Ultrathin PCB
Ultrathin PCB manufacturing, We offer the best thin 1 layer to 2 layer PCB with 3mil, 4mil, 5mil to 8mil. and the 4 layer to 6 layer PCB with 8mil to 12mil. or more big.we use the BT materials. it is rigid(hard) materials, we also has the flex materials. we can do the flex PCBs too.
Ultrathin PCBs, also known as ultrathin printed circuit boards, are specially designed circuit boards with an exceptionally slim profile, significantly thinner than standard PCBs. These boards are engineered to meet the demands of modern electronics, where space-saving and weight reduction are paramount.
Crafted from specialized materials such as flexible substrates or thin laminate materials, ultrathin PCBs offer unparalleled versatility in design and application. Their slim construction allows them to fit into compact electronic devices like smartphones, tablets, wearable gadgets, and medical implants, optimizing space utilization without compromising performance.
The manufacturing process of ultrathin PCBs involves precision techniques to achieve the desired thinness while maintaining robust electrical connectivity and mechanical stability. Despite their slender build, these boards exhibit remarkable durability and reliability, making them indispensable components in cutting-edge technology.
From consumer electronics to aerospace and medical industries, ultrathin PCBs play a crucial role in enabling innovative solutions that push the boundaries of what’s possible in the realm of electronics. With their sleek design and exceptional performance, ultrathin PCBs continue to drive advancements in electronics, shaping the future of technology.
What is an Ultrathin PCB?
An ultrathin PCB (Printed Circuit Board) is a type of PCB that is manufactured to be exceptionally thin, typically with a thickness significantly lower than standard PCBs. These boards are designed for applications where space constraints are critical, such as in compact electronic devices like smartphones, tablets, wearable devices, and other portable electronics.
The thickness of an ultrathin PCB can vary depending on the specific requirements of the application, but it is typically in the range of a fraction of a millimeter to a few millimeters. These boards are often made using specialized materials and manufacturing processes to achieve the desired thinness while still maintaining the necessary electrical and mechanical properties.
Ultrathin PCBs present unique design and manufacturing challenges due to their reduced thickness, such as handling delicate materials, managing heat dissipation, and ensuring mechanical stability. However, they offer advantages in terms of space-saving, weight reduction, and flexibility in design for products where every millimeter counts.
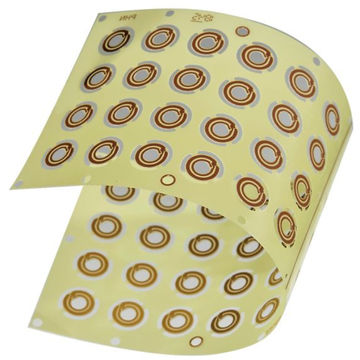
Ultrathin PCB
What are Ultrathin PCB Design Guidelines?
Designing ultrathin PCBs requires careful consideration of various factors to ensure reliable performance and manufacturability. Here are some general guidelines for designing ultrathin PCBs:
- Material Selection: Choose materials optimized for ultrathin PCBs, such as flexible substrates or thinner laminate materials with high dielectric strength. These materials should provide adequate electrical performance while maintaining flexibility and mechanical integrity.
- Layer Stackup: Keep the layer count to a minimum to reduce thickness. Consider using multilayer boards with thinner copper layers and thinner dielectric materials to achieve the desired thickness while maintaining signal integrity.
- Component Placement: Optimize component placement to minimize the overall footprint and ensure adequate clearance between components. Place components closer to the surface to reduce the overall thickness of the PCB.
- Trace Routing: Use thinner trace widths and spacings to conserve space and reduce impedance discontinuities. Implement controlled impedance routing techniques to maintain signal integrity, especially for high-speed signals.
- Via Design: Minimize the number of vias and use blind or buried vias where possible to reduce thickness and improve signal integrity. Avoid stubs in high-frequency circuits to minimize signal reflections.
- Mechanical Considerations: Consider the mechanical requirements of the application, such as bend radius and flexural strength, especially for flexible ultrathin PCBs. Reinforce areas prone to mechanical stress, such as connectors and mounting holes.
- Thermal Management: Ensure adequate thermal dissipation to prevent overheating, especially in densely packed designs. Use thermal vias and thermal pads to efficiently transfer heat away from critical components.
- Manufacturability: Work closely with PCB manufacturers to ensure that the design can be reliably manufactured with the desired thickness. Consider the limitations of the manufacturing process, such as minimum feature size and aspect ratio, and optimize the design accordingly.
- Testing and Validation: Perform thorough testing and validation of the ultrathin PCB design to verify electrical performance, mechanical robustness, and reliability under various operating conditions.
By following these guidelines, designers can create ultrathin PCBs that meet the requirements of compact electronic devices while ensuring reliable performance and manufacturability.
What is the Ultrathin PCB Fabrication Process?
The fabrication process for ultrathin PCBs shares similarities with standard PCB fabrication but often involves additional considerations to achieve the desired thinness. Here’s a general overview of the ultrathin PCB fabrication process:
- Design: The process begins with the design of the PCB layout using CAD (Computer-Aided Design) software. Design considerations for ultrathin PCBs, such as material selection, layer stackup, component placement, and trace routing, are taken into account during this stage.
- Material Selection: Specialized materials optimized for ultrathin PCBs are chosen, such as flexible substrates or thinner laminate materials with high dielectric strength. These materials should provide the necessary electrical performance while being thin and flexible.
- Preparation of Substrate: The chosen substrate material is prepared by cleaning and smoothing the surface to ensure proper adhesion of the copper layers.
- Copper Cladding: Thin copper foils are laminated onto the substrate using heat and pressure. The copper foils may be electroplated to achieve the desired thickness and copper distribution.
- Photoresist Application: A layer of photoresist is applied to the copper-clad substrate. The photoresist acts as a mask for the subsequent etching process.
- Exposure and Development: The PCB layout is transferred onto the photoresist layer using a photomask and exposure to UV light. After exposure, the unexposed areas of the photoresist are removed through a developing process, leaving behind the pattern of the PCB traces.
- Etching: The exposed copper areas not protected by the photoresist are etched away using an etchant solution, leaving only the desired copper traces on the substrate.
- Surface Finishing: Surface finishing processes such as solder mask application, silkscreen printing, and surface treatment (e.g., ENIG, HASL) are performed to protect the copper traces, provide insulation between conductive traces, and improve solderability.
- Drilling: Holes for component mounting and interconnection (vias) are drilled into the PCB using precision drilling machines. Laser drilling may be used for smaller holes in ultrathin PCBs.
- Plating and Plating Mask: Through holes and vias are plated with conductive material to ensure electrical continuity between layers. A plating mask is applied to define the areas where plating is required.
- Final Inspection: The finished ultrathin PCB undergoes thorough inspection to ensure it meets the required specifications for thickness, dimensions, electrical connectivity, and quality standards.
- Quality Control: Quality control measures are implemented throughout the fabrication process to identify and rectify any defects or inconsistencies.
The fabrication process may vary depending on the specific requirements of the ultrathin PCB and the capabilities of the PCB manufacturer. Collaboration between the design engineer and the manufacturer is essential to ensure the successful fabrication of ultrathin PCBs that meet the desired specifications and performance criteria.
How do you manufacture Ultrathin PCBs?
Manufacturing ultrathin PCBs involves specialized processes to achieve the desired thinness while maintaining electrical performance and reliability. Here’s a step-by-step overview of the manufacturing process for ultrathin PCBs:
- Material Selection: Choose specialized materials optimized for ultrathin PCBs, such as flexible substrates or thinner laminate materials with high dielectric strength. These materials should provide the necessary electrical properties while being thin and flexible.
- Preparation of Substrate: Clean and smooth the surface of the chosen substrate material to ensure proper adhesion of the copper layers. This may involve processes such as cleaning, surface treatment, and smoothing.
- Copper Cladding: Thin copper foils are laminated onto the substrate using heat and pressure. The copper foils may be electroplated to achieve the desired thickness and copper distribution. The thickness of the copper foil is crucial in achieving the overall thinness of the PCB.
- Lamination: If the ultrathin PCB requires multiple layers, the individual layers are laminated together using heat and pressure to form a single, unified structure. This process ensures proper alignment and bonding between the layers.
- Photoresist Application: A layer of photoresist is applied to the copper-clad substrate. The photoresist acts as a mask for the subsequent etching process.
- Exposure and Development: The PCB layout is transferred onto the photoresist layer using a photomask and exposure to UV light. After exposure, the unexposed areas of the photoresist are removed through a developing process, leaving behind the pattern of the PCB traces.
- Etching: The exposed copper areas not protected by the photoresist are etched away using an etchant solution, leaving only the desired copper traces on the substrate. Care must be taken to ensure uniform etching and avoid over-etching, which could compromise the thinness of the PCB.
- Surface Finishing: Surface finishing processes such as solder mask application, silkscreen printing, and surface treatment (e.g., ENIG, HASL) are performed to protect the copper traces, provide insulation between conductive traces, and improve solderability.
- Drilling: Holes for component mounting and interconnection (vias) are drilled into the PCB using precision drilling machines. Laser drilling may be used for smaller holes in ultrathin PCBs.
- Plating and Plating Mask: Through holes and vias are plated with conductive material to ensure electrical continuity between layers. A plating mask is applied to define the areas where plating is required.
- Final Inspection: The finished ultrathin PCB undergoes thorough inspection to ensure it meets the required specifications for thickness, dimensions, electrical connectivity, and quality standards.
- Quality Control: Quality control measures are implemented throughout the manufacturing process to identify and rectify any defects or inconsistencies.
Throughout the manufacturing process, precise control of parameters such as temperature, pressure, and chemical concentrations is essential to ensure the successful fabrication of ultrathin PCBs with the desired specifications and performance characteristics. Collaboration between the design engineer and the manufacturer is crucial to address any challenges and ensure the manufacturability of ultrathin PCBs.
How much should an Ultrathin PCB cost?
The cost of an ultrathin PCB can vary significantly depending on various factors, including the complexity of the design, the number of layers, the size of the board, the choice of materials, the manufacturing processes involved, and the quantity ordered. Here are some factors that can influence the cost of ultrathin PCBs:
- Design Complexity: More complex designs with intricate layouts, finer traces, and smaller components may require additional manufacturing steps and higher precision, leading to increased costs.
- Number of Layers: Ultrathin PCBs can be single-sided, double-sided, or multilayered. Multilayered boards with more layers generally cost more due to increased material and manufacturing complexity.
- Materials: Specialized materials optimized for ultrathin PCBs, such as flexible substrates or thinner laminate materials, may be more expensive than standard PCB materials.
- Manufacturing Processes: Certain manufacturing processes, such as laser drilling for small vias or specialized surface finishing techniques, may incur additional costs compared to standard processes.
- Size and Quantity: Larger boards or orders with higher quantities may benefit from economies of scale and lower per-unit costs.
- Lead Time: Expedited manufacturing or shorter lead times may incur additional charges.
- Quality Standards: Meeting specific quality standards or certifications may involve additional testing and verification processes, contributing to higher costs.
As a rough estimate, the cost of ultrathin PCBs can range from a few dollars to several hundred dollars per square inch, depending on the aforementioned factors. It’s essential to consult with PCB manufacturers and obtain quotes based on your specific requirements and volume needs to get an accurate cost estimate. Additionally, consider factors such as quality, reliability, and technical support when choosing a PCB manufacturer, as these can impact the overall value of the product.
What is Ultrathin PCB base material?
The base material for ultrathin PCBs typically consists of specialized substrates designed to be thin and lightweight while providing the necessary electrical and mechanical properties. Some common materials used for ultrathin PCBs include:
- Flexible Substrates: Flexible substrates, such as polyimide (PI) or polyester (PET), are often used for ultrathin PCBs that require flexibility or bendability. These materials offer good electrical insulation properties and can withstand high temperatures, making them suitable for applications where flexibility is important, such as wearable devices and flexible electronics.
- Thin Laminate Materials: Thinner laminate materials with high dielectric strength are used for ultrathin PCBs that require rigidity or stiffness while maintaining a low thickness. These materials may include thin FR-4 (a type of epoxy-based laminate) or other proprietary materials specifically designed for ultrathin PCB applications.
- Rigid-Flex Substrates: Rigid-flex PCBs combine rigid and flexible substrates in a single structure, allowing for both flexibility and rigidity in different areas of the board. Ultrathin rigid-flex PCBs use thin and lightweight materials for both the rigid and flexible portions of the board to achieve a low overall thickness.
- Metal Core Substrates: Metal core substrates, such as aluminum or copper-clad laminates, are used for ultrathin PCBs that require high thermal conductivity and heat dissipation. These substrates have a thin layer of metal sandwiched between layers of insulating material, providing excellent thermal performance while maintaining a low profile.
- Ceramic Substrates: Ceramic substrates, such as alumina (Al2O3) or aluminum nitride (AlN), are used for ultrathin PCBs that require high thermal conductivity, excellent electrical insulation, and resistance to high temperatures. These substrates are often used in high-power or high-frequency applications where heat dissipation is critical.
The choice of base material for ultrathin PCBs depends on the specific requirements of the application, including flexibility, rigidity, thermal performance, and electrical properties. Designers and engineers must carefully select the appropriate material to ensure the desired performance and reliability of the ultrathin PCB.
Which company manufactures Ultrathin PCBs?
There are many companies globally that manufacture Ultrathin PCBs (Printed Circuit Boards), and some of these companies specialize in producing Ultrathin PCBs to meet the increasing demands for space and weight reduction in electronic products. Some well-known Ultrathin PCB manufacturers include Foxconn Technology Group, Jabil Inc., and PCBWay (Shenzhen JLC Electronics Co., Ltd.), among others. These companies possess advanced technologies and equipment to meet various customer requirements for Ultrathin PCBs.
Representing our company, we are also one of the Ultrathin PCB manufacturers with extensive experience and expertise. We are committed to providing high-quality, reliable Ultrathin PCB solutions to our customers. Here are some advantages and features of our Ultrathin PCB manufacturing:
- Advanced Manufacturing Technology: We have advanced manufacturing equipment and technologies, including precision machining equipment, advanced material processing techniques, and strict quality control processes. This enables us to produce high-precision, high-quality Ultrathin PCBs.
- Diverse Material Selection: Our company can select materials suitable for various application scenarios according to customer requirements, including flexible substrates, thin laminate materials, metal core substrates, and others. We have a wide range of material selections to meet different design requirements.
- Customized Production Services: We can provide customized production services based on customer design requirements and specifications. Whether it’s single-sided, double-sided, or multilayer Ultrathin PCBs, we can produce according to customer needs and ensure that product quality and performance meet expectations.
- Strict Quality Control: We implement a strict quality control system, monitoring and inspecting every aspect of the production process from raw material procurement to production. We ensure that each batch of products meets customer requirements and standards to provide the highest quality Ultrathin PCB products.
In summary, as an Ultrathin PCB manufacturer, our company has extensive experience and expertise to provide high-quality, reliable Ultrathin PCB solutions to our customers. We are committed to collaborating with customers to drive innovation and development in electronic products.
What are the 7 qualities of good customer service?
Good customer service is essential for building strong customer relationships and fostering loyalty. Here are seven qualities that characterize good customer service:
- Responsiveness: Good customer service involves being prompt and proactive in addressing customer inquiries, concerns, and requests. Responding to customers in a timely manner demonstrates attentiveness and shows that their needs are valued.
- Empathy: Empathy is the ability to understand and share the feelings of customers. Good customer service representatives listen actively, show genuine concern for customers’ issues, and strive to put themselves in the customer’s shoes to provide personalized assistance.
- Professionalism: Professionalism encompasses qualities such as courtesy, respect, and integrity. Good customer service representatives maintain a professional demeanor at all times, communicate clearly and effectively, and uphold ethical standards in their interactions with customers.
- Knowledgeability: Good customer service requires having a deep understanding of the products or services offered, as well as company policies and procedures. Customer service representatives should be knowledgeable enough to provide accurate information, answer questions, and offer helpful guidance to customers.
- Flexibility: Good customer service involves being adaptable and flexible in addressing diverse customer needs and preferences. Customer service representatives should be willing to accommodate reasonable requests, explore alternative solutions, and go above and beyond to meet customer expectations.
- Problem-solving skills: Good customer service representatives possess strong problem-solving skills and are adept at resolving customer issues effectively and efficiently. They approach problems with a positive attitude, actively seek solutions, and follow through until the issue is fully resolved to the customer’s satisfaction.
- Consistency: Consistency is key to delivering good customer service across all interactions and touchpoints. Customers expect a consistent level of service quality regardless of when or how they engage with a company. Good customer service entails maintaining consistency in communication, standards, and service delivery to build trust and reliability with customers over time.
By embodying these qualities, companies can deliver exceptional customer service experiences that foster customer satisfaction, loyalty, and advocacy.
FAQs (Frequently Asked Questions)
What is an ultrathin PCB?
An ultrathin PCB is a type of printed circuit board that is manufactured to be exceptionally thin, typically with a thickness significantly lower than standard PCBs. These boards are designed for applications where space constraints are critical, such as in compact electronic devices like smartphones, tablets, and wearable devices.
What are the advantages of ultrathin PCBs?
Ultrathin PCBs offer several advantages, including space-saving, weight reduction, improved flexibility in design, and enhanced thermal management. They are particularly well-suited for applications where size and weight limitations are important considerations.
What materials are used in ultrathin PCBs?
Ultrathin PCBs can be made from a variety of materials, including flexible substrates like polyimide (PI) or polyester (PET), thin laminate materials with high dielectric strength, metal core substrates for enhanced thermal performance, and ceramic substrates for high-frequency applications.
What are the design considerations for ultrathin PCBs?
Designing ultrathin PCBs requires careful consideration of factors such as material selection, layer stackup, component placement, trace routing, mechanical stability, and thermal management. Designers must balance the requirements for thinness with the need to maintain electrical performance and reliability.
What manufacturing processes are involved in producing ultrathin PCBs?
The manufacturing process for ultrathin PCBs involves specialized processes to achieve the desired thinness while maintaining electrical performance and reliability. This process typically includes steps such as material preparation, copper cladding, photoresist application, etching, surface finishing, drilling, plating, and final inspection.
What are the applications of ultrathin PCBs?
Ultrathin PCBs are used in a wide range of applications, including smartphones, tablets, wearable devices, medical devices, aerospace and defense systems, automotive electronics, and IoT (Internet of Things) devices. Any application where space and weight are critical considerations can benefit from the use of ultrathin PCBs.
What are the challenges associated with ultrathin PCBs?
Despite their advantages, ultrathin PCBs present challenges such as handling delicate materials, managing heat dissipation, ensuring mechanical stability, and maintaining signal integrity. Designers and manufacturers must address these challenges to ensure the successful production and deployment of ultrathin PCBs.