Rogers PCB Manufacturer
Rogers PCB Manufacturer,Rogers PCBs, crafted with precision using advanced materials from Rogers Corporation, epitomize excellence in high-frequency circuitry. Renowned for their low dielectric loss and stable performance across temperature ranges, Rogers PCBs cater to industries demanding superior signal integrity and reliability. Engineered for aerospace, telecommunications, and cutting-edge electronics, they offer optimal solutions for RF, microwave, and high-speed digital applications. With meticulous design and fabrication, Rogers PCBs ensure seamless functionality, making them the preferred choice for mission-critical systems where performance is paramount. Experience the pinnacle of PCB innovation with Rogers, setting the standard for excellence in modern electronics.
What is a Rogers PCB?
A Rogers PCB, short for Rogers Printed Circuit Board, is a type of circuit board made using materials from Rogers Corporation, a leading manufacturer of high-performance specialty materials. These PCBs are known for their exceptional electrical properties, particularly in high-frequency applications like microwave and radio frequency (RF) circuits.
Rogers PCBs are constructed using specialized laminates composed of ceramic-filled PTFE (polytetrafluoroethylene) or other high-frequency dielectric materials. These materials offer low dielectric loss, excellent stability over a wide range of temperatures, and consistent electrical properties across a range of frequencies. This makes Rogers PCBs ideal for applications requiring precise signal integrity and minimal loss, such as in aerospace, telecommunications, radar systems, and satellite communications.
The unique properties of Rogers PCBs make them well-suited for demanding environments where reliability and performance are critical. However, they tend to be more expensive than standard FR-4 PCBs due to the specialized materials and manufacturing processes involved. Despite the higher cost, the superior electrical performance and reliability of Rogers PCBs often justify their use in high-frequency and high-power applications where performance is paramount.
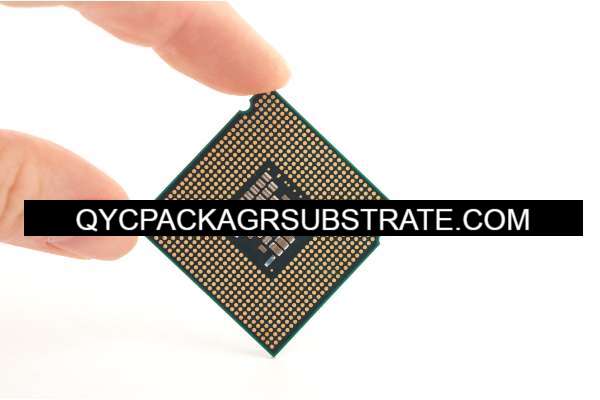
Rogers PCB Manufacturer
What are the Rogers PCB Design Guidelines?
Designing with Rogers PCB materials requires adherence to specific guidelines to ensure optimal performance. Here are some general guidelines:
- Material Selection: Choose the appropriate Rogers laminate material based on your application requirements, considering factors such as dielectric constant (Dk), dissipation factor (Df), and operating frequency range.
- Layer Stackup: Design the layer stackup carefully to maintain controlled impedance and minimize signal losses. Follow manufacturer recommendations for layer thickness, dielectric thickness, and copper thickness.
- Impedance Control: Maintain consistent trace widths, spacing, and dielectric thickness to control impedance. Use impedance calculation tools or simulation software to ensure accurate impedance matching.
- Ground Plane: Include solid ground planes adjacent to signal layers to provide shielding, reduce electromagnetic interference (EMI), and improve signal integrity.
- Trace Geometry: Use controlled impedance transmission lines with appropriate geometries (microstrips or striplines) to match the desired impedance. Maintain consistent trace widths and spacing to minimize signal distortion.
- Via Design: Use through-hole vias or blind/buried vias to transition signals between layers while maintaining controlled impedance. Minimize stub length to reduce signal reflections.
- Component Placement: Optimize component placement to minimize signal path lengths, reduce parasitic capacitance, and ensure signal integrity. Place high-speed components closer to each other to minimize signal skew.
- Thermal Management: Consider thermal management techniques such as thermal vias, copper pour, or heat sinks to dissipate heat efficiently, especially in high-power applications.
- Design for Manufacturability: Follow design rules and guidelines provided by the PCB manufacturer to ensure manufacturability and reliability. Consider factors such as minimum trace width/spacing, minimum drill size, and solder mask clearance.
- Simulation and Testing: Perform signal integrity simulations and prototype testing to verify the design’s performance before mass production. Use tools like SPICE simulation, electromagnetic simulation, and network analyzers for comprehensive analysis.
By following these guidelines, designers can ensure that Rogers PCB designs meet performance requirements and deliver reliable operation in high-frequency and high-speed applications. Additionally, consulting with experienced PCB designers or application engineers familiar with Rogers materials can provide valuable insights and assistance in optimizing the design for specific requirements.
What is the Rogers PCB Fabrication Process?
The fabrication process for Rogers PCBs is similar to that of standard printed circuit boards but involves additional considerations due to the specialized materials used. Here’s a general overview of the Rogers PCB fabrication process:
- Material Preparation: The process begins with the selection of the appropriate Rogers laminate material based on the specific requirements of the application. Rogers Corporation produces a range of high-performance laminates with different dielectric constants (Dk) and other properties. The chosen material is then prepared for use in the fabrication process.
- Prepreg Cutting and Layer Stacking: If the design involves multilayer PCBs, prepreg (pre-impregnated fiberglass material) is cut to the required dimensions. The prepreg layers, along with copper foil, are stacked according to the PCB design’s layer stackup. The layer stackup is carefully designed to achieve controlled impedance and signal integrity.
- Drilling:Precision drilling is performed to create holes for through-hole vias and component mounting. Special attention is paid to drill accuracy and registration to ensure alignment between layers.
- Copper Deposition: Copper is deposited onto the substrate surfaces using a process such as electroplating or chemical vapor deposition (CVD). This copper layer forms the conductive traces and pads on the PCB.
- Etching: A photoresist is applied to the copper layer, and the PCB is exposed to UV light through a photomask, which defines the trace patterns. After exposure, the PCB is developed to remove the unexposed photoresist, leaving behind the desired copper traces.
- Surface Finish:Surface finish options such as immersion gold, HASL (hot air solder leveling), or ENIG (electroless nickel immersion gold) may be applied to the copper traces to improve solderability and protect against oxidation.
- Solder Mask Application: A solder mask layer is applied over the copper traces, leaving only the areas for component mounting exposed. The solder mask protects the copper traces from environmental factors and prevents solder bridging during assembly.
- Silkscreen Printing: Component designators, logos, and other identifying information are printed onto the PCB surface using a silkscreening process.
- Routing and Profiling: The PCB is routed to separate individual boards, and any remaining copper is etched away. Precision routing ensures that the final PCBs match the intended dimensions and shape.
- Quality Control and Testing: The fabricated PCBs undergo rigorous quality control checks and testing to ensure they meet the specified design requirements. This may include electrical testing, dimensional inspection, and visual inspection.
- Final Finishing: After passing quality control, the PCBs may undergo final finishing processes such as edge plating or edge beveling before being packaged and shipped to the customer.
Throughout the fabrication process, strict adherence to design specifications and quality standards is essential to ensure the performance and reliability of the Rogers PCBs in their intended applications. Collaboration between PCB designers, fabricators, and manufacturers is often necessary to optimize the fabrication process for specific design requirements.
How do you manufacture a Rogers PCB?
Manufacturing a Rogers PCB involves several steps, from material selection to final testing. Here’s a detailed overview of the manufacturing process:
- Material Selection: Choose the appropriate Rogers laminate material based on the specific requirements of the application, such as frequency, signal integrity, and thermal properties.
- Panel Preparation:Cut the Rogers laminate material into panels of the desired size, taking into account the required number of PCBs per panel and any necessary fiducial marks for alignment.
- Layer Stackup Design:Design the layer stackup according to the PCB specifications, considering factors such as signal integrity, impedance control, and thermal management. This involves determining the arrangement of copper layers, prepreg layers, and Rogers laminate material.
- Copper Cladding: Apply copper foil to both sides of the Rogers laminate material using an adhesive or lamination process. The copper foil forms the conductive layers of the PCB.
- Drilling: Precisely drill holes in the panel for component mounting pads, vias, and interconnects. High-precision drilling equipment is used to ensure accuracy and consistency.
- Electroless Copper Plating: Coat the panel with a thin layer of electroless copper to ensure good adhesion between the substrate and the copper layers. This step prepares the panel for subsequent plating processes.
- Image Transfer: Apply a layer of photosensitive material, called photoresist, to the panel’s surface. Expose the photoresist to UV light through a photomask, transferring the PCB pattern onto the photoresist.
- Etching: Use chemical etching to remove the unwanted copper from the panel, leaving behind the desired copper traces and pads. The remaining photoresist acts as a protective mask during etching.
- Stripping and Cleaning:Remove the remaining photoresist and any etching residues from the panel’s surface using a stripping solution and cleaning process. This prepares the panel for the next manufacturing steps.
- Surface Finishing: Apply a surface finish to the exposed copper traces and pads to protect them from oxidation and improve solderability. Common surface finishes include immersion gold, HASL (Hot Air Solder Leveling), and ENIG (Electroless Nickel Immersion Gold).
- Solder Mask Application: Apply a solder mask layer over the entire panel, leaving openings for component pads and vias. The solder mask protects the copper traces from environmental factors and prevents solder bridges during assembly.
- Silkscreen Printing:Print component designators, logos, and other identifying information onto the panel’s surface using a silkscreen printing process. This step facilitates component placement and assembly.
- Routing and Profiling: Use precision routing equipment to separate individual PCBs from the panel and to cut any internal slots or cutouts. This step ensures that the PCBs have the correct dimensions and shape.
- Quality Control and Testing: Inspect the finished PCBs for defects, dimensional accuracy, and electrical continuity. Perform electrical testing to verify the functionality and performance of the PCBs according to the specified requirements.
- Packaging and Shipping: Package the finished PCBs securely to protect them during transit and storage. Ship the PCBs to the customer or assembly facility for further processing.
Throughout the manufacturing process, strict quality control measures and adherence to industry standards are essential to ensure the reliability and performance of the Rogers PCBs in their intended applications. Collaboration between PCB designers, fabricators, and manufacturers is often necessary to optimize the manufacturing process for specific design requirements.
How much should a Rogers PCB cost?
The cost of Rogers PCBs can vary significantly depending on various factors such as the complexity of the design, the choice of Rogers material, the number of layers, board size, surface finish, and quantity ordered. Here are some factors that influence the cost:
- Material Cost:Rogers materials tend to be more expensive compared to standard FR-4 materials due to their specialized properties and performance characteristics. The cost can vary depending on the specific Rogers material chosen for the PCB.
- Board Size and Thickness: Larger PCBs and thicker laminates typically cost more due to the increased material usage and processing requirements.
- Number of Layers: Multilayer PCBs require more materials and additional processing steps, which can increase the cost compared to single or double-sided PCBs.
- Surface Finish: The choice of surface finish, such as immersion gold or ENIG, can impact the cost. Some surface finishes are more expensive than others due to the materials and processes involved.
- Complexity of Design: PCBs with intricate trace patterns, tight tolerances, and high-density components may require additional manufacturing steps and higher precision, leading to increased costs.
- Quantity Ordered:Larger production volumes typically result in lower per-unit costs due to economies of scale. Ordering larger quantities can help reduce the cost per board.
- Lead Time:Expedited manufacturing and delivery options may incur additional costs compared to standard lead times.
To get an accurate cost estimate for a Rogers PCB, it’s best to consult with PCB manufacturers or suppliers. They can provide quotes based on your specific requirements, including the desired material, board specifications, quantity, and lead time. Additionally, many PCB manufacturers offer online quote calculators that allow you to input your design parameters and receive an instant cost estimate.
What is Rogers PCB base material?
Rogers PCBs use specialty materials manufactured by Rogers Corporation as the base substrate. These materials are engineered to provide high performance in terms of electrical properties, thermal stability, and reliability, making them ideal for demanding applications, particularly in high-frequency and high-speed designs.
Some common Rogers PCB base materials include:
- Rogers RO4000 Series: This series includes high-frequency laminates designed for applications requiring excellent signal integrity and low insertion loss over a wide frequency range. Materials in this series offer consistent dielectric constant (Dk) and low dissipation factor (Df) across a range of temperatures and frequencies.
- Rogers RO3000 Series: The RO3000 series features laminates optimized for high-speed digital and RF/microwave applications. These materials offer tight control over impedance, minimal signal loss, and excellent dimensional stability, making them suitable for high-speed digital and wireless communication systems.
- Rogers RO6000 Series: This series comprises thermoset high-performance laminates designed for high-frequency applications. Materials in this series offer low dielectric loss, stable electrical properties, and reliable performance in harsh environments, making them suitable for aerospace, defense, and automotive applications.
- Rogers RT/duroid Series:The RT/duroid series includes PTFE-based laminates known for their exceptional electrical properties, including low dielectric constant, low loss tangent, and high thermal conductivity. These materials are commonly used in high-frequency RF and microwave circuits where signal integrity and performance are critical.
These are just a few examples of Rogers PCB base materials, and Rogers Corporation offers a range of other specialty laminates tailored to specific application requirements. Each material in the Rogers portfolio is engineered with precise specifications to meet the needs of different industries and technologies, providing designers with options to optimize performance and reliability in their PCB designs.
Which company makes Rogers PCB?
Rogers PCBs are produced by Rogers Corporation. Rogers Corporation is a leading manufacturer of high-performance specialty materials headquartered in the United States, with global operations. The company focuses on developing and producing high-performance materials for various applications, including specialty laminates for printed circuit boards (PCBs).
Rogers Corporation’s Rogers PCB materials are widely used in fields such as high-frequency, radio frequency (RF), microwave, and high-speed digital circuits. These materials offer excellent electrical properties, thermal stability, and reliability, making them the preferred choice in many industries.
As a PCB manufacturer, our company is capable of producing Rogers PCBs. We have advanced manufacturing equipment and technology, and we have established partnerships with Rogers Corporation and other suppliers to ensure that we can provide high-quality, reliable, and high-performance Rogers PCB products.
Our manufacturing process adheres to industry standards and quality management systems, ensuring that each production step is rigorously monitored and controlled. Our team has extensive experience and expertise and can customize Rogers PCB designs according to customer requirements, providing technical support and solutions.
We are committed to providing customers with satisfactory products and services. Our goal is to establish long-term partnerships with customers and become their trusted collaborators. If you have any requirements or questions about Rogers PCBs or other PCB products, please feel free to contact us, and we will be happy to provide support and assistance.
What are the 7 qualities of good customer service?
Good customer service is characterized by several key qualities that contribute to a positive experience for customers. Here are seven important qualities:
- Responsiveness: Good customer service involves being prompt and attentive to customers’ needs and inquiries. Responding quickly to customer inquiries, whether through phone, email, or in-person interactions, demonstrates a commitment to addressing their concerns and providing assistance in a timely manner.
- Empathy: Empathy involves understanding and acknowledging customers’ feelings, concerns, and perspectives. Good customer service representatives listen actively, show genuine concern for customers’ issues, and strive to put themselves in the customers’ shoes to better understand their needs.
- Professionalism:Professionalism encompasses a range of behaviors and qualities, including courtesy, respect, and integrity. Good customer service representatives maintain a professional demeanor at all times, communicate clearly and effectively, and uphold ethical standards in their interactions with customers.
- Knowledgeability:Good customer service requires having a thorough understanding of the products or services offered by the company, as well as the policies, procedures, and resources available to assist customers. Knowledgeable representatives can provide accurate information, answer questions confidently, and offer helpful recommendations or solutions.
- Flexibility: Flexibility is essential in adapting to customers’ unique needs and situations. Good customer service representatives are adaptable and resourceful, capable of finding creative solutions to problems, accommodating special requests, and adjusting their approach based on individual customer preferences.
- Consistency: Consistency in service delivery helps build trust and reliability with customers. Good customer service is consistent across all channels and interactions, ensuring that customers receive the same level of quality and attention regardless of the communication method or the representative they encounter.
- Follow-through: Follow-through involves taking ownership of customers’ issues or requests and seeing them through to resolution. Good customer service representatives follow up with customers to ensure that their needs have been met satisfactorily, provide updates on the status of their inquiries or concerns, and take proactive steps to prevent future issues.
By embodying these qualities, businesses can cultivate strong relationships with customers, enhance their reputation, and foster loyalty and satisfaction among their customer base.
FAQs
What are the advantages of using Rogers PCBs?
Rogers PCBs offer several advantages, including low dielectric loss, excellent stability over temperature changes, consistent electrical properties across frequencies, and reliability in high-frequency applications. They are ideal for applications requiring precise signal integrity and minimal loss.
What types of applications are Rogers PCBs suitable for?
Rogers PCBs are commonly used in industries such as aerospace, telecommunications, radar systems, satellite communications, automotive electronics, and medical devices. They excel in high-frequency and high-speed applications where performance and reliability are critical.
What are the key considerations when designing with Rogers PCBs?
Designing with Rogers PCBs requires attention to factors such as material selection, layer stackup design, impedance control, trace geometry, ground plane placement, thermal management, and manufacturability. Adhering to design guidelines and consulting with experienced designers is essential.
How does the fabrication process for Rogers PCBs differ from standard PCBs?
The fabrication process for Rogers PCBs is similar to that of standard PCBs but involves additional considerations due to the specialized materials used. It includes steps such as material preparation, layer stacking, drilling, copper deposition, etching, surface finishing, solder mask application, and quality control.
What factors influence the cost of Rogers PCBs?
The cost of Rogers PCBs can vary depending on factors such as material selection, board size and thickness, number of layers, surface finish, complexity of design, quantity ordered, lead time, and additional services required.
Where can I find a reliable supplier for Rogers PCBs?
Reliable suppliers of Rogers PCBs can be found through online searches, industry directories, trade shows, and referrals from colleagues or industry contacts. It’s essential to research suppliers thoroughly, check their certifications and capabilities, and request quotes and samples before making a decision.