Semiconductor IC substrate Manufacturer
What is Semiconductor IC Substrate?
We are a professional Semiconductor IC substrate Manufacturer supplier, we mainly produce ultra-small bump pitch substrate, ultra-small trace and spacing packaging substrate and PCBs.
A Semiconductor IC Substrate, often simply referred to as a substrate, is a fundamental component of integrated circuits (ICs) or microchips. It serves as the physical foundation upon which various semiconductor devices are fabricated.
Here are some key points about semiconductor IC substrates:
Material: Substrates are typically made of silicon, although other materials such as gallium arsenide (GaAs) and silicon carbide (SiC) are also used, especially in specialized applications.
Structure: The substrate provides a solid, stable platform for the fabrication of semiconductor devices. It usually consists of a single crystal wafer of silicon or other semiconductor material.
Layers: Semiconductor devices are constructed on the substrate using various layers of materials, such as silicon dioxide (SiO2), polysilicon, and metal conductors, which are deposited or etched onto the substrate to form transistors, diodes, and other electronic components.
Interconnects: The substrate also contains interconnects, which are conductive pathways that allow electrical signals to travel between different components of the integrated circuit.
Size and Shape: Substrates come in various sizes and shapes depending on the specific application and the requirements of the integrated circuit design. Common sizes for substrates range from a few millimeters to several inches in diameter (e.g., 100mm, 150mm, 200mm, or 300mm wafers).
Manufacturing Process: The fabrication of semiconductor IC substrates involves a series of sophisticated processes, including crystal growth, wafer slicing, surface preparation, doping, deposition, lithography, etching, and packaging.
Overall, semiconductor IC substrates are essential components in the manufacturing of integrated circuits, providing a stable platform for the fabrication of semiconductor devices and enabling the miniaturization and integration of electronic components for various applications, including computers, smartphones, automotive electronics, and industrial control systems.
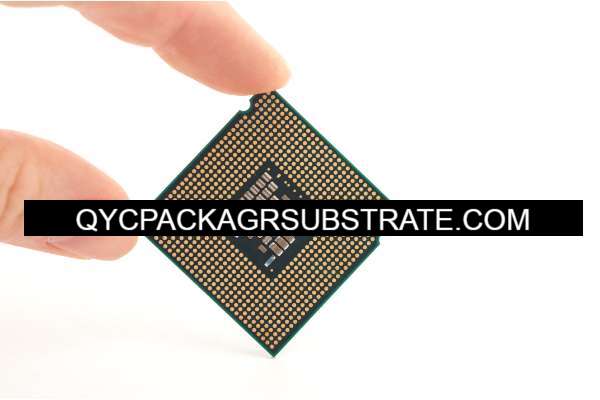
Semiconductor IC substrate Manufacturer
What are the Functions of Semiconductor IC Substrate?
Semiconductor IC substrates serve several critical functions in the fabrication and operation of integrated circuits (ICs). Here are some of the key functions:
Mechanical Support: The substrate provides a stable mechanical foundation for the various semiconductor components and interconnects that make up the integrated circuit. It ensures that the components are securely anchored in place and protected from mechanical stress and deformation.
Electrical Isolation: Substrates often act as insulators, preventing electrical signals from leaking between different components or layers of the integrated circuit. This electrical isolation is crucial for ensuring proper circuit operation and preventing interference or crosstalk between adjacent components.
Heat Dissipation: Substrates can help dissipate heat generated by the integrated circuit during operation. Many substrates have good thermal conductivity, allowing them to efficiently conduct heat away from the semiconductor devices and distribute it across the substrate surface. This helps prevent overheating and ensures the reliability and longevity of the IC.
Electrical Conduction: While substrates primarily provide electrical isolation between different components, they also play a role in conducting electrical signals to and from the semiconductor devices. Through the use of conductive pathways or interconnects on the substrate surface, electrical signals can be routed between various components of the integrated circuit.
Integration and Miniaturization: Substrates enable the integration and miniaturization of electronic components by providing a compact, three-dimensional platform for the fabrication of semiconductor devices. By packing multiple components onto a single substrate, ICs can achieve higher levels of functionality and performance in a smaller footprint.
Dielectric Properties: Depending on the specific material used for the substrate, it may possess dielectric properties that are important for the operation of certain semiconductor devices. For example, silicon dioxide (SiO2) is commonly used as an insulating layer in IC substrates due to its high dielectric strength and low leakage current.
Overall, semiconductor IC substrates play a crucial role in the performance, reliability, and miniaturization of integrated circuits, providing mechanical support, electrical isolation, heat dissipation, and electrical conduction for the various semiconductor components that make up the IC.
What are the Different Types of Semiconductor IC Substrate?
Semiconductor IC substrates come in various types, each suited for different applications and manufacturing processes. Here are some of the common types of semiconductor IC substrates:
Silicon Substrates: Silicon is the most widely used material for semiconductor IC substrates due to its abundance, excellent electrical properties, and well-established manufacturing processes. Silicon substrates are used in a wide range of applications, from consumer electronics to high-performance computing.
Gallium Arsenide (GaAs) Substrates: GaAs substrates are often used in applications requiring high-frequency operation, such as microwave devices, radio frequency (RF) amplifiers, and optoelectronic devices. GaAs substrates offer superior electron mobility compared to silicon, making them suitable for high-speed and high-frequency applications.
Silicon Carbide (SiC) Substrates: SiC substrates are used in high-power and high-temperature applications due to their excellent thermal conductivity, high breakdown voltage, and resistance to harsh environmental conditions. SiC substrates find applications in power electronics, automotive powertrains, and aerospace systems.
Sapphire Substrates: Sapphire substrates are commonly used in optoelectronic applications, such as light-emitting diodes (LEDs), laser diodes, and photovoltaic cells. Sapphire offers high optical transparency and mechanical durability, making it suitable for applications requiring high-performance optics.
Glass Substrates: Glass substrates are used in certain specialized applications, such as microfluidic devices, lab-on-a-chip systems, and biochips. Glass substrates offer biocompatibility, optical transparency, and chemical inertness, making them suitable for use in biomedical and analytical instruments.
Silicon-on-Insulator (SOI) Substrates: SOI substrates consist of a thin layer of silicon (the active layer) bonded to an insulating substrate, typically silicon dioxide (SiO2) or sapphire. SOI substrates offer advantages such as reduced power consumption, improved radiation tolerance, and enhanced performance in high-frequency circuits.
Germanium (Ge) Substrates: Germanium substrates are used in certain specialized applications, such as infrared sensors, photodetectors, and high-speed transistors. Germanium offers high carrier mobility and is transparent to infrared radiation, making it suitable for infrared imaging and sensing applications.
These are just a few examples of the various types of semiconductor IC substrates available. The choice of substrate material depends on factors such as the specific application requirements, performance characteristics, and manufacturing considerations.
How does Semiconductor IC Substrate Relate to IC Packaging?
Semiconductor IC substrate and IC packaging are two essential components of the overall integrated circuit (IC) manufacturing process, and they are closely related. Here’s how they relate to each other:
Physical Foundation: The semiconductor IC substrate serves as the physical foundation upon which the various semiconductor devices and components are fabricated. It provides a solid platform for the integration of electronic components and interconnects.
Integration and Connection: After the semiconductor devices are fabricated on the substrate, IC packaging comes into play. IC packaging involves encapsulating the semiconductor die (chip) with a protective package and providing electrical connections between the chip and the external environment. This packaging process typically involves bonding the semiconductor die to a substrate within the package, which acts as an intermediary between the chip and the external connections.
Signal Routing and Power Distribution: The substrate plays a crucial role in routing electrical signals and distributing power within the integrated circuit. It contains conductive pathways or interconnects that allow signals to travel between different components of the IC. Additionally, the substrate facilitates the distribution of power to the various semiconductor devices and components.
Thermal Management: Both substrate and IC packaging contribute to thermal management in integrated circuits. The substrate provides a pathway for heat dissipation from the semiconductor devices, while the packaging material and design influence the efficiency of heat transfer and dissipation to the external environment.
Protection and Reliability: IC packaging serves to protect the semiconductor die from physical damage, moisture, contaminants, and other environmental factors. It also provides mechanical support and ensures the reliability and longevity of the integrated circuit. The substrate, as part of the packaging assembly, contributes to these protective and reliability-enhancing functions.
Form Factor and Size: The substrate and IC packaging collectively influence the form factor and size of the integrated circuit. The choice of substrate material, package type, and packaging technology can impact the overall size, weight, and shape of the IC, which are important considerations for various applications, such as mobile devices, automotive electronics, and industrial systems.
In summary, semiconductor IC substrate and IC packaging are interrelated components of the integrated circuit manufacturing process, working together to provide physical support, electrical connectivity, thermal management, protection, and reliability for semiconductor devices and electronic components.
What are the Differences Between Semiconductor IC Substrate and PCB?
Semiconductor IC substrate and IC packaging are closely related aspects of semiconductor device manufacturing, as both play critical roles in the overall functionality, reliability, and performance of integrated circuits (ICs). Here’s how they relate to each other:
Physical Support and Protection: IC packaging encapsulates the semiconductor IC substrate and its components, providing physical support and protection against mechanical stress, moisture, contaminants, and other environmental factors. The substrate serves as the foundation upon which the semiconductor devices are fabricated, while the packaging encloses and shields them from external elements.
Electrical Interconnection: Both the semiconductor IC substrate and IC packaging facilitate electrical interconnection between the various components of the integrated circuit. The substrate typically contains interconnects that route electrical signals between different semiconductor devices and layers, while the packaging includes pins, leads, or solder balls that connect the IC to external circuits or systems.
Heat Dissipation: Both substrate and packaging contribute to heat dissipation in integrated circuits. The substrate may have a role in conducting heat away from the semiconductor devices, while the packaging often includes heat sinks, thermal pads, or other cooling mechanisms to dissipate heat generated during operation.
Miniaturization and Integration: Both substrate and packaging technologies enable the miniaturization and integration of electronic components in ICs. Advances in substrate manufacturing allow for the fabrication of smaller and more densely packed semiconductor devices, while innovations in IC packaging enable the assembly of multiple ICs or components into a single package, reducing overall size and improving performance.
Functionality and Performance: The choice of substrate material and packaging technology can significantly impact the functionality and performance of integrated circuits. Different substrate materials offer varying electrical, thermal, and mechanical properties, affecting factors such as speed, power consumption, and reliability. Similarly, the selection of packaging technology influences parameters such as signal integrity, electromagnetic interference (EMI), and thermal management.
Overall, semiconductor IC substrate and IC packaging are integral components of integrated circuit manufacturing, working together to provide physical support, electrical interconnection, heat dissipation, and protection for semiconductor devices, while also enabling miniaturization, integration, and optimization of IC functionality and performance.
What are the Main Structures and Production Technologies of Semiconductor IC Substrate?
Semiconductor IC substrates can have various structures and are produced using different technologies depending on the specific application requirements and manufacturing processes. Here are some of the main structures and production technologies of semiconductor IC substrates:
Monolithic Silicon Wafers: Monolithic silicon wafers are the most common type of semiconductor IC substrate. These substrates consist of a single crystal of silicon with uniform crystal orientation. Monolithic silicon wafers are produced through processes such as crystal growth (e.g., Czochralski method), wafer slicing (e.g., diamond wire sawing), surface preparation (e.g., polishing), and doping (e.g., ion implantation).
Silicon-on-Insulator (SOI) Substrates: SOI substrates consist of a thin layer of silicon (the active layer) bonded to an insulating substrate, typically silicon dioxide (SiO2). SOI substrates are produced using techniques such as wafer bonding (e.g., direct wafer bonding, smart-cut), thin-film deposition (e.g., chemical vapor deposition, physical vapor deposition), and substrate thinning (e.g., mechanical grinding, chemical mechanical polishing).
Epitaxial Silicon Wafers: Epitaxial silicon wafers are produced by depositing a thin layer of silicon (the epitaxial layer) onto a silicon substrate using epitaxial growth techniques such as chemical vapor deposition (CVD) or molecular beam epitaxy (MBE). Epitaxial silicon wafers are commonly used in applications requiring precise control of doping concentrations and layer thicknesses.
Gallium Arsenide (GaAs) Substrates: GaAs substrates are produced using techniques such as liquid phase epitaxy (LPE) or metalorganic chemical vapor deposition (MOCVD). GaAs substrates are commonly used in high-frequency and high-speed applications, such as RF amplifiers and microwave devices.
Silicon Carbide (SiC) Substrates: SiC substrates are produced using techniques such as physical vapor transport (PVT) or chemical vapor deposition (CVD). SiC substrates offer excellent thermal conductivity, high breakdown voltage, and resistance to harsh environments, making them suitable for high-power and high-temperature applications.
Glass Substrates: Glass substrates are produced using techniques such as float glass manufacturing or glass fusion bonding. Glass substrates are commonly used in specialized applications, such as microfluidic devices, biochips, and optical components.
These are just a few examples of the main structures and production technologies of semiconductor IC substrates. The choice of substrate structure and production technology depends on factors such as the specific application requirements, performance characteristics, and cost considerations.
Frequently Asked Questions (FAQs)
What is a semiconductor IC substrate?
A semiconductor IC substrate is the physical foundation upon which various semiconductor devices are fabricated. It serves as a platform for the integration and interconnection of electronic components to form an integrated circuit (IC) or microchip.
What materials are used for semiconductor IC substrates?
Common materials used for semiconductor IC substrates include silicon, gallium arsenide (GaAs), silicon carbide (SiC), sapphire, and glass. Each material offers different properties suited for specific applications and performance requirements.
What are the functions of semiconductor IC substrates?
Semiconductor IC substrates provide mechanical support, electrical isolation, heat dissipation, electrical conduction, integration, and miniaturization for semiconductor devices. They also play a crucial role in the reliability and performance of integrated circuits.
What are the different types of semiconductor IC substrates?
Different types of semiconductor IC substrates include silicon substrates, gallium arsenide (GaAs) substrates, silicon carbide (SiC) substrates, sapphire substrates, glass substrates, silicon-on-insulator (SOI) substrates, and germanium (Ge) substrates. Each type offers unique properties suited for specific applications.
How are semiconductor IC substrates manufactured?
Semiconductor IC substrates are manufactured using various techniques such as crystal growth, wafer slicing, surface preparation, doping, deposition, epitaxy, thin-film deposition, wafer bonding, and substrate thinning. The choice of manufacturing process depends on factors such as the substrate material, substrate structure, and application requirements.
What role does semiconductor IC substrate play in IC packaging?
Semiconductor IC substrate and IC packaging are closely related aspects of semiconductor device manufacturing. The substrate provides a foundation for semiconductor devices, while packaging encloses and protects them. Both substrate and packaging contribute to electrical interconnection, heat dissipation, miniaturization, and reliability of integrated circuits.
Conclusion
In conclusion, semiconductor IC substrates are foundational components in the manufacturing of integrated circuits (ICs) or microchips. They provide mechanical support, electrical isolation, heat dissipation, electrical conduction, and integration for semiconductor devices, contributing to the reliability, performance, and miniaturization of ICs. Semiconductor IC substrates come in various types, including silicon, gallium arsenide (GaAs), silicon carbide (SiC), sapphire, glass, silicon-on-insulator (SOI), and germanium (Ge), each offering unique properties suited for specific applications. Manufacturing techniques such as crystal growth, wafer slicing, surface preparation, doping, deposition, epitaxy, thin-film deposition, wafer bonding, and substrate thinning are used to produce semiconductor IC substrates. These substrates are closely related to IC packaging, working together to provide physical support, electrical interconnection, heat dissipation, and protection for semiconductor devices, while also enabling miniaturization, integration, and optimization of IC functionality and performance. Overall, semiconductor IC substrates play a crucial role in advancing technology and powering a wide range of electronic devices used in various industries and applications.