Rigid-flex packaging substrate Vender. We use the advanced Msap and Sap technology to do the BGA substrate with Rigid-Flex PCBs, High multilayer interconnection substrates from 4 to 20 layers.
Rigid-flex packaging substrates stand as a specialized electronic packaging material employed in crafting flexible printed circuit boards (FPCBs) and composite circuits harmonizing rigid and flexible elements seamlessly. This material is tailored to meet the demands of electronic devices with intricate shapes or those requiring a measure of flexibility.
Within the realm of rigid-flex packaging substrates, a fusion of rigid and flexible materials is strategically applied to a singular board. The rigid constituents provide structural support, housing critical components such as integrated circuits (ICs), while the flexible segments empower the board to flex or adapt to the device’s contours.
This packaging solution finds its niche in scenarios where spatial constraints, weight considerations, and design adaptability take precedence. Rigid-flex circuits find application across a spectrum of electronic devices, encompassing smartphones, wearables, medical devices, and automotive electronic systems.
The integration of rigid-flex packaging substrates streamlines assembly processes, reduces dependence on connectors and cables, and enhances the overall reliability of the electronic system.
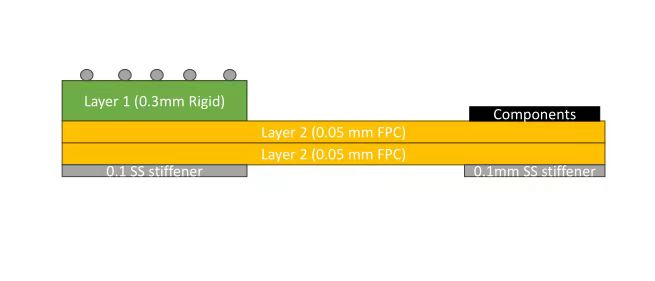
What Role Does Rigid-flex Packaging Substrate Play in PCB Engineering?
Rigid-flex packaging substrates play a pivotal and multifaceted role in the realm of PCB engineering, introducing a spectrum of advantages and innovations. Here’s an exploration of their key roles in shaping the landscape of electronic device design:
Unleashing Design Creativity:
Rigid-flex substrates empower PCB engineers with unparalleled design flexibility. Particularly valuable in confined spaces or applications demanding intricate geometries, these substrates allow for imaginative and efficient circuit designs.
Space Optimization Mastery:
The integration of rigid and flexible elements on a single board in rigid-flex PCBs serves as a masterstroke in space optimization. The eradication of connectors and cables not only conserves space but also contributes to a more streamlined and lightweight device design.
Elevating Reliability Standards:
Rigid-flex PCBs elevate reliability standards by mitigating potential points of failure. The reduction in connectors and solder joints enhances durability, reinforcing the resilience and robustness of electronic systems.
Streamlined Assembly Simplicity:
The amalgamation of rigid and flexible elements simplifies the assembly process, presenting a contrast to the complexity associated with using separate rigid and flexible boards connected by cables. This not only streamlines manufacturing but also minimizes the risk of assembly errors.
Durable Performance in Rigorous Environments:
Tailored for durability, rigid-flex substrates prove their mettle in challenging environments where PCBs may face bending, vibrations, or other mechanical stresses. This durability factor makes them particularly suitable for applications in aerospace, automotive, and medical devices.
Weight Reduction Expertise:
Contributing to weight reduction, rigid-flex PCBs eliminate excess weight associated with additional connectors and cables. This weight-conscious design makes them an ideal choice for portable devices and applications where weight is a critical consideration.
Enhanced Signal Integrity Mastery:
Rigid-flex PCBs exhibit prowess in maintaining superior signal integrity. The integrated design minimizes interconnect length and impedance variations, contributing to optimal signal quality and reducing the risk of signal degradation.
In essence, rigid-flex packaging substrates emerge as a transformative force in PCB engineering, seamlessly blending flexibility, space optimization, reliability, and durability to shape the future of electronic device design and performance.
What are the Technological Classifications of Rigid-flex Packaging Substrate?
The technological landscape of rigid-flex packaging substrates unfolds through various classifications, each shedding light on distinct aspects. Let’s delve into these classifications:
Material Composition Diversity:
Rigid-flex substrates showcase a spectrum of material compositions, incorporating flexible polyimide films, rigid FR-4 laminates, and copper foils. The interplay of these materials defines the substrate’s characteristics and functionality.
Layer Configuration Complexity:
Layer configuration, representing the arrangement of rigid and flexible layers, introduces intricacy into rigid-flex PCBs. These configurations can be sophisticated, catering to the demands of intricate and space-efficient designs.
Flexibility Spectrum:
The flexibility spectrum of rigid-flex substrates spans from highly pliable options, ideal for extensive bending, to moderately flexible solutions tailored to specific application nuances.
Circuit Complexity Dynamics:
Classifying rigid-flex PCBs involves considering the complexity of integrated circuits. These substrates accommodate a range of circuitry complexities, from fundamental components to advanced microprocessors and sensors.
Performance Resilience in Adverse Environments:
Some substrates are engineered to thrive in challenging environments, equipped with features like heightened temperature resilience, resistance to moisture, and tolerance to mechanical stress. This positions them favorably in aerospace, automotive, and industrial applications.
Manufacturing Process Variance:
The technological classification takes into account diverse manufacturing processes such as sequential lamination or adhesive-based techniques. These processes significantly influence the final performance and reliability of the substrates.
Flex-to-Rigid Ratio Dynamics:
Assessing the proportion of flexible to rigid sections contributes to the classification. Designs may lean towards increased flexibility for applications demanding substantial bending or strike a balance for versatility in both flexibility and structural support.
Tailoring for Application-Specific Needs:
Rigid-flex substrates embrace customization with features tailored to specific applications. Examples include biocompatible coatings for medical devices or designs optimized to minimize signal loss in high-frequency applications.
These technological classifications illuminate the nuanced and adaptable nature of rigid-flex packaging substrates, offering engineers a rich spectrum of options to align with the intricacies of diverse applications and design requirements.
How Does Rigid-flex Packaging Substrate Integrate with IC Packaging?
The fusion of rigid-flex packaging substrates with IC (Integrated Circuit) packaging signifies a sophisticated collaboration, bringing about a convergence of innovation in advanced electronic systems. Let’s delve into the intricacies of this seamless integration:
Foundation of Strength for ICs:
Rigid-flex packaging substrates establish a resilient foundation to house integrated circuits (ICs). The rigid components provide stability, ensuring secure mounting and optimal arrangement of ICs within the electronic framework.
Philosophy of Spatial Optimization:
The integration of rigid and flexible elements embodies a design philosophy centered around spatial optimization. This is particularly advantageous in applications where the emphasis is on minimizing size, such as in portable devices or components with stringent spatial constraints.
Simplified Interconnect Landscape:
Rigid-flex PCBs play a pivotal role in simplifying the interconnect landscape by minimizing reliance on additional connectors and cables. This streamlined approach not only simplifies the overall design but also mitigates potential points of failure, enhancing overall reliability.
Flexibility Paving the Way for Adaptive IC Placement:
The flexible segments of the substrate introduce adaptability in IC placement, proving beneficial in scenarios where devices exhibit unconventional shapes or when conforming to specific form factors is essential.
Elevated Reliability Standards:
The integrated design of rigid-flex substrates raises the bar for reliability in IC packaging. The reduction in solder joints and connectors contributes to a more resilient and enduring electronic system.
Efficiency Boost in Manufacturing Workflow:
Rigid-flex packaging substrates streamline the manufacturing process by consolidating rigid and flexible elements into a singular board. This enhances assembly efficiency and reduces the likelihood of errors during production.
Versatility Unleashed in Multi-Chip Modules (MCMs):
Rigid-flex substrates seamlessly adapt to Multi-Chip Modules (MCMs) where multiple ICs converge into a unified package. The flexible sections facilitate efficient routing of connections between ICs, allowing for the integration of intricate circuitry.
Harmonious Application in Wearable Devices:
The integration holds particular significance in wearable devices, where flexibility and compact design are pivotal. Rigid-flex substrates seamlessly align with IC packaging requirements, accommodating the form factor of wearables and contributing to ergonomic and efficient device designs.
In essence, the integration of rigid-flex packaging substrates with IC packaging not only provides a robust platform for ICs but also heralds a new era of design efficiency, reliability, and adaptability in the dynamic realm of electronic systems.
How is Rigid-flex Packaging Substrate Different from Traditional PCBs?
In the realm of electronic design, rigid-flex packaging substrates diverge from the conventional path of traditional PCBs, bringing forth a paradigm shift with their distinctive attributes. Let’s embark on a journey through these divergent landscapes:
Architectural Dynamics:
Traditional PCBs: Anchored in rigidity, traditional boards find their essence in materials like FR-4, upholding a steadfast and unyielding structure.
Rigid-flex Packaging Substrates: Pioneering a fusion of rigidity and flexibility, rigid-flex substrates seamlessly integrate both elements. This innovative synthesis creates a platform that harmonizes stability and adaptability within a singular board.
Flexibility Ballet:
Traditional PCBs: Stripped of inherent flexibility, traditional boards maintain a fixed form, offering limited adaptability to unconventional design demands.
Rigid-flex Packaging Substrates: In a departure from the norm, rigid-flex substrates introduce a dance of dynamic flexibility, allowing for bending and conformity to unique shapes. This attribute proves invaluable in applications requiring malleability and non-traditional form factors.
Design Choreography:
Traditional PCBs: Confined by design constraints, traditional boards grapple with accommodating intricate or three-dimensional configurations.
Rigid-flex Packaging Substrates: Unleashing a symphony of design possibilities, rigid-flex substrates expand the canvas. They facilitate the creation of complex and compact designs, catering to the demands of devices seeking non-standard shapes.
Spatial Ballet:
Traditional PCBs: Often tethered to additional connectors and cables, traditional boards inadvertently consume more space.
Rigid-flex Packaging Substrates: Redefining the spatial ballet, rigid-flex substrates streamline space utilization by eliminating the need for extra connectors and cables. The integrated design orchestrates efficient space optimization.
Application Symphony:
Traditional PCBs: Resonating in applications comfortable with rigidity, such as desktop computers and standard electronic devices.
Rigid-flex Packaging Substrates: Harmonizing with applications craving flexibility, space efficiency, and adaptability to distinctive shapes. They find a symphony in portable devices, wearables, medical instruments, and automotive electronics.
Reliability Overture:
Traditional PCBs: Inherently reliable, but the presence of connectors and cables introduces potential points of discord.
Rigid-flex Packaging Substrates: Pioneering a reliability overture, rigid-flex substrates minimize reliance on connectors and cables, reducing potential discord. The integrated design orchestrates heightened robustness in electronic systems.
In essence, transcending the established rigidity of traditional PCBs, rigid-flex packaging substrates take center stage as dynamic performers, orchestrating a harmonious blend of flexibility and stability. This makes them the virtuosos in applications seeking adaptability, spatial efficiency, and heightened reliability in design configurations.
What is the Structure and Manufacturing Technology of Rigid-flex Packaging Substrate?
Unveiling the intricacies of rigid-flex packaging substrates unveils a captivating dance between rigidity and flexibility, orchestrated through a meticulous manufacturing choreography. Let’s navigate the unique structure and the artistry involved in the crafting process:
Symphonic Structure of Rigid-flex Packaging Substrate:
Sturdy Crescendos:
The rigid segments, akin to robust musical crescendos, take shape from traditional PCB materials like FR-4 laminates. These sections provide a steadfast foundation for mounting components, weaving a melody of stability.
Flexibility Flourishes:
Introducing a dynamic movement, the flexible sections, crafted from polyimide (PI) films, perform flexible flourishes. This material’s pliability is akin to a dance, allowing the substrate to bend gracefully and adapt to the rhythm of specific shapes.
Copper Harmonies:
Like harmonious chords in a composition, copper foils resonate as conductive layers on both rigid and flexible segments. These layers interlace circuit traces, creating a harmonious flow for electrical signals to traverse.
Adhesive Bonds:
Serving as the unseen notes in the symphony, adhesive layers bind the rigid and flexible elements together. This adhesive harmony ensures a seamless connection, enhancing the overall structural harmony of the substrate.
Artistry in Manufacturing:
Preludes of Design:
The creative overture involves conceptualizing a layout that orchestrates the arrangement of rigid and flexible elements. Advanced design software acts as the conductor, harmonizing the layout for optimal performance.
Crafting Melodies of Material:
Traditional PCB fabrication processes bring the rigid sections to life, sculpting them from FR-4 laminates with precision. Simultaneously, the flexible sections, akin to a melodic interlude, emerge through the lamination and curing of polyimide films.
Layered Symphony:
The manufacturing journey unfolds as layers of rigid and flexible materials are artfully stacked, mirroring the composition of a symphony. This layering creates a visual and tactile experience, forming the 3D opus of the rigid-flex substrate.
Adhesive Crescendo:
The adhesive layers, akin to a crescendo building to a climax, play a pivotal role in bonding the rigid and flexible components. The lamination process applies heat and pressure, creating a crescendo of cohesive bonding for a durable performance.
Drilling Cadence:
Precision drilling, like a rhythmic cadence, punctuates the substrate with holes, creating vias for inter-layer connections. These drilled holes, plated with copper, become key notes in the substrate’s electrical symphony.
Component Concerto:
The integration of electronic components, resembling a concerto, unfolds seamlessly. ICs and connectors take center stage, orchestrated by standard surface-mount technology (SMT) or through-hole mounting techniques.
Finale of Inspection:
A grand finale ensues with a meticulous inspection and testing phase, scrutinizing every note of the substrate’s circuitry, connection reliability, and overall functionality. This final movement ensures the substrate’s performance meets the highest standards.
In essence, the symphonic collaboration of rigid and flexible materials, choreographed through a manufacturing masterpiece, positions rigid-flex packaging substrates as versatile compositions. They resonate across diverse applications, where adaptability, compact design, and unwavering reliability take center stage.
Frequently Asked Questions (FAQs)
What Key Benefits Do Rigid-flex Packaging Substrates Bring to the Table?
Rigid-flex substrates introduce a host of advantages, including optimal space utilization, adaptability to unconventional designs, a reduction in connectors and cables, heightened reliability, and an optimized manufacturing process.
How is the Manufacturing Symphony of Rigid-flex Substrates Conducted?
The manufacturing choreography encompasses steps like layout design, meticulous preparation of rigid and flexible materials, layered assembly, adhesive bonding, precision drilling for vias, copper plating, component integration, and a symphony of quality testing.
Which Materials Form the Backbone of Rigid-flex Substrates?
Traditional PCB materials like FR-4 laminates build the robust foundation of rigid sections, while flexible segments gracefully unfold with materials like polyimide (PI) films. Copper foils play a pivotal role in crafting conductive pathways.
How is the Manufacturing Symphony of Rigid-flex Substrates Conducted?
The manufacturing choreography encompasses steps like layout design, meticulous preparation of rigid and flexible materials, layered assembly, adhesive bonding, precision drilling for vias, copper plating, component integration, and a symphony of quality testing.
Which Materials Form the Backbone of Rigid-flex Substrates?
Traditional PCB materials like FR-4 laminates build the robust foundation of rigid sections, while flexible segments gracefully unfold with materials like polyimide (PI) films. Copper foils play a pivotal role in crafting conductive pathways.
How Does the Flexibility of Rigid-flex Substrates Influence Design Compositions?
The inherent flexibility of rigid-flex substrates acts as a design virtuoso, enabling the creation of products with avant-garde shapes and configurations. This flexibility becomes a crucial asset in applications pushing the boundaries of traditional designs.
Does the Integration of Rigid-flex Substrates Elevate Overall Reliability?
Indeed, the integration of rigid-flex substrates orchestrates an enhancement in reliability. By minimizing reliance on connectors and cables, this integrated design symphony contributes to an overall robust and reliable performance.
What Harmonies Should Designers Consider in the Composition of Rigid-flex Substrates?
Designers should harmonize considerations like required flexibility, thermal management, material selection, layer stackup, and alignment with the unique notes of specific application needs.
Conclusion
In summary, the narrative of rigid-flex packaging substrates unfolds as an innovative synthesis, seamlessly interweaving rigidity and flexibility within a single, cohesive composition. These substrates emerge not merely as components but as dynamic solutions, transcending conventional PCB designs.
The merits of rigid-flex substrates, including spatial optimization, adaptability, and heightened reliability, position them as influential players across diverse industries—from electronics to aerospace. Their capacity to gracefully conform to unconventional shapes and maximize spatial efficiency makes them instrumental in sculpting the contours of modern electronic devices.
The manufacturing journey of rigid-flex substrates is a carefully choreographed process, from the inception of layout design to the integration of electronic components and the rigorous orchestration of quality tests. This manufacturing symphony brings together an array of materials, including FR-4 laminates, polyimide films, and copper foils, conducting a harmonious 3D assembly that pushes the boundaries of traditional PCBs.
As designers explore the flexible dimensions of rigid-flex substrates, these substrates become a canvas for creative innovation—a space where unconventional shapes and configurations find expression. The minimized dependence on connectors and cables not only streamlines design but also elevates the overall reliability, making them resilient performers even in the face of challenging environmental conditions.
In essence, rigid-flex packaging substrates emerge as dynamic catalysts in the evolution of electronic design, offering a fusion of stability and flexibility that resonates with the needs of contemporary applications. As technology continues its march forward, these substrates stand poised to play an increasingly central role, providing a dynamic platform for the unfolding tapestry of future electronic innovations.