Wire Bonding Substrates Manufacturer
Wire Bonding Substrates Manufacturer. we can produce the best samllest bump pitch with 100um, the best smallest trace are 9um. and the smallest gap are 9um. most of the design are 15um to 30um trace and spacing.
Wire Bonding Substrates (PCBs) are foundational components in electronic devices, serving as the backbone for connecting various electronic components. They provide a platform for intricate circuitry, facilitating the transmission of electrical signals between components through wire bonding techniques. These substrates are crafted from materials like fiberglass-reinforced epoxy resin (FR4) or specialized materials such as Rogers or PTFE, chosen for their electrical properties, thermal stability, and mechanical strength. The manufacturing process involves precise design, meticulous material selection, and advanced fabrication techniques. PCBs come in various forms, from single-sided to multi-layered designs, tailored to suit the specific requirements of different applications. They play a vital role in enabling the functionality and performance of electronic devices across industries ranging from consumer electronics to aerospace and telecommunications. With their versatility, reliability, and adaptability, Wire Bonding Substrates continue to drive innovation and advancements in the field of electronics.
What is a Wire Bonding Substrate (PCB)?
A Wire Bonding Substrate, also known as a PCB (Printed Circuit Board), is a crucial component in electronic devices. It provides a platform for connecting various electronic components like integrated circuits (ICs), resistors, capacitors, and other electrical elements.
In wire bonding, thin wires made of materials like gold, aluminum, or copper are used to create electrical connections between different points on the substrate. These wires are typically bonded to metal pads on the substrate’s surface using heat, pressure, or ultrasonic energy. This process allows for the transmission of electrical signals between components, enabling the device to function as intended.
The substrate itself is usually made of a non-conductive material like fiberglass-reinforced epoxy resin, known as FR4. This material provides insulation and support for the electrical connections while also offering mechanical strength to the overall device.
Wire bonding substrates come in various shapes and sizes, tailored to fit the specific requirements of different electronic applications. They can be single-sided, double-sided, or multi-layered, depending on the complexity of the circuitry they need to accommodate.
Overall, wire bonding substrates play a fundamental role in the construction of electronic devices, facilitating the efficient transmission of electrical signals and ensuring the reliable operation of the final product.
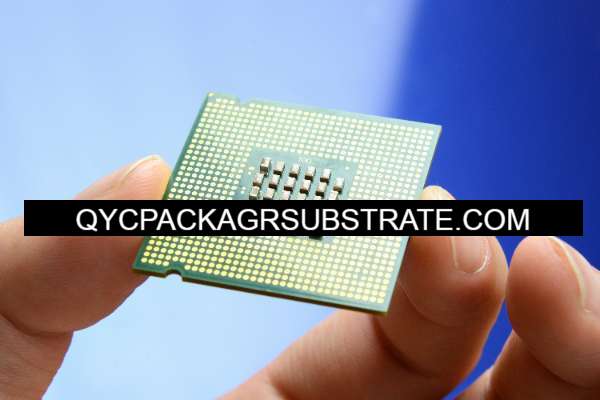
Ceramics Substrate ManufacturWire Bonding Substrates Manufacturerer
What are the Wire Bonding Substrate (PCB) Design Guidelines?
Designing a wire bonding substrate (PCB) involves adhering to specific guidelines to ensure the reliability and functionality of the electronic device. Here are some key design guidelines:
- Pad Layout: Arrange bonding pads strategically to facilitate wire bonding. Ensure proper spacing between pads to prevent short circuits and enable efficient wire bonding.
- Trace Routing: Design traces with appropriate widths and spacing to minimize impedance and signal loss. Avoid sharp turns and acute angles in trace routing to maintain signal integrity.
- Material Selection: Choose substrate materials with suitable electrical and mechanical properties. FR4 is commonly used for its balance of cost, performance, and availability, but high-frequency applications may require specialized materials like Rogers or PTFE.
- Layer Stackup: Determine the number of layers required based on the complexity of the circuitry. Plan the layer stackup carefully to minimize signal interference and impedance mismatches.
- Thermal Management: Incorporate thermal vias and heat sinks to dissipate heat generated by active components. Proper thermal management helps prevent overheating and ensures the reliability of the device.
- Component Placement: Place components strategically to optimize signal paths and minimize signal distortion. Consider the proximity of critical components and route traces accordingly to reduce parasitic effects.
- Grounding: Implement a solid ground plane to minimize noise and provide a stable reference for signals. Connect all ground pads and traces to the ground plane to create a low-impedance path for return currents.
- Signal Integrity: Perform signal integrity analysis to ensure signal integrity across the entire PCB. Consider factors like impedance matching, crosstalk, and signal reflection to minimize signal degradation and ensure reliable operation.
- Design for Manufacturing (DFM): Follow DFM guidelines to streamline the manufacturing process and reduce production costs. Consider factors like panelization, solder mask clearance, and minimum feature sizes to facilitate efficient PCB fabrication.
- Testing and Validation: Plan for thorough testing and validation of the PCB design to verify functionality and reliability. Conduct simulations, prototype testing, and design reviews to identify and address any potential issues early in the design process.
By adhering to these design guidelines, engineers can develop wire bonding substrates that meet the performance requirements and reliability standards of the electronic device.
What is the Wire Bonding Substrate (PCB) Fabrication Process?
The fabrication process of a wire bonding substrate (PCB) involves several steps to transform raw materials into a functional circuit board. Here’s an overview of the typical fabrication process:
- Design: The process begins with the design of the PCB layout using computer-aided design (CAD) software. Engineers create a detailed schematic, determine component placement, define trace routing, and establish the layer stackup.
- Material Selection: Select appropriate substrate materials based on the design requirements. Common materials include fiberglass-reinforced epoxy resin (FR4) for standard applications and specialized materials like Rogers or PTFE for high-frequency or high-temperature environments.
- Preparation of Substrate: The chosen substrate material is prepared for circuitry by cutting it to size and cleaning its surface to remove any contaminants.
- Layer Stackup: If the PCB requires multiple layers, individual layers of substrate material are laminated together using heat and pressure to create a single composite board. This process involves bonding layers with pre-applied copper foil to form the internal conductive layers.
- Circuit Patterning (Lithography): A layer of photosensitive material called resist is applied to the copper surface. The resist is exposed to ultraviolet light through a photomask, which defines the desired circuit pattern. After exposure, the resist is developed to remove the unexposed areas, leaving behind the pattern of conductive traces.
- Etching: The exposed copper areas not protected by resist are etched away using a chemical solution, leaving behind the desired conductive traces on each layer of the PCB.
- Drilling: Holes are drilled through the PCB at locations specified in the design, such as mounting holes and vias. These holes provide access for electrical connections between layers and for component mounting.
- Plating and Surface Finish: A thin layer of metal (typically copper) is plated onto the exposed copper surfaces to enhance conductivity and prevent oxidation. Surface finish processes like solder mask application and hot air solder leveling (HASL) are performed to protect the copper traces and facilitate soldering of components.
- Component Mounting: Electronic components are mounted onto the PCB using automated pick-and-place machines. The components are soldered to the board either through wave soldering or reflow soldering processes.
- Wire Bonding (if applicable): In some cases, wire bonding may be required to make electrical connections between components or between the PCB and external devices. This process involves bonding thin wires (typically made of gold or aluminum) to designated bonding pads on the PCB using heat, pressure, or ultrasonic energy.
- Testing and Inspection: The assembled PCB undergoes thorough testing and inspection to ensure functionality and reliability. Various tests, such as continuity testing, electrical testing, and visual inspection, are performed to identify and rectify any defects or issues.
- Final Finishing: Once testing is complete, the PCB is trimmed, cleaned, and labeled as needed before being packaged and prepared for shipping or assembly into the final electronic device.
Throughout the fabrication process, strict quality control measures are implemented to ensure the final product meets the required specifications and standards for performance, reliability, and safety.
How do you manufacture a Wire Bonding Substrate (PCB)?
Manufacturing a wire bonding substrate, also known as a PCB (Printed Circuit Board), involves several steps that transform raw materials into a functional electronic component. Here’s a simplified overview of the manufacturing process:
- Design: The process begins with the design of the PCB layout using specialized computer-aided design (CAD) software. Engineers create a detailed schematic, determine component placement, define trace routing, and establish the layer stackup.
- Material Selection: Choose appropriate substrate materials based on the design requirements and intended application. Common materials include fiberglass-reinforced epoxy resin (FR4) for standard applications and specialized materials like Rogers or PTFE for high-frequency or high-temperature environments.
- Panel Preparation: Cut the substrate material into panels or sheets of the required size. Clean the panel surfaces to remove any contaminants that could affect the fabrication process.
- Copper Cladding: Apply thin sheets of copper foil to one or both sides of the substrate panels using an adhesive layer. This copper cladding provides the conductive pathways for electrical signals on the PCB.
- Lamination: If the PCB requires multiple layers, stack the copper-clad substrate panels together with insulating layers in between. The stack is then pressed and heated to bond the layers together into a single composite board.
- Photoresist Application: Apply a layer of photosensitive material, called resist, to the surface of the copper-clad panels. This resist layer protects the copper during the etching process.
- Exposure and Development: Expose the resist layer to ultraviolet light through a photomask, which defines the desired circuit pattern. After exposure, the resist is developed to remove the unexposed areas, leaving behind the pattern of conductive traces on the copper surface.
- Etching: Use a chemical solution to etch away the exposed copper, leaving behind the desired conductive traces. The resist is then stripped away, leaving the copper traces exposed and ready for further processing.
- Drilling: Drill holes through the PCB at locations specified in the design, such as mounting holes and vias. These holes provide access for electrical connections between layers and for component mounting.
- Surface Finishing: Apply surface finish processes to protect the copper traces and facilitate soldering of components. Common surface finishes include solder mask application, hot air solder leveling (HASL), electroless nickel immersion gold (ENIG), and immersion silver.
- Component Mounting: Use automated pick-and-place machines to mount electronic components onto the PCB. Components are accurately positioned according to the design layout and then soldered to the board using wave soldering or reflow soldering processes.
- Wire Bonding (if applicable): In some cases, wire bonding may be required to make electrical connections between components or between the PCB and external devices. This process involves bonding thin wires (typically made of gold or aluminum) to designated bonding pads on the PCB using heat, pressure, or ultrasonic energy.
- Testing and Inspection: Conduct thorough testing and inspection of the assembled PCB to ensure functionality and reliability. Various tests, such as continuity testing, electrical testing, and visual inspection, are performed to identify and rectify any defects or issues.
- Final Finishing and Packaging: Trim, clean, and label the PCB as needed before packaging and shipping it or assembling it into the final electronic device.
Throughout the manufacturing process, strict quality control measures are implemented to ensure the final product meets the required specifications and standards for performance, reliability, and safety.
How much should a Wire Bonding Substrate (PCB) cost?
The cost of a wire bonding substrate (PCB) can vary significantly depending on several factors, including the size, complexity, materials used, quantity ordered, and additional features required.
For a standard, single-layer PCB with basic specifications and materials like FR4, the cost per unit can range from a few dollars to tens of dollars. However, as the complexity increases, such as with multi-layer designs, high-frequency requirements, or specialized materials, the cost can increase accordingly.
Here are some factors that can influence the cost of a wire bonding substrate (PCB):
- Board Size: Larger PCBs typically require more materials and processing time, resulting in higher costs.
- Layer Count:Multi-layer PCBs with more layers require additional manufacturing steps and materials, contributing to higher costs.
- Material Selection: Specialized materials like Rogers or PTFE are more expensive than standard FR4, impacting the overall cost of the PCB.
- Trace Density and Complexity: PCBs with dense trace routing or intricate designs may require more precise manufacturing processes, increasing costs.
- Surface Finish: Different surface finishes, such as ENIG or immersion silver, have varying costs that can affect the overall price of the PCB.
- Additional Features: Special features like impedance control, blind vias, buried vias, and controlled dielectric constants can add complexity and cost to the PCB fabrication process.
- Quantity Ordered:Larger production quantities often result in lower unit costs due to economies of scale. Ordering in bulk can help reduce the cost per unit.
- Lead Time: Expedited production or short lead times may incur additional fees from PCB manufacturers.
To obtain an accurate cost estimate for a wire bonding substrate (PCB) for a specific project, it’s advisable to consult with PCB manufacturers or suppliers. They can provide detailed quotes based on the project requirements and specifications. Additionally, online PCB cost calculators are available from some manufacturers to estimate costs based on input parameters like board size, quantity, and complexity.
What is a Wire Bonding Substrate (PCB) base material?
The base material of a wire bonding substrate (PCB) refers to the underlying material that forms the structural foundation of the PCB. This material provides mechanical support, insulation, and a platform for the conductive traces and components that make up the circuitry of the PCB.
The most commonly used base material for PCBs is fiberglass-reinforced epoxy resin, commonly known as FR4. FR4 is a versatile and widely available material that offers a good balance of properties such as mechanical strength, thermal stability, electrical insulation, and cost-effectiveness. It consists of a woven fiberglass cloth impregnated with an epoxy resin binder.
Other base materials used for PCBs include:
- High-Temperature FR4: Similar to standard FR4 but with enhanced thermal resistance, suitable for applications requiring operation at elevated temperatures.
- Rogers and Other High-Frequency Materials: Specialized materials optimized for high-frequency applications, offering low dielectric loss and controlled impedance characteristics. Examples include Rogers laminates and polytetrafluoroethylene (PTFE)-based materials.
- Metal Core: PCBs with a metal core, typically aluminum or copper, used for applications requiring enhanced thermal conductivity and heat dissipation.
- Flex and Rigid-Flex Materials: Flexible base materials like polyimide or polyester film for flexible PCBs, and combinations of flexible and rigid materials for rigid-flex PCBs.
- Ceramic: Ceramic-based substrates for high-power and high-frequency applications, offering excellent thermal conductivity and stability at high temperatures.
The choice of base material depends on various factors such as the intended application, operating environment, electrical performance requirements, thermal considerations, and cost constraints. Designers select the appropriate base material based on these factors to ensure the PCB meets the desired performance and reliability standards.
Which company makes Wire Bonding Substrates (PCBs)?
There are many companies specialized in producing Wire Bonding Substrates (PCBs), and some well-known manufacturers include Materion in the United States, Mitsubishi Materials in Japan, Schweizer Electronic AG in Germany, and AT&S in China. These companies have extensive experience and leading technology in the PCB industry, providing high-quality products for various applications.
As for our company, we are also a professional PCB manufacturer with extensive manufacturing capabilities and experience, capable of producing various types of PCBs, including Wire Bonding Substrates. We employ advanced production equipment and technologies, along with strict quality control measures, to ensure that our products meet customer requirements and industry standards.
Our manufacturing process covers the entire process from design to delivery. We have an experienced design team that can provide custom PCB design services tailored to customer needs. We select high-quality base materials such as FR4, Rogers, or PTFE to ensure the performance and reliability of the PCBs. Our production equipment includes advanced automation equipment such as pick-and-place machines and wave soldering machines, as well as precision machining equipment such as CNC drilling machines and chemical etching equipment.
During the manufacturing process, we strictly adhere to quality control standards, conducting multiple inspections and tests to ensure that each PCB meets specifications and meets customer expectations. We also offer flexible production capabilities and fast delivery times to meet urgent customer needs and large-volume orders.
Overall, as a PCB manufacturer, we are committed to providing high-quality, reliable, and customizable products to meet customer needs in various application fields. Our professional team is dedicated to providing excellent service and support to drive customer success and development.
What are the 7 qualities of good customer service?
Good customer service is characterized by several key qualities that contribute to positive interactions and relationships with customers. Here are seven qualities of good customer service:
- Responsiveness: Good customer service involves promptly addressing customer inquiries, concerns, and requests. Being responsive shows customers that their needs are valued and that you are committed to helping them in a timely manner.
- Empathy: Empathy is the ability to understand and relate to the feelings and perspectives of customers. Good customer service representatives demonstrate empathy by listening attentively, acknowledging customers’ emotions, and showing genuine concern for their well-being.
- Professionalism: Professionalism entails maintaining a courteous, respectful, and professional demeanor when interacting with customers. This includes using appropriate language and tone, adhering to company policies and procedures, and presenting a positive image of the organization.
- Knowledgeability: Good customer service representatives possess a thorough understanding of the products or services offered by the company. They are knowledgeable about features, benefits, pricing, and usage instructions, enabling them to provide accurate information and effective assistance to customers.
- Problem-Solving Skills: Effective problem-solving skills are essential for resolving customer issues and addressing their needs satisfactorily. Good customer service involves identifying problems, analyzing root causes, and implementing appropriate solutions in a timely manner.
- Flexibility: Flexibility is the ability to adapt to changing customer needs and circumstances. Good customer service representatives are flexible in their approach, willing to accommodate customer requests, and capable of finding creative solutions to unique situations.
- Consistency: Consistency is key to building trust and credibility with customers. Good customer service is consistent across all interactions and channels, ensuring that customers receive the same level of quality and attention regardless of who they speak to or how they reach out to the company.
By embodying these qualities, organizations can deliver exceptional customer service experiences that foster loyalty, satisfaction, and positive word-of-mouth referrals.
FAQs
What is a Wire Bonding Substrate (PCB)?
A Wire Bonding Substrate, also known as a PCB (Printed Circuit Board), is a fundamental component in electronic devices. It provides a platform for connecting various electronic components using wire bonding techniques.
How does Wire Bonding work on PCBs?
Wire bonding involves using thin wires made of materials like gold, aluminum, or copper to create electrical connections between different points on the PCB. These wires are bonded to metal pads on the PCB’s surface using heat, pressure, or ultrasonic energy.
What are the advantages of Wire Bonding Substrates?
Wire bonding offers several advantages, including low cost, flexibility in design, suitability for small and lightweight devices, and the ability to accommodate high pin counts and fine pitch components.
What are the different types of Wire Bonding?
The two main types of wire bonding are ball bonding and wedge bonding. Ball bonding involves creating a ball-shaped connection between the wire and the bonding pad, while wedge bonding creates a wedge-shaped connection.
What materials are commonly used in Wire Bonding Substrates?
Common materials used in Wire Bonding Substrates include fiberglass-reinforced epoxy resin (FR4), specialized materials like Rogers or PTFE for high-frequency applications, and metal-core substrates for enhanced thermal conductivity.
What are the design guidelines for Wire Bonding Substrates?
Design guidelines for Wire Bonding Substrates include considerations for pad layout, trace routing, material selection, layer stackup, thermal management, component placement, grounding, signal integrity, design for manufacturing (DFM), testing, and validation.
How are Wire Bonding Substrates manufactured?
The manufacturing process of Wire Bonding Substrates involves steps such as design, material selection, panel preparation, copper cladding, lamination, circuit patterning, etching, drilling, surface finishing, component mounting, wire bonding (if applicable), testing, and final finishing.
What factors affect the cost of Wire Bonding Substrates?
Factors affecting the cost of Wire Bonding Substrates include board size, layer count, material selection, trace density and complexity, surface finish, additional features, quantity ordered, lead time, and testing and inspection requirements.