Rogers 4003C PCB manufacturing
Rogers 4003C PCB Vendor, Ro4003c PCB and Rogers Series material PCB manufacturer, We offer microtrace and minimum spacing Rogers PCBs from 2 layer to 30 layers. HDI rogers PCBs with Mixed dielectric layer, such as Rogers & FR4, or other types PCB Mixed dielectric.
Rogers 4003C PCBs are high-performance printed circuit boards manufactured using Rogers 4003C laminate material. Renowned for their exceptional electrical properties, these PCBs offer low dielectric loss, stable performance across a wide temperature range, and excellent dimensional stability. Designed for high-frequency and high-speed applications, Rogers 4003C PCBs ensure superior signal integrity and reliability, making them ideal for critical industries such as aerospace, defense, telecommunications, and medical devices. Fabricated with advanced techniques and strict quality control measures, these PCBs adhere to industry standards, ensuring consistent and reliable performance. With their ability to meet the stringent demands of modern electronics, Rogers 4003C PCBs serve as the backbone for cutting-edge technologies, enabling innovation and advancement in various fields.
What is a Rogers 4003C PCB?
A Rogers 4003C PCB refers to a type of printed circuit board (PCB) made using Rogers 4003C laminates. Rogers Corporation is a well-known manufacturer of high-performance specialty materials used in various industries, including electronics. Rogers 4003C is a type of high-frequency laminate material commonly used in RF (radio frequency) and microwave applications.
The “4003C” designation signifies the specific type of laminate material composition and properties provided by Rogers Corporation. These laminates offer excellent electrical performance, stability over a wide range of temperatures, and low dielectric loss, making them suitable for applications where signal integrity is crucial, such as in telecommunications, aerospace, defense, and high-speed digital circuits.
PCBs manufactured using Rogers 4003C laminates are often used in high-frequency and high-speed applications where maintaining signal integrity and minimizing signal loss are essential requirements. These PCBs are typically designed for applications like RF/microwave circuitry, antennas, high-speed digital circuits, and other demanding electronic systems.
What are the Rogers 4003C PCB Design Guidelines?
The design guidelines for Rogers 4003C PCBs typically include recommendations and best practices to ensure optimal performance and reliability of the printed circuit board. While specific guidelines may vary based on the application and requirements, some common recommendations for designing PCBs with Rogers 4003C laminates include:
- Material Selection: Choose Rogers 4003C laminate material for its excellent high-frequency performance, low dielectric loss, and stability over a wide temperature range.
- Layer Stackup: Design an appropriate layer stackup considering the impedance requirements, signal integrity, and manufacturing constraints. Ensure proper impedance matching for high-speed signal transmission.
- Trace Width and Spacing: Follow recommended trace width and spacing guidelines to maintain controlled impedance and minimize signal loss. These parameters are crucial for high-frequency signal integrity.
- Via Design: Optimize via placement and design to minimize impedance discontinuities and ensure signal integrity. Use proper via structures such as plated-through vias (PTH) or microvias for high-density designs.
- Grounding and Power Planes: Implement a solid grounding strategy and power distribution network to minimize noise, reduce electromagnetic interference (EMI), and enhance signal integrity. Ensure low-inductance paths for power distribution.
- Component Placement: Carefully place components to minimize signal path lengths, reduce parasitic effects, and optimize signal integrity. Consideration should be given to high-speed signal paths and critical components.
- Thermal Management: Address thermal considerations by providing adequate thermal relief for components, proper heat sinking for high-power components, and optimizing copper pour for thermal dissipation.
- Manufacturability: Design the PCB with manufacturability in mind, considering factors such as panelization, solder mask design, and manufacturing tolerances to ensure smooth production processes.
- Signal Integrity Analysis:Perform signal integrity simulations and analyses using appropriate tools to validate the design and ensure compliance with performance requirements.
- Testing and Validation: Conduct thorough testing and validation of the PCB prototype to verify its performance, impedance characteristics, and reliability before mass production.
By adhering to these design guidelines, engineers can develop Rogers 4003C PCBs that meet the stringent requirements of high-frequency and high-speed applications while ensuring optimal performance, reliability, and manufacturability.
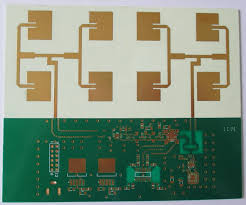
Rogers 4003C PCB Vendor
What is the Rogers 4003C PCB Fabrication Process?
The fabrication process for Rogers 4003C PCBs involves several steps, similar to the fabrication process for other types of printed circuit boards. Here is an overview of the typical fabrication process:
- Design: The PCB design process begins with schematic capture and layout using PCB design software. Engineers design the circuit layout, including component placement, routing, and layer stackup, while adhering to design guidelines for Rogers 4003C laminates.
- Preparation of Substrate Material: The first step in PCB fabrication is the preparation of the substrate material, which in this case is the Rogers 4003C laminate. This involves cutting the laminate sheets to the required size and cleaning them to remove any contaminants that could affect the bonding process.
- Layer Stackup: Depending on the design requirements, multiple layers of Rogers 4003C laminate may be stacked together with pre-preg layers in between to create a multilayer PCB. The layer stackup is carefully designed to meet impedance requirements and signal integrity considerations.
- Copper Cladding: Copper foil is then bonded to the surfaces of the laminate sheets using heat and pressure. The copper foil is etched to remove excess copper and define the traces and pads according to the PCB design.
- Drilling: Precision holes are drilled through the laminate stack at specified locations for vias and component mounting holes. Advanced techniques like laser drilling may be used for high-density designs.
- Plating: After drilling, the holes are plated with a conductive material, typically copper, to create the vias that establish electrical connections between different layers of the PCB.
- Etching:The outer layers of copper foil are etched away using chemical processes, leaving behind the desired traces and pads defined by the PCB design.
- Lamination: The layered structure of the PCB is assembled and laminated together under heat and pressure to bond the layers and ensure the integrity of the PCB stackup.
- Solder Mask Application: A solder mask is applied over the PCB surfaces to protect the copper traces from oxidation and facilitate soldering during assembly. Openings are created in the solder mask to expose the pads for component soldering.
- Silkscreen Printing: Optionally, component labels, logos, and other markings are printed onto the PCB surfaces using a silkscreen printing process for identification and assembly guidance.
- Surface Finish: A surface finish is applied to the exposed copper surfaces to improve solderability and prevent oxidation. Common surface finishes include HASL (Hot Air Solder Leveling), ENIG (Electroless Nickel Immersion Gold), and OSP (Organic Solderability Preservatives).
- Testing and Inspection: The fabricated PCBs undergo electrical testing, visual inspection, and quality assurance checks to ensure they meet the specifications and quality standards.
- Panelization and Routing: After passing inspection, the individual PCBs may be routed out of the larger panel for individual use, or they may remain part of a panel for ease of handling during assembly.
- Final Inspection and Packaging: The finished PCBs are inspected one final time before being packed and shipped to the customer or sent for further assembly.
Throughout the fabrication process, strict quality control measures are implemented to ensure the integrity, reliability, and performance of the Rogers 4003C PCBs. Advanced manufacturing techniques and equipment may be employed to meet the high precision and quality standards required for high-frequency and high-speed applications.
How do you manufacture a Rogers 4003C PCB?
Manufacturing a Rogers 4003C PCB involves a series of steps that are similar to the general PCB fabrication process, but with specific considerations tailored to the properties of Rogers 4003C laminate material. Here’s a detailed overview of how Rogers 4003C PCBs are manufactured:
- Material Preparation: The process begins with the preparation of Rogers 4003C laminate material. This involves cutting the laminate sheets to the required dimensions according to the PCB design specifications.
- Drilling: Precision holes are drilled into the laminate material at specific locations based on the PCB design. These holes will later accommodate vias and component mounting.
- Copper Cladding: Copper foil is bonded to one or both sides of the laminate material using heat and pressure. The thickness of the copper foil depends on the design requirements.
- Etching: A chemical etching process is used to remove excess copper from the surface of the laminate, leaving behind the desired circuit traces and pads as per the PCB design.
- Lamination: Multiple layers of copper-clad laminate material may be stacked together, along with prepreg layers, to create a multilayer PCB structure. The stack is then laminated together under heat and pressure to bond the layers.
- Plating: After drilling, the holes are plated with a conductive material (typically copper) to create vias that establish electrical connections between different layers of the PCB.
- Solder Mask Application:A solder mask is applied over the PCB surfaces to protect the copper traces from oxidation and facilitate soldering during assembly. Openings are created in the solder mask to expose the pads for component soldering.
- Surface Finish: A surface finish is applied to the exposed copper surfaces to improve solderability and prevent oxidation. Common surface finishes for Rogers 4003C PCBs include HASL (Hot Air Solder Leveling), ENIG (Electroless Nickel Immersion Gold), and OSP (Organic Solderability Preservatives).
- Silkscreen Printing: Optionally, component labels, logos, and other markings may be printed onto the PCB surfaces using a silkscreen printing process for identification and assembly guidance.
- Testing and Inspection: The fabricated PCBs undergo electrical testing, visual inspection, and quality assurance checks to ensure they meet the specifications and quality standards.
- Panelization and Routing: After passing inspection, the individual PCBs may be routed out of the larger panel for individual use, or they may remain part of a panel for ease of handling during assembly.
- Final Inspection and Packaging: The finished PCBs are inspected one final time before being packed and shipped to the customer or sent for further assembly.
Throughout the manufacturing process, strict quality control measures are implemented to ensure the integrity, reliability, and performance of the Rogers 4003C PCBs. Advanced manufacturing techniques and equipment may be employed to meet the high precision and quality standards required for high-frequency and high-speed applications.
How much should a Rogers 4003C PCB cost?
The cost of a Rogers 4003C PCB can vary significantly depending on various factors such as the size and complexity of the PCB, the number of layers, the quantity ordered, the manufacturing processes involved, and the supplier or manufacturer chosen. Additionally, factors like lead time, quality standards, and additional services (such as assembly or testing) can also affect the overall cost.
As a rough estimate, Rogers 4003C PCBs tend to be more expensive compared to standard FR-4 PCBs due to the higher performance characteristics and specialized materials involved. However, exact pricing would require obtaining quotes from PCB manufacturers or suppliers based on specific design requirements and quantities.
For a basic single-layer Rogers 4003C PCB of standard size and quantity, you might expect a starting price of several hundred dollars. However, for complex multilayer PCBs or larger quantities, the cost can increase significantly, potentially ranging into thousands of dollars or more.
It’s advisable to contact multiple PCB manufacturers or suppliers to request quotes based on your specific design requirements and quantities. This allows you to compare prices and services to find the best option that meets your needs within your budget. Additionally, keep in mind that factors such as quality, reliability, and customer support are also important considerations when selecting a PCB supplier.
What is Rogers 4003C PCB base material?
The base material of Rogers 4003C PCB is a specialty laminate manufactured by Rogers Corporation. Rogers 4003C laminate is composed of woven fiberglass reinforcement combined with a ceramic-filled hydrocarbon resin system. This combination of materials provides excellent electrical performance, dimensional stability, and mechanical strength, making it well-suited for high-frequency and high-speed applications.
The key properties of Rogers 4003C laminate include:
- Dielectric Constant (εr): Typically around 3.38 at room temperature, which remains stable over a wide frequency range.
- Loss Tangent (Dissipation Factor): Low loss tangent, typically around 0.0027 at 10 GHz, ensuring minimal signal loss and maintaining signal integrity.
- Thermal Stability: The material exhibits good thermal stability over a wide temperature range, making it suitable for applications with demanding thermal environments.
- Dimensional Stability: Rogers 4003C laminate offers excellent dimensional stability, which is essential for maintaining tight tolerances in PCB manufacturing.
- Flammability Rating: Typically UL 94 V-0 rated, indicating good flame resistance.
- RoHS Compliance: The material complies with RoHS (Restriction of Hazardous Substances) regulations, ensuring it is free from hazardous substances such as lead and mercury.
Overall, Rogers 4003C laminate is specifically engineered to meet the stringent requirements of high-frequency and high-speed PCB applications, providing exceptional electrical performance while maintaining reliability and stability.
Which company manufactures Rogers 4003C PCBs?
Manufacturing of Rogers 4003C PCBs is typically carried out by circuit board manufacturers with professional expertise and experience. These companies possess advanced production equipment and technology to manufacture high-quality Rogers 4003C PCBs according to customer requirements and design specifications.
Our company is a professional circuit board manufacturer with years of experience and extensive technical knowledge. We are committed to providing customers with high-performance, high-quality printed circuit board solutions, including Rogers 4003C PCBs. Here are our capabilities and advantages in producing Rogers 4003C PCBs:
- Professional Team: We have an experienced engineering team and technical staff capable of understanding and meeting customer needs, providing professional technical support and consulting services.
- Advanced Equipment: We utilize state-of-the-art production equipment and technology, including automated production lines and precision machining equipment, to ensure the efficiency and precision of the production process.
- Quality Control: We strictly adhere to international standards and quality management systems, ensuring that every Rogers 4003C PCB meets customer requirements and standards through rigorous quality control and testing procedures.
- Customization Capability: We can customize various types and specifications of Rogers 4003C PCBs according to customer-specific requirements, including single-layer, double-layer, and multilayer boards, to meet the needs of different application scenarios.
- Fast Delivery: With efficient production processes and supply chain management systems, we can deliver customer orders promptly, meeting the requirements of urgent customer needs.
In summary, our company has the professional capabilities, technical strength, and production capacity required to manufacture Rogers 4003C PCBs. Whatever the customer’s requirements, we can provide them with high-quality, reliable Rogers 4003C PCB solutions and comprehensive support for the success of their projects.
What are the 7 qualities of good customer service?
Good customer service is characterized by several key qualities that contribute to positive interactions and relationships with customers. Here are seven qualities of good customer service:
- Responsiveness: Good customer service involves promptly addressing customer inquiries, concerns, and requests. Responding in a timely manner demonstrates attentiveness and respect for the customer’s time.
- Empathy: Empathy involves understanding and acknowledging the customer’s perspective, feelings, and needs. Empathetic customer service representatives demonstrate genuine concern and compassion, fostering trust and rapport with customers.
- Clear Communication: Effective communication is essential for providing good customer service. Clear and concise communication helps ensure that customers understand information, instructions, and solutions provided, minimizing misunderstandings and frustration.
- Problem-Solving Skills: Good customer service involves the ability to effectively resolve customer issues and problems. Customer service representatives should be equipped with problem-solving skills to identify solutions, address concerns, and satisfy customer needs.
- Professionalism: Professionalism encompasses maintaining a positive attitude, demeanor, and appearance when interacting with customers. Professional customer service representatives exhibit courtesy, respect, and integrity, enhancing the customer experience.
- Product Knowledge: Good customer service requires a deep understanding of the products or services offered. Knowledgeable customer service representatives can provide accurate information, answer questions, and offer relevant recommendations, instilling confidence in customers.
- Consistency: Consistency is key to delivering good customer service across all interactions and touchpoints. Consistent service standards, policies, and procedures help build trust and reliability, reinforcing the customer’s confidence in the company.
By embodying these qualities, businesses can cultivate strong customer relationships, foster loyalty, and differentiate themselves in competitive markets.
FAQs
What is Rogers 4003C PCB?
Rogers 4003C PCB refers to a printed circuit board (PCB) manufactured using Rogers 4003C laminate material. Rogers 4003C is a high-frequency laminate known for its excellent electrical performance and stability, making it suitable for applications requiring signal integrity, such as RF/microwave circuits.
What are the advantages of Rogers 4003C PCBs?
Rogers 4003C PCBs offer several advantages, including low dielectric loss, stable electrical properties over a wide temperature range, excellent dimensional stability, and high reliability. These properties make them ideal for high-frequency and high-speed applications.
What applications are Rogers 4003C PCBs used for?
Rogers 4003C PCBs are commonly used in applications such as RF/microwave circuits, antennas, high-speed digital circuits, aerospace, defense, telecommunications, and medical devices where maintaining signal integrity is critical.
What are the design considerations for Rogers 4003C PCBs?
Design considerations for Rogers 4003C PCBs include impedance matching, controlled trace width and spacing, proper grounding techniques, thermal management, and adherence to manufacturer’s guidelines for optimal performance.
How are Rogers 4003C PCBs fabricated?
Fabrication of Rogers 4003C PCBs involves processes such as material preparation, layer stackup, copper cladding, drilling, plating, etching, lamination, solder mask application, surface finish, and testing. These processes ensure the creation of high-quality PCBs meeting design specifications.
What are the cost considerations for Rogers 4003C PCBs?
The cost of Rogers 4003C PCBs depends on factors such as size, complexity, quantity, manufacturing processes involved, and supplier. While they may be more expensive than standard FR-4 PCBs due to their specialized properties, the benefits in performance often justify the investment.
Where can I purchase Rogers 4003C PCBs?
Rogers 4003C PCBs can be purchased from reputable PCB manufacturers and suppliers specializing in high-frequency PCBs. It’s essential to choose a supplier with experience in handling Rogers materials and a track record of producing quality PCBs.
What are the quality standards for Rogers 4003C PCBs?
Rogers 4003C PCBs should adhere to industry standards such as IPC-A-600 for acceptance criteria, IPC-6012 for performance specifications, and ISO 9001 for quality management systems. Compliance with these standards ensures the reliability and performance of the PCBs.