Top 10 package Substrate Manufacturer
What are Top 10 Package Substrate?
We are a professional Top 10 package Substrate Manufacturer supplier, we mainly produce ultra-small bump pitch substrate, ultra-small trace and spacing packaging substrate and PCBs.
The term “Top 10 Package Substrate” might not be on everyone’s lips, but let’s navigate the landscape of commonly used materials for electronic packaging, especially in the domains of integrated circuits (ICs) and electronic components.
FR-4 (Flame Retardant 4): Visualize this as the reliable companion – an epoxy-based material armored with glass. It’s cost-effective and an all-rounder in various applications.
FR-5: Imagine FR-5 as the resilient sibling of FR-4, tailored to gracefully handle higher temperatures during operational stints.
Polyimide: This material boasts a blend of thermal stability and flexibility, making it the artist’s palette for applications with stringent temperature and spatial requirements.
Rogers Corporation Materials: Meet Rogers, the virtuoso in high-frequency laminates, lending finesse to RF and microwave applications.
Alumina (Aluminum Oxide): A ceramic substrate with a knack for thermal conductivity, frequently enlisted in the service of high-power applications.
Beryllium Oxide (BeO): Acknowledged for its mastery in thermal conductivity, particularly in setups where the limelight is on efficient heat dissipation.
LTCC (Low-Temperature Co-fired Ceramic): Picture this as the craftsman’s choice, fashioning multilayer ceramic substrates that seamlessly embrace passive components.
FRP (Flexible Reinforced Plastic): Envision a substrate that dances with flexibility – that’s FRP. Ideal for applications that crave a bit of bend, like those entwined with flexible PCBs.
Copper-Clad Laminates: These laminates are akin to a dynamic duo, with copper intimately bonded to a substrate, forming the bedrock of myriad PCB fabrication processes.
Metal Core PCBs (MCPCB): With a metal core, typically aluminum, these PCBs radiate excellence in the realm of heat dissipation, especially catering to high-power LED applications.
Choosing the right substrate is akin to selecting the perfect instrument for a symphony – it hinges on the distinctive needs of your electronic device. Whether it’s orchestrating effective heat management, maintaining peak electrical performance, or adhering to budgetary constraints, your material selection holds the key to orchestrating the harmony of your electronic package.
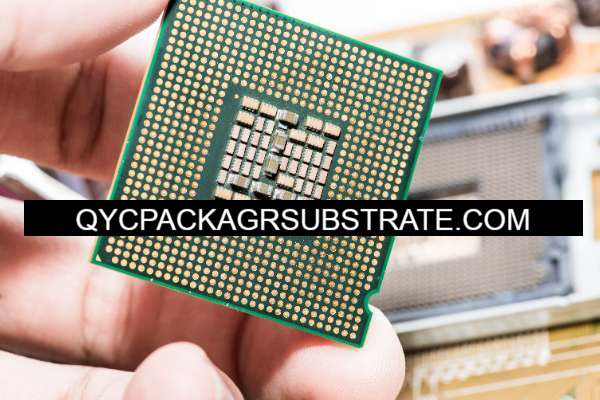
Top 10 package Substrate Manufacturer
What are the functions of Top 10 Package Substrate?
Certainly, let’s provide a fresh take on describing the functions of common substrate materials used in electronic packaging:
FR-4 (Flame Retardant 4):
Electrical Isolation and Sturdy Foundation: Serves as an insulating shield against electrical shorts while providing a robust base for component attachment.
FR-5:
Heat Endurance: Engineered to brave elevated temperatures during operation, ensuring reliability in challenging conditions.
Polyimide:
Flexibility and Thermal Resilience: Embraces flexibility for dynamic applications and stands resilient in the face of high-temperature challenges.
Rogers Corporation Materials:
Sculpted for High-Frequency Harmony: Crafted to orchestrate efficiency in RF and microwave applications, minimizing signal disturbances.
Alumina (Aluminum Oxide):
Heat’s Whisperer: Conducts and dissipates heat adeptly in high-power scenarios, doubling up as a reliable structural support.
Beryllium Oxide (BeO):
Mastering Heat’s Choreography: Particularly adept in applications demanding top-notch heat dissipation.
LTCC (Low-Temperature Co-fired Ceramic):
Passive Components’ Canvas: Allows the embedding of passive components, creating a canvas for compact and functional designs.
FRP (Flexible Reinforced Plastic):
Bendable Virtuoso: Tailored for applications desiring flexibility, bringing a touch of adaptability, especially in the realm of flexible PCBs.
Copper-Clad Laminates:
Conductive Harmony with Strong Bonds: Ensures a smooth flow of electrical signals through copper, forging robust bonds between copper and substrate.
Metal Core PCBs (MCPCB):
Heat’s Symphony Conductor: Conducts and dissipates heat efficiently, particularly beneficial in illuminating high-power LED applications.
Thermal Maestro: Elevates the overall thermal performance, orchestrating a symphony within electronic devices.
These substrate materials each play a unique role, addressing specific needs related to electrical efficiency, thermal regulation, mechanical robustness, and overall dependability within the intricate dance of electronic packaging. The selection of substrate material becomes an art, finely tuned to the distinctive requirements and performance aspirations of each electronic device.
What are the different types of Top 10 Package Substrate?
Certainly, let’s present information about different types of substrate materials used in electronic packaging in a different manner:
FR-4 (Flame Retardant 4): This is like the workhorse of substrate materials, blending epoxy with glass reinforcement for a cost-effective and versatile foundation.
FR-5: A close relative to FR-4 but tailored to endure higher temperatures during operation, making it a choice for more demanding applications.
Polyimide: Picture this material as the acrobat – flexible and stable even in the face of high temperatures, ideal for applications that require a bit of bending.
Rogers Corporation Materials: These materials are like tailored suits, specialized for high-frequency applications such as RF and microwave circuits.
Alumina (Aluminum Oxide): Meet the heat conductor – a ceramic substrate with commendable thermal conductivity, often enlisted in high-power scenarios.
Beryllium Oxide (BeO): The thermal maestro – recognized for its outstanding heat conductivity, a top pick when efficient heat dissipation is non-negotiable.
LTCC (Low-Temperature Co-fired Ceramic): Think of LTCC as the puzzle solver, adept at crafting multilayer ceramic substrates that seamlessly integrate passive components.
FRP (Flexible Reinforced Plastic): The contortionist – flexible and adaptable, making it suitable for applications that demand a bit of bending, like flexible PCBs.
Copper-Clad Laminates: This dynamic duo involves copper intimately bonded to a substrate, forming the backbone of PCB fabrication processes.
Metal Core PCBs (MCPCB): Imagine MCPCBs as the cool-headed conductors – with a metal core, usually aluminum, they efficiently dissipate heat, a perfect fit for the dazzling world of high-power LED applications.
Each substrate material has its unique characteristics, akin to different players in a symphony, contributing to the overall performance of electronic devices. The choice of substrate depends on the specific needs of the application, dancing between factors like thermal efficiency, mechanical stability, and budget considerations.
What is the relationship between Top 10 Package Substrate and IC packaging?
Certainly, let’s reframe and provide a different perspective on the relationship between substrate materials and IC packaging:
In the realm of IC packaging, the selection of substrate materials is akin to choosing a tailored suit for a complex dance performance. These materials are not only the stage but also the choreographers, influencing every move and nuance of the integrated circuit’s (IC) presentation.
Electrical Choreography: The substrate takes center stage in facilitating the intricate electrical connections between the IC and the external circuitry. Its dielectric properties are the composers, harmonizing signal integrity and ensuring a flawless performance.
Thermal Ballet: In the heat-intensive dance of IC operation, the substrate’s role as a conductor becomes crucial. Materials with excellent thermal conductivity, like metal core PCBs or ceramics, gracefully dissipate the heat generated, ensuring the IC doesn’t miss a beat.
Mechanical Waltz: Picture the substrate as the partner in a waltz, providing the IC with stability and support. It must gracefully navigate the stresses of assembly processes and external conditions, showcasing its mechanical prowess for an elegant and reliable performance.
Package Aesthetics: Like the framing of a masterpiece, the substrate significantly influences the size, form factor, and overall aesthetics of the IC package. Whether it’s the flexibility of polyimide for a dynamic display or the rigidity of FR-4 for a classic appearance, the substrate sets the visual tone of the performance.
Integration Choreography: Different IC packaging technologies, be it the intricate steps of surface mount technology (SMT) or the deeper movements of through-hole technology, require a substrate that can seamlessly integrate and synchronize with these processes.
In essence, the substrate is both the canvas and the conductor in the intricate dance of IC packaging. The choice of material is not just a technical decision but an artistic one, where the characteristics of the substrate mold and shape the overall performance of the electronic device. It’s a dance of technology and aesthetics, each substrate material bringing its unique flair to the stage of IC packaging.
How do Top 10 Package Substrate differ from PCBs?
Certainly, let’s provide a different angle on comparing “Top 10 Package Substrate” and Printed Circuit Boards (PCBs):
Core Purpose:
PCBs: Function as the architectural scaffold for electronic circuits, focusing on providing a structured layout for components and electrical connections.
Top 10 Package Substrate: Encompasses a spectrum of materials, each carefully chosen for its unique attributes to address specific requirements within the broader context of electronic packaging.
Composition Diversity:
PCBs: Typically consist of a rigid substrate layer, often FR-4, paired with a conductive layer, commonly copper, forming the intricate circuitry.
Top 10 Package Substrate: Goes beyond conventional PCB compositions, incorporating materials like metal cores, ceramics, and specialized laminates, each selected for its distinctive characteristics.
Adaptability Spectrum:
PCBs: Traditionally known for their rigidity, catering to applications where flexibility is secondary.
Top 10 Package Substrate: Introduces flexibility into the mix with materials such as Polyimide and FRP, designed for applications demanding pliability and adaptability.
Thermal Dynamics:
PCBs: Primarily engineered for electrical connectivity, with less emphasis on thermal conductivity.
Top 10 Package Substrate: Features materials like metal cores, Alumina, and Beryllium Oxide, showcasing a deliberate focus on superior thermal management, crucial for environments with heightened heat generation.
Application Specialization:
PCBs: Ubiquitous across various electronic devices, providing the fundamental structure for an array of applications.
Top 10 Package Substrate: Sheds light on a diversified material palette, with certain substrates catering to specific needs. For instance, Rogers Corporation materials cater to high-frequency applications, while Beryllium Oxide shines in scenarios requiring exceptional heat dissipation.
In summary, while PCBs remain the stalwart framework for electronic circuits, the term “Top 10 Package Substrate” introduces a curated selection of materials, each strategically chosen to address nuanced demands within the dynamic landscape of electronic packaging. It signifies a departure from the conventional rigidity of PCBs, delving into a realm where material choices are as diverse as the applications they serve.
What are the structure and production technology of Top 10 Package Substrate?
Certainly, let’s explore the structures and production technologies of various substrate materials used in electronic packaging with a different narrative:
FR-4 (Flame Retardant 4):
Structural Ensemble: FR-4, like a sturdy performer, boasts a core of woven fiberglass donned with epoxy resin. The dance floor is set with copper foils laminated gracefully on both sides.
Production Choreography: The production unfolds as layers of fiberglass are adorned with epoxy, undergoing a curing and lamination spectacle with the addition of copper foils. The etching process delicately sculpts circuit patterns.
Polyimide:
Structural Solo: Polyimide, the flexible virtuoso, takes center stage with a single-layered act. Its performance is marked by a polyimide film as the foundation, complemented by copper layers for a harmonious partnership.
Production Symphony: The production crescendos with the creation of a polyimide film, elegantly coated with copper through methods like sputtering or electrodeposition.
Rogers Corporation Materials:
Structural Sonata: Rogers materials, a diverse repertoire tailored for specific applications. For instance, Rogers 4350B, a high-frequency maestro, is composed of ceramic-filled PTFE and copper layers waltzing in unison.
Production Harmony: The manufacturing stage involves the fusion of PTFE with ceramic fillers, crafting a composite masterpiece. Copper layers join the ensemble through the artistry of lamination and etching.
Alumina (Aluminum Oxide):
Structural Overture: Alumina, the ceramic luminary, graces the stage with a single-layered act. The material, aluminum oxide, resonates with exceptional thermal conductivity.
Production Ballet: The production unfolds with the shaping and sintering of aluminum oxide, sculpting a ceramic substrate. Copper layers are introduced through various techniques, adding a touch of conductivity.
Beryllium Oxide (BeO):
Structural Serenade: Beryllium Oxide substrates, the thermal virtuosos, present a single-layered spectacle with beryllium oxide leading the thermal symphony.
Production Elegance: The production mirrors that of alumina, with shaping and sintering playing a pivotal role in crafting a ceramic substrate. Copper layers join the performance for electrical harmony.
LTCC (Low-Temperature Co-fired Ceramic):
Structural Symphony: LTCC substrates, the multilayered maestros, unfold a ceramic saga with layers fired in unison. The narrative features embedded conductive traces and a symphony of passive components.
Production Epic: The production narrates the co-firing of ceramic green tapes, each with a layer of circuit patterns. Layers come together in a harmonious firing, allowing for the integration of passive components.
FRP (Flexible Reinforced Plastic):
Structural Ballet: FRP substrates, the flexible dancers, take the stage with a single-layered act. The plastic film, fortified with fibers, brings both flexibility and strength to the performance.
Production Choreography: The production involves a dance of plastics and reinforcing fibers, creating a flexible yet robust substrate. Copper layers gracefully join the ballet for electrical resonance.
Copper-Clad Laminates:
Structural Duet: Copper-clad laminates emerge as a duet, featuring a core substrate, often FR-4, with copper foils laminated on both sides.
Production Fusion: Production involves the lamination of copper foils onto a core substrate, creating a composite piece. Etching refines the copper layers, shaping the duet into circuit patterns.
Metal Core PCBs (MCPCB):
Structural Rhapsody: MCPCBs, the thermal conductors, unfold with a metal core, typically aluminum, embracing dielectric and copper layers in a harmonious composition.
Production Crescendo: The production crescendos with the bonding of dielectric material to a metal core, followed by the laminating of copper foils. Etching adds the final strokes, crafting a symphony of circuits.
In the grand performance of electronic packaging, each substrate material plays a unique role, contributing to the overall symphony of electrical connectivity, thermal dynamics, and mechanical stability. The production processes, akin to choreographed routines, bring these materials to life, shaping the narrative of electronic devices.
Frequently Asked Questions (FAQs)
What is the significance of the term “Top 10 Package Substrate”?
Think of it as a curated playlist of versatile substrate materials. These materials, akin to rockstar performers, bring unique attributes to the electronic packaging stage, addressing diverse needs.
Why are there various types of substrate materials mentioned in the “Top 10 Package Substrate”?
Each material is like a specialist in the orchestra of electronics. From FR-4’s all-around reliability to Polyimide’s flexibility, and Alumina’s heat conductivity, the diversity caters to specific performance requirements.
How does the production process of “Top 10 Package Substrate” materials unfold?
Picture it as an intricate dance routine. Whether it’s the elegant co-firing of LTCC or the shaping and sintering of ceramics, each material undergoes a unique production choreography, adding flair to the electronic symphony.
Are “Top 10 Package Substrate” materials only used in PCBs?
Not just PCBs! These materials are the versatile actors in the electronic world. They play roles in PCBs, IC packaging, and various electronic devices, adapting to different scripts in the tech theater.
How do I choose the right “Top 10 Package Substrate” for my electronic device?
It’s a bit like matchmaking. Consider your device’s needs – does it crave flexibility, high thermal conductivity, or maybe a touch of high-frequency magic? Choose a substrate material that complements the device’s performance desires.
Can you explain the difference between “Top 10 Package Substrate” materials and traditional PCBs?
Think of traditional PCBs as the classics and “Top 10 Package Substrate” as the avant-garde. While PCBs provide a stable platform, the diverse substrate materials offer specialized features beyond the conventional rigidity.
How do these substrate materials contribute to the thermal management of electronic devices?
Imagine them as thermal conductors in a cooling ballet. Materials like Alumina and Beryllium Oxide are stars in dissipating heat, ensuring your device stays cool even during demanding performances.
Is flexibility a key feature of “Top 10 Package Substrate” materials?
Absolutely! Polyimide and Flexible Reinforced Plastic are like the contortionists in the lineup, bringing flexibility to the electronic circus. Ideal for applications that demand a bit of bending.
Where do I find these “Top 10 Package Substrate” materials in the electronics market?
Imagine it as a vibrant marketplace! Look for them in specialized electronics suppliers, and you’ll find a diverse array of materials ready to take center stage in your electronic creations.
Conclusion
In summary, the arena of electronic packaging unfolds as a captivating tapestry, woven with a myriad of substrate materials, each boasting its distinct attributes and purpose. While the term “Top 10 Package Substrate” may not adhere to a standardized industry classification, it serves as a nod to a diverse collection of materials that play pivotal roles in the intricate world of electronic devices.
From the reliable stalwart, FR-4, to the flexible virtuoso, Polyimide, and the high-frequency specialists in the form of Rogers Corporation materials, these substrates dance through the realms of electrical connectivity, thermal dynamics, and mechanical stability.
Alumina and Beryllium Oxide take center stage as thermal luminaries, deftly managing the heat dynamics. LTCC emerges as a multilayered maestro, seamlessly integrating passive components into its ceramic composition. FRP, with its flexible moves, and Copper-Clad Laminates, the dynamic duet of core and copper, add a touch of adaptability and conductivity to the performance.
Metal Core PCBs, with their aluminum cores, step into the limelight as thermal conductors orchestrating a symphony of dielectric and copper layers. Each substrate material assumes a distinct role, contributing to the visual aesthetics, electrical performance, and overall dependability of electronic devices.
In the production realm, the processes unfold as choreographed routines, shaping these materials into functional works of art. Whether it’s the intricate weaving of fiberglass and epoxy curing for FR-4, the shaping and sintering of ceramics for Alumina, or the co-firing of green tapes for LTCC, each production method is a meticulously planned performance.
As we navigate this ever-evolving landscape, the selection of substrate material emerges as an art form, a nuanced decision influenced by the unique demands of applications spanning consumer electronics to robust industrial machinery. The symphony of electronic packaging continues to evolve, with substrate materials at the forefront, shaping the trajectory of future technological landscapes.