Ultrathin Rigid PCB Manufacturer
Ultrathin Rigid PCB Manufacturer,Ultrathin Rigid PCBs are advanced circuit boards characterized by their exceptionally thin profile while maintaining rigidity and durability. These PCBs are crafted to be lightweight and compact, making them ideal for applications where space is limited, such as in smartphones, wearables, and other portable electronics. Despite their slim design, ultrathin rigid PCBs offer robust electrical performance and signal integrity. They are engineered with high-density interconnections and precise manufacturing techniques to ensure reliability and efficiency in compact electronic devices. Their innovative design helps meet the growing demand for miniaturized yet high-performance electronic solutions.
What is Ultrathin Rigid PCB?
Ultrathin rigid PCBs, or Printed Circuit Boards, are a type of circuit board characterized by their extremely thin profile combined with rigid properties. Unlike traditional PCBs, which are often several millimeters thick, ultrathin rigid PCBs typically have a thickness of less than 0.2 mm. Despite their slim design, they maintain structural rigidity, which makes them suitable for applications where space is at a premium, but a firm, stable substrate is necessary.
These PCBs are made using advanced manufacturing techniques that involve high precision in the deposition of copper layers and the etching process to achieve the desired thinness without compromising electrical performance or reliability. They often utilize high-performance materials, such as specialized laminates or composite materials, to ensure they can handle the electrical and thermal demands of modern electronics.
Ultrathin rigid PCBs are particularly valuable in sectors like consumer electronics, medical devices, and aerospace, where compact, lightweight designs are crucial. They can be used in applications such as smartphones, wearables, and other portable devices where saving space while maintaining durability and functionality is essential. Additionally, their rigid nature supports the reliable connection of electronic components and ensures that the PCB can withstand physical stresses and thermal cycling during operation.
Overall, ultrathin rigid PCBs represent a blend of advanced material science and precision engineering, meeting the evolving demands of modern electronics with a focus on both form factor and functionality.
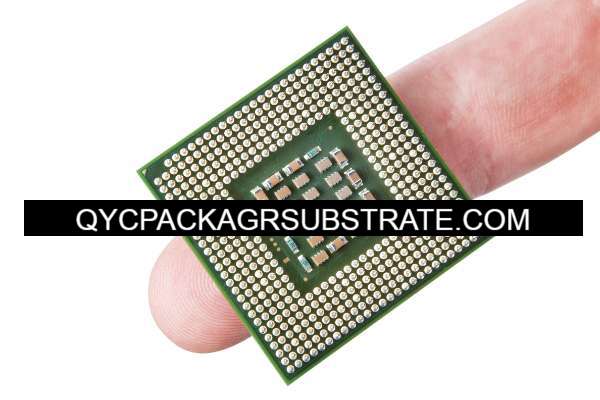
Ultrathin Rigid PCB Manufacturer
What are the Ultrathin Rigid PCB Design Guidelines?
Designing ultrathin rigid PCBs requires adherence to specific guidelines to ensure performance, reliability, and manufacturability. Here are key design guidelines for ultrathin rigid PCBs:
- Material Selection:Choose high-quality laminates and materials that support thin profiles without compromising mechanical strength and electrical performance. Materials like high-frequency FR-4 or polyimide are often used for their durability and electrical properties.
- Layer Stackup:Design the layer stackup to balance rigidity and signal integrity. Typically, an ultrathin PCB will have fewer layers compared to traditional PCBs. Carefully plan the layer sequence to ensure minimal signal loss and cross-talk.
- Trace Width and Spacing: Adjust trace widths and spacing to accommodate the thin profile. Ensure that traces are wide enough to handle the required current without excessive heat buildup and that spacing complies with manufacturing and electrical standards.
- Thermal Management:Incorporate effective thermal management strategies, as ultrathin PCBs can have limited heat dissipation capabilities. Use thermal vias, heat sinks, or copper planes to manage heat dissipation effectively.
- Via Design:Minimize the use of vias to reduce the thickness and potential for weak spots. When vias are necessary, use microvias or blind/buried vias to maintain the PCB’s thin profile and integrity.
- Component Placement:Carefully place components to optimize space usage and ensure proper clearance. Consider the height and footprint of components to avoid conflicts with the PCB’s thin profile.
- Signal Integrity:Address signal integrity issues by implementing appropriate routing techniques, such as controlled impedance traces and minimizing signal reflections and noise.
- Mechanical Strength:Design for mechanical robustness despite the thin profile. Ensure that critical areas of the PCB, such as mounting holes or connectors, are reinforced as needed.
- Testing and Quality Control:Implement rigorous testing procedures to ensure the ultrathin PCB meets performance standards. Conduct thorough inspections and functional tests to detect any potential issues early in the design phase.
By following these guidelines, designers can develop ultrathin rigid PCBs that achieve the desired balance between thickness, performance, and reliability, catering to the demands of modern electronic applications.
What is the Ultrathin Rigid PCB Fabrication Process?
The fabrication process for ultrathin rigid PCBs involves several specialized steps to ensure precision and performance while achieving the desired thin profile. Here is an overview of the ultrathin rigid PCB fabrication process:
- Material Preparation:Select and prepare high-quality laminate materials suitable for thin PCBs, such as advanced FR-4 or polyimide. Ensure that the chosen material supports the required electrical and mechanical properties.
- Layer Stackup: Define the layer stackup according to the design specifications. For ultrathin PCBs, this typically involves fewer layers. The stackup must be carefully planned to achieve the required electrical characteristics and mechanical rigidity.
- Photolithography:Apply a photoresist layer to the laminate and use photolithography to create the circuit patterns. This process involves exposing the photoresist to UV light through a mask that defines the circuit design. The exposed areas are then developed to reveal the copper underneath.
- Etching: Etch the exposed copper to form the circuit traces. The etching process removes unwanted copper, leaving behind the desired circuit patterns. Precision is crucial to ensure that the traces are accurately formed and maintain the required thickness.
- Drilling and Via Formation:Drill holes for vias and other through-hole components. For ultrathin PCBs, microvias or laser-drilled vias are often used to maintain the thin profile and ensure reliable electrical connections.
- Plating and Metallization: Plate the drilled vias and other exposed areas with a thin layer of metal, usually copper. This step involves electroplating or chemical deposition to ensure that the vias and pads have good electrical connectivity.
- Lamination: For multi-layer ultrathin PCBs, laminate the layers together using heat and pressure. This process bonds the layers and ensures structural integrity. Advanced lamination techniques are used to handle the thin profiles without causing warping or delamination.
- Surface Finish:Apply a surface finish to protect the PCB and ensure solderability. Common finishes include HASL (Hot Air Solder Leveling), ENIG (Electroless Nickel Immersion Gold), or immersion silver. The choice of finish depends on the specific application and performance requirements.
- Testing and Inspection:Conduct thorough testing and inspection to ensure that the ultrathin PCB meets all design specifications and quality standards. This includes electrical testing, visual inspection, and mechanical checks to identify any potential defects.
- Cutting and Shaping:Cut the PCB to the final dimensions and shape, ensuring that any mechanical features, such as mounting holes or slots, are accurately formed.
- Final Assembly: Assemble components onto the PCB using appropriate techniques, such as soldering or adhesive bonding. Ensure that the assembly process does not compromise the PCB’s thin profile or overall performance.
By following these steps, manufacturers can produce high-quality ultrathin rigid PCBs that meet the demanding requirements of modern electronic devices while maintaining precise dimensions and reliable performance.
How Do You Manufacture Ultrathin Rigid PCBs?
Manufacturing ultrathin rigid PCBs involves a series of specialized processes to ensure that the final product meets strict thickness, performance, and reliability standards. Here’s a step-by-step guide to the manufacturing process:
- Material Selection:Start with high-quality, thin laminate materials suitable for rigid PCBs, such as advanced FR-4, polyimide, or other specialized composites. The choice of material affects both the electrical performance and the mechanical properties of the PCB.
- Design and Layer Preparation:Create detailed PCB designs with precise specifications for layer stackup, trace widths, and spacing. For ultrathin PCBs, the design must account for minimal thickness while ensuring functionality. Prepare the laminate material according to the design requirements.
- Photolithography:Apply a thin layer of photoresist to the laminate. Using photolithography, expose the photoresist to UV light through a mask that represents the circuit pattern. Develop the exposed photoresist to reveal the underlying copper layer that will form the circuit traces.
- Etching:Perform etching to remove unwanted copper from the laminate, leaving behind the desired circuit patterns. For ultrathin PCBs, precise control of the etching process is crucial to achieve fine traces and maintain the thin profile.
- Drilling and Via Formation: Drill holes for vias and through-hole components using high-precision equipment. For ultrathin PCBs, microvias or laser drilling techniques are employed to minimize the impact on the PCB’s thickness while ensuring reliable electrical connections.
- Plating and Metallization: Plate the drilled vias and other exposed areas with a thin layer of metal, typically copper, through electroplating or chemical deposition. This process ensures that vias and pads have the necessary electrical conductivity and mechanical strength.
- Lamination:If the PCB is multi-layer, laminate the layers together using heat and pressure. For ultrathin PCBs, advanced lamination techniques are used to avoid warping and ensure that the layers adhere properly without compromising the thin profile.
- Surface Finish:Apply a surface finish to protect the PCB and improve solderability. Common finishes for ultrathin PCBs include HASL (Hot Air Solder Leveling), ENIG (Electroless Nickel Immersion Gold), or immersion silver, depending on the specific requirements of the application.
- Testing and Inspection: Conduct thorough testing and inspection to ensure the PCB meets design specifications and quality standards. This includes electrical testing to verify circuit functionality, visual inspection for defects, and mechanical checks for accuracy.
- Cutting and Shaping:Trim the PCB to its final dimensions and shape, including any necessary mechanical features such as mounting holes or slots. Precision cutting ensures that the PCB maintains its thin profile and functional integrity.
- Final Assembly:Assemble components onto the PCB using soldering or adhesive bonding techniques. Care must be taken to handle the ultrathin PCB carefully to avoid damage during the assembly process.
By adhering to these manufacturing steps, producers can create ultrathin rigid PCBs that are both high-performing and reliable, suitable for use in advanced electronic devices where space and thickness constraints are critical.
How Much Should Ultrathin Rigid PCB Cost?
The cost of ultrathin rigid PCBs can vary widely depending on several factors, including design complexity, material choice, quantity, and manufacturing processes. Here’s a general breakdown of factors influencing the cost:
- Material Costs:High-quality laminates and specialized materials used for ultrathin PCBs are more expensive than standard materials. The choice of material, such as advanced FR-4 or polyimide, impacts the overall cost.
- Design Complexity:More complex designs with intricate patterns, finer traces, and additional layers can increase the cost. The design needs to be optimized to balance performance and cost.
- Thickness and Layer Count:While ultrathin PCBs are defined by their thin profile, the specific thickness and number of layers will affect the cost. More layers or additional processing steps can increase the cost.
- Manufacturing Processes:The precision required for manufacturing ultrathin PCBs involves advanced processes such as microvia drilling, precise etching, and lamination. These specialized processes can add to the cost.
- Quantity:The cost per unit often decreases with larger production volumes due to economies of scale. Small quantities or prototypes may have a higher per-unit cost compared to larger production runs.
- Surface Finish:The choice of surface finish (e.g., ENIG, HASL, or immersion silver) affects the cost. High-quality finishes provide better performance but can be more expensive.
- Testing and Quality Control:Comprehensive testing and inspection processes ensure that the ultrathin PCBs meet quality standards, contributing to the overall cost.
- Lead Time:Rush orders or expedited manufacturing processes can increase the cost. Standard lead times typically cost less.
As a rough estimate, the cost for ultrathin rigid PCBs can range from $10 to $50 or more per unit, depending on the factors mentioned above. For high-volume orders or simpler designs, costs can be on the lower end, while custom or complex designs may be at the higher end.
For a more accurate quote, it’s advisable to contact PCB manufacturers with detailed specifications of your project. They can provide a tailored estimate based on your design requirements and production needs.
What is Ultrathin Rigid PCB Base Material?
Ultrathin rigid PCB base material is a specialized substrate used as the foundation for constructing ultrathin rigid PCBs. The choice of base material is crucial for achieving the desired thin profile while maintaining electrical performance and mechanical stability. Here are some commonly used base materials for ultrathin rigid PCBs:
- High-Frequency FR-4:Traditional FR-4 materials are often used, but for ultrathin designs, high-frequency variants are chosen. These materials are modified to support high-speed signal transmission while being available in thinner laminates.
- Polyimide:Polyimide is a high-performance polymer that provides excellent thermal stability, mechanical strength, and chemical resistance. It is well-suited for ultrathin PCBs due to its flexibility and durability, making it a popular choice for advanced electronics.
- Glass Epoxy Laminates:These laminates combine epoxy resin with glass fibers to offer high strength and durability while allowing for thinner profiles. They are used in applications where both rigidity and thinness are required.
- Ceramic Materials:Some ultrathin rigid PCBs use ceramic substrates, such as aluminum oxide or beryllium oxide, for applications that require high thermal conductivity and electrical insulation. These materials are rigid and provide excellent thermal management properties.
- Composite Materials: Advanced composite materials, such as those incorporating various resins and fillers, are used to achieve specific mechanical and electrical properties. These materials can be engineered to support very thin designs while maintaining performance.
- Polyester:Polyester-based materials are sometimes used for applications that do not require the high performance of FR-4 or polyimide. They are generally more cost-effective but may have limitations in terms of thermal stability and performance.
Each base material has its own set of properties that affect the overall performance of the ultrathin PCB, including electrical conductivity, thermal conductivity, mechanical strength, and flexibility. The choice of base material depends on the specific requirements of the application, such as operating frequency, environmental conditions, and mechanical stresses.
Which Company Makes Ultrathin Rigid PCBs?
Here are some companies that manufacture ultrathin rigid PCBs:
- AT&S: AT&S is a global leader in high-tech printed circuit board manufacturing, offering a range of high-performance PCB solutions, including ultrathin rigid PCBs. The company boasts advanced production facilities and technology to meet various complex design requirements.
- Unimicron:As a globally renowned PCB manufacturer, Unimicron provides ultrathin rigid PCB products used in consumer electronics, automotive electronics, and communication devices. The company has extensive experience and technical expertise in the field of ultrathin PCBs.
- Shenzhen Kinwong Electronic: Kinwong specializes in manufacturing various types of PCBs, including ultrathin rigid PCBs. The company is committed to providing high-quality, high-precision PCB solutions suitable for various electronic applications.
- Zhen Ding Technology:Zhen Ding is another company with strengths in the manufacturing of ultrathin rigid PCBs. The company has a solid technical foundation in PCB design and production, able to meet customized requirements from clients.
- Compeq Manufacturing: Compeq is a globally recognized PCB manufacturer whose products range from standard PCBs to high-frequency, high-speed, and ultrathin PCBs. The company also has capabilities and technical support in the field of ultrathin PCBs.
Our company can also manufacture ultrathin rigid PCBs. We have advanced manufacturing equipment and a skilled technical team capable of providing high-quality ultrathin rigid PCB solutions. Our production process includes precise photolithography, etching, microvia drilling, plating, lamination, and surface finishing, ensuring that each PCB meets strict design and quality standards. We can handle various materials and design requirements to meet customer needs in electronic products, whether in consumer electronics, medical devices, or high-tech communication products.
By combining advanced technology and extensive experience, we are dedicated to providing the best ultrathin rigid PCB products, ensuring their performance and reliability in various applications. No matter what your project needs are, we welcome you to contact us to discuss how we can tailor the most suitable PCB solutions for you.
What are the 7 Qualities of Good Customer Service?
Good customer service is essential for building strong customer relationships and ensuring customer satisfaction. Here are seven key qualities of excellent customer service:
- Responsiveness:Good customer service means being prompt in addressing customer inquiries, complaints, or requests. This involves responding quickly to communications, whether they are via phone, email, or social media, and taking immediate action to resolve issues.
- Empathy: Empathizing with customers means understanding their feelings, concerns, and perspectives. Demonstrating genuine care and concern for their situation helps build trust and shows that you value their experience.
- Knowledgeability:Customer service representatives should be well-informed about the products or services they support. This involves having a deep understanding of the offerings, policies, and procedures to provide accurate and helpful information.
- Patience:Handling customer interactions with patience, especially when dealing with difficult or frustrated customers, is crucial. Patience helps in addressing customer issues calmly and effectively, leading to better resolution outcomes.
- Communication Skills: Clear and effective communication is essential. This includes listening actively, speaking clearly, and providing information in a way that is easy for the customer to understand. Good communication also involves confirming that the customer’s needs have been fully addressed.
- Reliability: Consistency and dependability are key aspects of good customer service. This means following through on promises, meeting commitments, and providing reliable support. Customers should feel confident that they can rely on your service.
- Personalization:Tailoring the service experience to meet the specific needs and preferences of individual customers adds a personal touch. This involves recognizing returning customers, addressing them by name, and remembering their previous interactions or preferences.
By embodying these qualities, businesses can enhance their customer service, leading to increased customer satisfaction, loyalty, and positive word-of-mouth.
FAQs about Ultrathin Rigid PCBs
What are the benefits of Ultrathin Rigid PCBs?
They offer space-saving solutions without compromising on rigidity and durability.
What applications are suitable for Ultrathin Rigid PCBs?
Common applications include portable electronics, medical devices, and compact consumer products.
Can Ultrathin Rigid PCBs be custom designed?
Yes, they can be customized to meet specific design requirements and performance needs.
What are the challenges in manufacturing Ultrathin Rigid PCBs?
Challenges include maintaining rigidity while achieving thin profiles, and ensuring high reliability in compact designs.
How do I get a quote for Ultrathin Rigid PCBs?
Contact a manufacturer with your design specifications for an accurate quote based on your requirements.