Step cavity PCB Manufacturer
Step cavity PCB Manufacturer,Step cavity PCBs feature recessed areas or cavities at varying depths within the board, enabling the integration of components at different levels beneath the surface. This advanced PCB technology allows for reduced board thickness, improved spatial efficiency, and enhanced thermal management. Commonly used in compact electronic devices like smartphones, wearables, and IoT devices, Step cavity PCBs optimize space utilization while maintaining high performance and reliability. With precise manufacturing techniques and careful design considerations, Step cavity PCBs offer a versatile solution for applications requiring compactness, component integration, and thermal control.
What is a Step cavity PCB?
A Step Cavity PCB, or stepped cavity printed circuit board, is an advanced type of PCB designed with recessed areas or cavities at different depths within the board. This design allows for the placement of components at various levels beneath the surface of the PCB, which can help in achieving thinner overall profiles for electronic devices, better integration of different types of components, and improved electrical performance.
The creation of a step cavity PCB involves precise milling or controlled depth routing during the manufacturing process. The cavities are created according to the specific requirements of the components they will house, such as sensors, chips, or connectors that may need to be embedded into the board at different depths to meet design specifications, thermal management needs, or to optimize the spatial configuration of the circuitry.
This type of PCB is particularly useful in applications where space is at a premium, such as in smartphones, wearable technology, medical devices, and other compact electronic products. By allowing components to sit flush with or below the board surface, designers can minimize the thickness of the product, which is a critical factor in many modern electronic devices. Additionally, step cavity PCBs can also help in achieving more efficient connectivity and better reliability through a more secure mechanical fixation of the components. They also facilitate the integration of multi-layered board designs, enhancing the functionality and complexity of electronic devices without increasing their footprint.
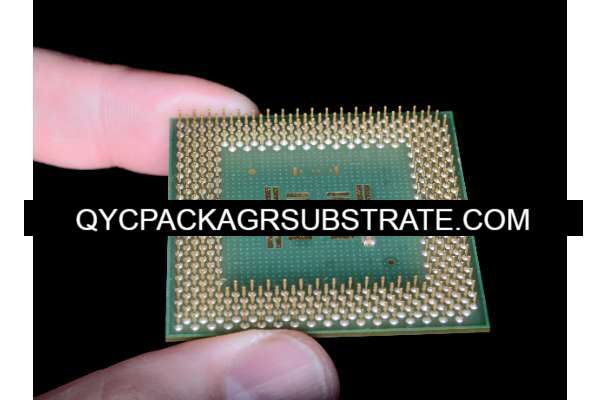
Step cavity PCB Manufacturer
What are the Step cavity PCB Design Guidelines?
Designing a step cavity PCB requires careful consideration of various factors to ensure optimal performance, manufacturability, and reliability. Here are some key guidelines:
- Component Placement: Plan the placement of components within the cavities to optimize space usage and electrical performance. Consider thermal management requirements and signal integrity.
- Cavity Dimensions: Design cavities with precise dimensions to accommodate components securely and with minimal clearance. Ensure that the depths and widths of the cavities match the components they will house.
- Material Selection: Choose PCB materials suitable for milling or routing cavities, considering factors like material thickness, rigidity, and thermal properties. High-quality materials ensure structural integrity and reliable performance.
- Cavity Depth Control: Maintain tight control over cavity depths to prevent damage to internal layers and ensure uniformity across the PCB. Use advanced manufacturing techniques such as depth control routing or milling.
- Edge Plating: Implement edge plating or other reinforcement techniques to strengthen the edges of cavities and prevent delamination or damage during assembly and use.
- Signal Integrity: Minimize signal interference by carefully routing signal traces away from cavities and ensuring proper shielding where necessary. Pay attention to impedance matching and signal integrity principles.
- Thermal Management: Incorporate thermal vias, heatsinks, or other thermal management features to dissipate heat efficiently, especially for components housed within cavities. Optimize airflow and consider the impact of cavity design on heat dissipation.
- Manufacturability: Collaborate closely with PCB manufacturers to ensure that the design is manufacturable within specified tolerances. Provide detailed fabrication drawings and instructions for cavity dimensions and depths.
- Assembly Considerations: Plan for component assembly and soldering processes, taking into account access to components within cavities and any special handling requirements.
- Testing and Quality Assurance: Develop testing procedures to verify the integrity of cavities and ensure that components are properly seated and connected. Conduct thorough quality assurance checks throughout the manufacturing process.
By adhering to these design guidelines, engineers can create step cavity PCBs that meet performance requirements, manufacturing constraints, and reliability standards for a wide range of electronic applications.
What is the Step cavity PCB Fabrication Process?
The fabrication process for step cavity PCBs involves several stages, including design preparation, material selection, cavity creation, layer lamination, and finishing. Here’s an overview:
- Design Preparation: Engineers create the PCB layout using specialized design software. They define the dimensions and depths of the cavities and ensure that the design meets the requirements for component placement, signal integrity, and thermal management.
- Material Selection: Select PCB materials suitable for step cavity fabrication. Typically, high-quality substrate materials such as FR-4 or specialized laminates with specific thermal and electrical properties are used. The choice of materials depends on the application requirements and manufacturing capabilities.
- Cavity Creation: Using advanced milling or routing techniques, the cavities are machined into the PCB substrate according to the design specifications. CNC (Computer Numerical Control) machines with precise depth control capabilities are often used to achieve accurate cavity dimensions and depths.
- Layer Lamination: Multiple layers of substrate material and copper foil are laminated together to form the complete PCB stack-up. Each layer may contain conductive traces, signal planes, and ground planes according to the PCB design. The cavities are incorporated into the appropriate layers during lamination.
- Drilling and Plating: Pinholes, via holes, and through-holes are drilled into the PCB to establish electrical connections between layers. These holes are plated with conductive material to ensure continuity and facilitate interconnection between components.
- Component Assembly: Surface-mount and through-hole components are soldered onto the PCB according to the design layout. Special attention is paid to components housed within cavities to ensure proper alignment and soldering.
- Testing and Inspection: The fabricated PCB undergoes rigorous testing and inspection processes to verify functionality, electrical performance, and adherence to design specifications. Various testing methods, including electrical testing, visual inspection, and functional testing, may be employed.
- Finishing: Finally, the PCB is finished with coatings or surface finishes to enhance durability, solderability, and resistance to environmental factors such as moisture and corrosion. Common finishes include solder mask, hot air leveling (HASL), immersion gold, and immersion silver.
Throughout the fabrication process, strict quality control measures are implemented to ensure the integrity and reliability of the step cavity PCB. Collaboration between design engineers and manufacturing experts is essential to address any challenges and optimize the fabrication process for specific application requirements.
How do you manufacture a Step cavity PCB?
Manufacturing a step cavity PCB involves several steps, from design preparation to final inspection. Here’s a detailed overview of the manufacturing process:
- Design Preparation: Engineers create the PCB layout using CAD (Computer-Aided Design) software, defining the dimensions, cavity locations, and other specifications. Design considerations include component placement, signal routing, thermal management, and manufacturability.
- Material Selection: Select PCB materials suitable for step cavity fabrication, considering factors such as substrate thickness, dielectric properties, and thermal conductivity. Common materials include FR-4 epoxy laminate, high-frequency laminates, and metal-core laminates.
- Cavity Creation: Utilize precision milling or routing equipment to create cavities within the PCB substrate. CNC (Computer Numerical Control) machines with depth control capabilities ensure accurate cavity dimensions and depths according to the design specifications.
- Layer Preparation: Prepare individual layers of the PCB stack-up by laminating substrate material with copper foil. Each layer may contain conductive traces, signal planes, ground planes, and pre-machined cavities.
- Drilling and Plating: Drill holes for vias, through-holes, and component mounting. Plating processes deposit conductive material (e.g., copper) inside the holes to establish electrical connections between layers and facilitate component attachment.
- Circuit Patterning: Apply a layer of photoresist material onto the copper surface and expose it to UV light through a photomask, defining the circuit patterns. Chemical etching removes unwanted copper, leaving behind the desired conductive traces and pad areas.
- Solder Mask Application: Apply solder mask ink over the PCB surface, covering areas not intended for soldering and providing insulation and protection for the copper traces. UV exposure and development processes define the solder mask pattern.
- Surface Finish: Apply surface finish to protect exposed copper surfaces, enhance solderability, and improve corrosion resistance. Common surface finishes include HASL (Hot Air Solder Leveling), ENIG (Electroless Nickel Immersion Gold), and immersion silver.
- Component Assembly: Place surface-mount and through-hole components onto the PCB using automated pick-and-place machines or manual assembly methods. Soldering techniques, such as reflow soldering and wave soldering, attach the components to the PCB.
- Testing and Inspection: Conduct electrical testing, visual inspection, and functional testing to verify PCB functionality, integrity, and adherence to design specifications. Test methods may include flying probe testing, automated optical inspection (AOI), and in-circuit testing (ICT).
- Final Finishing: Perform final finishing processes, such as edge profiling, routing, and depanelization, to separate individual PCBs from the manufacturing panel. Clean the PCBs to remove any residues or contaminants.
- Quality Control: Implement stringent quality control measures throughout the manufacturing process to ensure consistency, reliability, and compliance with industry standards. Inspectors perform visual checks, dimensional measurements, and electrical testing to identify and rectify any defects.
By following these steps and adhering to best practices, manufacturers can produce high-quality step cavity PCBs suitable for a wide range of applications, including consumer electronics, telecommunications, automotive, aerospace, and medical devices.
How much should a Step cavity PCB cost?
The cost of a step cavity PCB can vary widely depending on several factors, including the complexity of the design, the number of layers, the dimensions, the materials used, the manufacturing processes involved, and the quantity ordered. Here are some key factors that can influence the cost:
- Design Complexity:Intricate designs with multiple cavities, dense component placement, and complex routing patterns will typically incur higher manufacturing costs due to the increased production time and material usage.
- Number of Layers: Step cavity PCBs with more layers require additional material and manufacturing steps, leading to higher costs compared to simpler single or double-sided PCBs.
- Material Selection: The choice of PCB substrate material and surface finish can impact the cost. Specialized materials with unique properties or finishes may command higher prices.
- Manufacturing Processes: Advanced fabrication techniques such as precision milling, controlled-depth routing, and specialized plating processes can increase production costs.
- Quantity: Economies of scale apply to PCB manufacturing, meaning that larger production runs typically result in lower per-unit costs. Ordering higher quantities can lead to volume discounts from PCB manufacturers.
- Lead Time: Expedited production and delivery options may incur additional fees. Longer lead times can often result in lower costs as they allow for more efficient production scheduling.
- Additional Services: Optional services such as design validation, prototyping, testing, and assembly may add to the overall cost.
To obtain an accurate cost estimate for a step cavity PCB, it’s best to consult with PCB manufacturers or suppliers directly. They can provide detailed quotes based on your specific design requirements, quantities, and desired delivery schedule. Additionally, online PCB fabrication platforms often offer quoting tools where you can input your design specifications to receive instant estimates.
What is the Step cavity PCB base material?
The base material for step cavity PCBs typically consists of various types of laminates with specific dielectric properties and thermal characteristics. The choice of base material depends on the application requirements, performance specifications, and manufacturing capabilities. Here are some common base materials used for step cavity PCBs:
- FR-4 (Flame Retardant 4): FR-4 is the most widely used substrate material for PCBs due to its excellent electrical insulation properties, mechanical strength, and cost-effectiveness. It consists of woven fiberglass cloth impregnated with epoxy resin.
- High-Frequency Laminates: For RF (Radio Frequency) and microwave applications, high-frequency laminates with low dielectric constants and loss tangents are preferred to minimize signal loss and impedance mismatch. Materials such as Rogers RO4000 series, Taconic RF35, and Arlon AD series are commonly used.
- Metal-Core Laminates: In applications requiring enhanced thermal conductivity and heat dissipation, metal-core laminates are used as the base material. These laminates feature a metal core (usually aluminum or copper) sandwiched between layers of dielectric material.
- Polyimide (PI) Laminates: Polyimide laminates offer exceptional temperature resistance, making them suitable for high-temperature applications such as aerospace and automotive electronics. They are also flexible, allowing for the fabrication of flexible or rigid-flex PCBs.
- Specialized Laminates: Some applications may require specialized laminates tailored to specific performance requirements, such as high-speed digital signaling, high-voltage insulation, or harsh environmental conditions. Examples include materials like Teflon (PTFE), ceramic-filled laminates, and resin-coated copper (RCC) laminates.
When selecting the base material for a step cavity PCB, engineers consider factors such as electrical properties (dielectric constant, dissipation factor), thermal conductivity, dimensional stability, moisture absorption, and compatibility with manufacturing processes (milling, drilling, plating). Collaboration between design engineers and PCB manufacturers is essential to choose the most suitable base material for the intended application and ensure the overall performance and reliability of the PCB.
Which company makes Step cavity PCBs?
Step cavity PCBs are typically manufactured by specialized PCB manufacturing companies. Some well-known PCB manufacturers, such as Delta Electronics, Foxconn Technology Group, Omron, etc., have the capability to produce Step cavity PCBs in their advanced production facilities. These companies possess advanced equipment and technologies to meet the manufacturing needs of various complex PCB designs and ensure product quality and reliability through ISO quality management system certification.
Just like our company, we have advanced manufacturing equipment and experienced engineering team capable of producing various types of PCBs, including Step cavity PCBs. Our manufacturing process covers every step from design preparation to final inspection, ensuring that the quality and performance of the products meet customer requirements.
Our strengths include:
- Advanced Equipment: We invest in the latest PCB manufacturing equipment and technologies, including high-precision CNC milling machines, etching machines, drilling machines, etc., to ensure accurate manufacturing of Step cavity PCBs.
- Experienced Team: We have a team of experienced engineers and technical personnel who can provide comprehensive technical support and solutions, ensuring smooth PCB design and manufacturing processes.
- Quality Assurance: We strictly adhere to the ISO quality management system, conducting comprehensive quality control and inspection to ensure that each step meets standards and customer requirements.
- Customized Services:We can customize Step cavity PCBs according to customer-specific requirements, including size, materials, layers, surface finishes, etc., to meet the needs of different application scenarios.
Therefore, as an experienced and technologically advanced PCB manufacturer, we have the ability to provide high-quality Step cavity PCBs and offer customized solutions and comprehensive support to our customers. Whether in consumer electronics, communication equipment, medical devices, or industrial control, we can meet customer needs and provide high-quality products and services.
What are the 7 qualities of good customer service?
Good customer service is characterized by several key qualities that contribute to positive interactions and customer satisfaction. Here are seven qualities of good customer service:
- Responsiveness: Good customer service involves promptly addressing customer inquiries, concerns, and requests. Responding to customers in a timely manner shows respect for their time and demonstrates a commitment to meeting their needs.
- Empathy: Empathy is the ability to understand and empathize with customers’ feelings, concerns, and perspectives. Showing empathy helps build rapport and trust, making customers feel valued and understood.
- Clear Communication: Effective communication is essential for good customer service. Clearly conveying information, instructions, and solutions in a polite and understandable manner helps avoid misunderstandings and ensures that customers have the information they need.
- Problem-solving Skills: Good customer service representatives are skilled at identifying and resolving customer issues and complaints. They approach problems with a positive attitude, remain calm under pressure, and work proactively to find solutions that meet customers’ needs.
- Professionalism: Professionalism encompasses various qualities such as courtesy, respect, and integrity. Treating customers with professionalism creates a positive impression and fosters trust and confidence in the company’s products or services.
- Adaptability: Customer service representatives should be adaptable and flexible in their approach to different customer situations and preferences. Being able to adjust communication styles, problem-solving strategies, and service delivery methods based on individual customer needs enhances the overall customer experience.
- Follow-up and Follow-through: Good customer service doesn’t end with resolving a customer’s immediate issue. It also involves following up to ensure that the customer’s needs were met satisfactorily and following through on any promises or commitments made during the interaction. This demonstrates accountability and reinforces the company’s dedication to customer satisfaction.
By embodying these qualities, businesses can provide exceptional customer service experiences that foster customer loyalty, positive word-of-mouth referrals, and long-term success.
FAQs
What is a Step cavity PCB?
A Step cavity PCB is a type of printed circuit board that features recessed areas or cavities at different depths within the board. These cavities allow for the placement of components at various levels beneath the surface of the PCB, enabling thinner profiles and better integration of components.
What are the advantages of Step cavity PCBs?
Step cavity PCBs offer several advantages, including reduced board thickness, improved component integration, enhanced thermal management, and better overall space utilization. They are particularly useful in applications where space is limited and compactness is essential.
What are the typical applications of Step cavity PCBs?
Step cavity PCBs are used in a wide range of applications across industries such as consumer electronics, telecommunications, medical devices, automotive, aerospace, and industrial automation. They are commonly found in smartphones, wearables, IoT devices, RF/microwave systems, and high-density electronic products.
How are Step cavity PCBs manufactured?
The manufacturing process for Step cavity PCBs involves several steps, including design preparation, material selection, cavity creation through precision milling or routing, layer lamination, drilling and plating, component assembly, testing, and finishing. Advanced fabrication techniques and tight quality control measures are essential for producing high-quality Step cavity PCBs.
What design considerations are important for Step cavity PCBs?
Design considerations for Step cavity PCBs include cavity dimensions and depths, component placement, signal integrity, thermal management, material selection, and manufacturability. Collaboration between design engineers and PCB manufacturers is crucial to ensure that the design meets performance requirements and manufacturing constraints.
Are Step cavity PCBs more expensive than traditional PCBs?
The cost of Step cavity PCBs can vary depending on factors such as design complexity, material selection, manufacturing processes, quantity ordered, and additional services required. While Step cavity PCBs may incur higher manufacturing costs due to their complexity, the benefits they offer in terms of space savings and improved performance can justify the investment in many cases.
How can I determine if Step cavity PCBs are suitable for my project?
To determine if Step cavity PCBs are suitable for your project, consider factors such as space constraints, component integration requirements, thermal management needs, and desired performance characteristics. Consulting with PCB design experts and manufacturers can help assess the feasibility and benefits of using Step cavity PCBs for your specific application.