Packaging Substrate Vender. Semiconductor Packaging Substrate Quote. Quickly confirm the packaging substrate material and production process, quickly confirm and reply to the price and delivery.
In the intricate process of assembling integrated circuits (ICs) or microchips, the semiconductor packaging substrate emerges as a linchpin. Operating as a pivotal bridge, it serves both as a physical and electrical intermediary, forging a vital connection between the semiconductor die (the tangible silicon chip) and the printed circuit board (PCB) or alternative packaging methods.
The substrate acts as a foundational bedrock, facilitating the installation and interconnection of the semiconductor die with external components. Its primary objective lies in orchestrating the complex web of electrical connections between the die and the broader electronic system. Additionally, the substrate plays a crucial role in dissipating the heat generated by the semiconductor device.
With diverse manifestations, semiconductor packaging substrates come in various configurations, encompassing leadframe-based packages, organic substrates, and sophisticated alternatives like flip-chip packages. The choice of a specific substrate hinges on considerations such as the intended application, performance prerequisites, and cost dynamics within the intricate landscape of designing and manufacturing electronic devices.
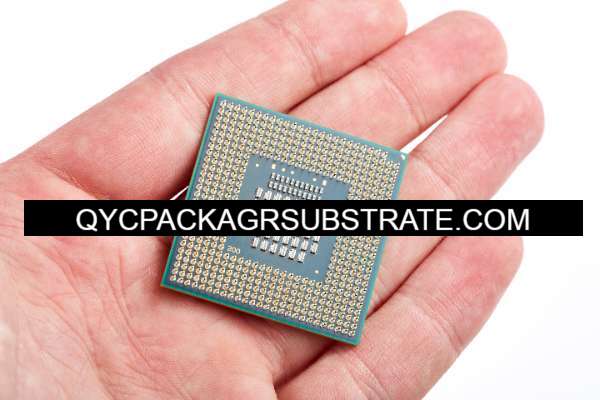
What Function Does Semiconductor Packaging Substrate Serve?
Within the intricate domain of assembling integrated circuits (ICs), the semiconductor packaging substrate assumes a multifaceted role, wielding an array of pivotal functions. Let’s infuse a different flavor into the description:
Confluence of Connectivity: In its essence, the substrate acts as a confluence, intricately merging both the physical and electrical dimensions between the semiconductor die and the printed circuit board (PCB) or alternative packaging methods.
Architect of Integration: Functioning as an architect, the substrate lays the groundwork for the semiconductor die, establishing a robust foundation for seamless integration and collaboration with external components.
Electrical Harmony Conductor: Analogous to a conductor leading a symphony, the substrate orchestrates the intricate interplay of electrical connections between the semiconductor die and the expansive landscape of the electronic system.
Thermal Dynamics Navigator: Beyond its electrical duties, the substrate transforms into a navigator in thermal dynamics, adeptly managing the dissipation of heat emanating from the semiconductor device. This expertise is crucial for maintaining optimal operational conditions.
Guardian of Mechanical Integrity: In the mechanical realm, the substrate serves as a guardian, offering resilient mechanical support to the delicate semiconductor die. This protective shield mitigates the impact of physical stress, vibrations, and environmental factors.
Adaptable Configurator: Much like an adaptable configurator, semiconductor packaging substrates manifest in diverse configurations—from leadframe-based packages to organic substrates and advanced alternatives like flip-chip packages. The selection process involves nuanced decisions influenced by factors such as application intricacies and cost considerations.
In essence, the semiconductor packaging substrate emerges not just as a functional component but as a versatile conductor and navigator, harmonizing a symphony of connectivity, resilience, and efficiency within the intricate landscape of electronic systems.
What Are the Different Types of Semiconductor Packaging Substrate?
Semiconductor packaging substrates unfold a tapestry of diversity, each intricately tailored for specific characteristics and applications. Let’s embark on a journey through these classifications with a fresh lens:
Leadframe-Based Packages: Rooted in tradition, leadframes fashion a metallic framework for mounting and connecting semiconductor dies. Revered for their cost-effectiveness, they carve a space in applications where avant-garde performance takes a back seat.
Organic Substrates: Forged from materials like epoxy resin or fiberglass-reinforced epoxy, organic substrates strike a delicate balance between weight and cost efficiency. They frequently grace the realm of consumer electronics, delivering practicality without compromising performance.
Ceramic Substrates: Applauded for their thermal prowess, ceramic substrates illuminate applications craving efficient heat dissipation. Industries like power electronics and high-frequency circuits bask in the thermal glow of ceramics.
Flip-Chip Packages: Embracing ingenuity, flip-chip packages orchestrate the inversion of the semiconductor die, delicately mounting it face-down on the substrate. This unconventional ballet optimizes both electrical performance and heat dissipation, earning applause in high-performance applications.
Chip Scale Package (CSP): CSP redefines spatial dynamics, sculpting a package size mirroring the semiconductor die closely. This streamlined design caters to electronic devices yearning for sleekness, epitomized by ubiquitous gadgets like mobile phones.
Ball Grid Array (BGA): Distinguished by a grid of solder balls beneath, BGAs are the architects of density, crafting high-density landscapes for microprocessors and fostering a profusion of connections.
Multi-Chip Module (MCM): MCM embraces synergy, encapsulating multiple semiconductor dies within a single module. This choreographed ensemble elevates functionality and performance, all neatly housed in a compact form factor.
Fan-Out Wafer-Level Packaging (FOWLP): FOWLP disrupts conventions by orchestrating a redistribution of connections from the semiconductor die to a broader area on the substrate. This avant-garde performance art enhances electrical prowess, particularly in cutting-edge applications like mobile devices.
The selection of the optimal semiconductor packaging substrate is an art, blending considerations of intended application, performance benchmarks, thermal dynamics, and budget constraints into a harmonious composition.
How Does Semiconductor Packaging Substrate Relate to IC Packaging?
Semiconductor packaging substrate and IC packaging join forces in a complex partnership, acting as the cornerstone of integrated circuit functionality. Let’s reshape their connection with a unique lens:
Foundational Nexus: The semiconductor packaging substrate emerges as a foundational nexus, establishing a sturdy base for the intricate assembly of integrated circuits (ICs). It becomes the canvas where the semiconductor die takes center stage, forging vital connections.
Electrical Conductor: At its core, the substrate transforms into an electrical conductor, orchestrating the seamless flow of electrical signals between the semiconductor die and external components or the printed circuit board (PCB). It assumes a central role in harmonizing the semiconductor device within the broader electronic landscape.
Thermal Director: The substrate takes on the role of a thermal director, directing the intricate choreography of heat dissipation. It ensures the graceful dispersion of heat generated during the semiconductor device’s operation, preventing overheating and maintaining an environment conducive to optimal performance.
Guardian of Structural Fortitude: Beyond its electrical functions, the substrate becomes a guardian, providing a protective fortress for the delicate semiconductor die. It acts as a shield against physical stresses, vibrations, and environmental elements, fortifying the structural integrity of the IC.
Diverse Packaging Ensemble: Semiconductor packaging substrates showcase a diverse ensemble of configurations, ranging from conventional leadframe-based packages to avant-garde solutions like organic substrates and flip-chip packages. This ensemble adapts to the unique demands of applications, orchestrating a symphony of performance and cost considerations.
Tailored Compatibility Choreography: The substrate’s design undergoes meticulous choreography, ensuring seamless compatibility with various types of ICs. It adjusts its form to align with the distinct characteristics of the IC it cradles, considering factors such as size, power specifications, and intended application.
Influence on Signal Dynamics: The substrate’s design intricacies influence the dynamic interplay of signals within the IC. Considerations such as signal propagation delay, impedance matching, and mitigation of parasitic effects become integral to the composition, orchestrating a dynamic symphony of electrical performance.
In essence, semiconductor packaging substrate and IC packaging engage in a sophisticated dance, seamlessly integrating the physical, electrical, and thermal elements to unveil the optimal functionality of integrated circuits in electronic devices.
What Are the Differences Between Semiconductor Packaging Substrate and Regular PCBs?
Semiconductor packaging substrates and regular printed circuit boards (PCBs) embark on distinct journeys in the electronic landscape, each bringing a unique set of skills to the canvas of connectivity. Let’s explore the nuances that set them apart:
Specialized Odyssey:
Semiconductor Packaging Substrate: Undertaking a specialized mission, these substrates carve out a niche as platforms dedicated to mounting and interconnecting semiconductor dies. Their focal point is precision, ensuring the seamless integration and connectivity of integrated circuits (ICs) with a meticulous focus on electrical pathways.
Regular PCB: In the vast expanse of electronics, regular PCBs adopt a versatile persona. Their mission extends beyond semiconductors, providing a flexible environment for a diverse array of electronic components. They weave connections and pathways for a varied ensemble of circuits.
Material Symphony:
Semiconductor Packaging Substrate: Fashioned from materials finely tuned to meet the distinctive requirements of semiconductor packaging, these include organic substrates such as FR-4, ceramics, or materials meticulously engineered to navigate the complexities of high-frequency and high-performance scenarios.
Regular PCB: Regular PCBs, embracing the dependable nature of FR-4, strategically choose materials that align with cost-effectiveness, catering to the broad spectrum of general electronic applications. Material selections undergo a tailored transformation to harmonize with the nuanced demands and specific requirements inherent in the circuit at hand.
Architectural Ballet:
Semiconductor Packaging Substrate: Unveiling a bespoke ballet of design, semiconductor packaging substrates choreograph their layout with precision to align seamlessly with the architecture of a semiconductor die. Bonding pads, vias, and traces perform an intricate dance dictated by the die’s blueprint.
Regular PCB: Taking a universal stance, the design of a regular PCB is a comprehensive composition, accommodating a variety of electronic components. Traces, pads, and components follow a broader choreography dictated by the overall circuit design.
Electrical Performance Art:
Semiconductor Packaging Substrate: A refined performance unfolds, with semiconductor packaging substrates adhering to stringent criteria. Controlled impedance, minimal signal loss, and efficient power distribution take center stage, orchestrating the optimal performance of the semiconductor device.
Regular PCB: While electrical competence remains crucial, regular PCBs may not demand the same level of precision. Their emphasis is on establishing reliable connections, with functionality taking precedence over the intricacies of high-frequency or high-performance scenarios.
Applications Tapestry:
Semiconductor Packaging Substrate: Reserved for the specialized realm of integrated circuits, semiconductor packaging substrates find applications in microprocessors, memory chips, and various integrated circuits.
Regular PCB: Ubiquitous and versatile, regular PCBs find homes in a myriad of electronic devices, spanning from consumer electronics to industrial machinery. Their adaptability caters to the diverse needs and flavors of electronic circuits.
In essence, semiconductor packaging substrates and regular PCBs, each wielding a distinctive brushstroke, contribute to the rich tapestry of electronic connectivity. Semiconductor packaging substrates are the artisans of semiconductor integration, while regular PCBs serve as the universal canvases accommodating a diverse ensemble of electronic components.
What Are the Main Structure and Production Technologies of Semiconductor Packaging Substrate?
Semiconductor packaging substrates exhibit a myriad of structural elements, carefully shaped by a range of production technologies to cater to the intricate needs of modern integrated circuits. Let’s explore the key structures and the technological tapestry that weaves them together:
Architectural Ensemble of Semiconductor Packaging Substrate:
Foundational Core:
Composition: The core substrate lays the groundwork, often composed of materials like FR-4 or other advanced alternatives. FR-4, renowned for its electrical insulation prowess, provides a cost-effective base.
Insulating Layer:
Material: Above the core, an insulating layer is delicately applied, commonly crafted from materials like polyimide or epoxy. This layer ensures insulation between the conductive layers, preventing unintended interactions.
Conductive Tapestry:
Copper Artistry: Woven into the substrate are conductive layers, usually fashioned from copper foils. These layers are meticulously patterned to give life to circuits, traces, and bonding pads, utilizing copper’s excellent conductivity.
Guardian Solder Mask:
Material Palette: A protective solder mask layer graces the surface, safeguarding the integrity of conductive traces and pads during assembly. This layer, often composed of epoxy-based materials, acts as a shield during the soldering process.
Surface Finishing Flourish:
Surface Elegance: A final surface finish adds a touch of refinement, enhancing solderability and shielding against oxidation. Choices include HASL, ENIG, or OSP, each contributing to the substrate’s surface aesthetics.
Via Symphony:
Structural Harmony: Viaducts, known as vias, traverse the layers, establishing vital electrical connections between different strata. Vias can take the form of filled or unfilled conduits, depending on the desired orchestration.
Copper Plating Crescendo:
Process Unveiled: A copper plating process unfolds, enriching the thickness of conductive layers and ensuring robust electrical connections, a crescendo of metallurgical artistry.
Artisanal Production Technologies:
PCB Pioneering:
Craftsmanship: The journey begins with PCB manufacturing processes, encompassing layer stacking, drilling, and imaging, shaping the initial canvas.
Copper Foil Lamination Ballet:
Thermal Choreography: Copper foils take center stage, undergoing a lamination ballet with heat and pressure, creating the intricate dance of conductive layers and bonding pads.
Etching Elegance:
Selective Unveiling: Etching gracefully removes excess copper, revealing the desired circuit patterns and traces with artistic precision.
Solder Mask Artistry:
Precision Brushstrokes: Solder mask material is delicately applied and selectively cured, providing protective strokes where needed and exposing areas for soldering.
Surface Finish Flourish:
Gilding Process: The chosen surface finish is applied, gilding the exposed copper surfaces with a touch of sophistication to enhance solderability and stave off oxidation.
Via Formation Symphony:
Drill Crescendo: Vias emerge through drilling or laser processes, conducting a symphony of connectivity by establishing vital electrical links.
Copper Plating Crescendo:
Metallurgical Flourish: Copper plating may be employed to augment the thickness of conductive layers, infusing a final touch of metallurgical flourish to enhance electrical conductivity.
Final Inspection Overture:
Curtain Call: The completed substrate takes a bow, undergoing a meticulous final inspection and testing, ensuring alignment with design specifications and functional excellence.
This intricate interplay of structures and production technologies crafts semiconductor packaging substrates, transforming them into tailored masterpieces designed to meet the diverse demands of integrated circuits, whether in traditional leadframe-based packages or avant-garde solutions like organic substrates and flip-chip packages.
Frequently Asked Questions (FAQs)
What are the different types of Semiconductor Packaging Substrates?
Types include organic substrates (e.g., FR-4), ceramics, and advanced configurations like flip-chip packages. The choice depends on the specific requirements of the integrated circuit.
What is the role of vias in Semiconductor Packaging Substrates?
Vias establish electrical connections between different layers of the substrate, ensuring the seamless flow of electrical signals through the integrated circuit.
How does the design of Semiconductor Packaging Substrates impact electrical performance?
The design influences electrical performance by considering factors such as controlled impedance, signal propagation delay, and mitigation of parasitic effects, ensuring optimal functionality.
In what applications are Semiconductor Packaging Substrates commonly used?
Semiconductor packaging substrates find applications in a wide range of electronic devices, including microprocessors, memory chips, and various integrated circuits used in consumer electronics, telecommunications, and industrial equipment.
Conclusion
In summary, Semiconductor Packaging Substrates emerge as the uncelebrated protagonists in the intricate saga of integrated circuits. Their significance transcends mere functionality, delving into the artistry of materials, intricate structures, and sophisticated production methodologies. These substrates serve as the unsung architects, crafting the backbone of electronic devices with a precision that often goes unnoticed.
As we navigate the labyrinth of electrical intricacies, thermal intricacies, and structural complexities, Semiconductor Packaging Substrates unveil themselves as not just platforms but as exquisite masterpieces finely tuned for the demands of contemporary integrated circuits. The dance of copper foils, the meticulous strokes of solder masks, and the orchestrated harmony of vias all contribute to a design symphony that defines these substrates.
The material selection, ranging from the steadfast FR-4 to avant-garde compositions, reflects a commitment to pushing the boundaries of performance across diverse applications. The exploration of frequently asked questions (FAQs) offers a glimpse into the curiosity surrounding Semiconductor Packaging Substrates, shedding light on their functions, materials, and distinctions from regular PCBs.
From the core substrate’s inception to the final inspection crescendo, the production journey unfolds as a meticulous symphony, where each process plays a crucial note in the substrate’s ultimate performance. Semiconductor Packaging Substrates, often operating behind the scenes, emerge as the silent artisans shaping the electronic landscape.