Wire Bonding Package Substrate Manufacturer, we mainly produce ultra-small bump pitch packaging substrate, ultra-small trace and spacing packaging substrate and microtrace HDI PCBs.
In the intricate landscape of semiconductor packaging, the wire bond substrate emerges as a linchpin, particularly in the sophisticated assembly of integrated circuits (ICs) and diverse electronic components. Wire bonding, a prevalent technique in the semiconductor sphere, strategically weaves connections between the internal circuitry of a semiconductor device and its external leads or terminals.
Within the tapestry of wire bonding, the substrate assumes a pivotal role as a foundational scaffold, providing the structural backbone for mounting and interconnecting a myriad of components within an electronic device. Material options for the substrate span ceramics, organic materials, or metal alloys, with the selection process finely tuned to the nuanced requirements of the specific application.
The wire bonding choreography unfolds with the intricate dance of thin wires, often composed of aluminum or gold, delicately crafting electrical connections. These connections artfully manifest either between the semiconductor die and the substrate or among distinct components artfully positioned on the substrate. The resulting interlacing of wire bonds forms a network of critical electrical pathways, facilitating the harmonious transmission of signals and power throughout the electronic device.
The decision matrix governing wire bond substrate material and the specific wire bonding technique encompasses a spectrum of considerations—device type, targeted electrical performance, thermal dynamics, and cost parameters. In essence, wire bonding stands as an artful method in semiconductor packaging, contributing to the symphony of creating resilient electrical connections within the confines of compact electronic devices.
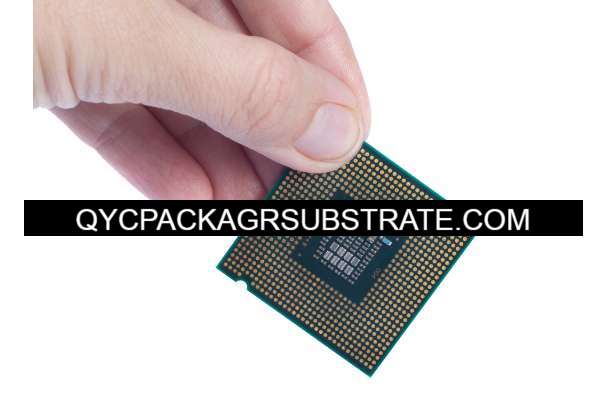
What functions does Wire Bonding package Substrate serve?
In the intricate landscape of semiconductor packaging, wire bond substrates emerge as versatile components, seamlessly performing a range of vital functions that collectively shape the effectiveness of electronic devices:
Foundational Strength: As a robust base, wire bond substrates provide essential mechanical support for securely housing semiconductor components. This foundational role is pivotal in upholding the structural integrity of electronic devices.
Central Hub for Connectivity: Positioned as a central nexus, these substrates facilitate a dynamic network of interconnections among diverse semiconductor components and external leads or terminals. This central hub ensures the creation of efficient electrical pathways, enabling smooth signal and power transmission.
Dynamic Thermal Regulation: Engaging actively in thermal management, wire bond substrates assist in the effective dissipation of heat generated by electronic components. This active involvement is indispensable for preventing overheating and ensuring the enduring performance and reliability of semiconductor devices.
Guardians of Electrical Isolation: Crafted from insulating materials like ceramics or specific organics, substrates act as a protective shield against unintended electrical connections. This safeguard guarantees robust electrical isolation between different components, ensuring flawless functionality.
Secure Platform for Die Attachment: Functioning as a secure platform, the substrate facilitates the stable attachment of the semiconductor die or integrated circuit. This secure anchoring is vital for maintaining precise alignment and continuous electrical connectivity.
Environmental Safeguard: Wire bond substrates operate as shields, providing protection against external elements such as moisture, dust, and contaminants. This protective role significantly contributes to the overall reliability and durability of electronic devices.
Contributors to Compact Design: Through meticulous material selection, wire bond substrates play a pivotal role in reducing the overall size and weight of electronic devices. This aspect is particularly critical in applications where stringent space and weight constraints dictate design considerations.
The specific roles and contributions of wire bond substrates vary based on the nuanced characteristics of the device, chosen materials, and the comprehensive design principles guiding semiconductor packaging.
What are the different types of Wire Bonding Substrate?
In the microelectronics domain, a diverse spectrum of substrates comes into play for wire bonding, facilitating the connection of semiconductor devices like integrated circuits (ICs) to their packages or within the components of a package. The selection of wire bond substrates is intricately tied to the distinctive demands and applications in play. Here’s a glimpse into some prevalent substrate types:
Aluminum Oxide (Alumina): Alumina, a frequently tapped ceramic material, assumes the role of a wire bonding substrate owing to its commendable thermal conductivity and electrical insulation properties.
Aluminum Nitride (AlN): Parallel to alumina, aluminum nitride emerges as another commonly employed ceramic substrate for wire bonding, marked by superior thermal conductivity suitable for applications mandating efficient heat dissipation.
Ceramic Multilayer Substrates: Crafted by layering multiple ceramic sheets, often incorporating materials like alumina and aluminum nitride, these substrates facilitate intricate circuit designs while maintaining a harmonious blend of electrical and thermal attributes.
Polyimide: In situations necessitating flexibility, polyimide, a malleable polymer material, steps in as a wire bonding substrate. It finds prevalent usage in flexible circuits and is esteemed for its thermal resilience.
Printed Circuit Boards (PCBs): Conventional PCBs double up as wire bond substrates. Fabricated from insulating materials like FR-4 or alternative laminates, these boards play host to wire bonds connecting to designated pads.
Ceramic on Metal (CoM): Introducing a layer of ceramic material onto a metal substrate is an approach where the electrical and thermal properties of ceramics seamlessly integrate with the mechanical robustness of metals.
Ceramic on Insulator (CoI): Similar to CoM, this substrate variant involves a slim layer of ceramic material atop an insulating base, providing a tailored amalgamation of properties for specific applications.
The substrate preference pivots on factors such as thermal requisites, electrical insulation, mechanical robustness, and the unique specifications of the application. Distinct manufacturing methodologies and materials come into play during substrate creation, with the ultimate choice being steered by the performance and reliability imperatives of the electronic device.
What is the relationship between Wire Bonding packaging Substrate and IC packaging?
The interplay between wire bond substrates and integrated circuit (IC) packaging is fundamental to the construction and functionality of semiconductor devices. In the realm of IC packaging, wire bond substrates assume pivotal roles that shape the overall performance of electronic components:
Foundation for Connection: Wire bond substrates serve as the bedrock upon which semiconductor dies are securely mounted. Through wire bonding techniques, electrical connections are meticulously established between the semiconductor die and the substrate. These wire bonds form the essential conduits for the transmission of signals and distribution of power within the IC.
Electrical Networking: Beyond connecting the die to the substrate, wire bond substrates foster electrical connectivity between diverse components on the substrate itself. This intricate networking is a linchpin for the comprehensive functionality of the integrated circuit, facilitating the seamless flow of signals across its various elements.
Heat Dissipation Role: Efficient thermal management is a critical facet of IC packaging. Wire bond substrates, influenced by their material composition, actively contribute to the dissipation of heat generated by semiconductor components. This thermal regulation is indispensable for preventing overheating and ensuring the sustained reliability of the IC.
Material Dynamics: The choice of material for wire bond substrates is a pivotal decision guided by the specific needs of the IC and its intended application. Materials ranging from ceramics to organic compounds or metal alloys offer diverse thermal, electrical, and mechanical properties, influencing the performance of the packaged IC.
Package Diversity: The type of IC package closely correlates with the use of wire bond substrates. Traditional packages like dual in-line packages (DIP) or quad flat packages (QFP) commonly employ wire bond substrates. While advanced packaging technologies may utilize alternative interconnection methods, the foundational role of the substrate remains central.
Environmental Safeguarding: Wire bond substrates act as protectors, shielding semiconductor components from external elements such as moisture, dust, and contaminants. This protective function significantly enhances the reliability and longevity of the IC, especially in diverse environmental conditions.
In essence, the intricate dance between wire bond substrates and IC packaging is symbiotic, with the characteristics and design of the substrate playing a pivotal role in shaping the overall functionality and reliability of the integrated circuit.
What are the differences between Wire Bond Substrate and traditional PCBs?
Wire bond substrates and traditional printed circuit boards (PCBs) navigate distinct realms within the electronics ecosystem, each bearing a unique imprint. Let’s explore the subtle differentiations between these two:
Targeted Utility:
Wire Bond Substrates: Meticulously tailored for the realm of semiconductor packaging, where their prowess lies in anchoring semiconductor dies and intricately weaving electrical connections within integrated circuits.
Traditional PCBs: Embrace a broader canvas, finding purpose across an array of electronic devices. They act as versatile stages for hosting an ensemble of components, from humble resistors to sophisticated integrated circuits.
Mounting Choreography:
Wire Bond Substrates: Choreographed for the artistry of semiconductor die mounting, employing wire bonding techniques to orchestrate connections with finesse.
Traditional PCBs: Exhibit adaptability, accommodating diverse electronic components through the flexible choreography of methods such as surface-mount technology (SMT) and through-hole technology (THT).
Material Symphony:
Wire Bond Substrates: Crafted from a palette of materials – ceramics, organics, or metal alloys – chosen strategically to compose thermal, electrical, and mechanical symphonies tailored for the intricacies of semiconductor packaging.
Traditional PCBs: Often find their notes in fiberglass-reinforced epoxy laminates (FR-4), renowned for the harmonious electrical insulation they provide.
Interconnection Ballet:
Wire Bond Substrates: Take center stage with the grace of wire bonding, where slender wires of aluminum or gold pirouette to form intricate electrical connections within the substrate.
Traditional PCBs: Engage in the dance of copper traces, vias, and soldered joints, orchestrating interconnections that resonate across a diverse ensemble of electronic components.
Domain Choreography:
Wire Bond Substrates: Flourish in the specialized theatres of semiconductor and microelectronics, where their performance shines in the delicate balance of compact dimensions, precise connectivity, and efficient heat dissipation.
Traditional PCBs: Showcase versatility on a grand stage, playing a role in the opus of consumer electronics, industrial machinery, automotive orchestras, and more.
Architectural Sonata:
Wire Bond Substrates: Often compose intricate layers, akin to a sonata, navigating the complexities of interconnections within integrated circuits.
Traditional PCBs: Sweep across a spectrum, from the simplicity of single-layer compositions to the grandeur of multi-layered symphonies, adapting seamlessly to the intricate demands of electronic systems.
Flexibility Waltz:
Wire Bond Substrates: Waltz through a spectrum of flexibility, from the rigid embrace to the nuanced adaptability, with variants tailored for the dynamic demands of flexible electronics.
Traditional PCBs: Engage in a waltz of versatility, offering options for rigid, flexible, or hybrid designs, allowing for bespoke solutions crafted to the rhythm of specific applications.
In essence, as both wire bond substrates and traditional PCBs take their place on the electronic stage, their unique choreography, orchestrated with materials, interconnections, and flexibility dynamics, tells a tale that resonates across diverse applications and design landscapes.
What is the structural composition and manufacturing techniques of Wire Bond Substrate?
In the realm of electronics, wire bond substrates emerge from a symphony of materials and manufacturing intricacies, each contributing to the substrate’s structural form and functional finesse. Let’s embark on a journey through the composition and crafting techniques that breathe life into these substrates:
Structural Ensemble:
Foundational Tapestry:
Wire bond substrates find their essence in a carefully curated selection of materials. Whether it’s the sturdiness of ceramics like alumina, the adaptability of organic compounds such as epoxy resins, or the flexibility of polymers, the choice sets the stage.
Conductive Threads:
Integral to the substrate’s fabric are conductive layers, often woven with metals like copper or aluminum. These layers act as the architectural backbone, crafting electrical pathways and facilitating the intricate interplay among semiconductor components.
Insulating Layers:
Balancing the conductivity dance are layers of insulation. Materials like silicon dioxide join the narrative, ensuring a harmonious electrical isolation between different layers and components, enhancing the substrate’s resilience.
Surface Embellishments:
The substrate’s exterior undergoes thoughtful embellishments, adorned with coatings or materials that elevate specific characteristics. Whether it’s a nod to solderability, resilience against corrosion, or a shield against the elements, each finish tells a story.
Crafting Techniques:
Genesis of Substrate:
The substrate’s origin story unfolds with its formation – a tale told through molding, deposition, or the layering dance of lamination. The base material takes shape, ready for the subsequent narrative.
Layer Artistry:
Layers of conductivity and dielectric prowess grace the substrate, painted onto the canvas through techniques like thin-film deposition. This layering sets the stage, establishing the groundwork for the substrate’s electrical pathways.
Photolithographic Symphony:
The play of light and pattern begins, orchestrated by photolithography. Photoresist material, exposed and developed, sculpts the substrate, leaving behind intricate circuit patterns. The etching finale refines the substrate’s artistic form.
Metalization Ballet:
Metalization takes center stage, as a thin layer of metal, often copper, is delicately deposited. The subsequent etching ballet defines the conductive pathways, allowing them to dance in harmony.
Die Attachment and Wire Bonding Choreography:
The semiconductor dies take their positions through meticulous die attach techniques, ensuring a seamless alignment. The wire bonding choreography commences, with fine wires of aluminum or gold elegantly connecting semiconductor components to their designated pads.
Encapsulation Overture:
A protective overture unfolds as the wire-bonded substrate is encapsulated. Whether through molding or the embrace of encapsulation resins, a protective layer is woven around the delicate components.
Surface Finishing Flourish:
The final act brings surface finishing into focus. Protective films, solder masks, or bespoke finishes grace the substrate, adding the finishing touches and preparing it for its role in the grand electronic narrative.
In this symphony of materials and techniques, wire bond substrates emerge as crafted ensembles, ready to play their part in the intricate ballet of semiconductor packaging.
FAQs for Wire Bond Substrate Manufacturers
Can You Outline the Manufacturing Process of Wire Bond Substrates?
The manufacturing journey of wire bond substrates encompasses substrate formation, layer deposition using techniques like thin-film deposition, photolithography for precise patterning, metalization, die attachment, wire bonding, encapsulation, and surface finishing. The specific steps can vary based on design requirements and material choices.
In Which Applications Are Wire Bond Substrates Primarily Applied?
Wire bond substrates find prominence in semiconductor and microelectronic applications, where compact dimensions, precise electrical connections, and efficient heat dissipation are paramount. They serve as essential components in various electronic devices.
Could You Provide Insights into the Different Varieties of Wire Bond Substrates?
Wire bond substrates exhibit diversity in types based on materials, designs, and intended applications. Common varieties include ceramic substrates, organic substrates, and flexible substrates, each catering to specific needs and demands.
How Does the Choice of Substrate Material Impact Overall Performance?
The material selection for substrates significantly influences thermal conductivity, electrical properties, and mechanical stability. Manufacturers choose materials based on the unique requirements of semiconductor packaging and the intended application.
What Quality Assurance Measures are Integrated into Wire Bond Substrate Manufacturing?
Quality control encompasses thorough testing of electrical properties, thermal performance, and dimensional accuracy. Visual inspections, automated testing, and adherence to industry standards are often implemented to ensure the reliability of manufactured wire bond substrates.
What Environmental Considerations Are Factored into Wire Bond Substrate Manufacturing?
Manufacturers pay heed to environmental aspects such as RoHS compliance, moisture protection, and resistance to contaminants. These considerations contribute to the overall reliability and durability of wire bond substrates.
Is Customization Available for Wire Bond Substrates Based on Specific Application Needs?
Yes, manufacturers commonly offer customization services, allowing wire bond substrates to be tailored for specific applications. Customizations may include variations in material selection, dimensions, and electrical specifications to meet unique requirements.
Conclusion
In summary, wire bond substrates emerge as indispensable elements within the intricate domain of semiconductor packaging, weaving a narrative of connectivity and foundational support within integrated circuits. Comprising a diverse palette of materials such as ceramics, organics, and metals, these substrates undergo a meticulous manufacturing odyssey, encompassing layer deposition, precision patterning, wire bonding, and encapsulation.
The selection of materials, conductive layers, and manufacturing methodologies exerts a profound impact on the substrate’s performance and suitability across diverse applications. Wire bond substrates carve their niche in the semiconductor and microelectronic landscapes, where compact dimensions, meticulous electrical connections, and efficient heat dissipation take precedence.
As we traverse the evolving saga of electronics, wire bond substrates, with their adaptability and customizable features, assume a pivotal role. They flexibly cater to the multifaceted demands of semiconductor packaging, delivering tailored solutions for various applications.
In this dynamic industry marked by constant innovation, wire bond substrates serve as catalysts for progress, furnishing a steadfast foundation for the integration of semiconductor components. The ongoing quest for heightened performance, reliability, and environmental considerations underscores manufacturers’ dedication to providing substrates aligned with the ever-shifting contours of electronic design.
Amid technological strides, wire bond substrates persist as keystones in the symphony of electronic devices, encapsulating the harmonious interplay of materials, precision manufacturing, and adaptability crucial for the sustained evolution of the semiconductor sector.