Step Cavity Package Substrate Manufacturer
We are a professional Step Cavity Package Substrate Manufacturer, we mainly produce ultra-small bump pitch substrate, ultra-small trace and spacing packaging substrate and PCBs.
Step Cavity Package Substrates (SCPS) are innovative solutions in semiconductor packaging, revolutionizing the integration of semiconductor dies within electronic devices. These substrates feature precisely engineered recessed cavities that cradle semiconductor chips, allowing for efficient use of space and improved thermal management. By embedding the die within the substrate, SCPS reduce the overall height profile of packaged components, making them ideal for compact electronic systems where space is at a premium. Moreover, SCPS designs integrate advanced thermal management features such as thermal vias and heat spreaders, enhancing heat dissipation and ensuring optimal performance even in demanding environments. With their ability to minimize parasitic inductance and capacitance, SCPS also contribute to enhanced electrical performance and signal integrity. Whether in consumer electronics, automotive applications, or industrial systems, SCPS offer a versatile and reliable solution, addressing the evolving needs of the semiconductor industry with ingenuity and precision.
What is a Step Cavity Package Substrate (SCPS)?
A Step Cavity Package Substrate (SCPS) is a type of substrate used in semiconductor packaging that provides a cavity or recessed area to accommodate a semiconductor die or chip. The SCPS design involves creating a step or recess within the substrate, which allows the die to be mounted inside the substrate rather than on top of it. This design offers several advantages over traditional packaging methods:
- Reduced Height Profile: By embedding the die within the substrate, the overall height of the packaged component is reduced compared to traditional surface-mounted packages. This can be particularly beneficial in applications where space constraints are a concern, such as in mobile devices or compact electronic systems.
- Improved Thermal Performance: SCPS designs often incorporate features such as thermal vias or heat spreaders within the substrate to enhance thermal dissipation. By integrating the die closer to the substrate’s thermal management features, heat can be more efficiently conducted away from the semiconductor, improving overall thermal performance and reliability.
- Enhanced Electrical Performance: Embedding the die within the substrate can also reduce parasitic inductance and capacitance, leading to improved electrical performance and signal integrity. This can be especially important in high-frequency applications where signal integrity is critical.
- Mechanical Stability: The step cavity design can provide mechanical stability and protection for the embedded die, reducing the risk of damage from mechanical shock or vibration. Additionally, the substrate material can be chosen for its mechanical properties to further enhance robustness.
- Integration of Passive Components: SCPS designs may allow for the integration of passive components, such as capacitors or resistors, within the substrate itself. This integration can further reduce the overall footprint of the packaged component and simplify the assembly process.
Overall, Step Cavity Package Substrates offer a compelling solution for semiconductor packaging, combining reduced height, improved thermal and electrical performance, mechanical stability, and potential integration of passive components. These advantages make SCPS an attractive option for a wide range of electronic applications, from consumer electronics to automotive and industrial systems.
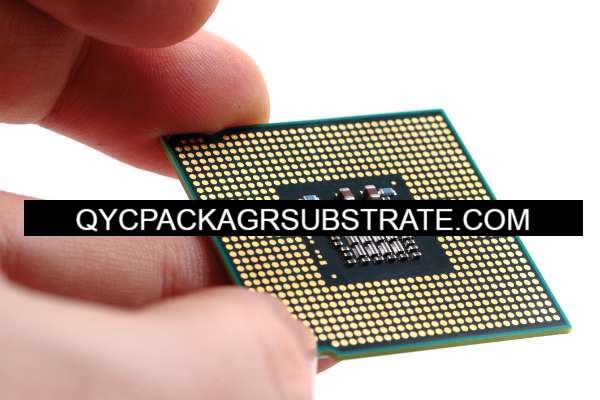
Step Cavity Package Substrate Manufacturer
What are the Step Cavity Package Substrate (SCPS) Design Guidelines?
Designing a Step Cavity Package Substrate (SCPS) involves several guidelines to ensure optimal performance, reliability, and manufacturability. While specific guidelines may vary depending on the application and manufacturing process, here are some general design considerations:
- Die Size and Placement: Determine the size and placement of the semiconductor die within the cavity. Consider factors such as electrical connectivity, thermal management, and signal integrity when positioning the die within the substrate.
- Cavity Dimensions: Design the cavity dimensions to accommodate the semiconductor die and any necessary clearance for wire bonding or other interconnect methods. Ensure that the cavity depth, width, and length are sufficient to house the die and any required passive components.
- Substrate Material Selection: Choose a substrate material with suitable thermal conductivity, mechanical strength, and electrical properties. Common substrate materials for SCPS include ceramics (such as alumina or aluminum nitride) and organic laminates (such as FR-4 or BT epoxy).
- Thermal Management Features: Integrate thermal management features such as thermal vias, heat spreaders, or metal layers into the substrate design to enhance heat dissipation from the semiconductor die. Optimize the placement and distribution of these features to maximize thermal performance.
- Interconnect Design: Design interconnects such as wire bonds, solder bumps, or flip-chip connections to establish electrical connections between the semiconductor die and external circuitry. Ensure that the interconnect design minimizes parasitic resistance, inductance, and capacitance to maintain signal integrity.
- Signal Integrity Considerations: Minimize signal degradation by carefully routing signal traces and minimizing signal path lengths. Use signal integrity simulation tools to analyze and optimize signal routing for high-speed and high-frequency applications.
- Assembly and Packaging Constraints: Consider assembly and packaging constraints such as soldering processes, component placement accuracy, and handling during manufacturing. Design the substrate layout to facilitate automated assembly and testing processes.
- Reliability and Durability: Ensure the SCPS design meets reliability and durability requirements for the intended application. Consider factors such as mechanical stress, thermal cycling, and environmental conditions (e.g., temperature, humidity) that may affect the long-term performance of the packaged device.
- Electromagnetic Compatibility (EMC): Mitigate electromagnetic interference (EMI) and ensure EMC compliance by incorporating shielding, ground planes, and signal isolation techniques into the substrate design.
- Design for Manufacturing (DFM): Collaborate with manufacturing partners early in the design process to optimize the SCPS design for manufacturability. Consider factors such as material availability, fabrication processes, and cost-effectiveness to streamline production.
By following these SCPS design guidelines, engineers can develop substrates that meet performance requirements, ensure reliability, and facilitate efficient manufacturing processes.
What is the Step Cavity Package Substrate (SCPS) Fabrication Process?
The fabrication process for Step Cavity Package Substrates (SCPS) typically involves several steps to create the cavity, integrate thermal management features, and assemble the semiconductor die and other components. Here’s an overview of the typical SCPS fabrication process:
- Substrate Preparation: The process begins with the preparation of the substrate material, which can be ceramic (e.g., alumina, aluminum nitride) or organic laminate (e.g., FR-4, BT epoxy). The substrate is typically in the form of a flat sheet or panel.
- Cavity Formation: Using machining or etching techniques such as laser ablation, milling, or chemical etching, a cavity or recessed area is created in the substrate to accommodate the semiconductor die. The dimensions of the cavity are carefully controlled to ensure proper fit and alignment of the die.
- Thermal Management Features: Thermal management features such as thermal vias, heat spreaders, or metal layers are integrated into the substrate design to enhance heat dissipation from the semiconductor die. These features may be fabricated using processes such as laser drilling, sputtering, or plating.
- Surface Preparation: The surface of the substrate is prepared for die attachment and wire bonding. This may involve cleaning and roughening the surface to improve adhesion and bond strength.
- Die Attachment: The semiconductor die is attached to the bottom of the cavity using die attach adhesive or solder. Precision alignment is critical to ensure proper electrical connectivity and thermal conduction between the die and the substrate.
- Wire Bonding or Flip-Chip Assembly: Interconnects such as wire bonds or flip-chip connections are formed between the semiconductor die and the substrate to establish electrical connections. Wire bonding involves bonding thin wires from the die to bond pads on the substrate using ultrasonic or thermocompression bonding techniques. In flip-chip assembly, solder bumps on the die are aligned and bonded directly to corresponding pads on the substrate.
- Integration of Passive Components: If required, passive components such as capacitors or resistors may be integrated into the substrate design. These components can be mounted within the cavity or on the substrate surface using standard assembly techniques.
- Encapsulation:The assembled substrate, including the semiconductor die and any integrated components, may be encapsulated with a protective material such as epoxy resin or molding compound to provide mechanical protection and environmental sealing.
- Testing and Inspection: The completed SCPS undergoes testing and inspection to verify electrical functionality, thermal performance, and reliability. This may include electrical continuity tests, thermal cycling tests, and visual inspection for defects.
- Final Packaging:Once testing is completed, the SCPS may be further packaged into a larger housing or module, depending on the specific application requirements.
Overall, the fabrication process for SCPS involves a combination of precision machining, assembly, and testing techniques to create substrates that meet performance, reliability, and manufacturability requirements for semiconductor packaging.
How do you manufacture a Step Cavity Package Substrate (SCPS)?
Manufacturing a Step Cavity Package Substrate (SCPS) involves a series of intricate processes aimed at creating a robust substrate with integrated thermal management features and precise cavity dimensions to house the semiconductor die. Here’s an expanded overview of the manufacturing process:
- Substrate Material Selection: The manufacturing process begins with selecting the appropriate substrate material based on the desired electrical, thermal, and mechanical properties. Common materials include ceramics like alumina or aluminum nitride, or organic laminates such as FR-4 or BT epoxy.
- Substrate Fabrication: The substrate material is prepared in the form of sheets or panels, which undergo machining processes to form the desired substrate shape and dimensions. This may involve cutting, grinding, and polishing to achieve the required flatness and surface finish.
- Cavity Formation:Precision machining techniques such as laser ablation, milling, or chemical etching are used to create the cavity or recessed area within the substrate. The dimensions of the cavity are carefully controlled to ensure proper fit and alignment of the semiconductor die.
- Integration of Thermal Management Features: Thermal management features such as thermal vias, heat spreaders, or metal layers are integrated into the substrate design to enhance heat dissipation from the semiconductor die. These features may be fabricated using processes such as laser drilling, sputtering, or plating.
- Surface Preparation:The surface of the substrate is prepared for die attachment and wire bonding. This involves cleaning and roughening the surface to improve adhesion and bond strength.
- Die Attachment: The semiconductor die is attached to the bottom of the cavity using die attach adhesive or solder. Precision alignment is critical to ensure proper electrical connectivity and thermal conduction between the die and the substrate.
- Wire Bonding or Flip-Chip Assembly: Interconnects such as wire bonds or flip-chip connections are formed between the semiconductor die and the substrate to establish electrical connections. This involves bonding thin wires from the die to bond pads on the substrate using ultrasonic or thermocompression bonding techniques. In flip-chip assembly, solder bumps on the die are aligned and bonded directly to corresponding pads on the substrate.
- Integration of Passive Components: If required, passive components such as capacitors or resistors may be integrated into the substrate design. These components can be mounted within the cavity or on the substrate surface using standard assembly techniques.
- Encapsulation:The assembled substrate, including the semiconductor die and any integrated components, may be encapsulated with a protective material such as epoxy resin or molding compound to provide mechanical protection and environmental sealing.
- Testing and Inspection:The completed SCPS undergoes rigorous testing and inspection to verify electrical functionality, thermal performance, and reliability. This may include electrical continuity tests, thermal cycling tests, and visual inspection for defects.
- Final Packaging: Once testing is completed and the SCPS is verified to meet specifications, it may be further packaged into a larger housing or module, depending on the specific application requirements.
Throughout the manufacturing process, strict quality control measures are implemented to ensure consistency, reliability, and adherence to specifications. Collaboration between design engineers, manufacturing engineers, and quality assurance teams is essential to optimize the manufacturing process and deliver high-quality SCPS products to customers.
How much should a Step Cavity Package Substrate (SCPS) cost?
The cost of a Step Cavity Package Substrate (SCPS) can vary significantly depending on several factors, including the substrate material, dimensions, complexity of the design, integrated features, manufacturing processes, and quantity ordered. Here are some factors that influence the cost:
- Substrate Material: The choice of substrate material (ceramic or organic laminate) can have a significant impact on cost. Ceramic substrates tend to be more expensive due to their higher thermal conductivity and mechanical strength compared to organic laminates.
- Manufacturing Processes: The complexity of the fabrication processes involved in creating the SCPS, such as cavity formation, integration of thermal management features, and assembly of components, will affect the overall cost. More intricate designs and specialized manufacturing techniques may result in higher costs.
- Size and Dimensions: Larger substrates or substrates with larger cavities typically require more material and additional processing steps, which can increase costs. Similarly, substrates with tighter dimensional tolerances may require more precise machining processes, adding to the overall cost.
- Integrated Features: SCPS with integrated thermal management features, such as thermal vias, heat spreaders, or integrated passive components, may command a higher cost due to the additional materials and manufacturing complexity involved.
- Quantity Ordered: Economies of scale often apply in manufacturing, meaning that larger order quantities typically result in lower per-unit costs. Ordering larger quantities of SCPS can help reduce the overall cost per unit.
- Supplier and Location: The choice of supplier and their location can also impact the cost of SCPS. Suppliers with lower labor costs or access to cheaper raw materials may offer more competitive pricing.
Given these factors, it’s challenging to provide a specific cost estimate for SCPS without knowing the exact specifications and quantities involved. However, SCPS can range in cost from a few dollars to tens or even hundreds of dollars per unit, depending on the aforementioned factors. Companies seeking to procure SCPS for their semiconductor packaging needs should work closely with suppliers to obtain accurate cost estimates based on their specific requirements.
What is a Step Cavity Package Substrate (SCPS) base material?
The base material used for Step Cavity Package Substrates (SCPS) can vary depending on the specific requirements of the application, manufacturing process, and performance characteristics desired. Two common types of materials used for SCPS are ceramics and organic laminates.
- Ceramic Substrates: Ceramics such as alumina (Al2O3) and aluminum nitride (AlN) are widely used as base materials for SCPS. Ceramic substrates offer excellent thermal conductivity, mechanical strength, and dimensional stability, making them well-suited for high-power applications and environments where thermal management is critical. Alumina is a popular choice for its relatively low cost and good electrical insulation properties, while aluminum nitride offers higher thermal conductivity for enhanced heat dissipation.
- Organic Laminates: Organic laminates, such as FR-4 (Flame Retardant 4) and BT (Bismaleimide Triazine), are also used as base materials for SCPS, particularly in applications where cost-effectiveness and flexibility are prioritized over thermal performance. Organic laminates offer good electrical insulation properties, ease of processing, and lower cost compared to ceramics. However, they typically have lower thermal conductivity and mechanical strength, which may limit their suitability for high-power or high-temperature applications.
The choice of base material for SCPS depends on factors such as thermal requirements, electrical properties, mechanical strength, cost considerations, and manufacturability. Design engineers select the most appropriate material based on the specific needs of the application and the desired performance characteristics of the SCPS.
Which company makes Step Cavity Package Substrates (SCPS)?
Step Cavity Package Substrates (SCPS) are typically manufactured by semiconductor packaging and materials manufacturing companies. Some well-known companies include Infineon, TSMC (Taiwan Semiconductor Manufacturing Company), Intel, and ASE (Advanced Semiconductor Engineering). These companies have extensive experience and expertise in the semiconductor industry and are capable of providing various types of packaging solutions, including SCPS.
In our company, we also have the capability to produce Step Cavity Package Substrates (SCPS). We have advanced manufacturing equipment, a professional engineering team, and rich experience to meet customers’ custom requirements and provide high-quality SCPS products.
Our manufacturing process includes:
- Design and Engineering Support: Our engineering team can collaborate with customers to design custom SCPS solutions according to their specific requirements. We utilize advanced design tools and simulation software to optimize designs, ensuring product performance and reliability.
- Material Selection: We offer a variety of material options, including ceramics (such as alumina and aluminum nitride) and organic laminates (such as FR-4 and BT epoxy), to meet the needs of different applications.
- Precision Machining: We employ advanced machining techniques such as laser processing, chemical etching, and CNC machining to ensure the accuracy and quality of SCPS.
- Assembly and Testing: Our production process includes assembly and testing stages to ensure that each SCPS meets customer specifications and performance requirements. We conduct rigorous quality control and testing to ensure product reliability and consistency.
- Customization Services: We provide customized production services to tailor SCPS according to customer requirements, including customization of dimensions, materials, integrated features, and more.
Through our professional team and advanced production equipment, we can provide high-quality, customized Step Cavity Package Substrates (SCPS) to meet various customer needs and maintain a competitive edge in the semiconductor packaging field.
What are the 7 qualities of good customer service?
Good customer service is characterized by several key qualities that contribute to positive customer experiences and satisfaction. Here are seven qualities of good customer service:
- Responsiveness: Good customer service involves promptly addressing customer inquiries, concerns, and requests. Whether it’s answering phone calls, responding to emails, or assisting customers in person, being responsive demonstrates attentiveness and a commitment to helping customers in a timely manner.
- Empathy: Empathy is the ability to understand and relate to the feelings and perspectives of customers. Good customer service representatives listen actively to customers, acknowledge their emotions, and demonstrate compassion and understanding, even in challenging situations.
- Clear Communication: Effective communication is essential for good customer service. Customer service representatives should communicate clearly, using language that is easy to understand and avoiding jargon or technical terms. They should also provide accurate and relevant information to address customer questions or concerns.
- Problem-Solving Skills: Good customer service involves effectively resolving customer issues and problems. Customer service representatives should have strong problem-solving skills to identify solutions, address customer complaints, and handle difficult situations with professionalism and efficiency.
- Professionalism: Professionalism encompasses behaviors such as politeness, respectfulness, and integrity. Good customer service representatives maintain a professional demeanor at all times, remaining courteous and composed, even in challenging interactions. They also uphold ethical standards and company policies when assisting customers.
- Product Knowledge: Having a deep understanding of the products or services offered by the company is crucial for providing good customer service. Customer service representatives should be knowledgeable about the features, benefits, and specifications of the products or services, enabling them to answer customer questions accurately and offer relevant recommendations.
- Follow-Up and Follow-Through: Good customer service extends beyond the initial interaction. Customer service representatives should follow up with customers to ensure that their issues have been resolved satisfactorily and that they are satisfied with the outcome. Additionally, following through on any promises or commitments made to customers demonstrates reliability and builds trust.
By embodying these qualities, businesses can deliver exceptional customer service experiences that foster loyalty, positive word-of-mouth referrals, and long-term relationships with customers.
FAQs
What is a Step Cavity Package Substrate (SCPS)?
A Step Cavity Package Substrate (SCPS) is a type of substrate used in semiconductor packaging that features a recessed area or cavity to accommodate a semiconductor die. SCPS designs offer advantages such as reduced height profile, improved thermal performance, and enhanced electrical performance.
What are the benefits of using SCPS?
SCPS designs offer several benefits, including reduced height profile, improved thermal management, enhanced electrical performance, mechanical stability, and potential integration of passive components. These advantages make SCPS suitable for various electronic applications.
What materials are used to manufacture SCPS?
SCPS can be manufactured using materials such as ceramics (e.g., alumina, aluminum nitride) or organic laminates (e.g., FR-4, BT epoxy). The choice of material depends on factors such as thermal conductivity, mechanical strength, and cost considerations.
What are the key design considerations for SCPS?
Key design considerations for SCPS include die size and placement, cavity dimensions, substrate material selection, thermal management features, interconnect design, signal integrity considerations, assembly and packaging constraints, reliability, and electromagnetic compatibility (EMC).
How are SCPS manufactured?
The manufacturing process for SCPS typically involves substrate preparation, cavity formation, integration of thermal management features, surface preparation, die attachment, wire bonding or flip-chip assembly, integration of passive components (if required), encapsulation, testing, and final packaging.
What companies produce SCPS?
SCPS are typically manufactured by semiconductor packaging and materials manufacturing companies such as Infineon, TSMC, Intel, and ASE. These companies have extensive experience and expertise in the semiconductor industry and can provide various types of packaging solutions, including SCPS.
What are the cost considerations for SCPS?
The cost of SCPS can vary depending on factors such as substrate material, dimensions, complexity of the design, integrated features, manufacturing processes, and quantity ordered. Companies seeking SCPS should work closely with suppliers to obtain accurate cost estimates based on their specific requirements.