Semiconductor Glass Package Substrates Manufacturer
Semiconductor Glass Package Substrates Manufacturer, Advanced production art, professional team, we mainly produce multi-layer packaging substrate, the main use of materials are BT material, ABF material, glass substrate, or other kinds of high-speed and high-frequency materials, we use the corresponding materials according to the needs of customers to produce substrate from 2 layers to 22 layers, the minimum trace 9UM, the minimum spacing 9UM.
Semiconductor Glass Package Substrates (SGPS) are advanced substrates revolutionizing semiconductor packaging. Comprising precision-engineered glass, SGPS offers unparalleled benefits in terms of electrical insulation, thermal conductivity, and dimensional stability. Its composition ensures superior reliability, making it ideal for demanding applications in automotive, aerospace, telecommunications, and beyond.
SGPS technology enables intricate designs with fine features and tight tolerances, facilitating high-density packaging solutions. The fabrication process involves meticulous steps, including glass preparation, patterning, metallization, and encapsulation, all executed with precision equipment and techniques.
The result is a robust platform that provides a stable foundation for mounting semiconductor chips and other electronic components. With SGPS, manufacturers can achieve optimal performance, miniaturization, and longevity in their products, meeting the stringent demands of modern technology. As the semiconductor industry continues to evolve, SGPS remains at the forefront, driving innovation and powering the next generation of electronic devices.
What is a Semiconductor Glass Package Substrate (SGPS)?
Semiconductor Glass Package Substrates Manufacturer. the Package Substrate will be made with Showa Denko and Ajinomoto High speed materials.or other types high speed materials and high frequency materials.
A Semiconductor Glass Package Substrate (SGPS) is a type of substrate used in semiconductor packaging. It’s made of glass, which offers several advantages over traditional substrates like ceramic or organic materials.
The SGPS provides a stable and reliable platform for mounting semiconductor chips and other electronic components. It offers excellent electrical insulation properties, thermal conductivity, and dimensional stability. Additionally, glass substrates can be manufactured with very fine features and tight tolerances, making them suitable for high-density packaging applications.
SGPS technology is often utilized in advanced semiconductor packaging solutions, particularly in applications where high-performance, reliability, and miniaturization are critical, such as in the automotive, aerospace, and telecommunications industries.
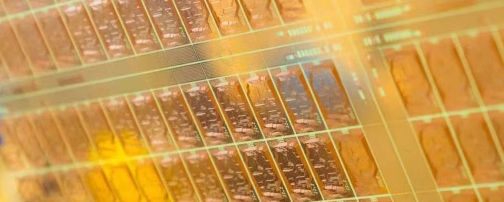
Semiconductor Glass Package Substrates
What are Semiconductor Glass Package Substrate (SGPS) Design Guidelines?
Design guidelines for Semiconductor Glass Package Substrates (SGPS) typically focus on optimizing the performance, reliability, and manufacturability of the package. Here are some common design considerations:
- Thermal Management: Ensure efficient thermal dissipation to prevent overheating of the semiconductor devices. This may involve incorporating thermal vias, thermal pads, or heat spreaders into the substrate design.
- Electrical Performance: Design the substrate to minimize signal loss, impedance mismatch, and electromagnetic interference (EMI). This may involve optimizing trace geometries, layer stackup, and grounding techniques.
- Mechanical Integrity: Ensure the substrate can withstand mechanical stresses such as bending, shock, and vibration without compromising the integrity of the semiconductor devices. Reinforce critical areas with additional support structures if necessary.
- Dimensional Stability: Choose glass materials with low coefficient of thermal expansion (CTE) to minimize dimensional changes due to temperature variations. This helps maintain precise alignment of semiconductor components and prevents reliability issues.
- Manufacturability: Design for manufacturability by considering the capabilities and limitations of glass substrate fabrication processes. Minimize complexity, optimize panelization, and incorporate features for automated assembly and testing.
- Reliability: Design for long-term reliability by minimizing sources of mechanical and thermal stress, such as solder joints, and ensuring adequate margin for thermal cycling and other environmental factors.
- Hermeticity: If required for the application, ensure the package provides a hermetic seal to protect the semiconductor devices from moisture and other contaminants. This may involve incorporating sealing materials or encapsulation techniques into the substrate design.
- Cost Optimization: Balance performance requirements with cost considerations by optimizing material usage, minimizing waste, and leveraging economies of scale in manufacturing.
These guidelines may vary depending on the specific requirements of the application, such as automotive, aerospace, or consumer electronics, and the characteristics of the semiconductor devices being packaged. Collaboration between semiconductor designers, substrate manufacturers, and packaging engineers is often necessary to achieve optimal results.
What is the Semiconductor Glass Package Substrate (SGPS) Fabrication Process?
The fabrication process for Semiconductor Glass Package Substrates (SGPS) involves several steps, typically including glass preparation, patterning, metallization, bonding, and finishing. Here’s a general overview of the process:
- Glass Selection: The process starts with selecting the appropriate type of glass based on the desired electrical, thermal, and mechanical properties. Glasses with low coefficients of thermal expansion (CTE) are often preferred to minimize dimensional changes during temperature variations.
- Glass Preparation: The selected glass is cleaned and prepared for further processing to ensure good adhesion and uniformity of subsequent layers.
- Patterning: Photolithography or laser ablation techniques are used to pattern the glass substrate. This step involves applying a photoresist or masking material to define the desired circuitry or features on the substrate. The exposed areas are then etched away to create the desired patterns.
- Metallization: Thin film metallization layers are deposited onto the glass substrate to create conductive traces, bond pads, and other interconnect features. Common metallization techniques include sputtering, evaporation, or chemical vapor deposition (CVD).
- Die Attach and Wire Bonding: Semiconductor chips are attached to the substrate using die attach materials, such as epoxy or solder. Wire bonding is then performed to connect the semiconductor chip to the metallized traces on the substrate. Alternatively, flip-chip bonding techniques may be used for direct chip attachment.
- Encapsulation and Sealing: The semiconductor chips and wire bonds are encapsulated and sealed within the SGPS to provide protection from environmental factors such as moisture, dust, and mechanical stress. This may involve applying encapsulation materials and sealing the package using bonding techniques such as glass frit bonding or solder sealing.
- Testing and Inspection: The fabricated SGPS undergoes electrical testing and visual inspection to ensure proper functionality and quality. This may include continuity testing, impedance measurements, and inspection for defects such as cracks or voids.
- Packaging and Integration:Once the SGPS passes quality control tests, it may be further integrated into larger electronic assemblies or packaged into final products, depending on the specific application requirements.
Throughout the fabrication process, strict quality control measures are implemented to ensure the reliability and performance of the SGPS for its intended application. Collaboration between semiconductor designers, substrate manufacturers, and packaging engineers is often necessary to optimize the fabrication process and achieve the desired performance characteristics.
How do you manufacture a Semiconductor Glass Package Substrate (SGPS)?
Manufacturing a Semiconductor Glass Package Substrate (SGPS) involves several intricate steps and specialized equipment. Here’s an overview of the manufacturing process:
- Glass Substrate Preparation: The process begins with selecting high-quality glass substrates with properties suitable for the desired application. These substrates are typically made of low-CTE (Coefficient of Thermal Expansion) glass to minimize dimensional changes during temperature variations. The glass substrates are cleaned thoroughly to remove any contaminants.
- Photolithography or Laser Patterning: A photoresist or masking material is applied to the glass substrate. Using photolithography or laser ablation techniques, the desired circuit patterns and features are defined on the substrate. UV light or laser beams are used to expose and develop the photoresist, creating the desired patterns on the glass surface.
- Metallization: Thin film metallization layers are deposited onto the glass substrate to create conductive traces, bond pads, and other interconnect features. Common metallization techniques include sputtering, evaporation, or chemical vapor deposition (CVD). These metallization layers provide the electrical pathways for the semiconductor devices and other components mounted on the substrate.
- Die Attach and Wire Bonding: Semiconductor chips are attached to the substrate using die attach materials such as epoxy or solder. Wire bonding techniques are then employed to connect the semiconductor chip to the metallized traces on the substrate. This step requires precision equipment to ensure accurate placement and bonding of the semiconductor devices.
- Encapsulation and Sealing: The semiconductor chips and wire bonds are encapsulated and sealed within the SGPS to provide protection from environmental factors such as moisture, dust, and mechanical stress. This may involve applying encapsulation materials such as epoxies or molding compounds and sealing the package using bonding techniques such as glass frit bonding or solder sealing.
- Testing and Quality Control: The fabricated SGPS undergoes rigorous testing and inspection to ensure proper functionality and quality. Electrical testing is performed to verify the integrity of the connections and the performance of the semiconductor devices. Visual inspection is also carried out to detect any defects such as cracks, voids, or misalignments.
- Packaging and Integration: Once the SGPS passes quality control tests, it may be further integrated into larger electronic assemblies or packaged into final products, depending on the specific application requirements.
Throughout the manufacturing process, strict quality control measures are implemented to ensure the reliability and performance of the SGPS for its intended application. Collaboration between semiconductor designers, substrate manufacturers, and packaging engineers is often necessary to optimize the manufacturing process and achieve the desired performance characteristics.
How much should a Semiconductor Glass Package Substrate (SGPS) cost?
The cost of a Semiconductor Glass Package Substrate (SGPS) can vary significantly depending on several factors such as:
- Complexity: The complexity of the substrate design, including the number of layers, size, and density of features, can impact the cost. More complex designs typically require advanced manufacturing processes and may incur higher fabrication costs.
- Material Costs: The cost of the glass substrate material itself, as well as any additional materials such as metallization layers, die attach materials, encapsulation compounds, and sealing materials, contributes to the overall cost.
- Manufacturing Processes: The cost of the manufacturing processes involved in fabricating the SGPS, including photolithography, metallization, die attachment, wire bonding, encapsulation, and testing, affects the final cost. Advanced manufacturing techniques and equipment may result in higher production costs.
- Volume and Scale: Economies of scale play a significant role in determining the cost of SGPS. Larger production volumes often lead to lower per-unit costs due to efficiencies in manufacturing and procurement.
- Quality and Reliability Requirements: Meeting stringent quality and reliability standards may require additional testing, inspection, and quality control measures, which can increase the overall cost of production.
- Technology Node: The level of technology used in the fabrication process, such as the feature sizes and tolerances achieved, can influence the cost. More advanced technology nodes may require specialized equipment and expertise, resulting in higher costs.
- Supplier Relationships: The relationship between the buyer and the supplier, including factors such as negotiation, contract terms, and supplier capabilities, can impact the final cost of the SGPS.
Given these factors, it’s challenging to provide a specific cost estimate for an SGPS without detailed information about the design specifications, manufacturing processes, and volume requirements. Typically, semiconductor packaging suppliers or manufacturers would provide quotes based on the specific requirements of a project.
What is Semiconductor Glass Package Substrate (SGPS) base material?
The base material for Semiconductor Glass Package Substrates (SGPS) is typically glass, which provides excellent electrical insulation, thermal stability, and mechanical strength for semiconductor device integration.
Which company manufactures Semiconductor Glass Package Substrates (SGPS)?
Currently, several companies are leading the manufacturing of Semiconductor Glass Package Substrates (SGPS). Some of the major manufacturers include Foxconn, Hitachi Chemical, Shin-Etsu Chemical Co., Nitto Denko Corporation, and Panasonic Corporation. These companies have extensive experience and technology in the semiconductor packaging field, offering various types of SGPS products to meet different customer needs.
For our company, if we have the relevant technology and manufacturing capabilities, we could consider expanding into the manufacturing of Semiconductor Glass Package Substrates (SGPS). As a company, we might need to invest in advanced manufacturing equipment and technology and establish partnerships within the semiconductor industry to ensure our products meet market demands and remain competitive.
If our company decides to enter the manufacturing of Semiconductor Glass Package Substrates (SGPS), we might need to undertake the following:
- Technology Research and Innovation: Conduct research and development related to SGPS, including material research, process development, and product design, to ensure our products have advanced performance and competitive advantages.
- Manufacturing Capability Building: Invest in advanced manufacturing equipment and technology, including lithography equipment, thin film deposition equipment, bonding equipment, and testing equipment, to efficiently produce high-quality SGPS products.
- Quality Management and Assurance: Establish a strict quality management system, including raw material procurement, production process control, and product testing, to ensure our products meet customer requirements and industry standards.
- Market Development and Sales Channel Establishment: Actively engage in marketing activities, expand customer base and sales channels, and establish long-term partnerships with customers in the semiconductor industry to ensure our products are steadily introduced to the market and gain a good market share.
In summary, although our company may not currently be involved in the manufacturing of Semiconductor Glass Package Substrates (SGPS), if we have the relevant technology and manufacturing capabilities and take appropriate measures and strategies, we could potentially succeed in this field and become a competitive manufacturer.
Qualities of Good Customer Service
Good customer service is essential for maintaining customer satisfaction and loyalty. Here are some qualities that define good customer service:
- Responsiveness: Being prompt in addressing customer inquiries, concerns, and requests. This includes timely responses to emails, phone calls, and messages.
- Empathy: Understanding and empathizing with the customer’s situation, feelings, and needs. Empathetic responses demonstrate care and concern for the customer’s well-being.
- Communication skills: Clear and effective communication is key to providing good customer service. This involves active listening, asking clarifying questions, and providing information in a manner that is easy to understand.
- Knowledgeable: Having thorough knowledge about the products or services offered allows customer service representatives to provide accurate information and solutions to customer inquiries and issues.
- Problem-solving skills: Being able to effectively identify and resolve customer problems and complaints. This may involve finding creative solutions, escalating issues when necessary, and following up to ensure resolution.
- Professionalism: Maintaining a professional demeanor and attitude at all times, regardless of the customer’s behavior or the nature of the interaction. This includes remaining calm, polite, and respectful, even in challenging situations.
- Personalization: Tailoring interactions to meet the specific needs and preferences of individual customers. This may involve addressing customers by name, remembering past interactions, and offering personalized recommendations or solutions.
- Consistency: Providing consistent levels of service across all customer touchpoints and interactions. Consistency builds trust and reliability, which are essential for fostering long-term customer relationships.
- Proactiveness: Anticipating customer needs and taking proactive steps to address them before they become issues. This may involve providing proactive updates, offering relevant information or assistance, and seeking feedback to identify potential areas for improvement.
- Follow-up: Following up with customers after their initial inquiry or interaction to ensure their needs have been met satisfactorily. This demonstrates commitment to customer satisfaction and helps identify opportunities for further assistance or improvement.
By embodying these qualities, businesses can deliver exceptional customer service experiences that leave a lasting positive impression on customers.
FAQs
What is a Semiconductor Glass Package Substrate (SGPS)?
A Semiconductor Glass Package Substrate (SGPS) is a type of substrate used in semiconductor packaging. It is made of glass and provides a stable platform for mounting semiconductor chips and other electronic components.
What are the advantages of SGPS over traditional substrates?
SGPS offers several advantages including excellent electrical insulation properties, high thermal conductivity, dimensional stability, and the ability to achieve fine features and tight tolerances. It also provides better reliability and performance in harsh environments compared to traditional substrates like ceramic or organic materials.
What industries use SGPS?
SGPS technology is used in various industries including automotive, aerospace, telecommunications, consumer electronics, and medical devices. It is particularly suitable for applications where high-performance, reliability, and miniaturization are critical.
What are the key considerations in SGPS design?
Key considerations in SGPS design include thermal management, electrical performance, mechanical integrity, dimensional stability, manufacturability, reliability, hermeticity (if required), and cost optimization.
What is the fabrication process of SGPS?
The fabrication process typically involves glass preparation, patterning, metallization, die attach, wire bonding, encapsulation, testing, and integration. Each step requires specialized equipment and techniques to ensure the quality and reliability of the SGPS.
How much does SGPS cost?
The cost of SGPS depends on factors such as complexity, material costs, manufacturing processes, volume and scale, quality and reliability requirements, technology node, and supplier relationships. It’s challenging to provide a specific cost estimate without detailed project information.
Which companies manufacture SGPS?
Leading manufacturers of SGPS include Foxconn, Hitachi Chemical, Shin-Etsu Chemical Co., Nitto Denko Corporation, Panasonic Corporation, and others. These companies have extensive experience and expertise in semiconductor packaging.
What are the latest developments in SGPS technology?
Recent developments in SGPS technology include advancements in material science, process optimization, miniaturization, integration of advanced features (such as sensors and antennas), and improved reliability in harsh environments. Research and development efforts continue to push the boundaries of SGPS capabilities.