Showa Denko MCL-E-705G package substrate Manufacturer
Showa Denko MCL-E-705G package substrate Manufacturer. the MCL-E-705G core materials for the ABF BGA substrates, the Package Substrate will be made with Showa Denko and Ajinomoto High speed materials.or other types high speed materials and high frequency materials.
Showa Denko MCL-E-705G package substrates represent the pinnacle of semiconductor packaging technology. Engineered with precision and expertise, these substrates offer unparalleled reliability and performance for high-performance electronic devices. Crafted from advanced epoxy resin formulations, MCL-E-705G substrates provide exceptional thermal stability and mechanical strength, ensuring the longevity and durability of semiconductor packages. With high-density interconnects and optimized electrical properties, they enable seamless integration into various semiconductor applications, including CPUs, GPUs, and memory modules. The meticulous fabrication process, combined with rigorous quality control measures, guarantees consistent and superior quality in every substrate produced. Showa Denko’s commitment to innovation and excellence shines through in the MCL-E-705G package substrates, empowering the electronics industry with the foundation for cutting-edge semiconductor technologies.
What is the Showa Denko MCL-E-705G package substrate?
The Showa Denko MCL-E-705G package substrate is a type of material used in the packaging of semiconductor chips. Specifically, it is a build-up film substrate designed to offer high reliability and performance for applications such as CPUs, GPUs, and other high-performance semiconductor devices.
The MCL-E-705G is characterized by several key features:
- Material Composition: It typically consists of advanced epoxy resin materials that are known for their thermal stability and mechanical robustness.
- High-Density Interconnect (HDI): The substrate allows for high-density interconnects, which is crucial for modern, high-performance semiconductor devices that require a large number of connections in a compact area.
- Thermal Management: Effective thermal management properties are crucial for substrates used in high-performance applications, and materials like MCL-E-705G are selected for their ability to handle the heat generated by modern chips.
- Electrical Performance: It offers excellent electrical insulation properties while also facilitating the rapid transmission of electrical signals, which is vital for maintaining the performance of high-speed semiconductor devices.
In the context of the semiconductor manufacturing industry, the choice of substrate material like MCL-E-705G directly impacts the performance, reliability, and overall efficiency of the electronic devices they are used in. The selection of such materials is critical as semiconductors become smaller, faster, and require more efficient heat dissipation and electrical performance.
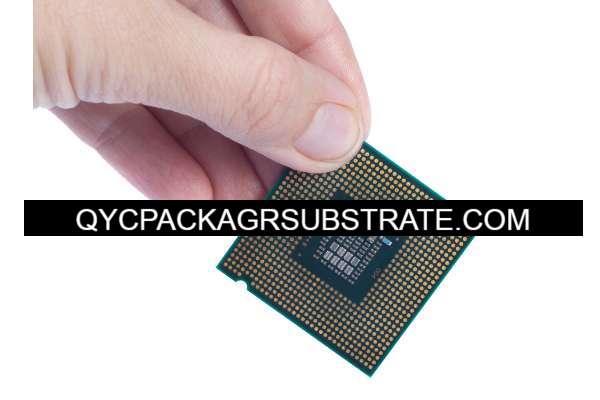
Showa Denko MCL-E-705G package substrate Manufacturer
What are the Showa Denko MCL-E-705G package substrate design guidelines?
The specific design guidelines for the Showa Denko MCL-E-705G package substrate may vary depending on the exact requirements of the application and the semiconductor device being packaged. However, in general, here are some common design guidelines that may apply:
- Layer Stackup: The substrate design should include a suitable layer stackup that meets the electrical and thermal requirements of the semiconductor device. This stackup typically includes signal layers, power distribution layers, and ground planes, with appropriate dielectric materials between them.
- Routing Density and Signal Integrity: The design should consider the routing density required to accommodate all the signal traces while maintaining signal integrity. High-speed signals may require controlled impedance traces and careful routing to minimize signal degradation and electromagnetic interference (EMI).
- Power Distribution and Decoupling: Proper power distribution and decoupling capacitor placement are essential to ensure stable power supply and minimize noise in the system. Decoupling capacitors should be placed close to the power pins of the semiconductor device to effectively filter high-frequency noise.
- Thermal Management: The substrate design should incorporate features for effective thermal management, such as thermal vias, thermal pads, or other heat dissipation techniques. These features help dissipate heat generated by the semiconductor device and prevent overheating, which can degrade performance and reliability.
- Component Placement and Routing: Components should be placed and routed in a way that minimizes signal path lengths, reduces crosstalk, and optimizes signal integrity. Critical components should be placed strategically to minimize parasitic effects and ensure reliable operation.
- Manufacturability and Reliability:The substrate design should take into account manufacturability considerations, such as material compatibility, fabrication process capabilities, and yield optimization. Design features should also enhance the reliability of the substrate, such as avoiding sharp corners and ensuring adequate spacing between features to prevent mechanical stress and potential failures.
- Compliance with Standards: The design should comply with relevant industry standards and specifications, such as those for dimensional tolerances, electrical performance, and reliability testing.
These guidelines are general principles that can help ensure a robust and reliable substrate design using materials like the Showa Denko MCL-E-705G. However, for specific applications, it’s essential to consult with substrate manufacturers and design engineers to tailor the design to the unique requirements of the semiconductor device and its intended use.
What is the Showa Denko MCL-E-705G package substrate fabrication process?
The fabrication process for the Showa Denko MCL-E-705G package substrate typically involves several steps to create a high-quality substrate suitable for use in semiconductor packaging. While the exact process may vary depending on specific requirements and manufacturing facilities, here is a generalized overview of the fabrication process:
- Substrate Material Preparation: The process begins with the preparation of the base substrate material. The MCL-E-705G package substrate material is typically supplied in the form of sheets or rolls. These materials may consist of advanced epoxy resin formulations with additives to enhance thermal and mechanical properties.
- Cleaning and Surface Treatment: The substrate material undergoes thorough cleaning to remove any contaminants that could affect adhesion or processing. Surface treatment processes may also be applied to improve adhesion between layers or facilitate subsequent processing steps.
- Layer Formation: The fabrication process involves building up multiple layers on the substrate material to create the desired circuitry and interconnects. This typically involves applying layers of dielectric material and conductive traces using techniques such as lamination, sputtering, or chemical vapor deposition (CVD).
- Pattern Definition: Photolithography or other patterning techniques are used to define the circuitry and interconnect patterns on the substrate layers. A photoresist material is applied to the substrate, exposed to a patterned light source, and developed to create the desired pattern. This pattern is then transferred to the underlying layers through etching or other material removal processes.
- Via Formation: Vias are small holes drilled or etched through the substrate layers to provide electrical connections between different layers. Laser drilling, mechanical drilling, or chemical etching processes may be used to create vias of various sizes and shapes depending on the design requirements.
- Metallization: After via formation, metallization processes are used to deposit conductive materials (typically copper) within the vias and on the surface of the substrate layers. These metal layers provide electrical connections between different circuit elements and facilitate signal transmission.
- Surface Finish: Surface finish processes are applied to the substrate to improve solderability and protect against oxidation. Common surface finishes include electroless nickel immersion gold (ENIG), solder mask application, and surface planarization techniques.
- Quality Control and Testing: Throughout the fabrication process, quality control measures are implemented to ensure the substrate meets specified requirements for dimensional accuracy, electrical performance, and reliability. Testing may include visual inspection, electrical testing, thermal cycling, and other reliability tests.
- Final Processing: After fabrication and testing, the substrate may undergo additional processing steps such as singulation (cutting into individual units), packaging, and labeling before being shipped to customers.
Overall, the fabrication process for the Showa Denko MCL-E-705G package substrate involves a combination of material deposition, patterning, metallization, and quality control steps to produce a high-performance substrate suitable for use in semiconductor packaging applications.
How do you manufacture a Showa Denko MCL-E-705G package substrate?
As of my last update in January 2022, detailed information on the specific manufacturing process for the Showa Denko MCL-E-705G package substrate was not readily available in the public domain. However, I can provide a generalized overview of the typical processes involved in manufacturing package substrates like the MCL-E-705G.
- Substrate Material Selection: The manufacturing process starts with the selection of suitable substrate materials. For the MCL-E-705G, this typically involves advanced epoxy resin formulations known for their thermal stability and mechanical strength.
- Substrate Preparation: The selected substrate materials are prepared in the desired form, typically as sheets or rolls, and undergo cleaning and surface treatment processes to remove contaminants and improve surface properties.
- Layer Formation: Multiple layers are built up on the substrate material to create the necessary circuitry and interconnects. This may involve processes such as lamination, sputtering, or chemical vapor deposition to deposit dielectric and conductive layers.
- Pattern Definition: Photolithography or other patterning techniques are used to define the circuitry and interconnect patterns on the substrate layers. Photoresist materials are applied, exposed to patterned light, and developed to create the desired patterns.
- Via Formation: Vias are created to provide electrical connections between different layers of the substrate. This can be achieved through processes such as laser drilling, mechanical drilling, or chemical etching to create holes in the substrate material.
- Metallization: Metallization processes are used to deposit conductive materials (typically copper) within the vias and on the surface of the substrate layers. This facilitates electrical connections between different circuit elements and improves signal transmission.
- Surface Finish: Surface finish processes are applied to the substrate to improve solderability and protect against oxidation. Common surface finishes include electroless nickel immersion gold (ENIG) and solder mask application.
- Quality Control and Testing: Throughout the manufacturing process, quality control measures are implemented to ensure the substrate meets specified requirements for dimensional accuracy, electrical performance, and reliability. This may involve visual inspection, electrical testing, thermal cycling, and other reliability tests.
- Final Processing: After manufacturing and testing, the substrate may undergo additional processing steps such as singulation (cutting into individual units), packaging, and labeling before being shipped to customers.
It’s important to note that the specific manufacturing process for the MCL-E-705G package substrate may involve proprietary techniques and equipment unique to Showa Denko. For detailed information on the manufacturing process, it would be best to consult directly with Showa Denko or refer to their technical documentation if available.
How much should a Showa Denko MCL-E-705G package substrate cost?
The cost of a Showa Denko MCL-E-705G package substrate can vary based on several factors, including the size of the substrate, its complexity, the quantity ordered, and market conditions. Unfortunately, without specific pricing data available, it’s challenging to provide an exact cost. However, I can offer some general considerations that may influence the pricing:
- Size and Thickness: Larger substrates typically require more material and may incur higher manufacturing costs. Additionally, thicker substrates may require more processing steps and materials, contributing to higher costs.
- Material Composition:The materials used in the MCL-E-705G substrate, including advanced epoxy resins and conductive metals like copper, can affect the overall cost. High-quality materials with enhanced thermal and electrical properties may command higher prices.
- Manufacturing Complexity: Substrates with intricate designs, high-density interconnects, or specialized features may require more advanced manufacturing processes, leading to increased costs.
- Volume and Ordering Quantity: Larger orders typically benefit from economies of scale, resulting in lower per-unit costs. Showa Denko or their distributors may offer pricing discounts for bulk orders or long-term contracts.
- Customization and Additional Services: If customization or additional services such as surface finishing or testing are required, they may incur additional costs.
- Market Demand and Competition: Market demand and competitive factors can influence pricing. Prices may fluctuate based on supply and demand dynamics, industry trends, and competition from other substrate manufacturers.
- Value-added Features: Substrates with value-added features such as enhanced thermal management capabilities, advanced signal integrity designs, or reliability enhancements may command higher prices due to their increased functionality and performance.
- Geographic Location: Manufacturing and shipping costs can vary depending on the geographic location of the production facilities and the final destination of the substrates.
To obtain specific pricing information for the Showa Denko MCL-E-705G package substrate, it’s best to contact Showa Denko directly or reach out to their authorized distributors. They can provide accurate pricing based on your specific requirements and ordering volume. Additionally, requesting quotes from multiple suppliers can help compare costs and ensure competitive pricing.
What is the Showa Denko MCL-E-705G package substrate base material?
The base material of the Showa Denko MCL-E-705G package substrate is typically composed of advanced epoxy resin formulations. Epoxy resins are widely used in the electronics industry for their excellent electrical insulation properties, mechanical strength, and thermal stability. These resins are often reinforced with additives to enhance specific characteristics such as thermal conductivity or dimensional stability.
Showa Denko, as a leading manufacturer of electronic materials, likely formulates the base material of the MCL-E-705G substrate to meet the demanding requirements of semiconductor packaging applications. This may involve selecting epoxy resins with precise properties tailored to achieve high reliability, thermal performance, and electrical insulation in the final product.
The exact composition and formulation of the base material may be proprietary to Showa Denko, designed through extensive research and development to meet the stringent performance standards of the semiconductor industry. For specific technical details on the base material composition of the MCL-E-705G substrate, consulting Showa Denko’s technical documentation or contacting their technical support team would provide the most accurate information.
Which company manufactures Showa Denko MCL-E-705G package substrates?
The Showa Denko MCL-E-705G package substrates are manufactured by Showa Denko, a Japanese company. As a renowned manufacturer of electronic materials, Showa Denko specializes in providing high-performance, high-reliability package substrates to meet the demands of the semiconductor industry. They possess profound expertise in materials science and engineering, enabling them to develop advanced substrate materials that meet the requirements of high-performance semiconductor packaging.
As for our company, we also have the capability to produce Showa Denko MCL-E-705G package substrates. With advanced production equipment and a skilled technical team, we can customize various package substrate products according to customer requirements. We prioritize quality control, employing stringent production processes and quality management systems to ensure the production of high-quality, reliable package substrate products.
Our company’s production capacity and experience enable us to meet various customer needs and provide customized solutions. Whether it’s product quality, delivery time, or after-sales service, we are committed to providing the best experience for our customers. By closely collaborating with customers, we can jointly drive product innovation, enhance market competitiveness, and achieve mutual development.
In summary, our company has the capability to produce Showa Denko MCL-E-705G package substrates and is dedicated to providing customers with high-quality products and services to meet their needs and achieve mutual development.
What are the 7 qualities of good customer service?
Good customer service is essential for building and maintaining positive relationships with customers. Here are seven qualities that contribute to providing exceptional customer service:
- Empathy: Empathy involves understanding and sharing the feelings of customers. It’s essential to listen actively to their concerns, acknowledge their emotions, and demonstrate genuine care and concern for their needs.
- Communication Skills: Effective communication is crucial in customer service. This includes clear and concise verbal communication, active listening, and the ability to convey information in a friendly and professional manner. Good communication helps ensure that customers feel understood and informed throughout their interactions.
- Patience: Patience is key when dealing with customers, especially in challenging situations or when resolving complex issues. Customer service representatives should remain calm, composed, and patient, even when faced with frustrated or irate customers. Taking the time to address concerns thoroughly can help build trust and satisfaction.
- Problem-Solving Skills: Good customer service involves the ability to identify and resolve customer issues efficiently and effectively. This requires strong problem-solving skills, including the ability to analyze situations, think critically, and offer practical solutions that meet customer needs.
- Product Knowledge: Having a thorough understanding of the products or services being offered is essential for providing quality customer service. Customer service representatives should be knowledgeable about product features, specifications, and usage guidelines, enabling them to answer questions accurately and help customers make informed decisions.
- Professionalism: Professionalism encompasses maintaining a positive attitude, remaining courteous and respectful at all times, and adhering to company policies and procedures. Demonstrating professionalism fosters trust and confidence in customers and reflects positively on the organization as a whole.
- Adaptability: Customer service situations can vary widely, and it’s important to be adaptable and flexible in responding to diverse customer needs and preferences. Being able to adjust communication styles, problem-solving approaches, and service delivery methods based on individual customer interactions contributes to a positive customer experience.
By embodying these qualities, organizations can deliver exceptional customer service that exceeds expectations, fosters customer loyalty, and contributes to long-term success.
FAQs
What is Showa Denko MCL-E-705G package substrate?
Showa Denko MCL-E-705G is a type of package substrate used in semiconductor packaging. It is designed to provide high reliability and performance for various semiconductor devices.
What are the key features of MCL-E-705G package substrates?
MCL-E-705G substrates typically offer high-density interconnects, excellent thermal management properties, and reliable electrical performance. They are designed to meet the demanding requirements of modern semiconductor devices.
What applications are suitable for MCL-E-705G package substrates?
MCL-E-705G substrates are commonly used in high-performance semiconductor devices such as CPUs, GPUs, memory modules, and other advanced electronic components.
What materials are used in the manufacturing of MCL-E-705G package substrates?
MCL-E-705G substrates are typically made from advanced epoxy resin formulations, which are chosen for their thermal stability, mechanical strength, and electrical insulation properties.
What are the design guidelines for using MCL-E-705G package substrates?
Design guidelines may include considerations such as layer stackup, routing density, thermal management, power distribution, and compliance with industry standards.
How is MCL-E-705G package substrate fabricated?
The fabrication process typically involves steps such as substrate material preparation, layer formation, pattern definition, via formation, metallization, surface finish, quality control, and final processing.
Where can I purchase MCL-E-705G package substrates?
MCL-E-705G substrates are available through authorized distributors of Showa Denko products. Customers can contact Showa Denko or their distributors for inquiries and purchases.
What are the benefits of using MCL-E-705G package substrates?
Benefits may include enhanced reliability, improved thermal performance, optimized electrical properties, and compatibility with advanced semiconductor packaging technologies.