Showa Denko Substrate Manufacturer
Showa Denko Substrate Manufacturer.High speed and high frequency material packaging substrate Manufacturer. Advanced packaging substrate production process and technology
Showa Denko Substrate (SDS) is a high-quality aluminum-magnesium alloy substrate used in the manufacturing of hard disk drives (HDDs). These substrates provide a stable and flat surface for the deposition of magnetic layers, which is essential for storing and accessing data in HDDs. As a product of Showa Denko, SDS is renowned for its exceptional quality and reliability, serving as a critical component for HDD manufacturers. The manufacturing process of SDS undergoes rigorous quality control to ensure compliance with various technical specifications and performance requirements. These substrates feature high rigidity, excellent dimensional stability, and surface smoothness, catering to the diverse needs of different HDD designs and applications. By opting for SDS, manufacturers can ensure their products deliver outstanding performance and reliability, providing durable data storage solutions for various applications.
What is a Showa Denko Substrate (SDS)?
A Showa Denko Substrate (SDS) is a type of substrate used in the production of hard disk drives (HDDs). Substrates are the base materials onto which data storage components are built, and they play a crucial role in the performance and reliability of HDDs. Showa Denko Co., Ltd. (SDK), a Japanese chemical company, is known for manufacturing these substrates.
The SDS is typically made from a material called aluminum-magnesium alloy, which offers high rigidity and stability necessary for the delicate components of HDDs. These substrates provide a flat and smooth surface for the deposition of magnetic layers, allowing for precise positioning and reading of data on the disk.
The quality of the substrate directly impacts the overall performance and longevity of the HDD. Showa Denko Substrates are known for their high quality, durability, and precision, making them a preferred choice for many HDD manufacturers. Their stability and reliability contribute to the consistent performance of HDDs in various applications, from personal computers to enterprise-level storage systems.
In addition to aluminum-magnesium alloy substrates, Showa Denko also manufactures other types of substrates tailored to specific HDD designs and requirements, ensuring compatibility and optimal performance across different applications and environments.
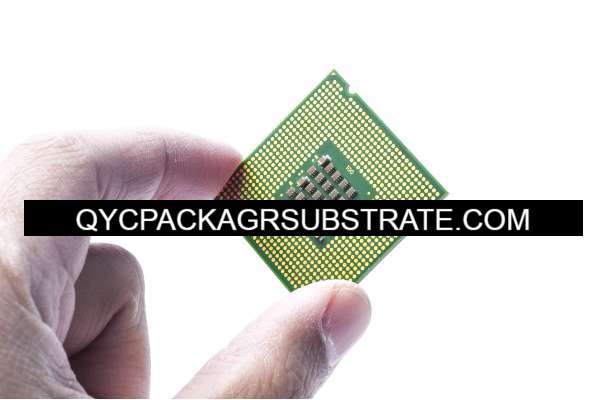
Showa Denko Substrate Manufacturer
What are the Showa Denko Substrate (SDS) Design Guidelines?
Showa Denko provides design guidelines for their substrates to ensure optimal performance and compatibility with hard disk drive (HDD) manufacturing processes. While specific guidelines may vary depending on the exact product and application, some common design principles include:
- Material Specifications: Showa Denko typically specifies the material composition and properties of their substrates, such as aluminum-magnesium alloy grades, thickness, and surface finish requirements.
- Dimensional Tolerances: Precise dimensional tolerances are crucial for compatibility with HDD assembly processes. Showa Denko provides guidelines for substrate thickness, flatness, and overall dimensions to ensure proper fit and alignment within the HDD.
- Surface Smoothness: The substrate’s surface smoothness is essential for uniform deposition of magnetic layers and reliable data reading and writing. Showa Denko specifies surface roughness requirements to achieve optimal performance.
- Edge Profile: The edges of the substrate should be smooth and free from burrs or defects to prevent damage to delicate HDD components during assembly and operation.
- Surface Treatment: Showa Denko may recommend specific surface treatments or coatings to enhance the substrate’s performance, such as chemical treatments to improve adhesion or corrosion resistance.
- Compatibility with Manufacturing Processes: The substrate design should facilitate seamless integration into HDD manufacturing processes, including handling, machining, and assembly steps.
- Thermal Stability: Thermal stability is critical to prevent warping or deformation of the substrate under operating conditions. Showa Denko may specify thermal properties and recommend design features to ensure stability over a range of temperatures.
- Electrical Properties: Substrate materials should exhibit suitable electrical properties to minimize signal interference and ensure reliable data transmission within the HDD.
These design guidelines help HDD manufacturers achieve consistent performance and reliability while using Showa Denko substrates in their products. Adhering to these recommendations ensures compatibility with manufacturing processes and enables the production of high-quality hard disk drives for various applications.
What is the Showa Denko Substrate (SDS) Fabrication Process?
The fabrication process for Showa Denko Substrates (SDS) involves several steps to produce high-quality aluminum-magnesium alloy substrates suitable for use in hard disk drives (HDDs). While specific details may vary depending on the exact product specifications and manufacturing facilities, the general process typically includes the following steps:
- Raw Material Preparation: The fabrication process begins with the selection and preparation of raw materials. Aluminum and magnesium alloys are commonly used for SDS production due to their desirable mechanical and thermal properties.
- Melting and Casting: The raw materials are melted in a furnace to form a homogeneous alloy mixture. The molten alloy is then cast into ingots or billets of specific dimensions using casting techniques such as continuous casting or direct chill casting.
- Hot Rolling: The cast ingots or billets are hot rolled to reduce their thickness and improve their mechanical properties. Hot rolling involves passing the material through a series of rolling mills at elevated temperatures to achieve the desired thickness and shape.
- Cold Rolling: After hot rolling, the material undergoes cold rolling to further reduce its thickness and improve its surface finish. Cold rolling involves passing the material through a series of rollers at room temperature to achieve precise dimensional tolerances and surface smoothness.
- Annealing: Cold-rolled substrates may undergo annealing to relieve internal stresses and improve their mechanical properties. Annealing involves heating the material to high temperatures and then slowly cooling it to achieve the desired microstructure and mechanical properties.
- Surface Treatment: The substrates may undergo surface treatments to enhance their properties, such as chemical cleaning to remove surface contaminants or coatings to improve corrosion resistance and adhesion.
- Cutting and Shaping: The processed substrates are cut and shaped to the final dimensions required for HDD assembly. Precision cutting techniques such as shearing or laser cutting are used to achieve the desired size and shape.
- Quality Control:Throughout the fabrication process, stringent quality control measures are implemented to ensure that the substrates meet the required specifications and quality standards. This may involve inspection of dimensional accuracy, surface finish, mechanical properties, and chemical composition.
- Packaging and Shipping: Once the substrates pass quality control checks, they are packaged and shipped to HDD manufacturers for further assembly and integration into hard disk drives.
By following these fabrication steps and adhering to strict quality control measures, Showa Denko produces high-quality substrates that meet the demanding requirements of HDD manufacturing processes and contribute to the performance and reliability of hard disk drives.
How do you manufacture Showa Denko Substrate (SDS)?
While the specific details of Showa Denko’s substrate manufacturing process may be proprietary, I can outline a general overview of the typical steps involved in manufacturing aluminum-magnesium alloy substrates for hard disk drives (HDDs):
- Raw Material Selection and Preparation: Showa Denko would start by selecting high-quality raw materials, typically aluminum and magnesium alloys, which meet the required specifications for the substrate. These materials may come in the form of ingots, billets, or coils, depending on the manufacturing process.
- Melting and Alloying: The selected raw materials are melted in a furnace at controlled temperatures to form a homogeneous alloy mixture. The alloy composition is precisely controlled to achieve the desired mechanical and thermal properties.
- Casting or Continuous Casting: The molten alloy is then cast into ingots or billets using casting techniques such as direct chill casting or continuous casting. This step forms the initial shape of the substrate material.
- Hot Rolling: The cast ingots or billets are hot rolled at elevated temperatures to reduce their thickness and improve their mechanical properties. Hot rolling involves passing the material through a series of rolling mills to achieve the desired thickness and shape.
- Cold Rolling: After hot rolling, the material undergoes cold rolling at room temperature to further reduce its thickness and improve its surface finish. Cold rolling helps to achieve precise dimensional tolerances and surface smoothness required for HDD substrates.
- Annealing: Cold-rolled substrates may undergo annealing to relieve internal stresses and improve their mechanical properties. Annealing involves heating the material to high temperatures and then slowly cooling it to achieve the desired microstructure and mechanical properties.
- Surface Treatment:The substrates may undergo surface treatments to enhance their properties, such as chemical cleaning to remove surface contaminants or coatings to improve corrosion resistance and adhesion.
- Cutting and Shaping: The processed substrates are cut and shaped to the final dimensions required for HDD assembly. Precision cutting techniques such as shearing, laser cutting, or machining may be used to achieve the desired size and shape.
- Quality Control: Throughout the manufacturing process, stringent quality control measures are implemented to ensure that the substrates meet the required specifications and quality standards. This may involve inspection of dimensional accuracy, surface finish, mechanical properties, and chemical composition.
- Packaging and Shipping: Once the substrates pass quality control checks, they are packaged and shipped to HDD manufacturers for further assembly and integration into hard disk drives.
By following these manufacturing steps and adhering to strict quality control measures, Showa Denko produces high-quality substrates that meet the demanding requirements of HDD manufacturing processes and contribute to the performance and reliability of hard disk drives.
How much should Showa Denko Substrate (SDS) cost?
The cost of Showa Denko Substrates (SDS) can vary depending on several factors, including the specific product specifications, volume of purchase, market demand, and prevailing economic conditions. Since I don’t have access to real-time pricing information, I can’t provide an exact figure.
However, typically, the cost of SDS would be influenced by:
- Material Cost: The cost of raw materials, such as aluminum and magnesium alloys, which are used in the production of the substrate.
- Manufacturing Process: The complexity of the manufacturing process, including melting, casting, rolling, annealing, surface treatment, cutting, and quality control, can impact the overall cost.
- Quality and Performance: Higher quality substrates with superior mechanical properties, surface finish, and dimensional accuracy may command a premium price.
- Market Competition: Pricing may also be influenced by market dynamics and competition from other substrate manufacturers.
- Volume Discounts:Larger orders or long-term contracts may be eligible for volume discounts or special pricing arrangements.
- Currency Exchange Rates: For international transactions, fluctuations in currency exchange rates can affect the final cost of the substrate.
For accurate pricing information, it’s best to directly contact Showa Denko or their authorized distributors to inquire about current pricing and availability based on your specific requirements and order volume.
What is Showa Denko Substrate (SDS) base material?
The base material for Showa Denko Substrates (SDS) is typically an aluminum-magnesium alloy. This alloy is specifically chosen for its combination of properties that are well-suited for the demanding requirements of hard disk drive (HDD) substrates.
Aluminum-magnesium alloys offer several advantages, including:
- Lightweight: Aluminum is inherently lightweight, which is beneficial for HDD applications where minimizing weight can be advantageous for portable devices or reducing energy consumption in data centers.
- High Strength: The addition of magnesium to aluminum enhances its strength and rigidity, allowing the substrate to withstand mechanical stresses encountered during HDD operation, handling, and assembly.
- Excellent Machinability: Aluminum-magnesium alloys are relatively easy to machine, allowing for precise cutting and shaping of the substrate to meet HDD design specifications.
- Good Thermal Conductivity: Aluminum has excellent thermal conductivity, which helps dissipate heat generated during HDD operation, contributing to the overall reliability and longevity of the drive.
- Corrosion Resistance: Aluminum naturally forms a protective oxide layer on its surface, providing corrosion resistance in various environmental conditions, which is crucial for the durability of HDD substrates.
By using aluminum-magnesium alloys as the base material for SDS, Showa Denko can produce substrates that meet the stringent requirements of HDD manufacturers in terms of mechanical properties, dimensional accuracy, surface finish, and reliability. These substrates play a critical role in the performance and longevity of HDDs in various applications, from personal computers to enterprise-level storage systems.
Which company manufactures Showa Denko Substrate (SDS)?
Showa Denko Substrate (SDS) is produced by Showa Denko Co., Ltd. of Japan. Our company is an enterprise specializing in material processing and manufacturing, with advanced production equipment and technical teams that can produce high-quality SDS that meets customer needs.
Our production process includes the following key steps:
- Raw material procurement and preparation:We select high-quality aluminum-magnesium alloy as the basic material of SDS. These raw materials must meet strict quality standards and technical requirements.
- Material processing:Under our advanced production equipment, raw materials go through process steps such as smelting, casting and rolling to form SDS motherboards that meet specifications.
- Surface treatment: We perform surface treatment on SDS, including cleaning, polishing and coating processes to ensure that its surface is flat, smooth and has good corrosion resistance.
- Cutting and processing:According to customer needs and design requirements, we precisely cut and process SDS to ensure that its size and shape meet the requirements.
- Quality inspection:During the production process, we strictly implement quality control measures and conduct quality inspection and testing on each batch of SDS to ensure that it meets product standards and customer requirements.
Through the above production process and strict quality control measures, we can produce high-quality, reliable SDS to meet customer needs in the field of hard disk drive manufacturing. Our goal is to provide customers with high-quality products and services and grow together with them.
What are the 7 qualities of good customer service?
Good customer service is characterized by several key qualities that contribute to positive customer experiences and satisfaction. Here are seven essential qualities:
- Responsiveness: Customers appreciate prompt responses to their inquiries, whether it’s answering questions, addressing concerns, or providing assistance. Being responsive demonstrates that the company values their time and is committed to meeting their needs in a timely manner.
- Empathy: Empathy involves understanding and empathizing with the customer’s perspective and emotions. Customer service representatives who demonstrate empathy show genuine concern for the customer’s situation and are more likely to provide personalized solutions that meet their specific needs.
- Clear Communication: Effective communication is crucial for ensuring that customers understand the information provided and the actions being taken to address their concerns. Clear and concise communication helps avoid misunderstandings and builds trust between the customer and the company.
- Knowledgeability: Customers expect customer service representatives to have a thorough understanding of the products or services offered by the company. Knowledgeable representatives can provide accurate information, offer helpful recommendations, and resolve issues more effectively, instilling confidence in the customer’s decision to do business with the company.
- Problem-Solving Skills: Good customer service involves being proactive in identifying and resolving customer issues. Customer service representatives with strong problem-solving skills can quickly assess situations, identify root causes, and implement effective solutions to address customer concerns, ultimately enhancing the overall customer experience.
- Professionalism: Professionalism encompasses qualities such as courtesy, respect, and integrity in interactions with customers. Customer service representatives who conduct themselves professionally convey a positive image of the company and help foster trust and credibility with customers.
- Follow-Up and Follow-Through: Following up with customers after resolving their issues or inquiries demonstrates a commitment to their satisfaction and reinforces the company’s dedication to customer service. Additionally, following through on promises or commitments made during interactions with customers helps build credibility and strengthens the customer-company relationship.
By embodying these qualities, companies can deliver exceptional customer service experiences that not only meet but exceed customer expectations, leading to increased customer loyalty and advocacy.
FAQs
What are Showa Denko Substrates (SDS)?
Showa Denko Substrates (SDS) are high-quality aluminum-magnesium alloy substrates used in the production of hard disk drives (HDDs). These substrates provide a stable and flat surface for the deposition of magnetic layers, essential for storing and accessing data in HDDs.
What are the advantages of using SDS in HDD manufacturing?
SDS offer several advantages, including high rigidity, excellent dimensional stability, precise surface finish, and compatibility with HDD manufacturing processes. These qualities contribute to the performance, reliability, and longevity of HDDs.
What are the different types of SDS offered by Showa Denko?
Showa Denko offers a range of SDS products tailored to meet the specific requirements of HDD manufacturers. These products may vary in terms of material composition, thickness, surface finish, and other properties to suit different HDD designs and applications.
How are SDS manufactured?
The manufacturing process for SDS typically involves steps such as melting and alloying of raw materials, casting, hot and cold rolling, annealing, surface treatment, cutting, and quality control. Showa Denko follows stringent quality standards to ensure that SDS meet the required specifications and performance criteria.
What are the key considerations when selecting SDS for HDD production?
When selecting SDS for HDD production, factors such as substrate material properties, dimensional tolerances, surface finish, thermal stability, and compatibility with manufacturing processes should be taken into account to ensure optimal performance and reliability of the HDD.
Where can I purchase Showa Denko Substrates (SDS)?
Showa Denko Substrates are typically available through authorized distributors or directly from Showa Denko. Interested customers can inquire about purchasing options and request additional information about SDS products and specifications.
What quality assurance measures are in place for SDS?
Showa Denko implements stringent quality assurance measures throughout the manufacturing process to ensure that SDS meet the required standards and specifications. This includes comprehensive testing and inspection of dimensional accuracy, surface finish, mechanical properties, and chemical composition.
How can I get technical support or assistance with SDS products?
Showa Denko provides technical support and assistance to customers regarding SDS products. Customers can contact Showa Denko directly or reach out to authorized distributors for inquiries, product information, technical assistance, and support related to SDS.