Semiconductor Substrate Supplier. High speed and high frequency material packaging substrate manufacturing. Advanced packaging substrate production process and technology.
In practical terms, picture the package substrate as a dynamic platform that provides support to the semiconductor chip housing integrated circuits and facilitates electrical connections to the broader electronic system through intricately embedded traces and vias. The careful selection of materials and the intricacies of package substrate design significantly impact the electrical performance, thermal dynamics, and overall reliability of electronic devices.
The contributions from semiconductor substrate suppliers are crucial. These industry players supply essential materials and cutting-edge technologies for the manufacturing of high-quality package substrates. Their efforts extend to the development of substrates with enhanced electrical properties, superior thermal conductivity, and heightened reliability. A continuous stream of innovations in substrate materials, including advanced organic substrates, laminate substrates, and sophisticated packaging technologies like System-in-Package (SiP) solutions, continually shapes the landscape of electronic device manufacturing.
For a PCB engineer, staying tuned to the latest breakthroughs in package substrates is imperative, providing the key to optimizing electronic device design and performance. Collaboration with esteemed semiconductor substrate suppliers ensures seamless access to state-of-the-art materials and technologies, empowering the creation of electronic products that meet the increasing demands for speed, miniaturization, and energy efficiency in the ever-evolving field of electronics manufacturing.
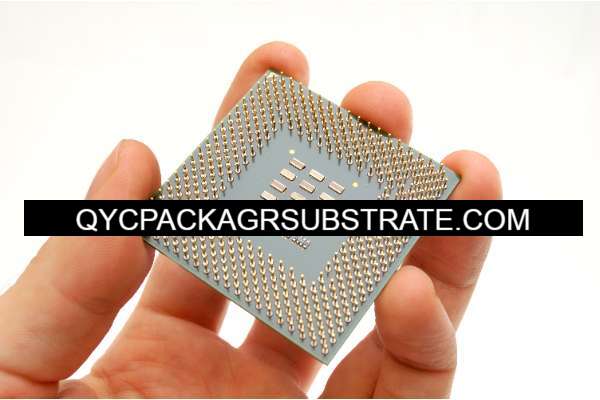
What Functions Does a Package Substrate Serve?
Semiconductor package substrates, sourced from diverse suppliers, are instrumental in sculpting the efficiency and dependability of semiconductor devices through a multifaceted array of functions:
Interconnectivity Nexus: Package substrates assume the crucial role of a bridge, establishing seamless connectivity between the integrated circuit (IC) or chip and the external circuit board components. Within their confines lies an intricate network of conductive traces that facilitate the fluid transmission of electrical signals.
Thermal Harmony Conductor: The effective management of heat is paramount to maintaining the optimal operational temperature of semiconductor devices. Package substrates incorporate tailored materials and design elements that skillfully disperse the heat produced during device operation, proactively preventing overheating and guaranteeing consistent reliability.
Structural Safeguard: Functioning as a sturdy base, package substrates offer indispensable structural reinforcement, safeguarding the semiconductor chip against the impact of mechanical stress, vibrations, and environmental elements. This reinforcement elevates the device’s resilience, mitigating the potential for mechanical failures.
Signal Integrity Custodian: The layout and quality of electrical interconnects on the substrate are pivotal for preserving signal integrity. Meticulously crafted package substrates minimize issues such as signal degradation and crosstalk, ensuring the reliable and swift transmission of data within the device and to external components.
Size Sleuth and Miniaturization Artisan: Package substrates play a pivotal role in advancing the ongoing trend of miniaturization, offering a compact and space-efficient platform for seamlessly integrating chips into smaller, more streamlined designs. This attribute is pivotal in crafting sophisticated and portable electronic devices.
Material Alchemy Artisan: The selection of materials for package substrates involves a meticulous consideration of factors such as thermal conductivity, electrical properties, and reliability under diverse environmental conditions. This material alchemy ensures compatibility with the specific requirements of semiconductor devices.
The intricate interplay of these functions within package substrates profoundly influences the overall performance, reliability, and lifecycle of semiconductor devices. A meticulously crafted substrate guarantees the smooth functioning of the device, not only meeting but surpassing performance benchmarks, and displaying robust resilience in the face of real-world demands. On the flip side, inadequacies in substrate design could lead to challenges in temperature control, breakdowns in electrical systems, or vulnerabilities in structure, putting the quality and reliability of the semiconductor device at risk.
What Are the Different Types of Package Substrates?
Within the semiconductor substrate domain, suppliers offer a varied assortment of package substrates, each intricately designed to address the nuanced requirements of particular applications. Among these, High-Density Interconnect (HDI) substrates and Substrate-like PCBs (SLP) stand out.
High-Density Interconnect (HDI) Substrates:
HDI substrates distinguish themselves with their intricate design catering to high circuit density and precise interconnections. Tailored for applications emphasizing compactness and miniaturization, these substrates feature multiple layers of conductive traces and vias. Their expertise lies in navigating complex signal routing within confined spaces, making them particularly suitable for cutting-edge electronic devices like smartphones, tablets, and high-performance computing systems where spatial optimization and signal integrity are paramount.
Substrate-like PCBs (SLP):
Substrate-like PCBs emulate the characteristics inherent in traditional semiconductor substrates, achieving a delicate equilibrium between high performance and a streamlined form factor. Leveraging advanced materials and manufacturing techniques, SLPs offer a leap in electrical performance and thermal characteristics. Their niche lies in applications demanding a symbiosis of miniaturization and high performance, spanning high-speed communication devices, automotive electronics, and sophisticated medical equipment.
These diverse package substrates cater to an array of application scenarios by deftly addressing specific requisites:
Space Maximization: HDI substrates shine in scenarios where spatial constraints necessitate ingenious design solutions, particularly in the realm of portable and compact devices.
Performance Pinnacle: SLPs are meticulously engineered to satiate the exacting demands of high-performance applications, presenting superior electrical and thermal characteristics.
Intricate Interconnections: Both HDI and SLP substrates seamlessly accommodate complex circuit designs, making them apt for applications with exacting interconnection demands.
Signal Integrity Assurance: The sophisticated design of these substrates guarantees optimal signal integrity, positioning them favorably in applications where the reliable and high-speed transmission of data is a pivotal consideration.
Semiconductor substrate suppliers wield a pivotal role in customizing these substrates to the ever-evolving needs of diverse industries. The solutions they deliver deftly navigate the intricate landscape between size, performance, and reliability, catering to a broad spectrum of electronic devices and applications.
What Role Does a Semiconductor Substrate Supplier Play in IC Packaging?
In the intricate dance of IC packaging, the role undertaken by a supplier of semiconductor substrates is nothing short of crucial. Their significance extends beyond mere contribution; they are the architects crafting varied solutions tailored to the multifaceted demands of integrated circuit packaging.
Semiconductor substrate suppliers bear the responsibility of sculpting the substrates that cradle and weave connections for semiconductor chips within a package. These substrates serve as both the robust skeleton and the intricate neural pathways for the integrated circuit (IC). The supplier’s prowess shines through in their ability to furnish substrates customized for different packaging technologies, navigating the intricacies of advanced packaging methodologies.
The repertoire of offerings from these suppliers spans diverse substrate types, spanning from the organic to the inorganic, intricately designed to align with the specific needs of diverse applications. Factors like thermal management, electrical connectivity, and form factor considerations are woven into the fabric of substrate design. Moreover, semiconductor substrate suppliers stand at the forefront of fashioning specialized substrates, such as High-Density Interconnect (HDI) substrates and Substrate-like PCBs (SLP), strategically addressing the challenges posed by compact designs and high-performance application scenarios.
Beyond the provision of substrates, semiconductor substrate suppliers emerge as catalysts for innovation in packaging technology. Their engagement revolves around the exploration and development of materials and designs that not only uplift electrical performance but also amplify thermal dissipation and fortify the overall reliability of IC packages. These strides are imperative in meeting the ever-shifting demands of industries spanning consumer electronics, telecommunications, automotive, and more.
How Do Package Substrates Differ From PCBs?
Package substrates and traditional Printed Circuit Boards (PCBs) share a common objective as foundations for electronic components, yet they diverge significantly in terms of their structures and functions.
Package Substrates:
Exclusively tailored to house and connect semiconductor devices such as integrated circuits (ICs) or chips, package substrates emerge as specialized boards within electronic packages. Beyond the basic functions inherent in PCBs, package substrates offer a complex support system, ensuring precise electrical connectivity and efficient heat dissipation for the enclosed semiconductor chip. Marked by intricate designs comprising numerous layers of conductive traces, vias, and insulating materials, these substrates are meticulously crafted to align with the unique demands of the semiconductor devices they encapsulate. This customized strategy places significant focus on compact design, ensuring signal reliability, and efficient thermal regulation.
Printed Circuit Boards (PCBs):
On the flip side, PCBs act as the foundational backbone for an extensive array of electronic systems. Their adaptability lies in providing a platform for mounting and connecting various electronic components, including resistors, capacitors, and ICs. Commonly found in electronic devices spanning consumer electronics to industrial applications, PCBs typically exhibit a more straightforward structure compared to the specialized design of package substrates. They are designed with flexibility in mind, accommodating various types of components and connections.
Technological Innovations by Semiconductor Substrate Suppliers:
Leading the charge in technological progression, suppliers of semiconductor substrates drive notable breakthroughs in the realm of electronic manufacturing. Their pioneering efforts span the development of state-of-the-art substrates, exemplified by High-Density Interconnect (HDI) substrates and Substrate-like PCBs (SLP).These substrates not only promise heightened electrical performance but also bring capabilities for miniaturization and enhanced thermal characteristics. Advances in material science, including the integration of advanced dielectric materials and metal alloys, contribute substantially to improving signal integrity and heat dissipation.
Semiconductor substrate suppliers play a pivotal role in collaborative initiatives with electronic manufacturers, continually refining substrates to meet the dynamic demands of contemporary electronics. Their innovative contributions pave the way for more streamlined, efficient, and high-performance electronic devices, fostering progress in electronic manufacturing across diverse industries.
What Are the Main Structure and Production Technologies of Semiconductor Substrate Suppliers?
Semiconductor substrate suppliers employ state-of-the-art manufacturing technologies to craft package substrates that align with the evolving needs of contemporary electronics. Central to their production processes are advanced techniques, including refined High-Density Interconnect (HDI) technology and elevated semi-additive methods.
Key Structure and Production Technologies:
High-Density Interconnect (HDI) Technology: HDI technology stands as a pinnacle of sophistication, utilizing advanced materials and intricate fabrication processes to achieve heightened circuit density and finer feature sizes on package substrates. This capability allows for the integration of increasingly complex and compact designs, responding to the prevalent trend of miniaturization in electronic devices.
Enhanced Semi-Additive Methods: In the realm of semi-additive methods, continuous refinement empowers semiconductor substrate suppliers to selectively introduce thin layers of conductive material, orchestrating the creation of intricate interconnects across multiple substrate layers. This refinement contributes significantly to the overall performance and connectivity of semiconductor devices.
Innovations and Broad Applications:
Miniaturization Mastery: The evolution of HDI fabrication technology facilitates the creation of finer traces and smaller vias, championing the cause of miniaturization in package substrates. This becomes paramount in meeting the spatial constraints inherent in compact electronic devices, including smartphones, wearables, and IoT gadgets.
Performance Prowess: Advanced manufacturing technologies elevate the electrical performance of package substrates, a boon particularly for high-performance applications where considerations of signal integrity, speed, and reliability take center stage.
Thermal Wizardry: The integration of materials with enhanced thermal conductivity, made possible by advanced production methods, addresses the thermal challenges accompanying densely packed electronic components. This becomes instrumental in maintaining optimal operating temperatures, especially in high-performance devices.
Interconnection Intricacy: The utilization of refined semi-additive methods allows for the creation of intricate and precise interconnections among semiconductor components. This aligns seamlessly with the demands of contemporary electronic systems characterized by intricate architectures.
In essence, semiconductor substrate suppliers harness advanced manufacturing technologies, encompassing improved HDI fabrication and refined semi-additive methods, to craft package substrates boasting refined structures. These innovations propel the widespread application of package substrates in compact, high-performance electronic devices, ushering in advancements in realms such as miniaturization, enhanced performance, thermal management, and complex interconnections.
What Are Frequently Asked Questions (FAQs) About Package Substrates?
What challenges are encountered in the manufacturing of package substrates?
Challenges in package substrate manufacturing include achieving higher circuit density, addressing thermal management concerns in compact designs, and ensuring precision in interconnections. Suppliers continually strive to overcome these hurdles to stay abreast of the evolving demands in electronic devices.
Could you provide an overview of Substrate-like PCBs (SLP)?
SLPs emulate the characteristics of traditional semiconductor substrates, offering a delicate balance between high performance and a compact form factor. They integrate advanced materials and manufacturing techniques to enhance electrical performance and thermal characteristics.
How do package substrates contribute to the ongoing trend of electronic device miniaturization?
Through the application of advanced fabrication technologies and strategic material choices, package substrates facilitate the creation of finer traces and smaller vias. This support aligns seamlessly with the prevailing trend of miniaturization observed in electronic devices like smartphones and wearables.
In what ways do semiconductor substrate suppliers foster innovation?
Suppliers lead innovation by harnessing advanced manufacturing technologies, such as improved HDI fabrication and enhanced semi-additive methods. These innovations result in package substrates featuring refined structures to meet the demands of miniaturization and high-performance requirements.