Ultrathin IC/BGA Substrate Manufacturer
Ultrathin IC/BGA Substrate Manufacturer,Ultrathin IC/BGA Substrates are specialized components designed for high-density integrated circuit (IC) and Ball Grid Array (BGA) packaging. These substrates feature an exceptionally thin profile, optimizing space within electronic devices while maintaining structural integrity. Engineered with advanced materials like thin-film polymers or reinforced ceramics, they offer superior thermal management and electrical insulation properties crucial for IC operation. Ultrathin IC/BGA Substrates support miniaturization in modern electronics, such as smartphones, tablets, and wearable devices, where space constraints and thermal efficiency are paramount. Their precise manufacturing ensures reliable performance and signal integrity, making them essential for high-performance computing and mobile applications.
What is an Ultrathin IC/BGA Substrate?
Ultrathin IC/BGA substrates are an advanced electronic packaging technology primarily used for integrating circuits (ICs) and ball grid arrays (BGAs). These substrates are characterized by their thin profile, typically under 0.3 mm, making them ideal for space-constrained applications such as smartphones, tablets, and portable devices.
The manufacturing of ultrathin substrates employs high-precision printed circuit board (PCB) technology combined with multilayer structural designs, effectively supporting high-density routing and compact component placement. They are usually made from low dielectric constant materials to reduce signal delay and electromagnetic interference (EMI), thereby enhancing signal integrity. Additionally, the thermal management properties of ultrathin substrates are optimized to efficiently dissipate heat in high-power applications, ensuring chip stability under heavy loads.
The key advantages of these substrates lie in their lightweight nature and high performance, making them increasingly popular in modern electronic products. As electronic devices become smaller and more complex, ultrathin IC/BGA substrates play a crucial role in improving integration and reducing power consumption. Consequently, ultrathin substrates are widely used across various high-end electronic products, including high-performance computing, consumer electronics, and automotive electronics.
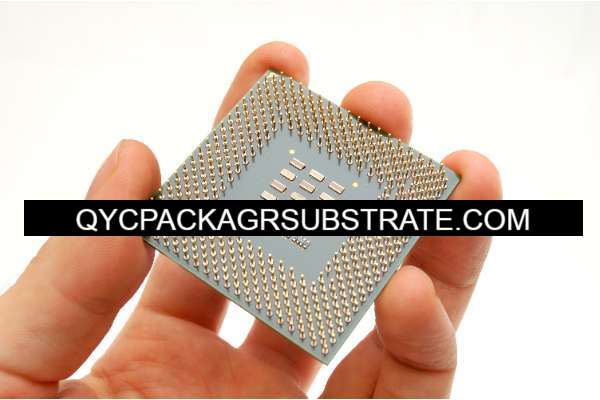
Ultrathin IC/BGA Substrate Manufacturer
What are the Ultrathin IC/BGA Substrate Design Guidelines?
Designing ultrathin IC/BGA substrates requires careful consideration of several key guidelines to ensure performance and reliability. Here are some important design guidelines:
- Material Selection: Choose low dielectric constant (low-k) materials to minimize signal loss and reduce crosstalk. Ensure materials have good thermal conductivity for effective heat dissipation.
- Layer Stack-Up: Optimize the layer stack-up to balance mechanical stability and electrical performance. Consider using a multilayer design that supports high-density interconnections.
- Trace Width and Spacing:Follow appropriate trace width and spacing rules to accommodate current carrying capacity and minimize impedance discontinuities. Use advanced routing techniques to manage tight spaces.
- Via Design:Utilize microvias and blind/buried vias to facilitate vertical connections in a compact layout. Ensure vias are appropriately sized to handle signal integrity and thermal performance.
- Thermal Management: Incorporate thermal vias and thermal pads to enhance heat dissipation from high-power components. Analyze thermal performance to prevent hotspots.
- Signal Integrity: Implement differential pairs for high-speed signals, maintaining consistent spacing and length. Use controlled impedance designs to ensure signal quality.
- Grounding and Power Distribution: Design a solid ground plane and effective power distribution network (PDN) to reduce noise and improve performance. Consider decoupling capacitors strategically placed close to power pins.
- Mechanical Support: Ensure adequate mechanical support to prevent warping or damage during manufacturing and assembly. Consider the impact of thinness on durability.
- Test Points:Include test pads or points for in-circuit testing to facilitate debugging and ensure manufacturing quality.
- Manufacturing Constraints:Work closely with manufacturers to understand their capabilities and constraints regarding ultrathin substrates, including minimum feature sizes and assembly processes.
By adhering to these guidelines, designers can optimize the performance and reliability of ultrathin IC/BGA substrates in various high-performance applications.
What is the Ultrathin IC/BGA Substrate Fabrication Process?
The fabrication process of ultrathin IC/BGA substrates involves several key steps to ensure high performance and reliability. Here’s an overview of the typical process:
- Material Selection: Begin with selecting appropriate substrates, usually made from low-k dielectric materials, which offer good electrical and thermal properties.
- Layer Preparation: Thin layers of the chosen material are prepared, often using processes such as lamination or coating. Multiple layers may be used to create a multilayer substrate.
- Photoresist Application: A photoresist layer is applied to the substrate surface. This layer is sensitive to UV light, allowing for patterning.
- Exposure and Development:The photoresist is exposed to UV light through a photomask, which defines the circuit pattern. The exposed areas are then developed, removing the photoresist to reveal the underlying substrate.
- Etching: Chemical etching or laser etching is used to remove unwanted material, creating the desired circuit pathways. This step is crucial for defining trace widths and spacing.
- Via Formation: Microvias are created using laser drilling or mechanical drilling techniques. These vias facilitate vertical connections between layers.
- Metal Deposition: A thin layer of metal (commonly copper) is deposited onto the substrate using methods like electroplating or sputtering. This metal layer forms the conductive traces.
- Surface Treatment: The substrate may undergo surface treatments to enhance adhesion and prepare for the next layer of photoresist or solder mask.
- Solder Mask Application: A solder mask is applied to protect the circuit traces and prevent solder from bridging during assembly. This is typically applied as a liquid and cured to form a solid layer.
- Final Inspection: The substrate undergoes thorough inspection for defects, ensuring it meets the required specifications before moving on to assembly.
- Assembly: The ultrathin substrates are populated with ICs and other components, typically using automated pick-and-place systems, followed by soldering processes such as reflow soldering.
- Testing: Final electrical testing is performed to ensure functionality and reliability, checking for signal integrity and thermal performance.
This meticulous fabrication process enables the production of high-density, high-performance ultrathin IC/BGA substrates suitable for various advanced electronic applications.
How do you manufacture an Ultrathin IC/BGA Substrate?
Manufacturing an ultrathin IC/BGA substrate involves several detailed steps, each critical to ensuring performance and reliability. Here’s a breakdown of the process:
- Material Selection: Choose low-k dielectric materials known for their excellent electrical and thermal properties. Common materials include specialized polymers or ceramic substrates.
- Substrate Preparation: Start with thin sheets of the selected material, typically less than 0.3 mm thick. These sheets are prepared through lamination or similar processes.
- Layering: For multilayer substrates, stack multiple thin layers of the dielectric material. This layering provides the necessary structural support and electrical pathways.
- Photoresist Application: Apply a thin layer of photoresist to the surface. This light-sensitive material will allow for patterning the circuitry.
- Exposure and Development: Expose the photoresist to UV light through a photomask, which defines the circuit layout. The exposed areas are then developed, removing the photoresist where needed.
- Etching: Use chemical or laser etching to remove excess material, creating the desired circuit patterns on the substrate.
- Via Formation: Create microvias using laser drilling techniques. These vias enable vertical connections between layers, essential for high-density designs.
- Metal Deposition: Deposit a thin layer of metal (usually copper) onto the substrate through electroplating or sputtering. This metal forms the conductive traces required for electrical connections.
- Surface Treatment: Perform surface treatments to enhance adhesion and prepare the substrate for subsequent layers like solder masks.
- Solder Mask Application: Apply a solder mask to protect the circuit traces and prevent solder bridging. This is typically cured to ensure a solid, protective layer.
- Final Inspection:Conduct thorough inspections to identify any defects, ensuring that the substrate meets quality standards.
- Component Assembly: Populate the substrate with ICs and other components using automated pick-and-place machines, followed by reflow soldering to secure connections.
- Testing: Perform final testing for electrical functionality and thermal performance, ensuring that the substrate operates reliably under expected conditions.
This comprehensive manufacturing process results in high-performance ultrathin IC/BGA substrates suitable for advanced electronic applications.
How much should an Ultrathin IC/BGA Substrate cost?
The cost of ultrathin IC/BGA substrates can vary widely based on several factors, including:
- Material Type: The choice of dielectric and metal materials can impact costs significantly. Low-k materials and specialized metals tend to be more expensive.
- Complexity and Design: More complex designs with tighter specifications, such as high-density routing and microvias, can increase manufacturing costs.
- Volume: Larger production volumes typically reduce the per-unit cost due to economies of scale.
- Manufacturing Technology: Advanced manufacturing processes, like laser drilling and multilayer stacking, may incur higher costs compared to traditional methods.
- Additional Features: Features like enhanced thermal management or specific surface treatments can add to the overall cost.
As a rough estimate, ultrathin IC/BGA substrates can range from $1 to $20 or more per unit, depending on the above factors. For precise pricing, it’s best to consult manufacturers based on specific design requirements and order quantities.
What is an Ultrathin IC/BGA Substrate base material?
An ultrathin IC/BGA substrate base material refers to the foundational material used to construct the substrate, which is typically designed for high-density and high-performance applications. The most common base materials include:
- Low-Dielectric Constant (Low-k) Materials: These materials reduce signal loss and crosstalk, enhancing signal integrity. Examples include specific polymers and composites.
- Ceramic Materials: Used for their excellent thermal stability and electrical properties, ceramics can withstand higher temperatures and are often used in advanced applications.
- Polyimide: A flexible material that provides good thermal and chemical resistance, polyimide is suitable for ultrathin applications.
- FR-4: While more common in standard PCBs, FR-4 can be used in ultrathin designs where lower performance specifications are acceptable.
These materials are chosen based on factors like thermal performance, electrical properties, mechanical strength, and the specific application requirements of the IC or BGA being used.
Which companies manufacture Ultrathin IC/BGA Substrates?
In the current electronics industry, many companies focus on manufacturing ultrathin IC/BGA substrates to meet the demands of high-performance and high-density packaging. Here are some well-known manufacturers:
- Nanya Technology: Based in Taiwan, Nanya Technology offers high-quality ultrathin substrates widely used in advanced integrated circuit packaging.
- TSMC (Taiwan Semiconductor Manufacturing Company): As a leading semiconductor foundry globally, TSMC excels in chip manufacturing and also provides packaging solutions that include ultrathin substrates, particularly for high-end applications.
- ASE Group: ASE is one of the largest semiconductor packaging and testing service companies in the world, and its ultrathin substrate products are well-regarded in the industry.
- Foxconn: A major player in electronics manufacturing, Foxconn’s subsidiaries are involved in the production of ultrathin substrates to meet the diverse needs of its extensive customer base.
- Xilinx: Specializing in high-performance programmable logic devices, Xilinx offers ultrathin substrate solutions that support complex packaging requirements.
These companies drive the advancement of ultrathin substrate technology through continuous research and innovation, catering to the growing market demands.
Our company also manufactures ultrathin IC/BGA substrates. We possess advanced technology and experience in this field, allowing us to provide high-quality, high-performance ultrathin substrate products. Our manufacturing process includes material selection, layer stacking, and micro-fabrication, ensuring that each product meets stringent industry standards.
Our ultrathin substrates are made from low-dielectric constant materials, offering excellent signal integrity and thermal management, making them ideal for applications in smartphones, tablets, and other high-end electronic devices. Additionally, we emphasize environmental protection in our manufacturing processes by using eco-friendly materials and practices to ensure sustainable development.
We also have an experienced technical team that can provide customized solutions based on specific customer requirements. Whether for small-batch production or large-scale manufacturing, we can respond flexibly, ensuring timely delivery and high quality.
In summary, our ultrathin IC/BGA substrate products will provide customers with higher integration and better performance, helping them stand out in a competitive market. We invite you to contact us for more information about the technology and applications of ultrathin substrates.
What are the 7 qualities of good customer service?
Good customer service is essential for building loyalty and satisfaction. Here are seven key qualities that characterize effective customer service:
- Responsiveness: Quickly addressing customer inquiries and issues shows that you value their time and concerns. Timely responses help build trust.
- Empathy: Understanding and relating to the customer’s feelings and experiences fosters a positive connection. Empathy helps in resolving issues more effectively.
- Knowledge: Well-trained staff who are knowledgeable about products or services can provide accurate information and solutions, enhancing the customer experience.
- Professionalism: Maintaining a courteous and respectful demeanor, even in challenging situations, reflects positively on the company and helps to de-escalate conflicts.
- Communication Skills: Clear and effective communication is vital. This includes listening actively, articulating responses well, and using positive language to ensure customers feel heard and understood.
- Problem-Solving Skills: The ability to identify issues and provide practical solutions is crucial. Good customer service representatives are proactive in finding ways to meet customer needs.
- Follow-Up: Checking in with customers after an issue has been resolved demonstrates commitment and care. It shows customers that their satisfaction is a priority.
These qualities collectively contribute to a positive customer experience, fostering long-term relationships and brand loyalty.
FAQs
What are ultrathin IC/BGA substrates?
Ultrathin IC/BGA substrates are advanced packaging materials designed for integrated circuits and ball grid arrays, typically less than 0.3 mm in thickness. They provide high-density interconnections and improved electrical performance.
What materials are used for ultrathin substrates?
Common materials include low-dielectric constant polymers, ceramics, and flexible materials like polyimide, which offer excellent thermal and electrical properties.
What are the advantages of using ultrathin substrates?
Advantages include reduced weight, improved signal integrity, better thermal management, and suitability for compact and high-performance electronic devices.
In which applications are ultrathin substrates used?
They are widely used in high-end electronics such as smartphones, tablets, wearables, automotive electronics, and high-performance computing.
How are ultrathin substrates manufactured?
The manufacturing process involves material selection, layering, photoresist application, etching, via formation, metal deposition, and assembly of components.
What are the design considerations for ultrathin substrates?
Design considerations include trace width, spacing, via size, thermal management, and ensuring signal integrity to meet high-performance requirements.
Are ultrathin substrates environmentally friendly?
Many manufacturers focus on using eco-friendly materials and processes to minimize environmental impact, aligning with sustainability goals.
How do I choose a supplier for ultrathin substrates?
Consider factors such as manufacturing capabilities, quality standards, experience, customer support, and the ability to meet specific design requirements.