WBPBGA Substrate Manufacturer
WBPBGA Substrate Manufacturer,WBPBGA Substrates combine wire bonding and plastic ball grid array technology, providing efficient packaging for semiconductor devices. These substrates feature precise wire bonding connections between the chip and the substrate, ensuring reliable electrical connections. With a compact design and excellent thermal management, WBPBGA substrates offer high-density integration and efficient heat dissipation. They find applications in various industries, including consumer electronics, telecommunications, automotive, and aerospace. With their cost-effectiveness and reliability, WBPBGA substrates play a crucial role in enabling advanced semiconductor devices.
What is a WBPBGA Substrate?
WBPBGA stands for Wire Bond Plastic Ball Grid Array, a type of integrated circuit packaging technology. This packaging method combines wire bonding and plastic ball grid array (PBGA) features to achieve efficient semiconductor device packaging.
In WBPBGA packaging, the semiconductor chip is first fixed onto a carrier with conductive pads, typically made of a substrate with high thermal conductivity, such as ceramic or high-density organic materials. The circuit points on the chip are connected to the corresponding solder pads on the substrate using gold or aluminum wires, a process known as wire bonding. This bonding technique ensures good electrical connections and is relatively cost-effective and efficient in the manufacturing process.
After completing the wire bonding, the chip and the connecting wires are encapsulated in a plastic material, usually epoxy resin, to protect the internal chip and connections from external environmental factors. Finally, a neatly arranged array of spherical conductive solder balls is attached to the bottom of the substrate, known as the ball grid array. These solder balls enable mechanical and electrical connections when the chip is mounted onto a circuit board.
WBPBGA packaging offers excellent electrical performance and thermal management. Its relatively mature production process makes it widely used in various consumer electronics and computing devices.
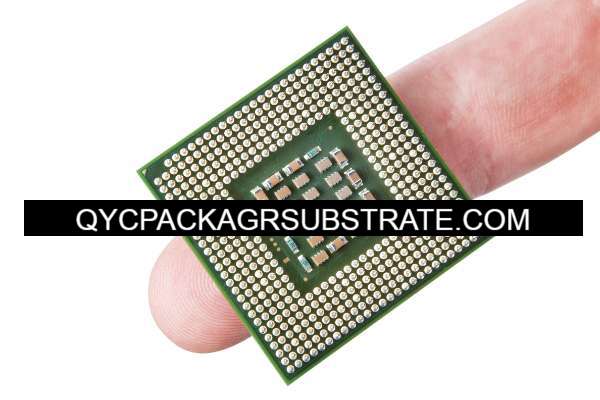
WBPBGA Substrate Manufacturer
What are the WBPBGA Substrate Design Guidelines?
The design guidelines for a Wire Bond Plastic Ball Grid Array (WBPBGA) substrate aim to optimize the substrate’s layout for durability, performance, and manufacturability. Here are some key guidelines typically followed when designing a WBPBGA substrate:
- Pad Design: The design of the pads on the substrate is crucial because they must align precisely with the wire bonding locations on the semiconductor die and the ball placements for the BGA. Pads should have a non-solder mask defined (NSMD) layout to minimize stress and prevent pad cratering under the solder balls.
- Trace and Space Widths: To ensure signal integrity and manufacturability, it is important to follow the minimum trace and space widths as recommended by the substrate manufacturer and relevant standards. This helps in avoiding issues like crosstalk and ensures the substrate can be reliably manufactured.
- Thermal Management: The substrate design should consider the thermal performance, especially in high-power applications. This can include the use of thermal vias under or near the chip, selecting materials with appropriate thermal conductivity, and considering the placement of heat sinks or other cooling mechanisms.
- Materials Selection: Choose materials that have adequate mechanical strength and good thermal properties. The coefficient of thermal expansion (CTE) should be closely matched to that of the silicon die to reduce stress during thermal cycling.
- Wire Bond Looping Profiles: The design must accommodate the physical constraints of wire bonding, including loop height and length. This ensures reliable connections without excessive stress on the wires, which could lead to failure.
- BGA Ball Map and Pitch: The arrangement and pitch of the BGA balls should be designed to balance between electrical performance and mechanical reliability. The pitch should allow for sufficient routing space for traces between the balls in high-density designs.
- Signal Integrity and Power Integrity: Design the substrate to minimize impedance discontinuities, provide adequate decoupling capacitors, and ensure a stable power supply to the die. This involves careful planning of the power and ground planes, as well as the placement and type of bypass/decoupling capacitors.
- Via Structures: Utilize appropriate via structures (through-hole, blind, or buried vias) depending on the layer count and signal integrity requirements. Vias help in connecting different layers of the substrate but can also impact the integrity of signals if not properly planned.
- Reliability Considerations:Include design features that address potential reliability issues such as via in pad, pad cratering, and stress on solder joints. This might involve using underfill materials, choosing robust pad structures, and conducting thorough reliability testing.
- Design for Testability (DFT): Ensure that the design includes features that facilitate testing of the integrated circuit post-packaging, such as test pads or probe points that are accessible without interfering with the function of the device.
Each of these guidelines helps in creating a robust, reliable, and efficient WBPBGA substrate that can effectively support the semiconductor devices it hosts. Adhering to these guidelines also ensures that the package can withstand the mechanical, thermal, and electrical stresses encountered during its operational life.
What is the WBPBGA Substrate Fabrication Process?
The fabrication process for a Wire Bond Plastic Ball Grid Array (WBPBGA) substrate involves several steps to create a robust substrate that can support the integration of semiconductor devices. Here’s a general overview of the fabrication process:
- Substrate Material Selection:The process starts with selecting a suitable substrate material, typically a high-density organic substrate or ceramic substrate. The choice of material depends on factors such as thermal performance, electrical properties, and cost.
- Preparation of Substrate: The substrate material is prepared by cleaning and surface treatment to ensure proper adhesion of subsequent layers and components.
- Lamination of Layers: Multiple layers of dielectric material are laminated onto the substrate material using a combination of heat and pressure. These layers form the insulating layers between conductive traces and provide structural support for the substrate.
- Circuit Patterning: A thin layer of conductive material, such as copper, is deposited onto the surface of the substrate using techniques like sputtering or electroplating. This conductive layer is then patterned using photolithography and etching processes to create the desired circuit traces and pad patterns.
- Via Formation: Vias, which are small holes that connect different layers of the substrate, are formed using drilling or laser ablation techniques. These vias allow electrical connections between different layers of the substrate.
- Surface Finish: The exposed copper surfaces are coated with a surface finish material to protect them from oxidation and facilitate soldering during the assembly process. Common surface finish options include electroless nickel immersion gold (ENIG) or hot air solder leveling (HASL).
- Solder Mask Application: A layer of solder mask material is applied over the substrate to define the areas where solder should be applied during the assembly process. This solder mask helps prevent solder bridging and ensures proper solder joint formation.
- Final Inspection and Testing: The fabricated substrate undergoes thorough inspection and testing to ensure that it meets the specified design requirements and quality standards. This may include visual inspection, dimensional measurement, electrical testing, and other quality control checks.
- Packaging and Shipping: Once the substrate passes inspection and testing, it is packaged and prepared for shipping to semiconductor assembly facilities where semiconductor chips will be mounted and wire bonded to the substrate.
Throughout the fabrication process, strict quality control measures are implemented to ensure the reliability and performance of the WBPBGA substrate. Any defects or deviations from the design specifications are identified and corrected to produce substrates that meet the required standards for semiconductor device integration.
How do you manufacture a WBPBGA Substrate?
Manufacturing a Wire Bond Plastic Ball Grid Array (WBPBGA) substrate involves a series of intricate processes that ensure the substrate’s integrity, functionality, and reliability. Here’s a step-by-step guide to the manufacturing process:
- Substrate Material Selection: The process begins with choosing a suitable substrate material based on the desired electrical, mechanical, and thermal properties. Common substrate materials include high-density organic substrates (e.g., FR-4) or ceramics (e.g., alumina or aluminum nitride).
- Substrate Preparation: The selected substrate material undergoes preparation, which typically involves cleaning and surface treatment to remove any contaminants and improve adhesion for subsequent layers.
- Layer Lamination: Multiple layers of dielectric material are laminated onto the substrate material. These layers provide insulation between conductive traces and structural support for the substrate.
- Conductor Patterning: A thin layer of conductive material, often copper, is deposited onto the surface of the substrate using techniques like sputtering or electroplating. This conductive layer is then patterned using photolithography and etching processes to create the desired circuit traces and pad patterns.
- Via Formation: Vias, which are small holes that connect different layers of the substrate, are formed using drilling, laser ablation, or other techniques. These vias allow for electrical connections between different layers of the substrate.
- Surface Finish: The exposed copper surfaces are coated with a surface finish material to protect them from oxidation and facilitate soldering during the assembly process. Common surface finish options include electroless nickel immersion gold (ENIG) or hot air solder leveling (HASL).
- Solder Mask Application: Alayer of solder mask material is applied over the substrate to define the areas where solder should be applied during the assembly process. This solder mask helps prevent solder bridging and ensures proper solder joint formation.
- Final Inspection and Testing: The fabricated substrate undergoes thorough inspection and testing to ensure that it meets the specified design requirements and quality standards. This may include visual inspection, dimensional measurement, electrical testing, and other quality control checks.
- Packaging and Shipping:Once the substrate passes inspection and testing, it is packaged and prepared for shipping to semiconductor assembly facilities where semiconductor chips will be mounted and wire bonded to the substrate.
Throughout the manufacturing process, stringent quality control measures are implemented to ensure the reliability and performance of the WBPBGA substrate. Any defects or deviations from the design specifications are identified and corrected to produce substrates that meet the required standards for semiconductor device integration.
How much should a WBPBGA Substrate cost?
The cost of a Wire Bond Plastic Ball Grid Array (WBPBGA) substrate can vary significantly depending on various factors such as:
- Material:The type of substrate material used (e.g., high-density organic substrate, ceramic) can greatly influence the cost. Ceramic substrates tend to be more expensive than organic substrates due to their higher thermal conductivity and reliability.
- Complexity: The complexity of the substrate design, including the number of layers, the density of traces and vias, and the size of the substrate, can impact the manufacturing cost. More complex designs typically require more materials and processing steps, leading to higher costs.
- Manufacturing Process: The specific manufacturing processes and technologies used to fabricate the substrate can affect the cost. Advanced processes and equipment may come with higher upfront costs but can result in higher yields and lower defect rates, ultimately reducing overall costs.
- Quality and Reliability Requirements: Substrates designed for high-reliability applications such as aerospace or automotive electronics may require additional testing, quality control measures, and certification, which can increase costs.
- Volume:The volume of substrates being produced also plays a significant role in determining the cost per unit. Higher volume production runs typically result in lower unit costs due to economies of scale.
- Supplier: Different suppliers may offer substrates at varying price points based on factors such as their manufacturing capabilities, location, and reputation in the industry.
Given these factors, it’s challenging to provide a specific cost for a WBPBGA substrate without more detailed information about the specific requirements and specifications of the substrate. However, you can expect the cost to range from a few dollars to tens or even hundreds of dollars per substrate, depending on the factors mentioned above.
What is WBPBGA Substrate base material?
The base material for a Wire Bond Plastic Ball Grid Array (WBPBGA) substrate can vary depending on the specific requirements of the application and the manufacturing process. However, some common base materials used for WBPBGA substrates include:
- High-Density Organic Substrates: These substrates are typically made of fiberglass-reinforced epoxy resin (FR-4) or other high-density organic materials. FR-4 substrates are widely used in electronics due to their relatively low cost, good electrical properties, and ease of fabrication.
- Ceramic Substrates: Ceramic substrates, such as alumina (Al2O3) or aluminum nitride (AlN), are preferred for applications that require high thermal conductivity, excellent mechanical stability, and reliability under harsh operating conditions. Ceramic substrates are commonly used in high-power and high-frequency applications.
- Metal Core Substrates: Metal core substrates, often made of aluminum or copper, feature a metal core sandwiched between layers of dielectric material. These substrates offer superior thermal conductivity compared to traditional organic substrates, making them suitable for applications that require efficient heat dissipation.
- Flexible Substrates: In some cases, flexible substrates made of polyimide or other flexible materials may be used for WBPBGA applications where flexibility and bendability are required, such as in wearable electronics or flexible displays.
The choice of base material depends on factors such as thermal management requirements, electrical performance, cost considerations, and the specific needs of the application. Each type of substrate material has its advantages and limitations, and selecting the appropriate material is crucial to ensure the reliability and performance of the WBPBGA package.
Which company manufactures WBPBGA Substrates?
Many companies manufacture WBPBGA (Wire Bond Plastic Ball Grid Array) substrates, including semiconductor packaging manufacturers, PCB (Printed Circuit Board) manufacturers, and companies specializing in substrate production. Some well-known companies include TSMC, Intel, Samsung, ASE, Amkor Technology, Unisem, and more. These companies typically have advanced manufacturing equipment and technologies to meet various WBPBGA substrate manufacturing needs and have rich experience and expertise in semiconductor packaging and electronics manufacturing.
Our company also manufactures WBPBGA substrates. We have advanced manufacturing equipment and a skilled technical team capable of providing high-quality, reliable WBPBGA substrates to meet our customers’ custom requirements. We prioritize quality control and customer satisfaction, committed to providing customers with the best products and services. Our manufacturing processes strictly adhere to international standards and industry best practices, ensuring that each WBPBGA substrate meets specifications and operates reliably and consistently.
With experienced engineers and technical staff, we collaborate closely with customers to understand their needs and provide customized solutions. Whether customers require high-performance high-density organic substrates, excellent thermal management capabilities, or applications involving special materials, we can meet their requirements and provide professional technical support and after-sales service.
In summary, our company has the technology and resources to manufacture WBPBGA substrates and is committed to providing customers with high-quality products and services. If you have any needs or questions regarding WBPBGA substrate manufacturing, please feel free to contact us, and we will be happy to assist you.
What are the qualities of good customer service?
Good customer service is characterized by several key qualities that ensure customers feel valued, heard, and satisfied with their experience. Some of these qualities include:
- Responsive: Good customer service is prompt and responsive to customer inquiries, concerns, and feedback. This means acknowledging customer inquiries in a timely manner and providing helpful assistance or solutions promptly.
- Empathetic: Empathy is essential in understanding and addressing customer needs and concerns. Good customer service representatives show empathy by actively listening to customers, acknowledging their feelings, and demonstrating understanding and compassion.
- Knowledgeable: Customer service representatives should have a thorough understanding of the products or services offered by the company. They should be able to answer customer questions accurately, provide relevant information, and offer helpful recommendations or solutions.
- Professionalism: Professionalism is crucial in maintaining a positive impression of the company and building trust with customers. Good customer service representatives conduct themselves in a courteous, respectful, and professional manner at all times, even in challenging situations.
- Effective Communication: Effective communication is key to providing good customer service. This includes clear and concise communication, active listening, asking clarifying questions, and ensuring that customers understand the information provided.
- Problem-solving Skills: Good customer service involves effectively resolving customer issues and problems. Customer service representatives should be proactive in identifying and addressing customer concerns, finding solutions, and following up to ensure customer satisfaction.
- Flexibility and Adaptability: Every customer interaction is unique, and good customer service requires flexibility and adaptability to meet individual customer needs and preferences. Customer service representatives should be able to adjust their approach and communication style based on the situation and the customer’s personality.
- Consistency: Consistency is important in delivering a positive customer service experience. Customers expect consistent levels of service quality and treatment across all interactions and touchpoints with the company.
- Follow-up and Follow-through:Good customer service doesn’t end with the resolution of a customer issue. Follow-up and follow-through are essential in ensuring customer satisfaction and building long-term relationships. This includes checking in with customers after a resolution, addressing any remaining concerns, and proactively seeking feedback to improve future interactions.
- Customer-centric Approach:Ultimately, good customer service is centered around the customer. It involves prioritizing customer needs and satisfaction, anticipating their needs, and going above and beyond to exceed their expectations whenever possible.
By embodying these qualities, companies can deliver exceptional customer service that fosters loyalty, positive word-of-mouth, and long-term success.
FAQs
What is a WBPBGA substrate?
A WBPBGA substrate is a type of integrated circuit packaging technology that combines wire bonding and plastic ball grid array (PBGA) features. It is used to encapsulate semiconductor chips and provide electrical connections between the chip and the printed circuit board (PCB).
What are the advantages of WBPBGA substrates?
WBPBGA substrates offer several advantages, including high-density packaging, good electrical performance, efficient heat dissipation, and cost-effectiveness compared to other packaging technologies.
What are the main components of a WBPBGA substrate?
The main components of a WBPBGA substrate include the substrate material (e.g., organic or ceramic), conductive traces, solder pads for wire bonding, solder mask, and ball grid array (BGA) solder balls.
How are WBPBGA substrates manufactured?
The manufacturing process for WBPBGA substrates involves several steps, including substrate material selection, layer lamination, conductor patterning, via formation, surface finish application, solder mask application, final inspection, and testing.
What are the key design considerations for WBPBGA substrates?
Key design considerations for WBPBGA substrates include pad design for wire bonding, trace and space widths, thermal management, materials selection, wire bond looping profiles, BGA ball map and pitch, signal integrity and power integrity, via structures, and reliability considerations.
What are the applications of WBPBGA substrates?
WBPBGA substrates are used in a wide range of applications, including consumer electronics, telecommunications, automotive electronics, industrial automation, medical devices, and aerospace systems.
What factors affect the cost of WBPBGA substrates?
The cost of WBPBGA substrates can vary depending on factors such as substrate material, complexity of design, manufacturing process, quality and reliability requirements, volume of production, and supplier.
Where can I find suppliers of WBPBGA substrates?
Suppliers of WBPBGA substrates include semiconductor packaging manufacturers, PCB manufacturers, and companies specializing in substrate production. Some well-known suppliers include TSMC, Intel, Samsung, ASE, Amkor Technology, and Unisem.