilized?
Rigid-flex packaging substrates exhibit versatility and adaptability across a diverse array of applications. Highlighted below are specific sectors, accompanied by case studies that illustrate how rigid-flex packaging substrates confer tangible benefits in practical situations, spanning from medical devices to consumer electronics.
Medical Devices:
Case Study: Pacemakers
In the realm of medical applications, rigid-flex packaging substrates assume a pivotal role, with a notable application being in devices like pacemakers. The intrinsic flexibility of these substrates enables seamless conformation to the curved contours of the implant, with the rigid sections serving as secure enclosures for vital electronic components. This innovative design not only enables pacemakers to maintain a compact and lightweight profile but also enhances their adaptability to the intricate shapes of implantation sites.
Consumer Electronics:
Case Study: Foldable Smartphones
Rigid-flex packaging substrates are crucial components within the consumer electronics sector, notably influencing the design and capabilities of foldable smartphones. Their significance lies in furnishing the required flexibility for screens to fold seamlessly. Simultaneously, the rigid section plays a pivotal role in upholding structural stability by supporting essential circuits and components. This innovative design not only facilitates a more expansive screen space but also ensures the overall robustness of the electronic device’s structure.
Aerospace Applications:
Case Study: Aircraft Electronic Systems
Rigid-flex packaging substrates are widely used in aerospace electronic systems, such as navigation and communication systems on aircraft. By combining rigid and flexible characteristics, they adapt to the space constraints inside aircraft and provide reliability and performance in complex electronic systems.
Wearable Devices:
Case Study: Smartwatches
Rigid-flex packaging substrates demonstrate superior design flexibility in wearable devices like smartwatches. The flexible part allows the device to conform to the curve of the wrist, while the rigid part houses processors and sensors. This design makes wearable devices more comfortable, lightweight, and conducive to integrating various functionalities.
Industrial Control Systems:
Case Study: Automated Production Line Controllers
In industrial control systems, rigid-flex packaging substrates are used in devices like automated production line controllers. Their flexibility and reliability ensure long-term stable operation in harsh industrial environments.
Through these case studies, rigid-flex packaging substrates showcase outstanding performance in various fields. Their unique design, combining both rigidity and flexibility, enables them to adapt to complex application scenarios, driving innovation and development in modern electronic devices.
What Are the Frequently Asked Questions (FAQs) About Rigid-Flex Packaging Substrate?
What Future Trends are Expected in Rigid-Flex Packaging Substrate Development?
Anticipated trends include further miniaturization, material advancements for improved performance, and increased integration of smart features in electronic devices, driven by the continuous evolution of rigid-flex technology.
What Constitutes Rigid-Flex Packaging Substrate?
Rigid-flex packaging substrate stands as an advanced electronic encapsulation technology, unifying rigid and flexible materials within a single substrate. This integration opens avenues for distinctive design possibilities in electronic devices.
What Advantages Characterize Rigid-Flex Technology?
Rigid-flex technology introduces design flexibility, space optimization, weight reduction, improved reliability, and adaptability to intricate shapes. It simplifies assembly processes and effectively addresses spatial constraints in applications.
How Does Rigid-Flex Substrate Boost Device Reliability?
Answer: By minimizing interconnects and solder joints, rigid-flex substrates mitigate potential failure points, elevating the overall reliability of electronic devices. This proves particularly beneficial in scenarios involving mechanical stress or fluctuating environmental conditions.
Is Rigid-Flex Technology Economically Viable?
Answer: While initial costs may surpass those of traditional PCBs, the benefits of reduced weight, space optimization, and heightened reliability often substantiate the investment. Cost-effectiveness is contingent on the application and production volume.
Is Rigid-Flex Packaging Substrate the Future Driver of Electronic Industry Advancements?
Rigid-Flex Packaging Substrate stands poised as a transformative force in electronic encapsulation, offering innovative avenues for product design and manufacturing. With its unique ability to seamlessly integrate rigid and flexible materials, this technology enables three-dimensional designs and adapts to complex spatial constraints. As electronic devices evolve towards greater miniaturization and enhanced functionality, Rigid-Flex Substrate emerges as a critical enabler. Its capacity to reduce weight, optimize space, and enhance reliability positions it as a catalyst for advancements in the electronic industry. As a result, it is anticipated to play a pivotal role in shaping the future landscape of electronic devices, fostering new possibilities in design, manufacturing, and overall technological innovation.