Exploring Package Substrates.Semiconductor Package Substrates manufacturer.High speed and high frequency material packaging substrate manufacturing. Advanced packaging substrate production process and technology. Package substrates, often referred to as “substrates” in the industry, are the structural backbone of modern semiconductor devices. These substrates serve as the interconnection platform for various electronic components, ensuring they work together seamlessly. Think of them as the bridge that connects and facilitates communication between the different parts of your electronic gadgets.
Importance in Semiconductor Packaging
Now, you might wonder, “Why are package substrates so crucial?” The answer lies in their multifaceted significance. Package substrates are not just passive components but active contributors to a device’s functionality. They play a pivotal role in various aspects, including signal transmission, power distribution, and, most critically, managing the heat generated by semiconductor components. In an era where electronic devices are becoming smaller, faster, and more powerful, the efficient dissipation of heat is of paramount importance. It is the key to preventing overheating and ensuring the extended lifespan and optimal performance of these advanced gadgets.Package substrates are instrumental in achieving this.
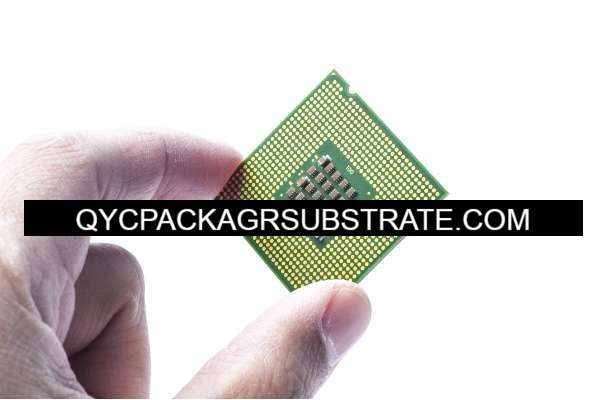
Moreover, as the demand for high-performance semiconductor devices continues to grow, package substrates must keep up with the ever-increasing complexity and performance requirements. Understanding the materials, functions, and differences between package substrates and PCBs is crucial for anyone involved in the semi conductor industry.
Brief overview of the article’s structure
This article is designed to be your comprehensive guide to package substrates. We will begin by exploring the materials used in these substrates, from organic options like FR-4 and BT to inorganic choices like ceramics and metal core substrates. We’ll discuss the critical role of dielectric materials and delve into the selection criteria for package substrate materials, shedding light on why certain materials are chosen for specific applications.
Next, we’ll examine the importance of substrates in semiconductor packaging. We’ll discuss how they enhance signal transmission, enable efficient power distribution, and, most importantly, handle thermal management. The compatibility of these substrates with various semiconductor devices will also be a key focus.
Composition of Package Substrates
Discuss the materials commonly used in package substrates When it comes to package substrates, material selection is paramount. These substrates serve as the foundational support for semiconductor devices, with their composition exerting a profound influence on the performance and reliability of the end product. In the semiconductor packaging industry, two broad categories of package substrates are commonly employed: organic substrates and inorganic substrates. These materials serve as the building blocks upon which the intricate world of electronics is constructed, each with its unique characteristics and advantages.
Organic Substrates
Organic substrates are known for their versatility and cost-effectiveness, making them a popular choice for various semiconductor packaging applications. Two notable organic substrate materials are FR-4 and BT (Bismaleimide Triazine).
FR-4 (Flame Retardant-4)
FR-4 is a widely used substrate material, primarily composed of woven fiberglass impregnated with epoxy resin. It offers excellent electrical insulation properties, mechanical strength, and dimensional stability.
FR-4 substrates are suitable for applications where moderate heat resistance and good electrical performance are essential, making them prevalent in many consumer electronic devices.
BT (Bismaleimide Triazine)
BT substrates are engineered with bismaleimide triazine resin, providing superior thermal and mechanical properties. They exhibit exceptional thermal resistance and low moisture absorption.
BT substrates find frequent use in demanding high-performance applications, notably in the realms of advanced microprocessors and integrated circuits. In these scenarios, where precise thermal management is of paramount importance, BT substrates shine as a preferred choice. Their exceptional thermal properties make them an invaluable asset in ensuring the efficient cooling and optimal operation of these sophisticated electronic components.
Inorganic Substrates
Inorganic substrates, in stark contrast to their organic counterparts, are typically crafted from non-organic materials such as ceramics and metal cores. These specialized substrates present unique advantages that are particularly well-suited for specific applications within the semiconductor industry. Their robust and distinct material properties unlock opportunities for tailored solutions in demanding electronic environments.
Ceramic Substrates
Ceramic substrates are prized for their excellent thermal conductivity, which helps dissipate heat efficiently. They are often used in high-power semiconductor devices that generate substantial heat.
Due to their superior heat management properties, ceramic substrates find applications in power amplifiers, high-frequency RF circuits, and power LEDs.
Metal-Core Substrates
Metal-core substrates incorporate a metal layer as the core material, which provides good thermal conductivity and mechanical stability. Common metals used include aluminum and copper.
Metal-core substrates are utilized in LED modules, automotive electronics, and power converters where both heat management and structural integrity are crucial.
Explain the role of dielectric layers and conductive traces
Beyond the substrate material itself, package substrates feature multiple layers, including dielectric layers and conductive traces. These additional layers are essential for the substrate’s functionality and interconnectivity within the semiconductor package.
Dielectric Layers: Dielectric layers serve as insulating materials between conductive traces, preventing electrical shorts and promoting signal integrity. These layers are typically composed of materials with low dielectric constants to minimize signal loss and ensure proper isolation.
Conductive Traces: Conductive traces are thin, patterned metal lines that facilitate electrical connections between various components within the semiconductor package.
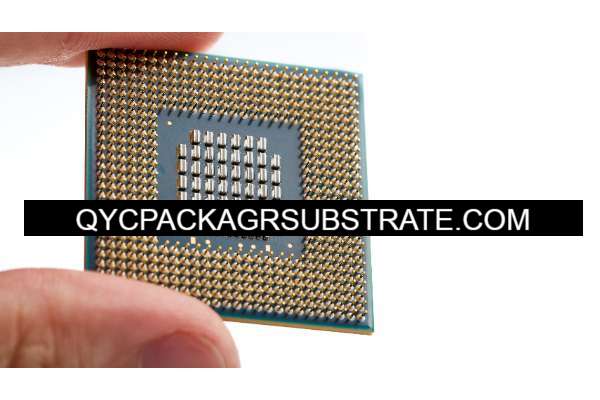
Substrates in Packaging: Their Crucial Role
Package substrates are the unsung heroes of the semiconductor world, playing an indispensable role in the functionality, signal transmission, and thermal management of electronic devices. Let’s delve deeper into these aspects:
Functionality of Substrates
When it comes to semiconductor packaging, functionality is key. Package substrates provide the structural foundation for semiconductor devices. They offer a stable platform on which the various components, including microchips, resistors, and capacitors, are mounted. These substrates are designed to ensure that the interconnected components work together seamlessly.
To achieve this, the substrate acts as an insulating layer, preventing unwanted electrical interactions between components. It also offers mechanical support, protecting delicate electronic elements from physical damage. This functional integrity is essential for the reliability and longevity of the final product.
Signal Transmission and Thermal Management
Signal transmission and thermal management are paramount in modern electronics. Package substrates are not passive elements; they actively participate in both of these critical functions.
1.Signal Transmission: Package substrates serve as the conduits for electrical signals between different components on a circuit board. The electrical traces etched onto the substrate facilitate the flow of data and power between the microchips, ensuring that your device operates smoothly. High-frequency signal transmission is especially crucial in applications like smartphones, where speed and efficiency are paramount.
2.Thermal Management: The demand for smaller, more powerful electronic devices has led to increased heat generation. Efficient thermal management is essential to prevent overheating and maintain optimal performance. Package substrates play a pivotal role in dissipating heat from the semiconductor devices. They are designed to have excellent thermal conductivity, ensuring that heat is effectively conducted away from the critical components. This is particularly important in applications such as gaming consoles and high-performance computers, where heat dissipation can significantly impact device reliability.
Compatibility with Semiconductor Devices
Compatibility with semiconductor devices is a non-negotiable requirement for package substrates. They must be designed to accommodate a wide range of semiconductor components, including microchips, integrated circuits, and sensors. The substrate’s material properties, size, and configuration must align with the specific needs of these devices.
Additionally, compatibility extends to the assembly process. Package substrates should be manufacturable using industry-standard processes, ensuring ease of integration into the overall product. Compatibility also involves electrical characteristics, such as impedance control, which ensures that signals propagate with minimal distortion.
In conclusion, package substrates are the unsung heroes of semiconductor packaging, providing the foundational support for electronic devices. They facilitate functionality, enable signal transmission, and ensure efficient thermal management while maintaining compatibility with a variety of semiconductor components. These substrates are the backbone of modern electronics, and their role continues to evolve with advancements in semiconductor technology.
PCB vs. Package Substrate
Printed Circuit Boards (PCBs) and package substrates are both essential components in electronic devices, but they serve distinct purposes and exhibit key differences that are crucial for semiconductor packaging. Let’s delve deeper into these disparities:
Application:
PCBs are primarily used as the central platform for connecting and supporting various electronic components within an electronic device. They serve as the backbone for interconnections, signal routing, and component attachment.
Package substrates, on the other hand, are specifically designed for semiconductor packaging. They provide the interface between the semiconductor chip and the larger electronic system, facilitating the connection and communication between the chip and the external world.
Material Selection:
PCBs are often constructed using a wide range of materials, including fiberglass-reinforced epoxy (FR-4) for traditional applications or more advanced materials like Rogers high-frequency laminates for RF (Radio Frequency) applications. Material selection in PCBs is driven by factors like electrical performance, cost, and environmental considerations.
Package substrates are typically made from materials optimized for the stringent demands of semiconductor packaging. Common materials include organic substrates like FR-4 and BT or inorganic substrates like ceramic and metal-core substrates. These materials are chosen to provide excellent thermal performance, electrical properties, and reliability, specifically for semiconductor applications.
Design Considerations:
PCB design revolves around optimizing signal integrity, electromagnetic interference (EMI) mitigation, and component placement. PCB designers need to consider factors such as trace lengths, impedance control, and layer stackup to ensure proper functionality.
Package substrate design places a strong emphasis on accommodating the semiconductor chip and its thermal management. The design must provide precise dielectric layers, fine-pitched conductive traces, and often incorporate advanced features like microvias for compact chip attachment and improved thermal dissipation.
In summary, while both PCBs and package substrates play pivotal roles in electronic devices, they are tailored for distinct applications. PCBs are versatile and used for interconnecting electronic components, while package substrates are specialized for semiconductor packaging, offering features and materials optimized for the unique demands of semiconductors. Understanding the differences between these two components is crucial for the efficient and reliable operation of electronic systems.
Packaging Semiconductor with Substrates
Discuss the Benefits of Using Package Substrates
The utilization of package substrates in semiconductor packaging offers a range of significant advantages:
Miniaturization: Package substrates enable the miniaturization of electronic devices by providing a compact and efficient platform for mounting and interconnecting semiconductor components. This is especially vital in applications where space is limited, such as smartphones, wearables, and IoT devices.
Thermal Management: Substrates with advanced thermal properties assist in heat dissipation from the semiconductor components, ensuring optimal operating temperatures. This is crucial for maintaining the long-term reliability of the devices.
Signal Integrity: Package substrates are engineered to provide consistent electrical performance, reducing signal losses and ensuring reliable data transmission. High-frequency applications, like 5G communication and automotive radar, benefit significantly from these improved signal integrity characteristics.
Reliability: Well-designed package substrates enhance the overall reliability of semiconductor devices. They protect against mechanical stress, thermal cycling, and environmental factors, extending the lifespan of the electronics.
Versatility: Package substrates come in various material options, such as organic and inorganic substrates, allowing designers to choose the best-suited material for a specific application.
Explore Challenges and Advancements in Substrate Technology
While package substrates offer numerous advantages, they also come with their set of challenges and areas for improvement. Advancements in substrate technology aim to address these challenges:
High-Density Interconnect (HDI): With the increasing demand for more compact and powerful electronic devices, HDI technology in package substrates is advancing. HDI substrates offer finer pitch interconnects, enabling increased component density and improved electrical performance.
Material Innovation: Ongoing research focuses on developing new substrate materials with enhanced thermal properties, electrical performance, and environmental sustainability. This innovation aims to meet the evolving requirements of the semiconductor industry.
3D Integration: Three-dimensional integration using package substrates allows for stacking multiple semiconductor chips on top of each other, saving space and improving overall system performance. However, this technology is still facing challenges in terms of cost and manufacturability.
Environmental Considerations: As sustainability becomes a growing concern, advancements in substrate technology aim to reduce the environmental impact of manufacturing processes and materials used in package substrates.
Cost Efficiency: Balancing technological advancements with cost efficiency remains a challenge. Manufacturers aim to deliver high-performance substrates at competitive prices to meet the demands of various industries.
In summary, package substrates are the unsung heroes of semiconductor packaging, providing a solid foundation for the world of microelectronics. Their role in enabling miniaturization, managing heat, maintaining signal integrity, and ensuring reliability cannot be overstated. The continuous evolution of substrate technology promises to meet the challenges of the ever-changing semiconductor landscape and drive innovation in electronic devices.