Rogers 5880 Substrate Manufacturer
Rogers 5880 Substrate Manufacturer,Rogers 5880 substrate is a high-frequency laminate renowned for its exceptional electrical performance and stability. It features a low dielectric constant (2.20 ± 0.02) and low loss tangent (0.0009 at 10 GHz), making it ideal for high-frequency applications such as antennas, microwave circuits, and radar systems. The substrate is composed of PTFE (polytetrafluoroethylene) reinforced with glass microfibers, ensuring excellent dimensional stability and mechanical integrity. Rogers 5880 is also known for its low moisture absorption and high thermal conductivity, which enhance its reliability and performance in demanding environments. This combination of properties makes Rogers 5880 a preferred choice for designers seeking high-performance RF and microwave solutions.
What is Ultra-small Size BGA Substrates?
Ultra-small Size BGA (Ball Grid Array) substrates are high-density substrates used for integrated circuit packaging, widely applied in electronic devices, especially in scenarios that require space-saving and enhanced performance. Compared to traditional BGA packages, ultra-small BGA substrates are characterized by their smaller package size and denser pin arrangement, making them more flexible in design and able to meet the demands of modern miniaturized electronic products.
Ultra-small BGA substrates are typically made from high-performance materials such as FR-4, ceramic, or high-frequency materials, offering excellent electrical properties and thermal conductivity. Their design allows for higher pin density, accommodating more complex circuit designs and supporting higher frequencies and faster data transmission rates. These substrates also provide outstanding thermal performance, effectively dissipating the heat generated by electronic components during operation, thereby extending the product’s lifespan.
Moreover, the manufacturing process of ultra-small BGA substrates requires precise craftsmanship and strict quality control to ensure the reliability and consistency of solder joints. They are extensively used in smartphones, tablets, smart wearables, and other miniaturized electronic products, driving the electronics industry toward higher integration and smaller sizes. With continuous technological advancements, the application scope of ultra-small BGA substrates is expected to expand further, leading to more innovative electronic products.
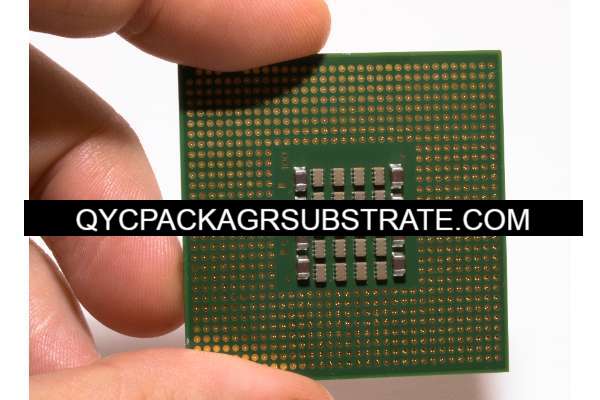
Rogers 5880 Substrate Manufacturer
What are the Ultra-small Size BGA Substrates Design Guidelines?
Design guidelines for ultra-small size BGA (Ball Grid Array) substrates typically focus on several key aspects to ensure optimal performance and reliability:
- Pad and Via Design: Proper pad and via design is crucial to ensure adequate electrical connectivity and signal integrity. Guidelines include appropriate pad sizes and spacing, via types (such as microvias for high-density routing), and their placements to minimize signal degradation and impedance issues.
- Thermal Management:Effective thermal management is essential due to the compact size and high component density of ultra-small BGAs. Guidelines often include recommendations for thermal vias, thermal pads, and heat dissipation strategies to prevent overheating and ensure long-term reliability.
- Material Selection: Choosing the right substrate material is critical for achieving desired electrical and thermal performance. High-performance materials like FR-4, ceramic, or specialized high-frequency laminates are common choices. Guidelines may specify material properties such as dielectric constant, thermal conductivity, and coefficient of thermal expansion (CTE).
- Routing and Trace Considerations: Routing guidelines focus on minimizing crosstalk, impedance mismatches, and signal loss. This includes guidelines for trace widths, spacing, and impedance control techniques to maintain signal integrity throughout the PCB.
- Assembly and Manufacturing Constraints: Design guidelines also address assembly and manufacturing constraints specific to ultra-small BGAs. These may include solder mask requirements, assembly tolerances for fine-pitch components, and considerations for automated assembly processes.
- Reliability and Testing: Ensuring reliability through design involves guidelines for design for manufacturability (DFM), design for testability (DFT), and reliability testing methodologies. This ensures that the ultra-small BGA substrates can meet performance specifications and withstand operational stresses over their lifecycle.
- Electromagnetic Compatibility (EMC): Guidelines for EMC compliance include strategies to minimize electromagnetic interference (EMI) and ensure the substrate design does not adversely affect nearby electronic components or systems.
These design guidelines collectively aim to optimize the performance, reliability, and manufacturability of ultra-small size BGA substrates, supporting the development of high-density, miniaturized electronic products.
What is the Ultra-small Size BGA Substrates Fabrication Process?
The fabrication process for ultra-small size BGA (Ball Grid Array) substrates involves several key steps to ensure precision and reliability. Here’s an overview of the typical fabrication process:
- Material Preparation: High-performance substrate materials, such as FR-4, ceramic, or specialized laminates, are selected based on the electrical and thermal requirements. The material is cut to the desired size and thickness.
- Layer Lamination: If the design requires multiple layers, the layers are laminated together. This process involves applying heat and pressure to bond the layers, ensuring uniform adhesion.
- Drilling: Precision drilling is performed to create vias and holes for component leads and interconnects. Microvias may be used for high-density designs, allowing for smaller hole sizes and finer pitch.
- Copper Plating: The drilled holes are plated with copper to establish electrical connectivity. This can include through-hole plating for vias and surface plating for pads.
- Patterning: A photolithography process is used to apply a photoresist layer, which is then exposed to UV light through a mask that defines the circuit patterns. The unexposed areas are developed away, revealing the copper surface.
- Etching: The exposed copper areas are etched away to create the desired circuit patterns on the substrate. This step defines the traces that connect various components.
- Solder Mask Application: A solder mask is applied to protect the copper traces and pads, preventing solder bridging during assembly. The solder mask is usually green but can come in other colors.
- Surface Finish: A surface finish, such as ENIG (Electroless Nickel Immersion Gold) or OSP (Organic Solderability Preservative), is applied to the pads to enhance solderability and prevent oxidation.
- Ball Attachment:For BGA substrates, solder balls are attached to the pads. This can be done through a stencil printing process where solder paste is applied, or pre-formed solder balls can be reflowed onto the pads.
- Testing and Inspection: The substrates undergo various tests, including electrical testing for continuity and short circuits, as well as visual inspections to ensure quality and reliability.
- Final Finishing: Any additional finishing processes, such as edge trimming or final cleaning, are completed before the substrates are ready for assembly.
This fabrication process ensures that ultra-small size BGA substrates meet the stringent requirements for modern electronics, providing high-density interconnects in compact form factors.
How do you manufacture Ultra-small Size BGA Substrates?
Manufacturing ultra-small size BGA (Ball Grid Array) substrates involves a series of precise steps to ensure high quality and reliability. Here’s a detailed overview of the manufacturing process:
- Material Selection: Choose suitable substrate materials such as FR-4, ceramic, or high-frequency laminates based on the specific application requirements for electrical performance and thermal management.
- Cutting and Preparation: The selected materials are cut to the required dimensions and thickness. Special care is taken to ensure that the material surface is clean and free of contaminants.
- Layer Lamination:If the design involves multiple layers, the layers are stacked and laminated together using heat and pressure to create a solid composite substrate.
- Drilling: High-precision drilling is performed to create vias and holes. Advanced techniques like laser drilling may be used for microvias, which are essential for high-density designs.
- Copper Plating:The drilled holes are plated with copper through an electroplating process, establishing electrical connections between layers and providing pads for component mounting.
- Photoresist Application: A photoresist layer is applied to the substrate. This layer is sensitive to UV light and is used in the subsequent photolithography process.
- Photolithography: A photomask is used to expose the photoresist to UV light, transferring the desired circuit pattern onto the substrate. The exposed photoresist is developed, leaving the circuit pattern intact.
- Etching: The exposed copper is etched away using chemical solutions, forming the required traces and pads according to the design specifications.
- Solder Mask Application: A solder mask is applied to protect the copper traces and pads. This helps prevent solder bridging during assembly and provides electrical insulation.
- Surface Finishing: The pads receive a surface finish, such as ENIG (Electroless Nickel Immersion Gold) or OSP (Organic Solderability Preservative), which enhances solderability and prevents oxidation.
- Ball Attachment: Solder balls are attached to the pads either by stencil printing solder paste or by placing pre-formed solder balls and reflowing them onto the pads.
- Testing and Inspection: The substrates undergo rigorous testing, including electrical continuity tests and visual inspections, to ensure there are no defects and that they meet quality standards.
- Final Processing: Any additional finishing processes, such as edge trimming and cleaning, are performed before the substrates are packaged and shipped for assembly.
This manufacturing process enables the production of ultra-small size BGA substrates that meet the high-performance demands of modern electronic applications.
How much should Ultra-small Size BGA Substrates cost?
The cost of ultra-small size BGA (Ball Grid Array) substrates can vary widely based on several factors, including:
- Material Type: Different materials, such as FR-4, ceramic, or specialized high-frequency laminates, have varying costs.
- Layer Count: Multi-layer substrates typically cost more due to the complexity of fabrication.
- Design Complexity: More intricate designs with higher density and tighter tolerances will generally increase manufacturing costs.
- Volume: Higher production volumes can reduce per-unit costs due to economies of scale.
- Surface Finishing: The choice of surface finish (e.g., ENIG, OSP) can also impact pricing.
- Lead Time: Rush orders may incur additional costs.
Typically, prices can range from a few dollars to several tens of dollars per substrate, depending on the specifications. For accurate pricing, it’s best to consult with specific manufacturers, as they can provide quotes based on detailed requirements.
What is Ultra-small Size BGA Substrates base material?
Ultra-small size BGA (Ball Grid Array) substrates are typically made from several types of base materials, chosen based on their electrical, thermal, and mechanical properties. Common base materials include:
- FR-4: A widely used fiberglass-reinforced epoxy laminate, known for its good electrical insulation and mechanical properties. It is cost-effective and suitable for many applications.
- Ceramic: Provides excellent thermal stability and electrical performance. Ceramic substrates are often used in high-frequency and high-power applications due to their superior heat dissipation capabilities.
- High-Frequency Laminates: Materials like PTFE (Teflon) or specialized resins that offer low dielectric constants and low loss tangent, making them ideal for RF and microwave applications.
- Polyimide: Known for high thermal stability and flexibility, polyimide is used in applications requiring high-temperature performance.
The choice of base material depends on the specific application requirements, including frequency, thermal management, and cost considerations.
Which company makes Ultra-small Size BGA Substrates?
Currently, many companies focus on producing ultra-small size BGA (Ball Grid Array) substrates. These companies typically have advanced manufacturing technologies and specialized design teams to meet the high-density packaging demands of modern electronic products. Here are some well-known manufacturers:
- TSMC (Taiwan Semiconductor Manufacturing Company): As a leading global semiconductor foundry, TSMC not only provides chip manufacturing services but also engages in high-performance packaging technologies, including the production of ultra-small BGA substrates.
- Intel: Intel, known for its processors, also develops high-performance packaging solutions, including ultra-small BGA substrates, which are widely used in high-end computing and mobile devices.
- ASE Group: As one of the world’s largest providers of packaging and testing services, ASE focuses on various packaging technologies, including the design and manufacture of ultra-small BGA substrates.
- Samsung Electronics:With strong capabilities in semiconductor and display technologies, Samsung produces ultra-small BGA substrates that are commonly used in smartphones and other consumer electronics.
- Micron: Micron primarily manufactures memory and storage solutions, and its packaging technology includes ultra-small BGA, suitable for high-performance computing and embedded systems.
In this competitive market, our company is also capable of producing ultra-small BGA substrates. We possess advanced production equipment and a team of experienced engineers, enabling us to deliver high-quality products. Our manufacturing process includes stringent quality control and testing to ensure that each substrate meets the performance and reliability requirements of our customers.
Additionally, our company offers customized services, designing and manufacturing ultra-small BGA substrates according to specific customer needs. Whether it’s material selection, layer design, or surface treatment processes, we can respond flexibly to provide the best solutions for our clients.
By closely collaborating with customers, we can better understand market demands and continuously improve our manufacturing processes, ensuring our products are competitive in both technology and cost. Our goal is to become the preferred partner for customers in the ultra-small BGA substrate sector, helping them achieve success in the rapidly evolving electronics industry.
What are the 7 qualities of good customer service?
Good customer service is essential for building strong relationships with customers and fostering loyalty. Here are seven key qualities of effective customer service:
- Empathy: Understanding and relating to the customer’s feelings and experiences helps create a connection and shows that their concerns are valued.
- Responsiveness:Timely responses to inquiries or issues demonstrate that the company values the customer’s time and is eager to assist them.
- Knowledgeability: A well-informed customer service representative can provide accurate information and solutions, enhancing the customer’s experience.
- Communication Skills: Clear and effective communication helps prevent misunderstandings and ensures that customers feel heard and understood.
- Patience: Taking the time to listen and assist customers, even in challenging situations, shows that the company is dedicated to providing support.
- Positivity: A friendly and positive attitude can significantly impact customer interactions, making them feel welcome and appreciated.
- Follow-up: Checking in with customers after resolving their issues or answering their questions demonstrates commitment to their satisfaction and fosters trust.
These qualities together create a positive customer experience, encouraging repeat business and positive word-of-mouth referrals.
FAQs
What are ultra-small size BGA substrates?
Ultra-small size BGA substrates are high-density circuit boards designed for packaging integrated circuits, featuring a compact footprint and closely spaced solder balls to maximize space efficiency in electronic devices.
What materials are used in ultra-small size BGA substrates?
Common materials include FR-4, ceramic, and specialized high-frequency laminates, chosen for their electrical and thermal properties.
What industries use ultra-small size BGA substrates?
These substrates are widely used in consumer electronics, telecommunications, automotive, and medical devices, where miniaturization and high performance are critical.
What are the benefits of using ultra-small size BGA substrates?
Benefits include reduced size and weight, improved thermal management, enhanced electrical performance, and higher component density, allowing for more compact device designs.
How are ultra-small size BGA substrates manufactured?
The manufacturing process involves material preparation, layer lamination, drilling, copper plating, photolithography, etching, solder mask application, and ball attachment, followed by testing and inspection.
What are the design considerations for ultra-small size BGA substrates?
Key considerations include pad and via design, thermal management, routing and trace widths, material selection, and assembly constraints to ensure performance and reliability.
What is the typical lead time for ultra-small size BGA substrates?
Lead times can vary based on complexity and volume but typically range from a few weeks to several months. Custom designs may require longer lead times.