Semiconductor Packaging Substrate Maker. we can produce the best samllest bump pitch with 100um, the best smallest trace are 9um. and the smallest gap are 9um. most of the design are 15um to 30um trace and spacing.
Semiconductor packaging substrates, the unsung heroes of the intricate ballet that is the assembly and packaging of integrated circuits (ICs) or microchips, take center stage in orchestrating the connection between semiconductor devices and the broader external environment. These substrates wear multiple hats, seamlessly integrating electrical connections, adeptly managing thermal dynamics, and providing a robust foundation for mechanical support.
Coming in a variety of forms, such as the versatile printed circuit boards (PCBs), resilient ceramic substrates, and organic substrates, each variant caters to specific needs within the grand performance. PCBs, with their layered composition of conductive traces and insulating materials, perform a cost-effective dance, skillfully directing the flow of electrical signals and power distribution. In contrast, ceramic substrates, esteemed for their role in high-performance scenarios, boast impressive thermal conductivity and mechanical resilience.
The essence of semiconductor packaging substrates becomes apparent in their role as conductors of the symphony of electronic device functionality and reliability. They choreograph the intricate electrical connections between semiconductor chips and the external world, ensuring a seamless performance of signal transmission and power management. Simultaneously, these substrates take on the responsibility of dissipating the heat generated by semiconductor devices, preventing any overheating that could compromise the show’s grand finale of optimal performance.
In the ever-evolving landscape of semiconductor technology, the ongoing performance involves a continuous search for innovation in packaging substrates – a quest to enhance performance, shrink dimensions, and fortify overall efficiency. As electronic devices gracefully pirouette towards sleeker potency, semiconductor packaging substrates emerge as indispensable conductors, facilitating the integration of cutting-edge semiconductor components across diverse stages, from the chic realm of consumer electronics to the robust grandeur of industrial systems.
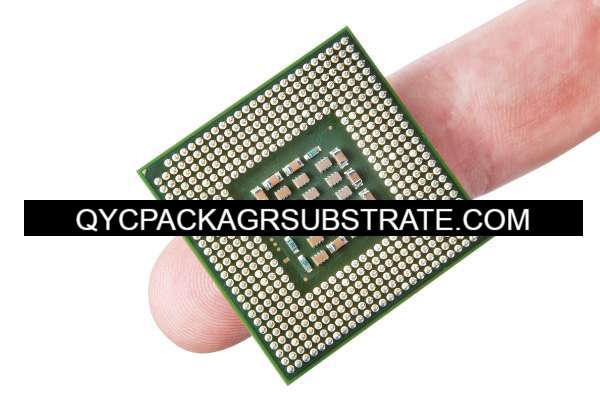
What Functions Does Semiconductor Packaging Substrate Serve?
Consider semiconductor packaging substrates as the unsung maestros orchestrating the intricate ballet within electronic devices. These substrates wear many hats, each contributing to the overall efficiency, reliability, and performance of electronic systems. Let’s unravel the distinct roles undertaken by semiconductor packaging substrates:
Architects of Connectivity: Fundamentally, these substrates act as architects, designing intricate electrical connections that form the backbone between the semiconductor chip and other electronic companions. The delicate dance of conductive traces creates a pathway, allowing signals and power to gracefully traverse through various components on a printed circuit board (PCB).
Maestros of Power Distribution: Picture the substrate as a seasoned maestro, skillfully directing the distribution of electrical power throughout the electronic device. Its expertise ensures a harmonious flow of power from the source to the semiconductor chip and other components, ensuring each receives the necessary energy for peak performance.
Conductors of Signal Harmony: Serving as conductors of a musical symphony, substrates channel the harmonious flow of signals between the semiconductor chip and other elements in the electronic orchestra. This orchestration is pivotal for the smooth exchange of data and instructions, contributing to the coherence and brilliance of the overall device performance.
Ballet Masters of Thermal Dynamics: In the ballet of operation, semiconductor devices emit heat, and the substrate takes on the role of a ballet master, orchestrating the graceful dissipation of this heat. By preventing overheating, it ensures the electronic components perform flawlessly, taking center stage and extending their operational lifespan.
Sturdy Stage Managers: Imagine substrates as reliable stage managers, providing essential mechanical support and protection for the delicate semiconductor chip. This support ensures a seamless performance, safeguarding against mishaps like bending or breakage during handling, assembly, and use.
Artisans of Form Factor Elegance: Substrates act as artisans, sculpting the form factor and size of the electronic device. Their craftsmanship allows for the art of miniaturization and seamless integration of components, aligning with the contemporary trend towards sleek and compact electronic devices.
Guardians against Environmental Elements: In the grand production, substrates function as vigilant guardians, shielding the semiconductor chip from environmental elements such as moisture, dust, and contaminants. This protective role ensures the longevity and reliability of the electronic device throughout its performance lifecycle.
In essence, semiconductor packaging substrates are the masterful conductors behind the scenes, shaping the intricate infrastructure required for the seamless integration of semiconductor devices into electronic systems. Their diverse roles contribute to the proper functioning, resilience, and optimal performance of electronic components across a spectrum of applications, making them indispensable orchestrators in the electronic ballet.
What Are the Different Types of Semiconductor Packaging Substrates?
Semiconductor packaging substrates exhibit diverse types, each tailored to specific applications based on their unique characteristics. Here’s a glimpse into the various types and their roles across different applications:
Versatile Printed Circuit Boards (PCBs):
Material: Organic compositions like glass-reinforced epoxy.
Function: PCBs serve as ubiquitous platforms in numerous electronic applications. Their conductive traces facilitate electrical connections, making them adaptable for applications spanning consumer electronics, automotive systems, and industrial devices.
Thermally Efficient Ceramic Substrates:
Material: Alumina or aluminum nitride ceramics.
Function: Ceramic substrates excel in thermal conductivity and mechanical stability. They find applications in scenarios demanding efficient heat dissipation, such as power modules, RF devices, and LED packages.
Flexible Substrates for Bendable Electronics:
Material: Polyimide or other flexible materials.
Function: Flexible substrates cater to applications requiring flexibility, such as wearable devices and flexible displays. Their pliability and lightweight nature make them essential in bendable electronics.
Sturdy Leadframe Substrates:
Material: Metal frames predominantly made of copper or alloy.
Function:Leadframes act as the robust underpinning and efficient heat dissipators, playing a vital role in managing thermal conditions. They find widespread use in packaging integrated circuits for consumer electronics and automotive components.
Cost-Effective Organic Substrates:
Material: BT (Bismaleimide Triazine) or FR-4 (Flame Retardant 4).
Function: Organic substrates present a budget-friendly alternative, boasting commendable electrical insulation properties. Widely embraced in the domain of consumer electronics, these organic substrates seamlessly meld into the architecture of devices like mobile phones and laptops.
Interposer Substrates for 3D Integration:
Material: Silicon or organic materials.
Function: Interposer substrates facilitate the integration of semiconductor components in a three-dimensional arrangement, enhancing performance. They are instrumental in applications such as high-performance computing and advanced memory systems.
System-in-Package (SiP) Substrates:
Material: Varied, including organic and laminate materials.
Function:System-in-Package (SiP) substrates empower the amalgamation of diverse semiconductor components within a singular enclosure. Embraced extensively in smartphones, IoT gadgets, and medical apparatus, SiP technology propels an elevation in the comprehensive efficacy and efficiency of the entire system.
The selection of a substrate type depends on specific application requirements, encompassing thermal considerations, form factor constraints, and electrical performance criteria. Each substrate type plays a crucial and distinct role in the packaging and integration of semiconductor devices across diverse industries and applications.
How Does Semiconductor Packaging Substrate Differ from PCB and IC Packaging?
Semiconductor packaging substrates, Printed Circuit Boards (PCBs), and Integrated Circuit (IC) packaging weave a complex web within the landscape of electronics, each contributing its unique role and features.
Semiconductor Packaging Substrates:
Function: These substrates play a vital role, providing a robust foundation for semiconductor devices. They excel in facilitating electrical connections, efficient thermal management, and sturdy mechanical support.
Design: With meticulous craftsmanship tailored to the specific integration demands of semiconductor components, these substrates emerge as central figures in the packaging process, guaranteeing the smooth integration of chips into the expansive realm of the electronic landscape.
Application: From consumer electronics to a diverse array of electronic applications, semiconductor packaging substrates emerge as crucial contributors, enhancing both functionality and reliability across a broad spectrum.
Printed Circuit Boards (PCBs):
Role: Serving as the nerve center, PCBs interconnect and support a diverse array of electronic components. Their layered composition of conductive traces and insulating materials makes them versatile for accommodating various elements, including semiconductors.
Design: Functioning as a dynamic canvas, PCBs provide a platform adaptable to a wide spectrum of electronic components, forming the backbone of electronic systems.
Application: Whether in everyday gadgets or sophisticated computing devices, PCBs lay the architectural groundwork for electronic systems.
Integrated Circuit (IC) Packaging:
Purpose: IC packaging transcends mere protection, encapsulating semiconductor chips within shields that offer not only electrical connections but also a defense against external elements.
Design: Focused on encapsulating and connecting individual semiconductor chips, IC packaging introduces a range of types, such as DIP, BGA, and QFP, tailored to specific application needs.
Application: IC packaging doesn’t just shield semiconductor chips; it plays a pivotal role in sculpting the overall form and external connections of electronic devices, seamlessly integrating these chips into the broader design.
In navigating the intricate landscape of electronics, semiconductor packaging substrates, PCBs, and IC packaging emerge as indispensable threads, each weaving its own pattern into the fabric of electronic systems. The classification of chip package technologies delves into mounting techniques, form factors, and integration intricacies, adding layers to the richness of electronic design.
How Do Semiconductor Packaging Substrates Differ from PCBs?
Semiconductor packaging substrates and conventional Printed Circuit Boards (PCBs) may share a structural foundation, but their destinies diverge when it comes to applications and design intricacies. Let’s navigate through the subtleties of their commonalities and disparities, all while embarking on a journey to discern their differences from motherboards, substrates, Substrate-Like PCBs (SLP), and High-Density Interconnect (HDI) substrates.
Semiconductor Packaging Substrates vs. PCBs:
Similarities:
Structure: Both exhibit a layered composition with insulating material and conductive traces.
Function: Both serve as platforms for mounting and interconnecting electronic components, ensuring electrical connections and power distribution.
Differences:
Purpose: Semiconductor packaging substrates carve a niche as specialists in the realm of semiconductor integration. In contrast, PCBs cast a wider net, embracing a diverse range of electronic components within their expansive application scope.
Application: Semiconductor packaging substrates play a key role in the specific context of semiconductor device integration, whereas PCBs find use across diverse electronic systems.
Differences from Motherboards:
Semiconductor Packaging Substrates and PCBs: While both contribute to connecting electronic components, motherboards stand out as larger, more intricate PCBs, serving as central hubs in computers or electronic systems.
Differences from Substrates:
Semiconductor Packaging Substrates and PCBs: “Substrates” serves as a broad term encompassing both semiconductor packaging substrates and conventional PCBs. The key divergence surfaces in their distinct designs and purposes, as semiconductor packaging substrates are meticulously crafted for the specific task of seamlessly integrating semiconductor components.
Differences from Substrate-Like PCBs (SLP):
Semiconductor Packaging Substrates: Specialized for semiconductor integration, providing a foundation for chip mounting.
SLP: Mimic the structure of semiconductor substrates but remain traditional PCBs, designed for compactness and thin profiles, often used in mobile devices.
Differences from High-Density Interconnect (HDI) Substrates:
Semiconductor Packaging Substrates: Primarily focus on supporting and integrating semiconductor devices with attention to their specific requirements.
HDI Substrates: Emphasize high-density interconnects, maximizing components and connections in a confined space, commonly used in applications with stringent space constraints like smartphones.
In essence, while semiconductor packaging substrates and traditional PCBs share foundational characteristics, their divergent applications and target components set them apart. Motherboards, substrates, SLPs, and HDI substrates each bring unique features, tailoring their functionalities to distinct roles within electronic systems.
What are the Main Structure and Production Technologies of Semiconductor Packaging Substrates?
Semiconductor packaging substrates boast a sophisticated structural composition that plays a pivotal role in the optimal functioning of electronic devices. Here’s a detailed exploration of the key components and the innovative production technologies involved:
Structural Elements:
Base Material:
The foundation includes diverse materials like organic substrates, ceramics such as alumina or aluminum nitride, and cutting-edge options like liquid crystal polymer (LCP).
Organic materials like BT (Bismaleimide Triazine) or FR-4 (Flame Retardant 4) offer cost-effective solutions with reliable electrical insulation.
Conductive Traces:
Intricate layers of conductive materials, often copper, form the intricate web of wiring that facilitates seamless electrical connections.
Dielectric Layers:
Insulating layers, crafted from materials like epoxy or polyimide, ensure a precise separation between conductive traces, preventing any risk of short circuits while maintaining essential isolation.
Solder Mask:
This protective layer, applied meticulously over conductive traces, shields against oxidation and streamlines the soldering process during the assembly of electronic components.
Surface Finish:
Final layers, which may include gold plating or tin-lead finishes, dictate surface properties to optimize the attachment of electronic components.
Production Techniques:
HDI Fabrication Technology:
High-Density Interconnect (HDI) technology revolutionizes substrate creation by enabling the development of densely packed substrates with intricate wiring patterns.
Advanced HDI fabrication incorporates multiple layers of thin traces and vias, minimizing signal delays and amplifying overall performance.
Semi-Additive Methods:
Departing from conventional subtractive methods, semi-additive processes selectively introduce copper to construct conductive features, allowing for finer details and heightened complexity.
Laser Direct Imaging (LDI):
LDI technology takes the reins from traditional photolithography, offering precise imaging of circuit patterns on the substrate and elevating accuracy in trace placement.
Embedding Technologies:
Forward-thinking packaging substrates leverage embedding technologies, integrating components like passive devices or semiconductor chips within the substrate material. This innovative approach enhances electrical performance, reduces footprint, and bolsters thermal dissipation.
Advanced Materials and 3D Printing:
Emerging technologies push boundaries with the incorporation of advanced materials and 3D printing techniques, providing unparalleled design flexibility and optimizing electrical and thermal properties.
The intricate dance between these structural elements and production technologies underscores the adaptability of semiconductor packaging substrates to meet the dynamic demands of electronic devices. This synergy fosters miniaturization, heightened performance, and expanded functionality across diverse applications.
Frequently Asked Questions (FAQs)
Can you explain the manufacturing process of semiconductor packaging substrates?
Manufacturing involves advanced processes like High-Density Interconnect (HDI) fabrication, semi-additive methods, Laser Direct Imaging (LDI) for precise circuit pattern imaging, and embedding technologies. These methods contribute to finer features, increased complexity, and improved accuracy in substrate fabrication.
What is the significance of High-Density Interconnect (HDI) technology in semiconductor packaging substrates?
HDI technology is integral for crafting densely packed substrates with intricate wiring patterns. It facilitates high-density interconnections, leading to reduced signal propagation delays, improved electrical performance, and streamlined miniaturization in electronic devices.
How do semiconductor packaging substrates differ from traditional printed circuit boards (PCBs)?
While sharing a structural foundation, semiconductor packaging substrates specialize in semiconductor integration, addressing the unique needs of chips or dies. In contrast, PCBs have a broader application, accommodating various electronic components beyond semiconductors.
In what ways do semiconductor packaging substrates contribute to the miniaturization of electronic devices?
Semiconductor packaging substrates significantly contribute to miniaturization by providing efficient platforms for semiconductor integration. HDI technology, advanced materials, and embedding technologies collectively enable the reduction of device footprint while maintaining or enhancing functionality.
Conclusion
In the intricate realm of electronic packaging, semiconductor packaging substrates emerge as silent champions, propelling innovation and shaping the landscape for the seamless integration of electronic components in the forthcoming era of devices. Delving into the intricacies of these substrates and remaining attuned to technological strides not only enhances our comprehension of their complexities but also provides a glimpse into the future trends that will define this dynamic industry. As we acknowledge the pivotal role played by semiconductor packaging substrates, we anticipate a future where their advancements continue to catalyze progress and redefine the possibilities within electronic systems.