Rogers Ro4003c Substrate Manufacturer
Rogers Ro4003c Substrate Manufacturer,Rogers RO4003C Substrate is a high-frequency material renowned for its exceptional performance in RF and microwave circuits. With a stable dielectric constant of approximately 3.38 and a low dissipation factor of 0.0027, it ensures minimal signal loss and superior signal integrity. This substrate offers excellent mechanical stability and thermal reliability, making it ideal for demanding applications such as antennas, amplifiers, and high-speed digital circuits. RO4003C substrate, available in various thicknesses, is compatible with standard PCB fabrication processes, providing designers with flexibility and reliability for their designs.
What is Rogers Ro4003c Substrate?
Rogers RO4003C is a substrate material used for high-frequency microwave circuits, widely applied in RF (Radio Frequency) and microwave applications, particularly where high performance and reliability are essential. Developed by Rogers Corporation, this material meets the demanding requirements for circuit substrates in high-frequency communication equipment.
RO4003C is a glass-reinforced, ceramic-filled thermoset material that provides a very low dielectric constant and loss factor, making it excellent for high-frequency applications. Specifically, it has a stable dielectric constant of about 3.38 at a frequency of 10 GHz, and a dielectric loss of only 0.0027. These low-loss characteristics minimize signal degradation during transmission, thus enhancing signal integrity and transmission efficiency.
In addition to its excellent electrical properties, RO4003C also offers good mechanical stability and thermal performance. Its coefficient of thermal expansion is matched to that of copper, which helps reduce mechanical stress caused by temperature changes, thereby improving component reliability and durability. RO4003C also maintains its physical and electrical properties across a broad temperature range, making it suitable for high-frequency applications in various environmental conditions.
Therefore, RO4003C is ideal for demanding RF and microwave applications such as radar systems, satellite communications, and mobile communication equipment. Its high performance ensures these devices operate effectively while also extending product lifespan.
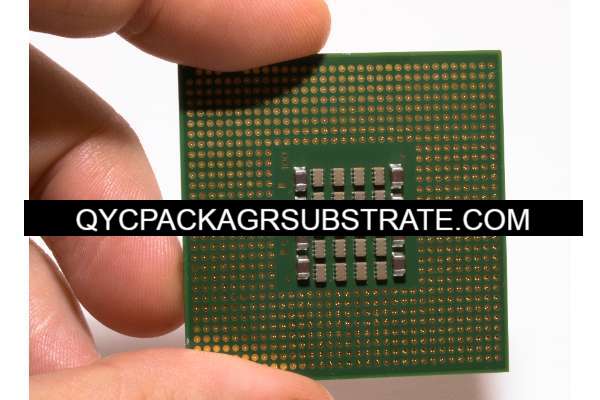
Rogers Ro4003c Substrate Manufacturer
What are the PCB Design Guidelines for Rogers Ro4003c Substrate?
Designing PCBs with Rogers RO4003C substrate involves specific considerations to optimize performance, particularly in RF and microwave applications. Here are some essential guidelines to follow when designing PCBs using RO4003C:
- Controlled Impedance Matching:One of the primary reasons for using RO4003C is its consistent dielectric constant, which helps in achieving accurate impedance control. Design your traces to meet the impedance requirements of your application, which typically involves precise calculations and adjustments in trace width and spacing.
- Minimize Signal Loss: Utilize the low-loss characteristics of RO4003C by designing your circuit with minimal bends and shorter trace lengths. This approach reduces signal degradation and maintains the integrity of high-speed signals.
- Thermal Management:Although RO4003C has good thermal stability, managing heat in high-power applications is crucial. Use thermal vias and consider the placement of heat-generating components to ensure efficient heat dissipation.
- Layer Stack-up Considerations: Since RO4003C is available in different thicknesses, plan your layer stack-up carefully. For multilayer designs, it might be necessary to use hybrid constructions, mixing RO4003C with other materials like FR4, depending on cost considerations and electrical requirements.
- Via Design: Use vias carefully to connect different layers without compromising the integrity of the RF signal. Back-drilled or blind vias can be effective in reducing parasitic capacitance and inductance associated with through-hole vias.
- Surface Finish: Choose a surface finish that suits the frequency and environmental requirements of your application. Options like ENIG (Electroless Nickel Immersion Gold) provide good signal integrity and are favorable for high-frequency applications.
- Moisture Sensitivity: Consider the effects of moisture absorption on dielectric properties. RO4003C performs well under varying environmental conditions, but appropriate protective measures such as conformal coatings might be necessary in high-humidity environments.
- Avoid Sharp Corners: In high-frequency designs, sharp corners can lead to signal reflection and other undesired effects. Use mitered or curved bends in your trace designs where possible.
- Grounding and Shielding:Ensure that the board has adequate grounding and that sensitive components are properly shielded. This is crucial in reducing noise and preventing interference in RF circuits.
- DRC and Verification: Always run a thorough Design Rule Check (DRC) specific to high-frequency PCBs. Verify the design with simulations and prototype testing to ensure that all parameters meet the desired specifications.
By adhering to these guidelines, designers can effectively harness the advantages of Rogers RO4003C, such as its low dielectric constant and low loss, critical for high-performance RF and microwave circuits. These practices help mitigate common design challenges associated with high-frequency signal behavior, thereby enhancing the reliability and functionality of the final product.
What is the Rogers Ro4003c Substrate Fabrication Process?
The fabrication process for PCBs using Rogers RO4003C substrate is similar to that of other high-frequency materials but with some specific considerations to maximize performance. Here’s an overview of the typical fabrication process:
- Material Preparation: The process begins with preparing the RO4003C substrate material. This involves cutting the material into the desired panel size according to the PCB design specifications.
- Surface Cleaning: Before proceeding with any fabrication steps, the substrate surfaces must be thoroughly cleaned to remove any contaminants that could affect adhesion or conductivity. This typically involves processes such as scrubbing, rinsing, and drying.
- Copper Foil Lamination: The next step involves laminating copper foil onto the substrate surfaces. This is typically done using a heat and pressure lamination process, where the copper foil is bonded to the substrate to form the conductive layers of the PCB.
- Photoresist Application: A layer of photoresist is then applied to the copper foil surfaces. This photoresist acts as a protective layer during the etching process and allows for the creation of the desired circuit patterns through photolithography.
- Exposure and Development:The PCB design patterns are transferred onto the photoresist layer using a photomask and exposure to UV light. After exposure, the photoresist is developed, removing the unexposed areas and leaving behind the circuit patterns.
- Etching: The exposed copper areas are then etched away using chemical processes. This selectively removes the copper from the substrate surface, leaving behind the desired circuit traces defined by the photoresist patterns.
- Strip and Clean: Once the etching process is complete, the remaining photoresist is stripped from the substrate surfaces, and the PCB is thoroughly cleaned to remove any remaining etchant residues or contaminants.
- Drilling: Holes are drilled into the PCB for component mounting and interconnection purposes. High-precision drilling equipment is used to ensure accuracy and consistency in hole placement.
- Plating and Surface Finish: Through-hole vias and pads are typically plated with a conductive material, such as copper, to improve electrical conductivity and solderability. The PCB may also undergo a surface finish process, such as immersion gold or ENIG (Electroless Nickel Immersion Gold), to protect the exposed copper surfaces and enhance solderability.
- Final Inspection: The fabricated PCB undergoes a final inspection to ensure that it meets the required specifications and quality standards. This may include electrical testing, visual inspection, and dimensional verification.
By following these fabrication steps and paying close attention to material handling and process parameters, manufacturers can produce high-quality PCBs using Rogers RO4003C substrate, optimized for high-frequency RF and microwave applications.
How do you manufacture a Rogers Ro4003c Substrate?
Manufacturing Rogers RO4003C substrates involves several specialized processes to create high-performance material suitable for RF and microwave applications. Here’s an overview of the typical manufacturing process:
- Preparation of Base Materials: The manufacturing process starts with preparing the base materials. This involves mixing the main components, including epoxy resin, reinforcement materials (such as woven glass fabric), fillers, and catalysts, in precise proportions.
- Coating Application: The mixed materials are then coated onto a release liner or carrier film using a roll coating or curtain coating process. This coating forms the base layer of the substrate.
- Curing: After coating, the substrate material undergoes a curing process to transform it from a liquid or semi-liquid state to a solid state. This is typically done in a temperature-controlled oven or using other curing methods such as UV curing, depending on the specific material composition.
- Lamination of Copper Foils: Once the base substrate material is cured, copper foils are laminated onto one or both sides of the substrate. This is often achieved using heat and pressure in a lamination press, which bonds the copper foils to the substrate surface.
- Surface Treatment: The copper foils on the substrate surface are then treated to remove any oxidation and contaminants and to improve adhesion. This may involve processes such as surface roughening, cleaning, and chemical treatment.
- Circuit Patterning: The next step is to pattern the copper foils to create the desired circuitry. This is typically done using photolithography, where a photoresist layer is applied to the copper surface, exposed to UV light through a photomask, developed to remove the unexposed areas, and then etched to remove the exposed copper.
- Dielectric Layer Formation: After circuit patterning, additional layers of dielectric material may be added to the substrate to achieve the desired thickness and dielectric properties. These layers are typically applied using the same coating and curing processes as the base material.
- Final Inspection and Testing: Once all manufacturing processes are complete, the finished substrate undergoes rigorous inspection and testing to ensure it meets the required specifications and quality standards. This may include dimensional verification, electrical testing, and visual inspection.
By carefully controlling each step of the manufacturing process and adhering to strict quality standards, manufacturers can produce high-quality Rogers RO4003C substrates optimized for high-frequency RF and microwave applications. These substrates offer excellent electrical performance, thermal stability, and reliability, making them ideal for use in various electronic devices and systems.
How much should a Rogers Ro4003c Substrate cost?
The cost of Rogers RO4003C substrate can vary significantly based on several factors including the thickness of the material, the type and amount of copper cladding, the size of the order, and the supplier. As of my last update, the approximate cost for Rogers RO4003C substrate generally ranges from $5 to $20 per square foot. Here are some key factors that influence the cost:
- Material Thickness: Thicker substrates typically cost more. Rogers RO4003C is available in various thicknesses, commonly ranging from 0.008 inches (0.203 mm) to 0.060 inches (1.524 mm).
- Copper Cladding: The type and weight of the copper cladding can affect the price. Standard copper cladding weights are 1 oz/ft² (35 µm) and 2 oz/ft² (70 µm), but custom weights can also be requested, often at a higher cost.
- Order Size: Bulk orders typically result in lower per-unit costs due to economies of scale. Smaller orders or custom-sized substrates may be more expensive on a per-square-foot basis.
- Supplier and Location: Prices can vary depending on the supplier and the geographical location. Suppliers with established relationships with Rogers Corporation may offer competitive pricing.
- Special Requirements: Any additional specifications such as tighter tolerance control, specific dielectric constant requirements, or additional surface treatments can increase the cost.
For a more accurate and up-to-date price, it’s recommended to contact suppliers or distributors directly. Some prominent suppliers and distributors of Rogers materials include Digi-Key, Mouser Electronics, and specialized PCB material distributors. Additionally, obtaining quotes from multiple suppliers can help you get the best price for your specific needs.
In summary, while $5 to $20 per square foot is a general range, the actual cost can vary based on the factors mentioned above. Always verify with suppliers for the most accurate and current pricing.
What is the Rogers Ro4003c Substrate base material?
The base material of Rogers RO4003C substrate is a composite material consisting primarily of reinforced woven glass fabric and epoxy resin. This composite material forms the foundation of the substrate and provides mechanical strength, dimensional stability, and dielectric properties necessary for high-frequency RF (Radio Frequency) and microwave applications.
The epoxy resin acts as a binder, holding the glass fabric reinforcement together and providing structural integrity to the substrate. It also contributes to the dielectric properties of the material, influencing parameters such as dielectric constant and dissipation factor.
The woven glass fabric reinforcement adds strength and stiffness to the substrate while also helping to control dimensional stability and thermal expansion. The orientation and weave pattern of the glass fabric reinforcement can be tailored to optimize mechanical and electrical performance.
Overall, the combination of epoxy resin and woven glass fabric reinforcement in Rogers RO4003C substrate results in a material with excellent electrical characteristics, low loss, high thermal stability, and mechanical reliability, making it well-suited for demanding RF and microwave circuit applications.
Which company makes Rogers Ro4003c Substrate?
Rogers RO4003C substrates are manufactured by Rogers Corporation, a leading company based in the United States. Rogers Corporation specializes in providing high-performance materials solutions for various applications, including electronics, automotive, telecommunications, aerospace, and more.
Rogers RO4003C substrate is one of the outstanding products of the company, designed specifically for high-frequency RF and microwave applications. It offers stable dielectric properties, low loss factor, and excellent thermal stability, making it suitable for a wide range of RF and microwave circuit designs, such as antennas, amplifiers, filters, and more.
Our company is also capable of producing Rogers RO4003C substrates. As a company focused on the production of high-performance electronic materials, we have advanced manufacturing equipment, extensive experience, and a professional technical team. Our production processes and quality control systems are carefully designed to ensure the production of high-quality RO4003C substrates that meet customer requirements.
Our production capacity can meet various order demands, whether it’s small batch production or large-scale customized orders, we can provide flexible solutions. We are committed to providing customers with high-performance, reliable RO4003C substrates, along with customized technical support and services to meet specific application requirements.
In summary, Rogers RO4003C substrates are manufactured by Rogers Corporation, and our company can also provide RO4003C substrates that meet the same standards to meet various high-frequency RF and microwave circuit design requirements of customers.
What are the 7 qualities of good customer service?
Good customer service is characterized by several key qualities that contribute to a positive experience for customers. Here are seven qualities of good customer service:
- Responsiveness: Good customer service is prompt and responsive to customer inquiries, concerns, and needs. Whether it’s answering questions, addressing complaints, or providing assistance, being responsive shows customers that their needs are being prioritized.
- Empathy: Empathy involves understanding and acknowledging the customer’s perspective, feelings, and situation. Good customer service representatives show empathy by actively listening to customers, expressing understanding of their concerns, and showing genuine concern for their well-being.
- Professionalism: Professionalism in customer service means conducting oneself in a courteous, respectful, and competent manner at all times. This includes maintaining a positive attitude, communicating clearly and effectively, and adhering to company policies and procedures.
- Knowledgeability: Good customer service representatives possess thorough knowledge of the products or services they are supporting. They can provide accurate information, answer questions confidently, and offer helpful recommendations or solutions to customer issues.
- Flexibility: Flexibility is essential in adapting to the unique needs and preferences of each customer. Good customer service involves being flexible in finding solutions, accommodating special requests, and adjusting processes as needed to meet customer expectations.
- Reliability: Reliability entails delivering consistent and dependable service to customers. This includes following through on promises, meeting deadlines, and ensuring that customers can rely on the company to fulfill its commitments.
- Proactiveness: Good customer service involves being proactive in anticipating and addressing customer needs before they arise. This may involve reaching out to customers with relevant information or assistance, identifying potential issues early on, and taking proactive steps to resolve them.
By embodying these qualities, businesses can provide exceptional customer service that fosters trust, loyalty, and satisfaction among their customer base.
FAQs
What are the key characteristics of RO4003C substrate?
The key characteristics include stable dielectric constant (~3.38), low dissipation factor (0.0027), excellent electrical performance at high frequencies, good mechanical stability, and thermal reliability.
What are the typical applications of RO4003C substrate?
RO4003C substrate is commonly used in various RF and microwave circuits, such as antennas, amplifiers, filters, couplers, and high-speed digital applications. It is widely utilized in telecommunications, aerospace, defense, and automotive industries.
How does RO4003C substrate compare to other materials?
RO4003C substrate offers superior electrical performance compared to traditional FR-4 materials. Its low dielectric constant and low loss make it ideal for high-frequency applications where signal integrity is critical.
What thicknesses are available for RO4003C substrate?
RO4003C substrate is available in various thicknesses, typically ranging from 0.008 inches (0.203 mm) to 0.060 inches (1.524 mm), catering to different design requirements.
Is RO4003C substrate compatible with standard PCB fabrication processes?
Yes, RO4003C substrate is compatible with standard PCB fabrication processes, including drilling, etching, plating, and soldering. However, it may require adjustments in processing parameters to optimize performance.
Where can I purchase RO4003C substrate?
RO4003C substrate is available through authorized distributors of Rogers Corporation products. Companies specializing in PCB materials and components may also offer RO4003C substrate for sale.
What are the cost considerations for RO4003C substrate?
The cost of RO4003C substrate depends on factors such as thickness, copper cladding, order size, and supplier. It typically ranges from $5 to $20 per square foot, with larger quantities often resulting in lower unit costs.