Professional Semiconductor substrate supplier, we mainly produce ultra-small bump pitch substrate, ultra-small trace and spacing packaging substrate and HDI PCBs.
The semiconductor substrate functions as the essential canvas for the intricate construction of semiconductor devices or chips. It serves as the pivotal foundation where diverse semiconductor elements, including transistors, diodes, and interconnects, are meticulously brought into existence, imparting both structural support and electrical pathways.
Within the domain of semiconductor chips, the substrate plays a central role, even though its primary emphasis isn’t on encapsulation.The actual encapsulation typically takes place through packaging materials after the semiconductor devices have undergone manufacturing on the substrate. The core duties of the substrate involve furnishing a robust and conductive groundwork for assembling semiconductor components and facilitating the smooth establishment of electrical connections among them.
Silicon assumes a central role as the primary material for semiconductor substrates, yet alternatives like gallium arsenide (GaAs) and silicon carbide (SiC) make their presence felt, tailored to specific applications. The selection of substrate material pivots on factors including the intended purpose of the semiconductor device, preferred electrical characteristics, and considerations in the manufacturing process.
Precision technology emerges as the unsung hero throughout the manufacturing journey, ensuring the reliability and prowess not only of the semiconductor substrate but also of the entire chip. The fabrication of semiconductor devices involves intricate processes like photolithography, etching, deposition, and doping, demanding precision and control at the nano-level to sculpt the intended patterns and structures on the substrate. Any deviation from the designated design parameters can resonate, affecting the functionality and performance of the semiconductor device.
In summary, while the substrate itself doesn’t take on the encapsulation or packaging of the semiconductor chip, it assumes a vital role in shaping the chip’s core and facilitating electrical connections. Precision technology stands as the linchpin throughout the manufacturing adventure, ensuring the attainment of required specifications and securing the reliability of the semiconductor device.
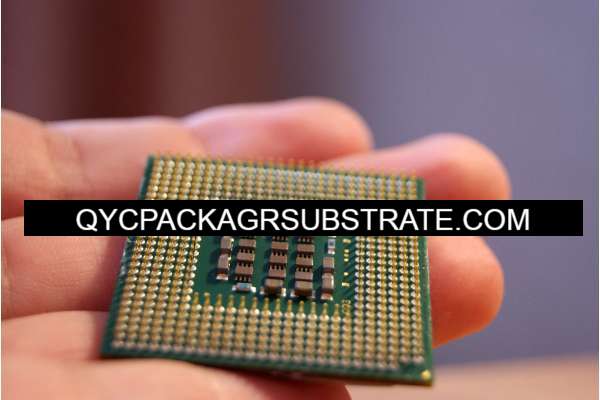
What is the Function of a Semiconductor Substrate?
The semiconductor substrate assumes a dynamic and indispensable role in the realm of electronic devices, contributing to their intricate functionality. It encompasses a spectrum of functions essential to modern electronics:
Groundwork for Semiconductor Components:
Serving as a steadfast platform, the substrate facilitates the creation of pivotal semiconductor components like transistors and diodes, forming the elemental architecture of electronic circuits.
Enabler of Electrical Connectivity:
The substrate acts as a conduit, fostering smooth electrical connections between diverse semiconductor components. This function is paramount for the coherent operation of electronic devices.
Provider of Structural Support:
Beyond its electrical duties, the substrate extends critical mechanical support to semiconductor components. It ensures the resilience of these intricate structures, safeguarding against physical strains during handling and operation.
Contributor to Thermal Management:
In certain scenarios, the substrate plays a role in managing heat. Efficient heat dissipation plays a critical role in maintaining the peak performance and reliability of semiconductor devices. Specific substrate materials and designs are harnessed to address thermal considerations.
Hub for Integration:
Operating as an integration nexus, the substrate facilitates the amalgamation and interlinking of diverse semiconductor components. This integrative capability is fundamental to the evolution of sophisticated electronic devices.
Comprehending the diverse roles undertaken by the substrate underscores its paramount importance in shaping the performance and reliability of electronic devices. Whether anchoring a resilient foundation, fostering electrical connectivity, providing mechanical reinforcement, or contributing to heat regulation, the substrate’s versatile functions stand at the core of the design and manufacturing processes of contemporary electronic devices.
What are the Different Types of Semiconductor Substrates?
Within the intricate tapestry of semiconductor technology, two intertwined realms come to the forefront—semiconductor substrate manufacturing and integrated circuit (IC) packaging. These collaborative processes dance in unison to bring electronic devices into existence. Let’s navigate through their classifications to unravel the nuances of their roles and applications:
Semiconductor Substrate Manufacturing:
Technology Classifications: This realm revolves around sculpting the foundational material where semiconductor devices take shape. Technologies like wafer fabrication employ processes such as lithography, etching, and doping on a silicon wafer, weaving the intricate threads of essential semiconductor components.
Applications: Semiconductor substrates serve as the foundational canvases for the construction of integrated circuits and a diverse range of electronic devices. The meticulous selection of materials, sizes, and fabrication processes is finely tuned to cater to the distinct requirements of a variety of semiconductor devices.
IC Packaging:
Technology Classifications: IC packaging steps onto the stage to enrobe the semiconductor device within a protective package, providing not just a shield but also electrical connections, thermal regulation, and fortification against environmental elements. Packaging technologies unfold in diverse forms, including Ball Grid Array (BGA), Quad Flat No-Lead (QFN), Chip-on-Board (COB), and more.
Applications: The dance of IC packaging technologies adapts to the rhythm of device size, thermal dissipation needs, and the specific application at hand. Each packaging technique offers a unique blend of protection, thermal management, and electrical connectivity.
The Harmonious Convergence:
Interplay between Substrate and Packaging: The collaboration between semiconductor substrate manufacturing and IC packaging is akin to a seamless dance. Following the meticulous crafting of semiconductor components on the substrate, the packaging process takes center stage—ensuring the components are shielded from external influences while establishing precise electrical connections. This orchestrated integration is paramount for the flawless functionality of electronic systems.
System Integration: The fusion of semiconductor substrate manufacturing and IC packaging stands as the linchpin for comprehensive system integration. This collective effort ensures not only the artful fabrication of semiconductor components but also their secure encapsulation and efficient interconnection, laying the foundation for robust functionality.
In essence, semiconductor substrate manufacturing and IC packaging engage in a symbiotic dance within the expansive landscape of semiconductor manufacturing. The diverse classifications within these processes converge to craft bespoke semiconductor devices, addressing a spectrum of needs across various applications in the ever-evolving realm of modern electronics.
Differences Between Semiconductor Substrates and PCBs?
Semiconductor substrates and printed circuit boards (PCBs) stand apart with distinct structures and functionalities, each tailored meticulously for specialized roles in the electronics industry. To elucidate these differences, let’s embark on a comparative exploration, focusing our analysis on motherboards, Substrate Like PCBs (SLPs), and High-Density Interconnect (HDI) substrates.This exploration endeavors to furnish readers with a holistic understanding of semiconductor substrate characteristics in comparison to traditional PCBs:
Motherboards:
Structure:Motherboards, categorized within the realm of printed circuit boards (PCBs), function as the central hub in computers, skillfully coordinating the harmonious integration of vital components such as the CPU, memory, and peripherals.
Function:Motherboards are designed with the central goal of creating a cohesive platform that seamlessly integrates and interconnects diverse electronic elements, facilitating efficient communication and data transfer throughout the entire system.
Substrate Like PCBs (SLPs):
Structure: SLPs, frequently deployed in mobile devices, bear a structural resemblance to semiconductor substrates rather than traditional PCBs. They boast a sleeker and more compact design.
Function: Engineered for miniaturization, SLPs excel in applications where space constraints are paramount. They provide an efficient platform for integrating components, commonly seen in devices like smartphones and tablets.
High-Density Interconnect (HDI) Substrates:
Structure: HDI substrates, falling under the PCB category, are purpose-built for high-density electronic packaging. Leveraging advanced technologies, they achieve fine-line and high-density interconnections.
Function: HDI substrates find their niche in applications demanding miniaturization, high signal integrity, and reduced electronic noise. They are prevalent in cutting-edge electronic applications, including high-performance computing and telecommunications.
Key Observations:
Material and Design: Semiconductor substrates often adopt materials like silicon, departing from the conventional fiberglass associated with traditional PCBs. Semiconductor substrates prioritize providing a stable foundation for semiconductor components, while traditional PCBs emphasize the intricate connectivity of diverse electronic elements.
Applications: Motherboards form the backbone of computers, SLPs cater to the compact needs of electronic devices, and HDI substrates shine in high-performance and high-density electronic applications.
Size and Thickness: Semiconductor substrates often boast a slender and more compact profile compared to traditional PCBs, aligning seamlessly with the specific requirements of semiconductor devices.
By exploring these distinctions and conducting a comparative analysis across semiconductor substrates, encompassing motherboards, SLPs, and HDI substrates, readers gain a nuanced understanding of the unique characteristics of semiconductor substrates vis-à-vis conventional PCBs.
What are the main structure and production technologies involved in semiconductor substrates?
In the intricate realm of semiconductor technology, the building blocks lie in semiconductor substrates. These substrates, crucial for crafting integrated circuits and electronic devices, follow a unique structure and undergo a sophisticated production journey. Silicon, renowned for its stellar semiconductor properties, takes the lead in this venture. Let’s navigate through the core structural elements and the refined production processes that shape semiconductor substrates:
Structural Elements of Semiconductor Substrates:
Material Mastery:
Silicon, with its exceptional semiconductor prowess, is the undisputed protagonist in semiconductor substrates, prominently showcased through the ubiquitous silicon wafers.
Crystal Precision:
High-caliber semiconductor substrates begin as meticulously grown single crystals of silicon, ensuring a seamless and consistent electronic structure.
Lattice Orientation:
The orientation of the crystal lattice, denoted by facets like (100), (111), and (110), plays a pivotal role, with the (100) orientation emerging as a common choice.
Doping Dynamics:
Controlled doping introduces atoms such as boron or phosphorus strategically, shaping the electrical landscape and creating distinct n-type and p-type regions.
Production Odyssey:
Czochralski (CZ) Crystal Elegance:
CZ crystal growth involves delicately immersing a seed crystal into molten silicon, resulting in a single-crystal ingot that undergoes precise slicing to yield wafers.
Float-Zone (FZ) Symphony:
FZ crystal growth introduces a touch of finesse with a radiofrequency induction coil over a polycrystalline silicon rod. A molten zone traverses the rod, giving rise to a high-quality single crystal.
Wafer Ballet:
Precision takes center stage in wafering, where the single-crystal ingot is artfully sectioned into thin wafers, followed by a polishing dance to achieve a smooth surface.
Oxidation and Epitaxy Performance:
Oxidation processes contribute to the formation of silicon dioxide layers, while epitaxy gracefully adds layers of semiconductor material to the wafer, introducing elements like silicon or gallium arsenide.
Photolithography Artistry:
Photolithography unveils its artistry, employing selective exposure to light through a mask to delineate regions for subsequent semiconductor processes.
Doping Choreography:
Targeted doping enters the stage, strategically introducing dopants to specific wafer regions. Techniques like diffusion or ion implantation perform a choreography of precision.
Deposition Elegance:
Thin films of materials, be it metals or insulators, elegantly grace the wafer surface through techniques like chemical vapor deposition (CVD) or physical vapor deposition (PVD).
Etching Precision:
Unwanted materials are sculpted away with precision through etching processes, shaping the final structure of integrated circuits with an artful touch.
These production methodologies intertwine, giving rise to semiconductor substrates characterized by exacting electrical properties and structures. This serves as the foundation for the intricate tapestry of integrated circuits, embodying the heartbeat of diverse electronic devices.
Frequently Asked Questions (FAQs)
How does a semiconductor substrate dance with electronic devices?
Picture this: a semiconductor substrate as the dance floor, and electronic components as the star performers. What role does the substrate play in ensuring a flawless dance routine among integrated circuits?
Why is precision technology the unsung hero in semiconductor substrate manufacturing?
In the world of substrates, precision is not just a virtue; it’s the guiding star. Uncover the role of precision technology in orchestrating the ballet of crystal growth, wafer slicing, and beyond.
How does the substrate choice become the director in the performance of electronic devices?
Think of it as casting for a blockbuster movie. The choice of substrate is the director’s decision, impacting everything from electrical conductivity to thermal dynamics. How does this casting choice influence the electronic stage?
Can semiconductor substrates get a second act through recycling?
While the journey to reincarnation for semiconductor substrates is challenging, the story of recycling in semiconductor manufacturing does have its own unique twists. What role does sustainability play in this electronic saga?
How do the technological sonatas of semiconductor substrates compose the future of the electronics industry?
In a world where technology is the composer, semiconductor substrates play the notes of innovation. Unravel the symphony of advancements and their impact on diverse industries, from computing to telecommunications.
Conclusion
In conclusion, the intricate world of semiconductor substrates serves as the canvas for the artistic creation of integrated circuits and electronic devices. With silicon often taking the lead role due to its exceptional properties, the substrate manufacturing process is a symphony of precision and innovation.
From the orchestration of crystal growth to the finesse of wafer slicing, semiconductor substrate manufacturing is a journey that combines scientific mastery with artistic flair. The choice of substrate becomes a directorial decision, influencing the electronic performance on the grand stage.
Doping introduces an element of magic, transforming a simple substrate into a semiconductor powerhouse with distinct electrical characteristics. Recycling endeavors may encounter challenges, but sustainability remains an integral part of the ongoing electronic narrative.
As technological advancements compose the overture of the future, semiconductor substrates play the foundational notes, driving innovation across industries. The symphony of electronic progress continues, with semiconductor substrates at the core, shaping the evolution of our interconnected and high-tech world.