Top 10 Packaging Substrate Manufacturer
What is Top 10 Packaging Substrate?
The “Top 10 Packaging Substrates” typically refers to the most commonly used materials for packaging electronic components or devices. These substrates are chosen based on their electrical, thermal, mechanical, and cost-related properties, as well as their suitability for various manufacturing processes. The specific ranking may vary depending on factors such as industry trends, technological advancements, and application requirements. However, some common packaging substrates include:
FR4 (Flame Retardant 4): A widely used epoxy-based laminate material with glass reinforcement, commonly used in printed circuit boards (PCBs) due to its excellent electrical insulation properties and affordability.
Ceramic: Known for its high thermal conductivity, low coefficient of thermal expansion (CTE), and excellent electrical properties, ceramic substrates are often used for high-power applications and in environments requiring high reliability.
Flexible PCBs: Made of flexible plastic materials like polyimide or polyester, flexible PCBs offer advantages in terms of space-saving, lightweight design, and the ability to conform to complex shapes or bend during use.
Metal-Core PCBs (MCPCB): These substrates feature a layer of thermally conductive material (usually aluminum or copper) sandwiched between layers of insulating material, making them suitable for applications requiring efficient heat dissipation, such as LED lighting and power electronics.
FR2: Similar to FR4 but with phenolic resin instead of epoxy, FR2 is a lower-cost alternative used in simpler electronic applications where less demanding electrical and thermal properties are acceptable.
Rigid-Flex PCBs: Combining elements of rigid and flexible PCBs, rigid-flex PCBs offer the advantages of both, allowing for complex three-dimensional designs while maintaining the structural integrity of rigid sections.
HDI (High-Density Interconnect) PCBs: Designed to accommodate higher circuit density and smaller components, HDI PCBs feature advanced technologies such as microvias, fine-pitch traces, and multiple layers to achieve compact designs and high signal integrity.
COB (Chip-On-Board) Substrates: Used in semiconductor packaging, COB substrates involve directly mounting bare semiconductor chips onto a substrate and wire bonding or encapsulating them to form a compact, cost-effective package.
Organic Substrates: These substrates use organic materials such as epoxy resin or polyimide for their base material, offering advantages in terms of cost, flexibility, and ease of manufacturing compared to ceramic or metal substrates.
Silicon Interposers: A relatively newer technology, silicon interposers provide a high-density platform for integrating multiple semiconductor dies, enabling heterogeneous integration and improved performance in advanced packaging applications.
These are just a few examples of the diverse range of packaging substrates used in the electronics industry, each offering specific advantages and trade-offs depending on the application requirements.
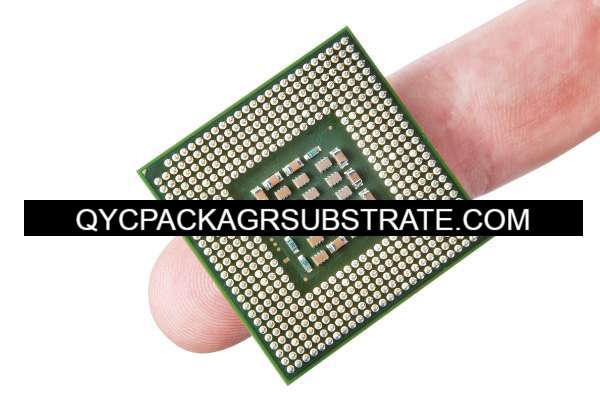
Top 10 Packaging Substrate Manufacturer
What are the functions of Top 10 Packaging Substrate?
The functions of the top 10 packaging substrates in electronic applications vary based on their material properties and specific use cases. Here’s a general overview of the functions they serve:
FR4: Provides mechanical support and electrical insulation for printed circuit boards (PCBs), facilitating the mounting and interconnection of electronic components.
Ceramic: Offers excellent thermal conductivity and electrical insulation, enabling efficient heat dissipation and high-frequency signal transmission in high-power and high-frequency applications.
Flexible PCBs: Enable the creation of flexible and lightweight electronic devices, allowing for compact designs, conformability to irregular shapes, and resistance to mechanical stress.
Metal-Core PCBs (MCPCB): Facilitate efficient heat dissipation from high-power electronic components, such as LEDs and power transistors, by providing a thermally conductive pathway to dissipate heat.
FR2: Provides a cost-effective alternative to FR4 for simpler electronic applications, offering basic electrical insulation and mechanical support for components.
Rigid-Flex PCBs: Enable the integration of rigid and flexible sections in electronic assemblies, allowing for three-dimensional designs, improved reliability, and reduced assembly complexity.
HDI PCBs: Accommodate higher circuit density and smaller components in electronic assemblies, enabling miniaturization, improved signal integrity, and enhanced electrical performance.
COB Substrates: Facilitate the integration of bare semiconductor chips into compact electronic packages, providing electrical interconnection and protection for the chips.
Organic Substrates: Offer a flexible and cost-effective platform for mounting and interconnecting electronic components, suitable for a wide range of consumer and industrial applications.
Silicon Interposers: Enable heterogeneous integration of multiple semiconductor dies, providing high-density interconnection and improved performance in advanced packaging applications such as 3D integrated circuits and system-in-package (SiP) designs.
Overall, these packaging substrates play critical roles in electronic device manufacturing, providing structural support, electrical insulation, thermal management, and interconnection for electronic components and circuits.
What are the different types of Top 10 Packaging Substrate?
The “Top 10 Packaging Substrates” encompass a variety of materials used in electronic packaging. Here’s a breakdown of the different types:
FR4: FR4 is a widely used epoxy-based laminate material with glass reinforcement, commonly used in printed circuit boards (PCBs) due to its excellent electrical insulation properties and affordability.
Ceramic: Ceramic substrates are known for their high thermal conductivity, low coefficient of thermal expansion (CTE), and excellent electrical properties. They are often used in high-power applications and environments requiring high reliability.
Flexible PCBs: Made of flexible plastic materials like polyimide or polyester, flexible PCBs offer advantages in terms of space-saving, lightweight design, and the ability to conform to complex shapes or bend during use.
Metal-Core PCBs (MCPCB): MCPCBs feature a layer of thermally conductive material (usually aluminum or copper) sandwiched between layers of insulating material. They are suitable for applications requiring efficient heat dissipation, such as LED lighting and power electronics.
FR2: FR2 is similar to FR4 but with phenolic resin instead of epoxy. It is a lower-cost alternative used in simpler electronic applications where less demanding electrical and thermal properties are acceptable.
Rigid-Flex PCBs: Rigid-flex PCBs combine elements of rigid and flexible PCBs, allowing for complex three-dimensional designs while maintaining structural integrity.
HDI PCBs: HDI PCBs accommodate higher circuit density and smaller components, featuring advanced technologies such as microvias, fine-pitch traces, and multiple layers to achieve compact designs and high signal integrity.
COB Substrates: COB substrates involve directly mounting bare semiconductor chips onto a substrate and wire bonding or encapsulating them to form a compact, cost-effective package.
Organic Substrates: Organic substrates use materials such as epoxy resin or polyimide, offering advantages in cost, flexibility, and ease of manufacturing compared to ceramic or metal substrates.
Silicon Interposers: Silicon interposers provide a high-density platform for integrating multiple semiconductor dies, enabling heterogeneous integration and improved performance in advanced packaging applications.
These substrates serve various functions in electronic packaging, including providing mechanical support, electrical insulation, thermal management, and interconnection for electronic components and circuits.
What is the relationship between Top 10 Packaging Substrate and IC packaging?
The relationship between the Top 10 Packaging Substrates and IC (Integrated Circuit) packaging is intertwined, as the substrates are essential components of IC packaging. IC packaging involves enclosing semiconductor devices (integrated circuits) in protective casings and providing electrical connections to the outside world. Packaging substrates form the foundation upon which these integrated circuits are mounted and interconnected. Here’s how they are related:
Mounting Surface: Packaging substrates serve as the mounting surface for the integrated circuit chips. The chips are attached to the substrate using various bonding techniques such as wire bonding, flip-chip bonding, or soldering.
Electrical Interconnection: The substrate provides the necessary electrical connections between the integrated circuit chip and the external world. This includes routing electrical signals between the chip and other components on the substrate, as well as providing connections for power and ground.
Thermal Management: Many packaging substrates, such as metal-core PCBs and ceramic substrates, are designed to facilitate efficient heat dissipation from the integrated circuit chip. Proper thermal management is crucial for maintaining the reliability and performance of the IC.
Mechanical Support: Packaging substrates provide mechanical support for the integrated circuit chip and other components mounted on the substrate. This support helps protect the chip from physical damage and ensures the integrity of the overall electronic assembly.
Miniaturization and Integration: Advanced packaging substrates, such as HDI PCBs and rigid-flex PCBs, enable miniaturization and integration of electronic components. This allows for the creation of smaller and more compact electronic devices, which is essential for many modern applications.
Overall, the choice of packaging substrate is critical in IC packaging design, as it directly impacts factors such as electrical performance, thermal management, reliability, and overall form factor of the integrated circuit package. Different types of packaging substrates are selected based on the specific requirements of the IC application, including factors such as operating environment, performance goals, cost considerations, and manufacturing constraints.
How does Top 10 Packaging Substrate differ from PCB?
The Top 10 Packaging Substrates and PCBs (Printed Circuit Boards) are closely related components in electronic device manufacturing, but they serve different purposes and have distinct characteristics. Here are the key differences between them:
Functionality:
Packaging Substrates: Packaging substrates primarily serve as the foundation for mounting and interconnecting semiconductor chips (integrated circuits) within electronic packages. They provide electrical connections, thermal management, and mechanical support for the chips.
PCBs: PCBs are used to mechanically support and electrically connect electronic components using conductive pathways etched from copper sheets laminated onto a non-conductive substrate. They provide the structural framework for mounting various components such as resistors, capacitors, and integrated circuits.
Component Mounting:
Packaging Substrates: Packaging substrates typically mount semiconductor chips using techniques like wire bonding, flip-chip bonding, or soldering directly onto the substrate.
PCBs: PCBs mount discrete electronic components onto their surface using soldering techniques. They also provide interconnection between these components through traces and pads.
Materials:
Packaging Substrates: Packaging substrates are often made of materials optimized for thermal management and electrical performance, such as ceramics, metal-core laminates, or organic substrates.
PCBs: PCBs are commonly made of materials like fiberglass-reinforced epoxy (FR4), which offer a good balance of electrical insulation, mechanical strength, and cost-effectiveness.
Design Complexity:
Packaging Substrates: Packaging substrates are designed to accommodate the specific requirements of the integrated circuit they house. They may include advanced features such as high-density interconnects (HDI), microvias, and thermal vias to optimize electrical and thermal performance.
PCBs: PCBs vary in complexity depending on the circuitry they support. They can range from simple single-layer boards to complex multi-layer boards with intricate routing and signal integrity considerations.
Usage:
Packaging Substrates: Packaging substrates are used in semiconductor packaging processes to create integrated circuit packages such as BGAs (Ball Grid Arrays), QFNs (Quad Flat No-leads), or flip-chip packages.
PCBs: PCBs are used in a wide range of electronic devices and systems, including computers, smartphones, automotive electronics, and industrial equipment, to provide the electrical connections and mechanical support necessary for circuit operation.
In summary, while both packaging substrates and PCBs are critical components in electronic device manufacturing, they have distinct roles, materials, and design considerations tailored to their specific functions within electronic assemblies.
What are the structure and production technology of Top 10 Packaging Substrate?
The structure and production technology of the Top 10 Packaging Substrates vary depending on the specific material and design requirements. Here’s an overview of the structure and production technologies commonly used for each type:
FR4:
Structure: FR4 substrates typically consist of layers of woven glass fabric impregnated with epoxy resin. Copper foils are bonded to both sides of the substrate, forming the conductive layers for electrical traces.
Production Technology: The production process involves laminating layers of glass fabric and epoxy resin under heat and pressure, followed by drilling, etching, and plating to create the desired circuit patterns.
Ceramic:
Structure: Ceramic substrates are composed of a ceramic material such as alumina (Al2O3) or aluminum nitride (AlN), which provides high thermal conductivity and electrical insulation. Metal layers are deposited onto the ceramic surface to form conductive traces.
Production Technology: Ceramic substrates are manufactured using processes such as tape casting, where a ceramic slurry is cast onto a tape, dried, and then sintered at high temperatures to form a dense ceramic substrate. Metal deposition techniques such as sputtering or screen printing are used to create the conductive traces.
Flexible PCBs:
Structure: Flexible PCBs are typically made of a flexible polymer material such as polyimide or polyester. Copper foils are laminated onto the polymer substrate to create conductive layers, and the board may have coverlay or solder mask applied for protection.
Production Technology: Flexible PCBs are manufactured using processes similar to rigid PCBs, including etching, plating, and solder mask application. However, additional steps such as laser cutting or mechanical milling may be used to shape the flexible substrate.
Metal-Core PCBs (MCPCB):
Structure: MCPCBs feature a layer of thermally conductive material (usually aluminum or copper) sandwiched between layers of insulating material such as FR4 or ceramic. Copper foils are bonded to the metal core to create conductive layers.
Production Technology: The production process involves laminating layers of insulating material and metal core under heat and pressure, followed by drilling, etching, and plating to create the circuit patterns.
FR2:
Structure: FR2 substrates are similar in structure to FR4, consisting of woven glass fabric impregnated with phenolic resin. Copper foils are bonded to both sides of the substrate to form conductive layers.
Production Technology: The production process for FR2 substrates is similar to FR4, involving lamination, drilling, etching, and plating to create the circuit patterns.
The production technologies for the remaining Top 10 Packaging Substrates, such as rigid-flex PCBs, HDI PCBs, COB substrates, organic substrates, and silicon interposers, involve similar processes of lamination, material deposition, drilling, etching, and plating, but with variations to accommodate the specific material properties and design requirements of each substrate type.
Frequently Asked Questions (FAQs)
What are Top 10 Packaging Substrates?
This refers to the most commonly used materials for packaging electronic components or devices. These substrates are chosen based on their electrical, thermal, mechanical, and cost-related properties.
What are the functions of Top 10 Packaging Substrates?
The functions vary based on the specific substrate, but generally include providing mechanical support, electrical insulation, thermal management, and interconnection for electronic components and circuits.
What are the different types of Top 10 Packaging Substrates?
Top 10 Packaging Substrates include FR4, ceramic, flexible PCBs, metal-core PCBs, FR2, rigid-flex PCBs, HDI PCBs, COB substrates, organic substrates, and silicon interposers.
How does Top 10 Packaging Substrate differ from PCB?
While both are critical in electronic device manufacturing, packaging substrates primarily serve as the foundation for mounting and interconnecting semiconductor chips, while PCBs support and connect discrete electronic components.
What is the relationship between Top 10 Packaging Substrate and IC packaging?
Packaging substrates are essential components of IC packaging, providing the foundation for mounting and interconnecting semiconductor chips within electronic packages.
What are the structure and production technology of Top 10 Packaging Substrate?
The structure and production technology vary depending on the specific substrate but generally involve processes such as lamination, etching, plating, and assembly, tailored to the material properties and design requirements of each substrate.
Conclusion
In conclusion, Top 10 Packaging Substrates are crucial components in electronic device manufacturing, providing the foundation for mounting, interconnecting, and protecting semiconductor chips within electronic packages. These substrates serve various functions such as mechanical support, electrical insulation, thermal management, and interconnection for electronic components and circuits.
The different types of Top 10 Packaging Substrates include FR4, ceramic, flexible PCBs, metal-core PCBs, FR2, rigid-flex PCBs, HDI PCBs, COB substrates, organic substrates, and silicon interposers. Each substrate type has unique characteristics and is selected based on specific application requirements.
While Top 10 Packaging Substrates are closely related to PCBs, they serve different purposes and have distinct design considerations. Packaging substrates primarily focus on housing and connecting semiconductor chips, whereas PCBs support and connect discrete electronic components.
Understanding the structure and production technology of Top 10 Packaging Substrates involves various processes such as lamination, etching, plating, and assembly, tailored to the material properties and design requirements of each substrate. Overall, these substrates play a critical role in the functionality, reliability, and performance of electronic devices across a wide range of industries.